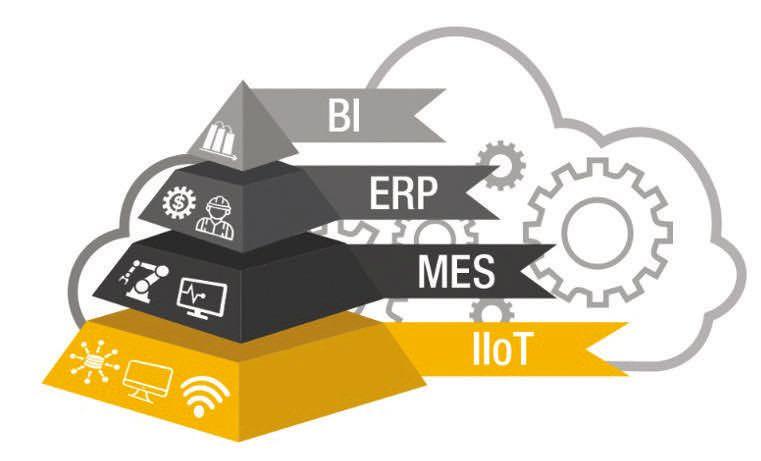
16 minute read
Maintenance automation create a new recipe for data integration
Brian Harrison, CRL, Fluke Reliability
Maintenance automation: Data integration, a new recipe
Advertisement
To get top ROI for digitalizing asset maintenance, consider a modern version of the automation pyramid using ISA-95 Enterprise-Control System Integration.
Process manufacturing has reaped automation’s benefits for decades. Under the guidance of ISA-95 Enterprise-Control System Integration from International Society of Automation, organizations looking to adopt automation standards-based best practices. As new technologies emerge, there are more ways to apply the automation standard.
Under Industry 4.0, digitalization has spawned countless new manufacturing technologies and systems, in departments and industries far outside process manufacturing. These include:
• Service-oriented architecture (SOA). It is considered crucial for the success of complex enterprise resource planning (ERP) systems and has many advantages for integration, extensibility, agility, and reusability.
• Industrial Internet of Things (IIoT). This technology is no longer a buzzword; it is changing how we monitor and interact with critical equipment, such as smart sensors.
• Wi-Fi and digital networks. These are becoming a primary alternative for industrial connectivity, with 5G wireless networks commonly discussed as a promising technology to enable ubiquitous and scalable connectivity to the shop floor for industrial wireless communications.
• Big Data, edge computing, robotics, artificial intelligence (AI), machine learning, application program interfaces (APIs) and augmented/virtual reality (AR/VR). These have moved from concept to pilot and will be ready soon for broader adoption.
Moving technological growth forward was challenging enough, but then the COVID-19 pandemic hit. The disruption from COVID-19 is fueling urgency among plant managers for system improvements previously viewed as “future considerations.” Remotely monitoring asset condition, for example, has gone from a “want” to a “need” – something essential to be effective in the near term and competitive over the long run. As of late summer 2020, some 82% of maintenance organizations were considering how to effectively add or increase digitalization technologies, according to Fluke Reliabil-
ity research. Meanwhile, more than 35% Mhave experienced at least a quarter drop in production, with only 15% operating as “normal.”
Many of these companies understand how automation could deliver a valuable step change in their day-to-day operations. Many previous IIoT pilots have failed to live up to expectations. Sometimes this was due to system conflicts, technology limitations, or, more often, gaps in communication and change management.
Today’s manufacturing environment is leaner than usual. Planners seek to optimize initiatives to their fullest extent so when people are working on-site, work is prioritized and executed based on how it fits into the big picture.
To do this effectively, teams need more than tribal knowledge or ad hoc standard operating procedures. They need a better framework for successful digitalization. More
ANSWERS KEYWORDS: process
manufacturing, automation pyramid, maintenance automation
The ISA-95 automation pyramid was originally designed to help process manufacturers. The pyramid can be adjusted for the Industrial Internet of Things (IIoT) and help other manufacturers. A maintenance automation strategy should increase the team’s ability to rely on condition-based maintenance (CBM). ONLINE See more about optimizing equipment lifecycles, ROI and augmenting the field technician. CONSIDER THIS What benefits could your company derive from the maintenance automation pyramid?
Figure 1: The ISA-95 automation pyramid. Images courtesy: Fluke Reliability
ISA-95 and the automation pyramid have provided a critical framework for automating the interface among five levels of enterprise and control systems: 1. Physical production processes 2. Sensors 3. Monitoring and supervision 4. Manufacturing operations management 5. Business planning and logistics.
