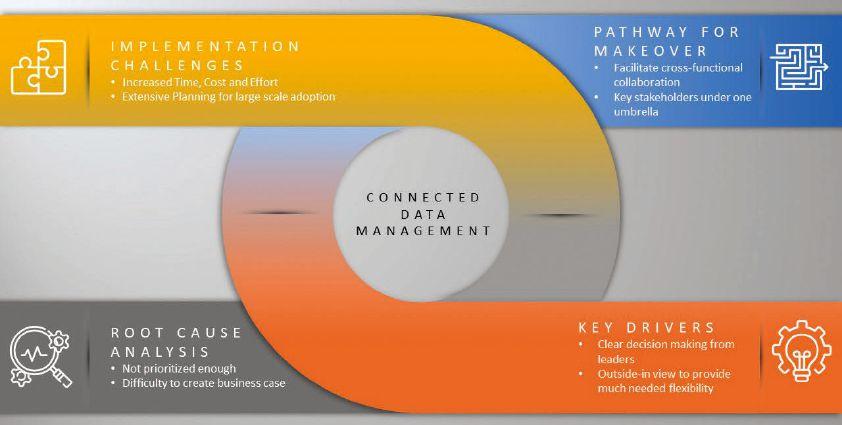
6 minute read
Better data during COVID-19
Sanjay Barnwal, Sanjay Barnwal, L&T Technology Services
Better data management for manufacturers during COVID-19
Advertisement
Will COVID-19 compel manufacturers to streamline connected data management?
‘As engineering
project timelines, costs and efforts start escalating and pressure builds, teams start returning to old manual interventions.’
Decision-makers and executives understand the value and need for modelbased design (MBD), model-based engineering (MBE), and model-based systems engineering (MBSE). These have existed for decades and enabled thousands of high quality and extremely complex product design, development and support activities. Many projects are unable to apply the concepts for full product lifecycle right from design, development and manufacturing to support engineering activities. The result is disjointed systems, significant manual interventions with time to market impact, poor quality, high cost of ownership and poor customer satisfaction.
Product lifecycle management (PLM) systems are still widely used as document management systems across enterprises for storing engineering artifacts. Quality aspects in the product design stage are managed in separate systems, processes, and often through Microsoft Excel and Word documents linked to PLM or other engineering systems.
Reality of engineering transformation
Before COVID-19 disrupted industries globally, engineering transformation programs did not guarantee success because of the perception vs. reality factor.
A. Real life vs. perceived values: Most of the new engineering programs start with the intent to follow the great design principles and methodologies with an understanding of great value. As the project timeline, costs and efforts start escalating and the pressure builds, teams start returning to the old ways of manual interventions. Newer ways take up too much of time, budget and efforts and may carry perceived risks.
B. Live for today or sacrifice some for tomorrow:
Leaders and executives have businesses to run. Disruptions with newer tools and technologies require upfront planning, communication and commitments. This is why, except for some areas (pure R&D, proof of concepts [POCs], digital technology groups), MBD, MBE and MBSE remain in beginning stages within engineering organizations. It’s no wonder they do not move to manufacturing, maintenance and repair operations (MRO) and aftermarket areas.
Getting to digital transformation
Engineering and aftermarket leaders understand the value that comes with connecting engineering data to aftermarket for spare parts leaflets, associated technical documents, training materials, videos, effective field performance analysis and improvements. In most cases, the concepts just stay on paper and seldom are implemented. Similar initiatives on making factories paperless, and generating a manufacturing bill of material (mBOM) from an engineering bill of material (eBOM) in a connected way, and performing virtual tooling, manufacturing and simulation activities to detect and fix issues early on remains a wish-list for many operation leaders. Key decision-makers of business units are optimistic and frustrated with the pace of transformation and outcomes these initiatives are generating.
Some manufacturing plants have large-scale capital investments in robotics and automation. In some areas multi-million-dollar machines may reallocate workers with a $25-per-hour wage. Such robotics and automation projects are getting approvals. While critical data management projects that promise longterm value have been shelved off, automation and robotics have gained steady acceptance. Is automation a priority because a business case for headcount reductions is easier to create and understand? Is it difficult to create a business case for productivity, cost-avoidance opportunities and investments for linking engineering data models to manufacturing?
