Selected Works
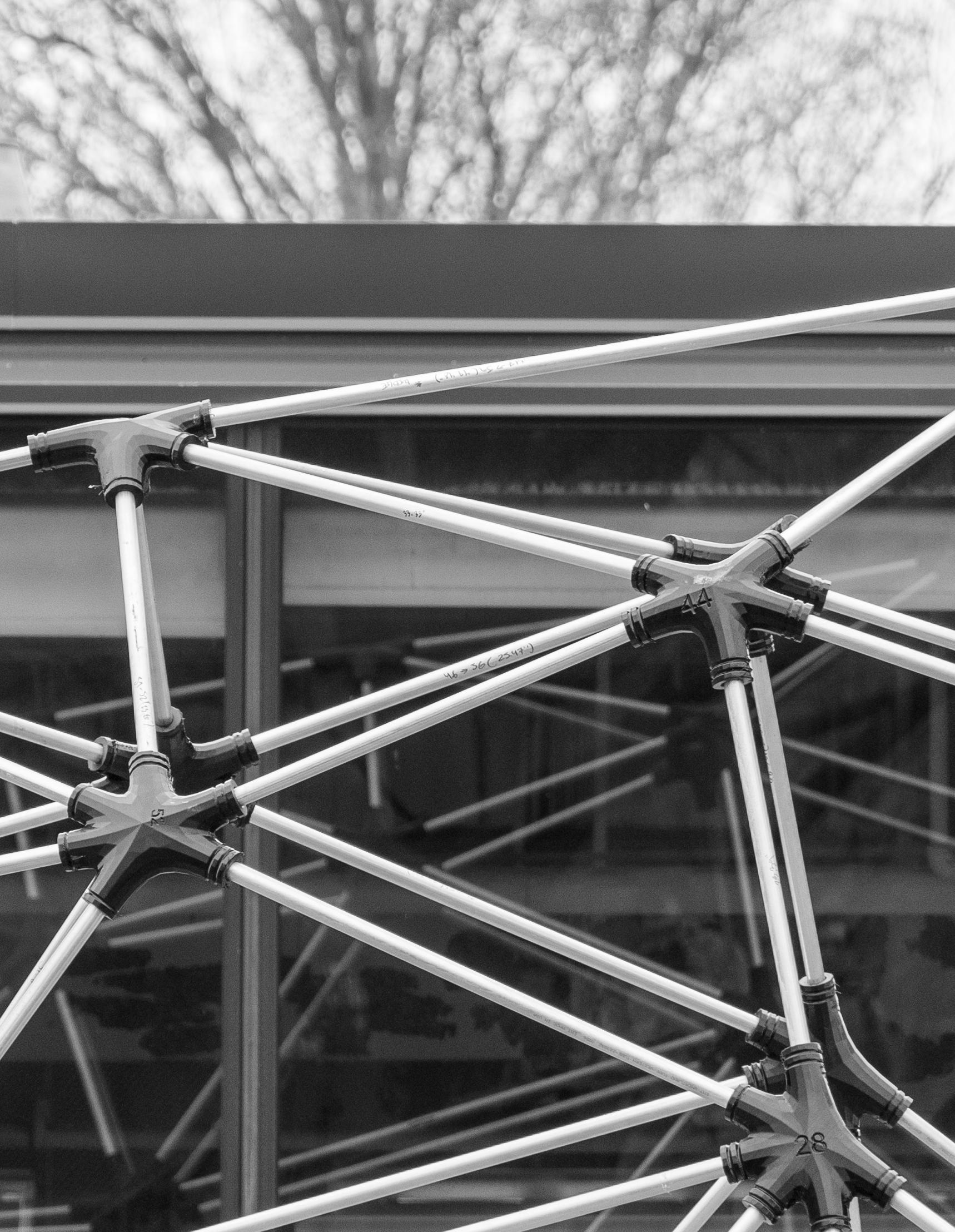
mkarkoutly@hotmail.com
https://mohammadkarkoutly.com/
(956) 280-2920
mkarkoutly@hotmail.com
https://mohammadkarkoutly.com/
(956) 280-2920
ARCH
This project seeks to find a convergence between standardized and 3D Printed materials to develop a process for designing and fabricating complex space frame assemblies that harnesses the inherent precision and adaptability of additively manufactured parts. When combined with widely available off-the-shelf components, this system reduces the material use, cost, and time needed to 3d print architectural scale structures.
This includes the development of a program that allows users to design their own structures using meshes, in addition to 3D printing the joints. The program is user-friendly, enabling the development of structures from low-resolution meshes or more complicated structures from high-resolution meshes. Enabling additional freedom in the design of the structure by employing a digital mesh, allowing for modification depending on unique demands and requirements placed upon the structure. This mesh can be designed as a structurally determinant form, or can be developed as a highly articulated, freeform structure that relies on external supports and structures.
Youtube Video: https://rb.gy/ifz3y
The final full scaled prototype took 22 days on a single 3D printer, spread over 3 printers the joints were finished printing in a week. 40 Kg of filament was used with only 3.5 Kg of waste generated. The primary filament type used in the project was TPU due to its elasticity and durability as it allowed us to solve the traingle problem that has plauged so many other joint projects. Triangulated scenarios within the pavilion are resolved simply by bending and shifting the tubes into the correct position due to the flexibility found within the system.