ISA-95 was developed because the differences across industries, systems, departments and objectives made it challenging to communicate and collaborate. Businesses suffered in the absence of a common language. Now in its 35th year, ISA-95 continues to be revalidated and incorporated into more technologies. Many of these technologies and programs continue to focus on process manufacturing.
Automation system integration
Proven systems-integration thinking is needed now outside of process manufacturing. By extending the ISA-95 framework to other industries, many
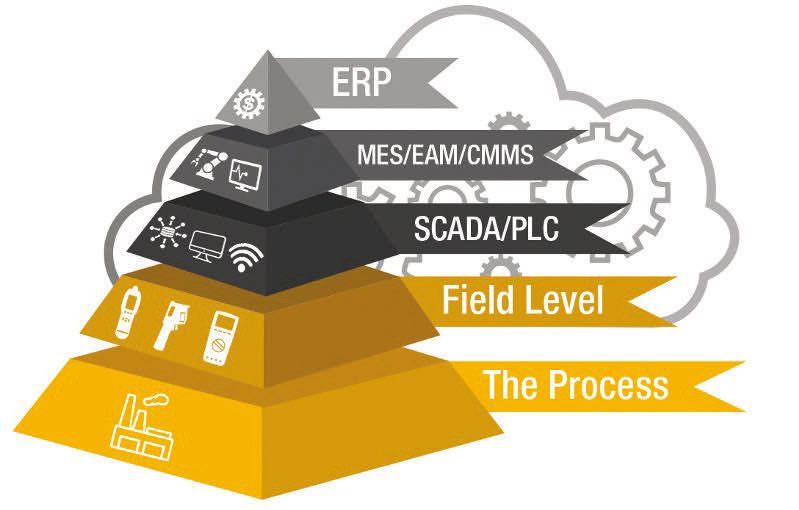
Figure 2: The maintenance automation pyramid, adjusted from the original ISA-95 version.
Manufacturing automation pyramid levels
Reference Figure 2, above.
Level 1: The process
• This layer includes the physical assets, the maintenance and reliability teams (M&R) that care for them, and the machine operators. • Some assets are wired or wirelessly connected, while others operate out of visual management.
Level 2: Field-level tools and sensors
• Equipment-level tools and sensors provide manual as well as automated readings; not all data from un-connected measurement devices is currently saved or tracked, and not all sensor data is in a useful format. • Wireless sensors applied to legacy machines are bringing a more significant percentage of assets into electronic view.
Level 3: Supervisory control and data acquisition (SCADA)
• While most manufacturers employ SCADA/programmable logic controller (PLC) systems, less than 30% can use this information for asset management. • Early artificial intelligence (AI) studies of SCADA data lakes are finding applicable health indicator data for triggering work orders, creating the potential for meaningful real-time, early-detection work orders.
• Integrating level-3 SCADA data into the maintenance automation/enterprise asset management (EAM) framework improves overall equipment effectiveness (OEE) and mean time to repair (MTTR). It also reduces downtime and supplements skills shortages by helping automate work order creation and prioritization.
Level 4: Enterprise asset management (EAM)
• The EAM or computerized maintenance management system (CMMS) is the M&R system of record. • Integrating the EAM with the maintenance automation framework supports shifting work from calendar- to condition-based PMs, prioritizing work based on actual asset status. • Tying meaningful data to the asset management system equates to a step-change in the quantity and quality of data informing daily decisions.
Level 5: Enterprise resource planning (ERP)
• Integrating layers 1 through 4 into the company’s primary business layer feeds accurate M&R data into the overall financial accounting and reporting system. It increases the visibility of M&R contributions to the company’s bottom line and empowers data-driven decision making at the plant management level. • Key metrics include total cost of ownership for assets and cost comparisons between planned versus condition-based work.
can achieve the same benefits from yield improvements to cost reductions.
Automation thinkers often use a pyramid to show the interaction between levels. The automation pyramid in Figure 2 is updated to include the IIoT at the physical layer. What if the automation pyramid was adjusted to reflect the levels or layers found in manufacturing operations in nonprocess industries? It might look something like Figure 2. The pyramid’s layers help identify the data points from various subroutines useful to aspects of the overall system. Reconfiguring the pyramid to support maintenance and reliability operations (MRO) adds a “process” layer at the bottom. It adjusts the other levels to reflect maintenance interactions with the larger plant and organizational architecture.
With the proper framework to support internal collaboration and integration, digitalization could better help pull operations through times of tight resources. But, just like in 1995 process manufacturing, ROI must be a central consideration from the beginning. For the pyramid to be useful, it has to help maintenance leaders identify where connected systems will have the most significant positive impact at their facilities.
