Most Successful MINING CEOs
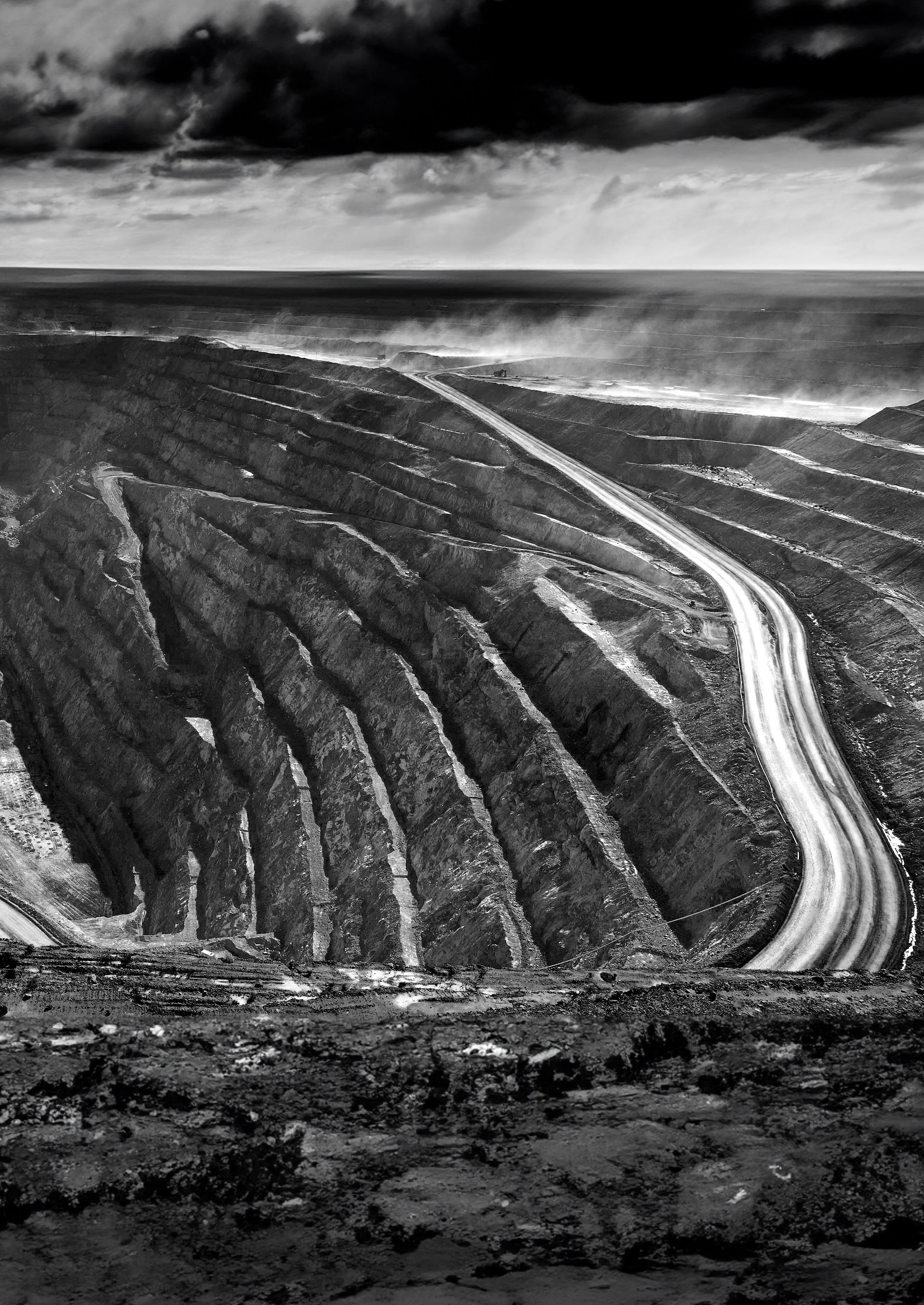
6 - 7 September 2023
Business Design Centre, London
SPONSORSHIPS GET YOUR PASS
EDITOR-IN-CHIEF
SCOTT BIRCH
CHIEF CONTENT OFFICER
SCOTT BIRCH
CHIEF DESIGN OFFICER
MATT JOHNSON
HEAD OF DESIGN
ANDY WOOLLACOTT
LEAD DESIGNER
HECTOR PENROSE
FEATURE DESIGNERS
MIMI GUNN
SOPHIE-ANN PINNELL HECTOR PENROSE
SAM HUBBARD
JUSTIN SMITH
REBEKAH BIRLESON
ADVERT DESIGNERS
JORDAN WOOD
DANILO CARDOSO
CALLUM HOOD
VIDEO PRODUCTION MANAGER
KIERAN WAITE
SENIOR VIDEOGRAPHER
HUDSON MELDRUM
DIGITAL VIDEO PRODUCERS
MARTA EUGENIO
ERNEST DE NEVE
THOMAS EASTERFORD
DREW HARDMAN
JOSEPH HANNA
SALLY MOUSTAFA
JINGXI WANG
PRODUCTION DIRECTORS
GEORGIA ALLEN
DANIELA KIANICKOVÁ
PRODUCTION MANAGERS
JANE ARNETA
MARIA GONZALEZ
CHARLIE KING
YEVHENIIA SUBBOTINA
MARKETING MANAGER
INDIA BERRY
PROJECT DIRECTORS
MATT ANSELL
CRAIG KILLINGBACK
BILLY EVANS
MEDIA SALES DIRECTORS
JAMES WHITE
MANAGING DIRECTOR
LEWIS VAUGHAN
CEO
GLEN WHITE
This issue is very much looking towards the future of the mining industry – and it’s bright.