The answers lie in addressing the fundamental challenges of how current teams are structured to meet cross-functional transformation needs.
Driving digital transformation
At an MRO facility for a tier 1 automotive customer, it was surprising to see the engineering team unaware of how to access 3D models of PLM system parts. Engineers were working with an outdated drawing and instructions. If a manufacturing plant works with Industry 4.0 technologies, it must do so with deep involvement. Even with the best intentions, engineers who are busy with activities only can provide part-time support to manufacturing plants. Mainstream companies need to overhaul structures to facilitate cross-functional collaboration.
IT/OT, digital transformation
Standalone functions such as engineering, manufacturing, aftermarket, MRO, digital and even information technology (IT)/operations technology (OT)
Connected data management graphic explains implementation challenges, rootcause analysis, key drivers for change, and the pathway for improvement. Courtesy: L&T Technology Services
M
More
can be consolidated in one engineering division. A ing mundane POCs, experimentation and debates new structure can have better chances of success. about the connected data management journey. 1. Engineering, manufacturing, MRO, and after- When radical organizational changes are to be market as standalone functions are siloed. Merging implemented, management consultants come into each function can facilitate a seamless flow of data the picture frequently. This is not because they know between disparate and disjointed processes. The more than company leadership. Management conteams can replicate standard operating procedures sultants bring an outside-in view while working on (SOPs) and leverage best practices and a given timeline with set objectives. They are flex-
INSIGHTS technology in tandem to drive long-term value. ible to work with and don’t come with preconceived notions of what’s possible and what isn’t. This is why KEYWORDS: COVID- 2. If a manufacturing plant has to organizations should explore collaborations with 19, manufacturing, data management Money for robotics and automation continue to flow in the pandemic, but data work with 3D models for work orders, virtual tooling, testing then the manual process changes in the factory can’t happen without deep engineering consulting organizations for data management initiatives. With a support system for requirement gathering to design, develop, and test, management consultants can ensure the success of a data managemanagement funds have slowed involvement. ment project end-to-end. for manufacturers. 3. MRO and aftermarket functions Productivity for Industry 4.0, also need constant engineering support to Looking beyond COVID-19IIoT digital transformation requires streamlined data integration for manufacturers. drive seamless data management. Transformation project capital has slowed. Kneejerk reactions are natural where key supplier resources Lack of data connections result Help digital transformation and employees are getting laid off and only essentials in disjointed systems, significant For this restructured organization, are getting done. This is where supplier, non-core manual interventions with time the strategic and decision-making func- activities consolidations can free-up funds, and key to market impact, poor quality, high cost of ownership and poor customer satisfaction. tions need to happen at the top, and then respective teams can figure ways to move forward. The company also will have to resources can be funneled for technical data management transformations. Enterprises will need to rely on integrated data management to plan and structure CONSIDER THIS incur added costs of maintaining multiple organizational blueprints. What data integration initiatives would improve manufacturing productivity? technologies, tools and platforms. With thorough planning, companies can reduce valuable time lost in creating mundane Data is a strategic weapon and backbone of Industry 4.0. Everything depends on data, its seamless exchange and effective use. Organizations need to cap-ONLINE POCs figuring out which path to take in italize on this crisis, a stress test for transforming techIf reading from the digital edition, click on the headline for more resources. www.controleng.com/magazine www.ltts.com See the L&T Electrical & Automation listing in the Global connected data management journeys. No matter which tool, platforms and solutions are chosen, there will always be soft corners and shortcomings in meeting and satisfying all needs. This is where executives need to use the 80/20 rule, make nical data management and capabilities. ce System Integrator Database. clear decisions and save teams time, avoidSanjay Barnwal is vice president of transportation and aerospace at L&T Technology Services, a Control Engineering content partner. Edited by Mark T. Hoske, content manager, Control Engineering, CFE Media and Technology, mhoske@cfemedia.com.