Applying the framework
In most facilities, the more connected maintenance and operations teams become, the more benefits their actions generate. Consider the process of troubleshooting a particular asset. Technicians may take a variety of measurements to get to the root cause of an issue, but they use those measurements only at that moment. If this data can be preserved in the asset’s health history, it contributes to the broader maintenance strategy for the machine – potentially adjusting how often specific parameters are checked, contributing to fewer unplanned failures, and extending an asset’s overall lifespan.
In the long term, a maintenance automation strategy should increase the team’s ability to rely on condition-based maintenance and decrease the number of calendar-based PMs, saving labor and parts cost to safety. It can be a difficult transition. Clear communication, change management and partnership are essential. ce
Brian Harrison, CRL, is industry lead for IIoT at Fluke Reliability. Edited by Chris Vavra, associate editor, Control Engineering, CFE Media and Technology, cvavra@cfemedia.com.
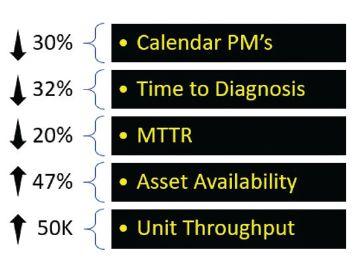
Figure 3: Short-term automation goals and ROI.
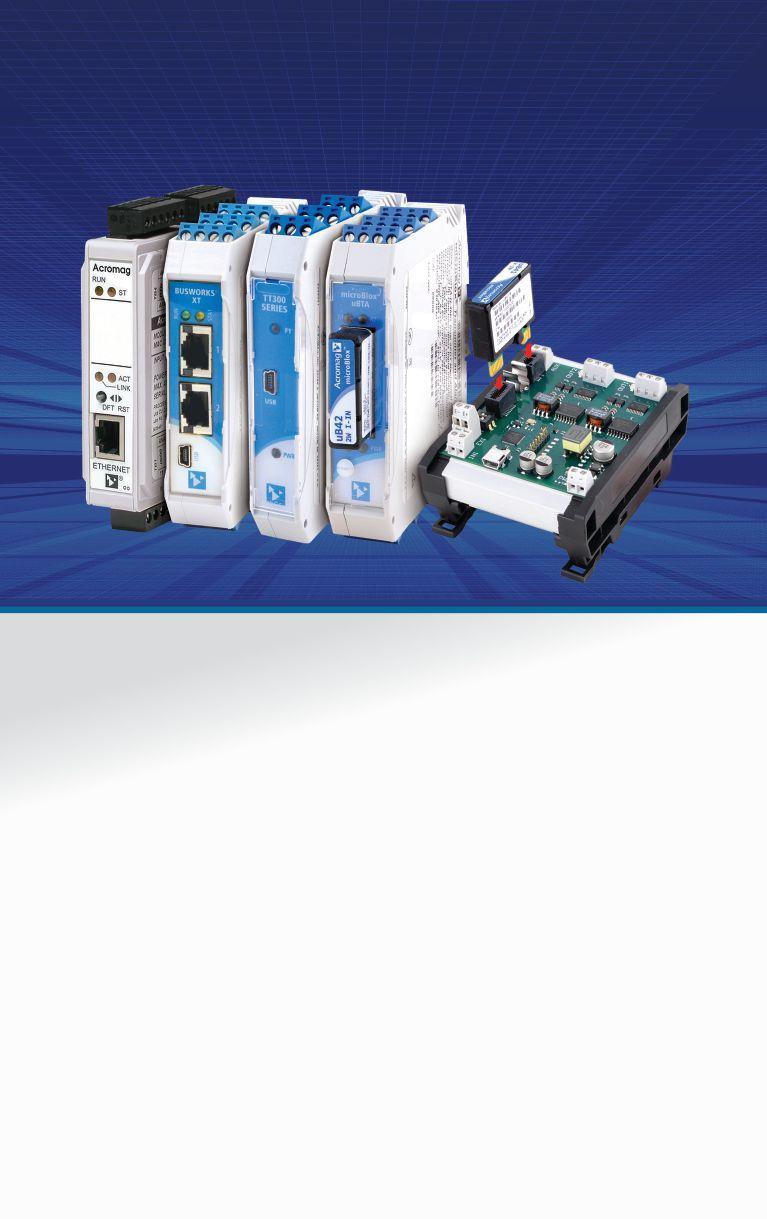
Because We Know I/O
You Get Personalized Support- Guaranteed
You can trust Acromag for all your signal conditioning and remote I/O solutions. You can be confident that with our more than 60 years I/O experience that you will get professional personalized support – guaranteed.