From innovative technology making mines safer and more productive, to supply chain sustainability ensuring operational excellence, we have it all buried away in the digital pages of this latest edition.
In many ways, mining is at the leading edge of industry 4.0 – marrying super-smart technology with some of the world’s largest machines to enhance efficiency and make the most of the ‘old’ ways and the ‘new’.
The irony is not lost on us that those batteries and microchips enabling the digital revolution rely on the mining industry to deliver the essential elements from beneath the world’s surface.
When society is disconnected from the end products it sees on its supermarket shelves – from food to flatscreens – and the raw materials required to make those, it can sometimes be hard to be a champion and fight popular misconceptions.
Yet mining is in the ascendancy, and a vital, essential industry like never before.
scott.birch@bizclikmedia.com
“Batteries and microchips enabling the digital revolution rely on the mining industry to deliver the essential elements from beneath the world’s surface”
Mining magazine is an established and trusted voice with an engaged and highly targeted audience of 100,000 global executives
Digital Magazine
Website Newsletters
Industry Data & Demand Generation
Webinars: Creation & Promotion
White Papers & Research Reports
Lists: Top 10s & Top 100s
Events: Virtual & In-Person
WORK WITH US
Time to dig out those cheque books, as the Liebherr R9300 Generation 8 (G8) is now available for purchase. The latest addition to the firm’s excavator portfolio was first unveiled in 2022 and will update the R9250. The R9300 is packed with technology and compatibility with future enhancements including automation, zero emission technologies, and digital services.
» Several years ago, I worked for a bank dealing with metal clients. That’s when I realised the supply chain was broken. I could tell that everyone wanted transparency. After leaving the bank in 2017, my team and I started establishing a global metals exchange with the aim of democratising the world’s markets, creating price benchmarks, and building supply chains.
The Technology Metals Market (TM2) connects institutional investors, physical markets, and proprietary traders with metals issuers – miners, refiners, recyclers, and mints – to exchange technology metals. We are the world’s first company that offers direct investment opportunities in the metals that power technology.
In 2021, we partnered with NASDAQ after about 20 months, making thousands of phone calls to understand each vertical’s supply chain and supply chain operation. We realised there was much more demand than supply. In order to build a liquidity-rich exchange, we had to pivot into the upstream, into the mining side of our business and build partnerships there. We are currently active in over a dozen metal verticals. Our team is developing the supply chain pathways for critical battery metals.
» We operate in Africa, Europe, South America, and Asia. We aim to build concentration plants and move critical materials and metals further into the supply chain by using the supply network we have created to deliver goods to original equipment manufacturers (OEMs). Among these materials are hydroxides, carbonates, lithium, graphite, iron ore, zinc, manganese, and many others.
As miners have always wanted to extend their products downstream, transparency and vertical supply chain integration are essential. In the same way, global brands have always sought to get close to their suppliers because that means durability and security.
Our role is to bridge this market by connecting products and end users and removing opacity. To accomplish this, we have created the world’s first physical exchange to provide price indexing, benchmarks, and transparency.
» Often, the best results aren’t easy to achieve. They require a great deal of effort. Getting here has taken us tens of thousands of calls and research, so putting in the effort is the challenge. There is a massive shock affecting global commercial markets. Yet, everything is moving faster, and everyone expects a welldesigned supply chain. However, you must put in the effort to create better-designed supply chains. Our challenge is simply designing what has yet to be developed, mapping what hasn’t been mapped, and pioneering what hasn’t been done. We have contacted many suppliers, processors, and secondary processors, so it’s a puzzle we are putting together.
» It is anything that increases efficiency and lowers waste. The future of mining is centered on any implementation or technology that allows one to reduce pollution and wastage and increase yield and efficiency.