This project seeks to rethink the way we utilize topology optimization and robotic additive manufacturing within architectural design. By discretizing the componenets of the overall structure into a joint and tube construction, we can reduce the total material used and lower the fabrication time of the overall structure. This work would be used to create a quickly deployable temporary structure.
collaboration with Zach Darmanian-Harris + Zach Keller
Professor: Wes McGee
ARCH 581: Advanced Robotics Digital Material Processes
University of Michigan | Winter 2023
This work explores designing and programming a KUKA robot’s movements to create specific patterns and textures, as well as experimenting with material and color. The objective was to investigate how the robot’s precision and flexibility can be utilized to create intricate and unique surface textures on 3D-printed objects. A simple vase form was desconstructed in Grasshopper and a generative workflow was developed to create toolpaths for the extruded surfaces. A custom pellet extruder end effector and heated build plate were utilized to extrude a carbon fiber reinforced and a clear PETG. The resulting objects showcase the potential of robotic extrusion in the creation of visually and tactilely engaging 3D printed objects with a wide range of applications in design, art, and engineering.
Tha primary materials used in printing the vases was clear PETG and carbon fiber pellets that were oven dried and mix in varying quantities. The grasshopper script developed allowed for various design iterations that output varying toolpaths which were converted for the robot to start moving and extruding.
ARCH 703: Virtual Engagement
University of Michigan | Fall 2022
Coded assemblies seeks to create new architectural artifacts utilizing Python and Rhinoscript. This project allows for the creation of matrixes that can be manipulated randomly or be conformed to a more rigid and recognizable architectural assembly. The assemblies leave points and lines as remenants of the code’s logic embedded within each uniquely generated assembly allowing for a variety of iterations to be performed.
Geometric Coding Logics
In collaboration with Tharanesh Varadharajan + Zhijuan Liu
Professor: Catie Newell + Mark Meier
ARCH 700: MS Practicum
University of Michigan | Summer 2022
Light leak is about understanding the relationship between 2D cuts transforming to create 3D volumes. The project utilized the Zund, a CNC knife cutter, and an Adafruit Circuit Playground Bluefruit (CPB). The materials used was thin PETG sheets and Yupo paper. The two volumes were designed as a handheld lamp and lamp base. Once the lamp head is placed above the base they both light up showing they successfully docked. Different colors light up when in the vicinity to each other until they are linked.
Lantern Internals
In collaboration with Tharanesh Varadharajan + Zhijuan Liu
ARCH 700: MS Practicum
University of Michigan | Summer 2022
Material change is a continuation of the previous project, Light Leak. The material switch from a translucent and transparent materials to an opaque and less forgiving material such as 22 gauge steel required us to rethink how we would approach the design. The project still required the understanding of transforming 2D cuts into 3D volumes, however how does one re-adapt the previous form and envision it with a new material? Using the same CPB, we took the lantern portion of the project and reimagined it into a handheld lantern that is porous from the cuts into the steel surface. The sheets were bent and attached with a tooth and groove mechanism that allowed for the various components to be assembled.
Waterjet File Layout
In collaboration with Zach Darmanian-Harris + Jacob Brown
Professor: Dr. Mania Aghaei Meibodi
ARCH 708: Systems Engagement
University of Michigan | Fall 2022
Hangprinter is an open-source FDM 3D printer most notable for having a frameless design. Developed by Torbjørn Ludvigsen, the hangprinter is a relatively low cost printer. The focus of this project was to develop, test, and recreate the Hangprinter based off the model, plans, and wiki info available. Although the printer is of a frameless design, a custom frame was create to allow for deployment anywhere using 3D printed joints and steel tubes.
The hangprinter took 3 days of printing all the componenets on a single 3D printer. All the 3D printed components were printed using PETG because it is stronger and durable than PLA.
It has a print volume of 1.5m x 1.5 m x 2.5 m. The printer uses a mainstream slicing software, prusaslicer, to be able to create the gcode necssary for 3D printing. However, custom gcode can be uploaded and used to 3D print as well.
In collaboration with Dishant Patel
Meibodi ResearchProfessor: Dr. Mania Aghaei
Work University of Michigan | Fall 2022
Developing a paste extruder for a robot involves designing and building a mechanism that can accurately dispense and control the flow of a viscous material, such as pastes, biomaterial, and clay, through a nozzle. The extruder must be compatible with the robot’s existing hardware and software, and must be capable of maintaining a consistent extrusion rate and pressure. The design of the extruder was developed by Bryan Cera’s open source projects where he designed and tested the mechanical system. The software and eletronics portion was developed independently and made custom to fit DART lab’s needs. The extruder runs a 30:1 worm gear drive which allows for a steady and continous depostion of materials such as clay, concrete, and biomaterial. The end effector eventually became a fundamental tool in the test of various research projects within the lab.
In collaboration with Kyle Zhang + Grace Shanks
Professor: Sora Key
Arch 5602: Architectural Design Studio
Texas Tech University | Spring 2021
A health clinic that was developed to serve the under-resourced communities of Lubbock’s East side neighborhoods. This preventative health clinic will allow diseases to be detected earlier and diagnosed in order for both adults and children to be treated and to provide medical accessibility within the area. By using the sites natural scenery such as the lake as a focal point in connecting the occupants and staff to nature as a healing property. Environmental lungs are placed throughout the facility to allow staff and patients to become constantly engaged with nature.