
2 minute read
Friction (Koepe) winding installations
upper suspension beam accommodates the lifting and lowering operations. It is moved by means of two electrically powered synchronized lead screws that can comfortably travel at 2.5 m/min under a full load of up to 650 kN. The lead screws are driven by an electric motor through a self-locking worm gearbox complete with an additional fail-safe brake arrangement.
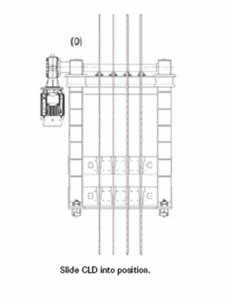
Advertisement
During operation, the CLD will be securely anchored to the headgear structure by means of clamps and/or anchor bolts to prevent lateral movement.
Operation
The winding ropes are clamped on the upper suspension beam and pulled upwards by means of the rotating lead screws. Upon completion of each stroke, the rope clamps are manually engaged in the fixed suspension beam. The movable suspension beam is then moved slightly downwards, transferring the load to the clamping wedges in the fixed suspension beam. The movable suspension beam now becomes load free and allows for the manual removal of its wedges before moving to its original position for the start of the next cycle.
Wedges are removed using small jacks mounted on a common rail powered by a manually operated hydraulic pump. Though this is a manual process this sequence can be repeated as many times as needed.
Tehnical data table
Advantages of Electro-Mechanical CLD
• Lower capital cost option when compared to the fully automated hydraulic CLD
• Lower maintenance costs when compared to the automated hydraulic CLD
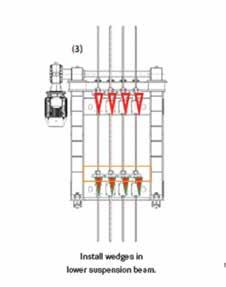
• No hydraulic power pack is required
General applications of the CLD
• Clamping and lifting of multiple steelwire ropes suspended in a friction winder mine shaft compartment
• Lifting and lowering the maximum loads within a hoisting compartment
• Creation of slack rope (for removal of pins, or removal of ropes from the winder drums and sheaves
• Accurate positioning of conveyances during rope-up or rope-changing operations.
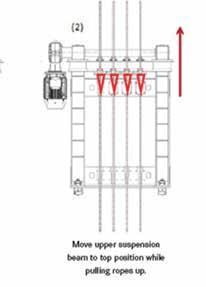
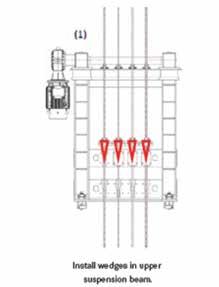
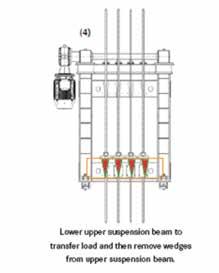
HEAD OFFICE
1st Floor, Osborne Office Suites, 4 Osborne Lane, Bedfordview, 2007
South Africa
PO Box 3037, Bedfordview 2008, South Africa, Tel. +27 11 383 9300
WADEVILLE FACTORY
12 Tedstone Road, Wadeville 1428, Ekurhuleni, South Africa www.winder.co.za
We offer our clients a comprehensive service including design, manufacturing, supply, installation, commissioning and site servicing of winders, winches, hoists, sheaves, rope-handling and related equipment.
Our single point of contact service provides seamless interfacing between all disciplines and covers all major equipment brands.
Our Divisions Mechanical
As an independent systems integrator for shaft hoisting systems, we have extensive systems engineering and project management experience. Our service includes planning, mechanical design and construction of winders and various systems. We satisfy clients' hoisting and general industrial requirements with custom-designed solutions.


AUTOMATION, DRIVE TECHNOLOGY AND SYSTEMS INTEGRATION
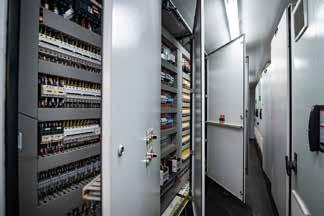
We provide full engineering, manufacture and supply of all electrical aspects for legacy as well as modern winders including drive, control and safety systems for all winder types and all rope handling equipment. Our products cover fully automated as well as manual control systems, brake control systems and cage and level-control systems and can be provided as retro-fit or new equipment. Our extensive systems integration experience enables us to incorporate electrical, mechanical and hydraulic equipment of all makes.
Hydraulics
We design, manufacture, install, commission, maintain and refurbish a variety of hydraulic systems for industrial and mining applications. A comprehensive range of specialist hydraulic products and related services is available. We offer our clients individually tailored solutions in compliance with applicable standards and regulations.
Site Services And Spares
Our experienced, in-house Services Department personnel manage and execute the site work required to install and commission both new and refurbished winders as well as carry out site upgrades, emergency breakdown repairs and maintenance work. We also offer Level 1 dynamic braking and cage accelerometer inspections as well as annual inspections of hoisting systems.