» You can expect to see new sustainable global supply chains built to deliver ethical products from an honest relationship with communities into a world where everyone benefits from its value. We are designing and implementing supply chains for most battery metals, and we will expand our exchange to offer a democratic and transparent price for these metals. That’s where our uniqueness lies; the ability to connect upstream, processors, and end users.
» Throughout my life, my father has given me plenty of advice; he always believed that when you do the right things, good things will happen to you. What stuck with me most is what he refers to as the 3Ds – drive, determination, and desire. As I’ve noted, nothing worthwhile takes place quickly. So, I’ll say hard work always pays off, so be determined, have the desire to achieve, and have dedication and the drive to succeed.
From combat in the Gulf War when Iraq invaded Kuwait in the 90s to leading one of the fastest-growing mining companies in the world, Robert ‘Bob’ G Wilt is one of those outstanding executives with fascinating personalities. He is a veteran with years of experience in the mining industry and an executive leader who has led companies through good times and bad.
He is the Chief Executive Officer of Saudi Arabian Mining Co., Ma’aden, the Middle East’s largest mining and metals company. Previously, Bob served as president and CEO of Sofina Foods, a privately held meat and seafood processor with 44 locations in Canada and Europe, from 2020 until January 2022. He holds an MBA from Harvard Business School and a bachelor’s degree in Engineering Management from the United States Military Academy at West Point, New York.
Upon completing his MBA from Harvard Business School, Bob enlisted in the US Army. During his service in the 101st Airborne Division, he served as a combat engineer officer and platoon leader. During the Gulf War, he oversaw construction of two base camps while planning and leading combat engineering missions. At the time, Bob had no idea he’d be carving a path to the upper echelons of the mining industry or he’d be leading the largest mining company in the Middle East.
When he left the US Army, Bob worked as a senior consultant for the organising committee for the 1996 Olympic Games in Atlanta. In 1999, Bob began working as a production supervisor at Alcoa, one of the world’s top 10 aluminium producers with headquarters in Pittsburgh, Pennsylvania.
From plant manager, he rose through the ranks to become VP of energy development, VP of operations, and ultimately the company’s executive vice president in 2013, responsible for the company’s upstream business, including the world’s largest mining and refining of bauxite, and the third largest smelting process. In 2017, he became President of Precision Castparts Corporation’s Metals Group, managing its aerospace and industrial subsidiaries.
As a leader, Bob has demonstrated exceptional strategic and operational results in a variety of challenging environments over the course of 30-plus years in various leadership positions. His appointment coincided with Ma’aden’s rapid expansion in search of untapped mineral deposits across the Kingdom. On the sidelines of the UN Climate Change Summit in Egypt, he spoke at the Saudi Green Initiative about Ma’aden’s plan to become the third pillar of the Saudi Arabian economy as the Gulf nation steps up efforts to diversify its revenue sources and progress in line with Vision 2030.
In addition to commissioning a gold mine and an ammonia plant since joining Ma’aden, Bob secured long-term partnerships with strategic institutions like the Public Investment Fund (PIF), and entered joint ventures with Ivanhoe Electric to accelerate exploration activities by six times. Yet, Ma’aden’s largest gold project, which is expected to produce 250,000 ounces per year, is underway.
In the company’s 2023 first-quarter report, Bob said “we continued to focus on rolling out our transformation program to make Ma’aden a more agile, responsive business, better equipped to capture growth opportunities and unlock long-term value for shareholders. We have increased production and sales volumes in our core Phosphate Business Unit and delivered another period of strong cash generation.”
According to him, Ma’aden is on track to optimise existing operations and implement new projects.
Ma’aden’s commitment to being a leading company in sustainable mining is Bob’s driving force as he continues to build the company’s operations on a solid foundation of profitability and sustainable practices.
WHEN HE LEFT THE US ARMY, BOB WORKED AS A SENIOR CONSULTANT FOR THE ORGANISING COMMITTEE FOR THE 1996 OLYMPIC GAMES IN ATLANTA
Why more sustainable supply chains are essential to help combat climate change, and three ways to help achieve those goals
WRITTEN BY: LANRE-PETER ELUFISANClimate change is one of the biggest challenges facing today’s global supply chain. That’s why governments and multinational companies, especially in the mining sector, want to keep global warming below 2°C. However, we must build a more sustainable supply chain to achieve that goal.
For the mining sector, the problem appears in the solution and vice versa. We can’t transition to a circular economy until we have all the materials (metals and minerals) essential to functioning green technologies. Yet, extracting resources from
the earth requires heavy machinery and transportation, which are significant sources of greenhouse gas emissions.
According to a World Bank report, the production of minerals, such as graphite, lithium, and cobalt, could increase by nearly 500% by 2050 to meet the growing demand for clean energy technologies. This means that the more ambitious the climate goals, the more minerals are needed for the transition. Therefore, as the demand for minerals grows, so does the need to ensure that mining operations run on sustainable environmental practices.
Reap the benefits of SAP’s shopfloor manufacturing execution system (MES) for your overall manufacturing process.
Enabling a new level of production continuous improvement, from raw materials to finished goods, while achieving Industry 4.0 benefits:
y Increased product quality
y Increased profitability
y Waste reduction
y Better staff utilization
y Easier regulatory compliance
y Increased customer satisfaction
Reach out to us for a consultation on how Industry 4.0 and Digital Transformation can help you achieve the “Factory of the Future”.
Greenhouse gas emissions and global warming are severe threats to the green future that the world now envisions. As a result, businesses must embrace sustainability principles and comply with government regulations because supply chains contribute to CO2 emissions. Take a mining company like Rio Tinto, for example. It has about 20,000 suppliers across many industries and countries and 230 marine vessels transporting products to its 2000 customers worldwide.
This vast ecosystem shows the role large companies, especially those in the mining sector, should play in the journey to a low-carbon future. Knowing the mineral intensity of the clean energy transition, the mining sector needs to contribute to tackling climate change and building more sustainable supply chains and to do that, there are inherent challenges in establishing supply chain sustainability.
An essential component of ensuring green supply chains is the visibility of vendors’ performance. Suppose a company has thousands of first-, second-, and
“Companies need to establish strong supplier relationship management and collaborate within their ecosystem to share knowledge on challenges, local regulations, and new methods of reaching their ESG goals”
ADEBAYO ADELEKE FOUNDER OF SUPPLY CHAIN AFRICA
third-tier suppliers. In that case, it may be impossible to control the mode of operation of the lower-tier suppliers because realising visibility at every stage of a company’s supply chain network is complex. Sometimes the lower-tier suppliers are from undeveloped countries where sustainable initiatives are not seriously enforced.
Another concern for some companies is the initial cost of investment required to develop new sustainability standards and strategies to meet regulatory or customer requirements. A survey conducted by the Economic Intelligence Unit revealed that 38% of companies believe the higher initial costs are a major barrier to implementing sustainability.
Nevertheless, the same survey also revealed that 34% of the participating companies think that a sustainable supply chain will eventually reduce costs and enable them to break even soon. The estimated cost of ignorance in supply chain sustainability will reach US$120 billion by 2026. Therefore, embracing sustainability as early as possible will help businesses conserve market share in the future and remain competitive.
the most risk
According to Harvard Business Review, “companies tend to focus on their top-tier suppliers, but the real risks come lower.’’ Unknowingly, it could be one lower-tier supplier overseas making employees work in hazardous conditions or dumping toxins into rivers. This is why companies must not ignore the lower-tier suppliers in their network.
Since corporations are more conscious of their impact on people and the environment, companies have been trying to work only
with suppliers that adhere to social and environmental standards. These companies expect their first-tier suppliers to comply with those standards and also ask that those suppliers ask for compliance from their suppliers – to create a cascade of sustainable practices that flows smoothly throughout the supply network. As admirable as this concept is, it’s been hard to realise in practice.
The study found lower-tier suppliers lack environmental management systems and procedures for handling social problems and are the least equipped to handle sustainability requirements. Additionally, they often operate in countries with non-existent or non-enforced regulations and are usually unaware of big corporations’ sustainability requirements.
As a result, lower-tier suppliers are the most risky. If they have poor or dubious sustainability performance, companies that do business with them can endanger their reputation and suffer profound repercussions. To minimise such risks, companies must consider all their suppliers in their sustainability programs.
According to the CDP 2022 supply chain report, 70% of companies did not assess the impact of their value chain on biodiversity. This means companies fail to track supply chain emissions, risking falling foul of sustainability regulations.
According to the European Sustainability Reporting Standards, transparency in Scope 3 emissions could be required in a matter of months in the EU. The story is similar in the United States, where climate-related financial reporting will soon be required under the International Sustainability Standards Board (ISSB) global baseline standard.
In other words, if a company does not prepare for future regulations on nature in the supply chain, it will be exposed to a
wide range of risks and possibly miss out on opportunities that may arise from tackling climate change.
Alf Barrios, Rio Tinto Chief Commercial Officer, said “consumers want products that are sustainably sourced, and companies want products that help them meet their emissions and sustainability targets. Investors also seek ESG-based opportunities to deliver sustainable, longterm returns, further driving demand for responsibly produced materials. He added that many of the materials used in products today might not be preferred choices in the future unless they can establish their environmental, social, and governance (ESG) credentials.
Businesses can gauge their operational efficiency and sustainability by tracking greenhouse gas (GHG) emissions generated during operations and can monitor and report on their energy and sustainability performance. As companies will soon start tracking emissions to prepare for mandatory reporting, they need to understand their supply chain’s emissions of CO2 to work on reducing those emissions.
3. Collaborate and adopt innovative technologies quickly Collaboration is also a key element in creating sustainable supply chains. Adebayo Adeleke, a supply chain management consultant and founder of Supply Chain
Africa, asserts that ‘‘sustainability has made collaboration the new competition.’’ adding that ‘‘more than ever, companies need to establish strong supplier relationship management and collaborate within their ecosystem to share knowledge on challenges, local regulations, and new methods of reaching their ESG goals.’’
By working closely with suppliers, mining companies can work together to create more efficient and environmentally friendly solutions that benefit everyone involved. For example, suppliers can provide feedback on production processes and share working practices for reducing energy consumption or improving waste management systems. Creating such a communication channel
builds trust and is vital for achieving sustainable supply chains.
Another effective strategy for creating a sustainable supply chain is embracing technology. Technology enables businesses to identify inefficiencies and implement new processes that reduce waste and environmental impact while maintaining quality standards. This could be electrification technology or digital solutions to improve visibility and traceability across the supply network.
There is no shortcut to building a sustainable supply chain because sustainability is not a destination but a journey. So companies have to be truthful in assessing their people, environmental, and profitability impact to know how to get where they want to, says Adebayo Adeleke.
To create a more sustainable supply chain, companies must establish trust and open communication across their supply network, evaluate where they are in the sustainability journey, and embrace technology that reduces their carbon footprint. This would help mitigate climate change risks and optimise profits and human resources.
The estimated cost of ignorance in supply chain sustainability will reach US$120bn by 2026
Report from McKinsey says electrification of mining could mean doubling demand for electricity. Can operators meet the challenges, and reap the rewards?
Electrifying mining may be an ambition for many companies looking to reduce their carbon footprints and energy costs, but reaching that goal will also mean significant investment.
That’s according to a new report from McKinsey that says electrifying mines could double the demand for electricity. This will require some serious investment in the power infrastructure, with McKinsey saying this could top US$45 billion for the iron ore industry alone.
However, the potential benefits are just as eye-catching. Energy costs could be reduced by up to 70%, while the all-important carbon footprint could be reduced by as much as 80%.
Of course, this is not some unachievable target, as the report authors – Marc Henrio, Otto van der Ende, Gabriel Motta, and Raj Kumar Ray – tell Mining Digital.
“There are already 100% electric underground mines around, and it is definitely a possibility that fully electric open pit mines should start to come up in the future as the equipment technology matures.”
SuperBattery dump trucks could be fully charged in just 90 seconds – 100-times faster than standard lithium-ion batteries
While companies such as Epiroc are already producing battery electric vehicles (BEVs) suitable for underground use, the sheer scale of open pit mining machinery means the technology needs to advance to make it commercially viable.
Mining has a critical role to play in the transition to a net-zero economy and mining companies are under increased pressure from consumers and investors to clean up their act. It is therefore vital to secure access to significant amounts of renewable electricity to turn mines fully electric and replace diesel.
McKinsey says electrifying the global iron ore industry would require as much as 11 gigawatt-hours of additional electricity per metric ton of iron ore.
The consultancy says that once electric haul trucks become available, the need for electricity could double, simply by replacing 27 diesel trucks and the associated equipment.
So where could this extra electricity come from?
“The best solution to supply electricity to remote operations depends largely on the geographical context of the mine,” says McKinsey.
“Some remote regions have significant solar/wind potential, and those solutions tend to be the cheapest option in high potential areas. In the future, as storage alternatives get more competitive (battery storage, long-duration energy storage), the grid stability issues related to solar/wind could reduce, making it more feasible to run whole operations based on those energy sources.
“When solar and wind potential is not high, small modular reactors (SMRs) could be an alternative to be evaluated, together with carbon capture and storage (CCS) for abating emissions from fossil sources.”
Generating the electricity is one challenge, storing it is another. As the experts from McKinsey say, developments in battery technology will help smooth out those demand curves.
One company already leading the charge on battery tech is Skeleton Technologies which has developed what it calls the ‘SuperBattery’. This graphenebased battery is being developed to power dump trucks for a Shell-led consortium for electrified mining.
With your SAP MII and ME system being paramount to achieving high-performance manufacturing, let RTS support your shopfloor solution to maintain peak plant operating performance at all times.
Our experienced and knowledgeable staff provide quick support response on a 24/7 basis. RTS not only provides support but will also deliver:
y System upgrades to newer versions
y Modifications to your existing MES solution
y Adding completely new capabilities to your existing system
y IoT connectivity
Reach out to us for details on how we can “support and service” your existing SAP MII and ME shop floor solution.
These dump trucks could be fully charged with 400kW of electricity in just 90 seconds – 100-times faster than standard lithiumion batteries. The SuperBattery also has an extended lifespan, lasting for around 50,000 cycles compared to 4,000 for lithium-ion.
The key challenges of electric mining Electrifying mines is challenging but has the potential to generate considerable value. Here are the key challenges:
Large capital expenditures requirements. The costs for implementing the power infrastructure for electrifying the iron ore industry alone could reach US$45 billion. This will surely mean that new sources of capital (such as green bonds) will be needed.
Large infrastructure improvements. Mines will need to upgrade grid connections, build on-site networks, and install or contract renewable-power capacity.
BEV technological challenges. Battery technologies need to achieve higher density, lower costs, faster charging rates, and larger scale to make electric equipment competitive.
McKinsey says that adapting the operations to a new type of technology
7-11 GWh
Additional electricity needed per metric ton of iron ore
20-30 TWh
Additional electricity needed to electrify global iron ore mining McKinsey
Equivalent to 7-11 GWh of Australia's annual electricity consumption
“The best solution to supply electricity to remote operations depends largely on the geographical context of the mine”MCKINSEY
Energy consumption after electrification, GWh/year
Electricity
Fuels
Current energy required
Fuel displaced Additional electricity required
Future energy required
+115175% Increase in electricity demand after mobile fleet electrification
McKinsey & Company
All-electric mines are not new. Newmont made its Borden Gold project in Canada all-electric back in 2019, replacing all of its underground diesel fleet of trucks with BEVs.
Newmont says this not only makes the mine more efficient but also improves health & safety and reduces the environmental footprint.
Newmont worked with Sandvik Mining and MacLean Engineering on the BEVs. The tech included drilling and blasting equipment, electric bolters, personnel carriers and a 40-tonne haul truck.
The company says it has reduced GHG emissions by 50%, or 5,000 tonnes of CO2 per year, and reduced underground ventilation requirements by half.
presents multiple challenges, and has the following recommendations for a successful transition to electric.
Before the actual implementation of electric equipment:
• Adapt the mine planning and the operations planning to the new equipment – eg. location of charging stations, design of ramps and haulage ways
• Funding the investment for equipment and infrastructure
• Build the infrastructure at site (access to electricity, transmission, charging)
• Obtain access to the equipment, in a scenario where most companies are competing for a limited supply of electric mining equipment
When implementing and operating electric equipment:
• Upskill the operators and maintainers to adapt to the new type of equipment
• Adapt the operational strategy (eg. dispatch logic with energy management, rotation of crew during charging downtime)
• Adapt the maintenance strategy (eg. inventory of parts, batteries, maintenance of chargers, power infrastructure)
While those challenges may seem a barrier right now, the potential gains mean the effort (and expense) will be worthwhile. Those opportunities are:
Operational expenditure. Electrification could reduce energy costs by as much as 70% and reduce maintenance costs for mobile equipment by around 30%.
Operational improvements. Electric equipment could allow for steeper ramp designs, lower stripping ratios, faster cycle times, and less-frequent breakdowns.
CO2 emissions reduction. A fully electrified mine with renewable power could have a carbon footprint that is 80% lower. As well as being good for the environment, this could also avoid carbon taxes and capture potential greenproduct premiums.
As well as those benefits, McKinsey points to improved working conditions, especially in underground mines (for instance less noise, vibration, better air quality).
In the longer term, mine operators could redesign the mine, adapting to hauling in declines, steeper ramps potentially leading to lower stripping ratios. There would also be lower infrastructure requirements for ventilation in underground mines.
The Global Sustainability Awards 2024 will be celebrating the very best in Sustainability & ESG with the following categories:
Sustainability Strategy Award
–
ESG Program Award
–
Climate Change Award
–
Diversity & Inclusion Award
–Net Zero Award
–
Sustainable Supply Chain Award
–
Sustainable Technology Award
–
Sustainable Consultancy Award
–
Future Leader Award
–
Executive of the Year Award
–
Project of the Year Award
–
Lifetime Achievement Award
Mine-site technology adoption survey says investment in safety tech is rising. We speak with David Kurtz,
GlobalData’s recent global minesite technology adoption survey suggests a greater level of investment in site safety, as well as mine planning and management software.
The survey also highlights investment in mine communication and predictive maintenance, but it is safety-related technologies – such as drones, collision avoidance, and fatigue detection – that are showing the most movement, according to the data and analytics firm.
Its survey of 150 senior mine-site personnel said the share that had invested in drones has risen from 44% to 74% in the past five years, collision avoidance from 62% to 72%, and fatigue detection from 53% to 72%.
Fatigue detection was also high on future spending plans, with 38% saying they intended to invest in the next two years, while 40% would spend on predictive maintenance and 39% on management software.
There were also some interesting regional findings from the survey. When it comes to
drones, for instance, 56% of mines use them for safety purposes in Australia compared to just 36% in Africa.
Some 30% of respondents said that they had fully implemented collision avoidance technology, with the largest share in Australasia. The highest share expecting to invest in the next two years is in the Americas (37%).
Mining Digital spoke exclusively to David Kurtz, Research & Analysis Director at GlobalData, to dig deeper into the findings.
When it comes to where investment is being made, is that naturally being driven by the technology itself? For instance, five years ago drones would have been less available, higher cost, and lower quality? Yes, that is true. There is pressure to ensure a return on investment with any technology spend, and for many miners investment has become more feasible as costs have fallen.
Many mining companies are risk averse, with the sector initially slower to adopt new technologies compared with others such
The proven, trusted industry leader for unrivalled performance and innovation – always. When it comes to specifying your next pump or pump upgrade, it’s not a question of whether you can afford Warman®, it’s whether you can afford not to. alwayswarman.weir
as, say, financial services or retail, and mines with only a few years left to run may not see the benefit of new investment. However, as the cost of technologies has fallen and new mines begin operating where use of these technologies can be embedded from the start, so take up has increased.
What are the key regional variations that you see in terms of who are the adopters and who are the laggards?
Over the years we have generally seen mines in Australia lead the way in terms of investment and they have tended to have invested to a greater extent in drones, predictive maintenance and autonomous equipment compared with other regions. As far as other regions are concerned, it has varied depending on the technology – for example, mines in Asia lag behind in areas such as autonomous equipment and remote control.
How would you rate the overall adoption of technology in mining?
It is progressing well, particularly where it can have an impact on key areas such as productivity and safety. We have seen an increasing share of mines extend the degree to which they have invested in areas such as predictive maintenance, collision avoidance and fatigue detection, for example. Some
areas, such as autonomous equipment, will see much more selective investment in the short to medium term as they are more suited to particular operations.
What do you think is the biggest opportunity in the next two years?
We would expect an increasing share of miners investing in predictive maintenance,
“There are a wide range of benefits to investing in autonomous equipment, which is an example of how AI is being employed. Figures from OEMs and mining companies include 15-30% improvements in productivity, 80% reduction in accidents, 15-25% reduction in operating costs and 15% increase in machine life”
DAVID KURTZ RESEARCH & ANALYSIS DIRECTOR, GLOBALDATA
“Avoiding machine failures can save hundreds of thousands of dollars a year”
DAVID KURTZ RESEARCH & ANALYSIS DIRECTOR AT GLOBALDATA
even only partially, as they have gradually moved from reactive to planned to proactive maintenance and then predictive maintenance. It has become much more accessible because of the falling cost of sensors, improved computing power and bandwidth, and general technological advancements. Avoiding machine failures can save hundreds of thousands of dollars a year.
There is a lot of talk about AI, how are mines adopting that technology, and what benefits can it bring? There are a wide range of benefits to investing in autonomous equipment, which is an example of how AI is being employed. Figures from OEMs and mining companies include 15-30% improvements in productivity, 80% reduction in accidents, 15-25% reduction in operating costs and 15% increase in machine life.
Technology can be a great leveller, do you see smaller mines being able to close the gap on larger majors in terms of efficiency that they currently struggle to do? Yes, certainly. When we first began surveying mines in 2018, across the various technologies we asked about, on average non-majors had not invested 51% of the time. By 2023 this had fallen to 35%. In contrast, for majors it has fallen from 35% to 26% – so majors are still investing more of the time, but the non-majors are improving well. Looking at where mines stated they had either ‘’fully invested’’ or made ‘’considerable investment’’, the average share across all technologies has increased for non-majors from 15% to 33% between 2018 and 2023. For majors it has risen from 29% to 42%, principally helped by the declining costs and faster return on investment.
In today’s world, mining CEOs are making an impact on the global economy. This list of the top 10 most successful global mining CEOs includes some of the most influential and renowned figures in the industry. These figures rose to prominence through sheer dedication to their industry and developing business acumen.
Their passion for mining has been instrumental in propelling them to the top of their field and has enabled them to become leaders in both their respective companies and the global market.
Serving as a beacon of leadership and motivation for many, they demonstrate what can be achieved through consistency and determination.
German Larrea Mota-Velasco is one of Mexico’s top business magnates and he serves as the CEO of Grupo México, the country's largest mining corporation. He has chaired, served as president, and held the role of CEO since 1994. This is after a successful stint as Executive Vice Chairman from 1981 to 1989.
Larrea Mota-Velasco’s success is seen in one of his earlier ventures in 1978 when he founded Grupo Impresa, a printing and publishing company.
He received an undergraduate degree from Universidad Anáhuac México Sur.
Lai Chang Zou currently serves as the President and Executive Director of Zijin Mining Group Co., Ltd since December 2019. Prior to this, he held the esteemed position of Head-Production Division at Shanghang County Forestry and Chemical Factory. His educational background comprises an undergraduate degree from Fujian Agriculture and Forestry University and an MBA from Xiamen University.
With Chang Zou’s astute analysis and executive leadership, the company expects a prosperous future ahead, and recently broke into the Forbes top 300 global companies.
Richard Adkerson has been the President, CEO, and Vice Chairman of Freeport-McMoRan Copper and Gold Inc. since December 2003.
Under his guidance, FreeportMcMoRan underwent a dramatic transformation in 2007 with the US$26 billion acquisition of Phelps Dodge Corp. This move, a testament to Adkerson’s leadership, catapulted FreeportMcMoran to become the world’s largest publicly traded copper company.
In September 2018, Jakob Stausholm assumed the role of Executive Director and Chief Financial Officer at Rio Tinto, and finally took the helm as Chief Executive in January 2021.
His 20 years of experience in senior finance roles, having worked for both Maersk Group and Royal Dutch Shell plc, equip Stausholm with significant business and strategic insight which he puts to use in his current role.
Stausholm is a citizen of Denmark and holds a degree from the University of Copenhagen.
Change is hard. The truth is that many mining companies are still very hesitant about furthering their digital mining transformations in fear of cost of implementation, risk and uncertainty. However, digital solutions from AVEVA can help mining companies reduce complexity and optimize business and operational performance.
aveva.com
@avevagroup
linkedin.com/company/aveva
For more information, read our free E-Book on Digital Mining Transformation.
Since his appointment as its General Manager and Executive Director in March 2019, Zheng Gaoqing has been a respected figure inside Jiangxi Copper Company Limited. Throughout his tenure, he has demonstrated remarkable leadership and organisation skills, successfully managing several projects that have helped to further the company’s development. His expertise and dedication have been integral to Jiangxi Copper’s ongoing milestones. He holds a Masters in Business Administration from a prestigious university making him suitably qualified for the position.
Duncan Wanblad is presently Chief Executive Officer and Executive Director at Anglo American Plc and a board member of five other firms.
Wanbland joined Anglo back in 1990 and among his many achievement is the Quellaveco copper mine in Peru, which started producing in 2022, and was successfully developed thanks in large part to his leadership as head of Anglo’s copper division. He graduated with a degree in mechanical engineering from the University of the Witwatersrand in South Africa.
Born in 1964 in Brazil, Eduardo Bartolomeo has served as Vale’s Chief Executive Officer since 2019 where he focuses on health, safety, effectiveness, and productivity.
Bartolomeo played a pivotal role in structuring the logistics to support Vale’s operations while also devising two new strategic pillars for the company and is currently in the process of effecting a cultural transformation in order to make Vale one of the most secure and dependable mining companies in the world.
Gary Nagle is Glencore’s Chief Executive Officer, succeeding Ivan Glasenberg in the top post in July 2021. Nagle has had a long and illustrious career with Glencore, having joined the company in 2000. He has worked in a variety of roles across marketing and industrial businesses in multiple countries including Australia, Colombia, South Africa, and Switzerland.
His years of experience have enabled him to develop a deep understanding of the global commodities industry, giving him the necessary foundation to excel in his role.
Tom Palmer, who took up the role of President and Chief Executive Officer of Newmont in October 2021, is a seasoned leader and results producer. He had a successful 20-year career with Rio Tinto before joining Newmont.
In addition to serving as general manager of technology for the bauxite and alumina business, general manager of operations at the Hail Creek coal mine, and general
manager of asset management at the South African Palabora Mining Company, Palmer has held a range of positions across a number of commodities.
He is a renowned Monash University alumni who graduated with both a Bachelor of Engineering and a Master of Engineering Science. His commitment to creating a better and more diverse workplace has been demonstrated through a variety of initiatives, such as his efforts to establish and improve safety culture projects.
Palmer’s dedication to this cause is indicative of his pledge to making a lasting positive impact on the working environment.
Mike Henry currently serves as the the CEO and Executive Director of BHP, one of the world's largest resources companies, and has been a member of its Executive Leadership Team since 2011.
With over 30 years’ experience in the global mining and petroleum industries, he is a highly experienced and respected leader who is renowned for his discipline and focus. His extensive operational and commercial experience has been developed across the Americas, Europe, Asia and Australia.
Under his leadership at BHP, the company has seen significant growth and success in recent years. He has focused on improving operational performance while also returning substantial and consistent cash returns to shareholders. This achievement has resulted in increased shareholder satisfaction.
His efforts have allowed BHP to remain competitive and stay ahead of the industry, making Henry's leadership an invaluable asset to the success of the organisation.
6 - 7 September 2023
Business Design Centre, London
SPONSORSHIPS GET YOUR PASS