Acromag’s signal conditioning line features more than 100 transmitters, isolators, alarms, and computation modules. If networked I/O is required, Acromag offers analog and discrete I/O modules for Ethernet, Modbus, and Profibus.
Products Designed for Dependable Value
877-295-7057
Visit Acromag.com/IOSolutions TO SEE WHAT’S NEW
Allen Kern, P.E., APC Performance LLCAllen Kern,
Changes in store for advanced process control
Closed-loop multivariable control brings greater timeliness and consistency, fewer alarms and constraint violations and more effective process optimization.
Multivariable model-predictive constraint control and real-time optimization, better known as MPC technology, has had a very good run. It has dominated advanced process control (APC) for several decades, to the exclusion of most other types of APC activity. Operating companies have invested tens of millions of dollars in MPC (hundreds of millions or billions collectively) and earned millions of dollars in return.
Multivariable controls changes needed
The attractive promise of closed-loop multivariable control and real-time optimization has meant users have stood by their commitments to MPC for decades, even though its high costs, fragile performance, and complex ownership demands have persisted, rather than improving over time. The conventional MPC technology ownership paradigm increasingly is considered unsustainable. MPC has proven too expensive and unwieldy to form the centerpiece of a multivariable control core competency, which the manufacturing industry needs. Accumulated experience now suggests changes in the industry’s multivariable control paradigm may hold more promise than continued efforts to fix and overcome conventional MPC’s challenges.
Multivariable control is fundamental
MPC technology can be said to comprise three parts: model-based control, real-time optimization and multivariable control. For APC purposes, multivariable control is the essential piece (noting that optimization, though not necessarily real-time optimization, is always part of multivariable control – see sidebar). Model-based control and real-time optimization are part of the way MPC technology solves the multivariable control problem, but experience has revealed there are other simpler ways to solve multivariable control that don’t require these elaborate methods.
MPC has often been shrouded in complexity. A simple way to view multivariable control is it automates the single-loop controller adjustments (setpoint and output changes) that otherwise are left to the operating team to manually implement. When operators make controller adjustments in the course of a day – of which there are often many – that’s manual multivariable control. When APC is applied to better coordinate and automate those adjustments for groups of related controllers, that’s automatic (or closed-loop) multivariable control. Like single-loop control, closed loop multivariable control brings the inherent benefits of greater timeliness and consistency, fewer alarms and constraint violations, and more effective process optimization. In many applications, this can earn hundreds of thousands or even millions of dollars annually.
When operating teams carry out manual
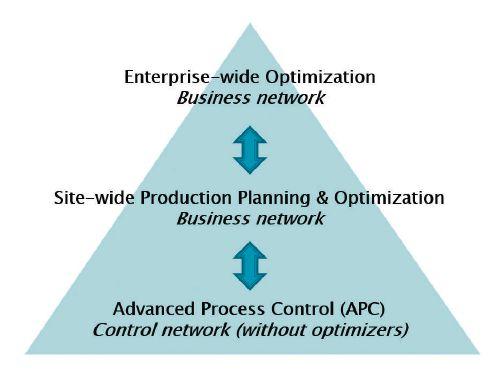
M
More
ANSWERS KEYWORDS: Advanced process
control (APC), model-based multivariable control (MPC)
LEARNING OBJECTIVES Discover why changes are needed in multivariable controls.
Learn why automatic
multivariable control is better than manual multivariable control. Understand the need for multivariable competency for better process automation. CONSIDER THIS
Is your software improving or decreasing process efficiency? ONLINE
If reading from the digital edition, click on the headline for more resources. www.controleng.com/ magazine “Feedforward: Not as popular as expected, again”
Figure 1: Business layer production planning is the natural home of process optimization. At the control network layer, optimization has been in conflict with mission criteria principles in terms of reliability and cybersecurity and is likely to disappear from the control network layer. Images courtesy: APC Performance LLC
‘Multivariable
multivariable control, they do it without the aid of detailed process models and real-time optimizers. This shows how automatic multivariable control also can be solved without detailed models and real-time optimizers by automating proven methods that have always been manually employed by operating teams. (See later Figure 1 explanation.)
Not only are model-based control and realtime optimization dispensable to the central objective of multivariable control, but experience and insights suggest they may be undesirable aspects of the control network layer going forward.
Model-based control has been a huge source of costs and maintenance. It was originally anticipated that a plant step test, though expensive and intrusive, would be a one-time event. As experience accumulated that models are actually short-lived, the need for performance monitoring, model maintenance, and periodic retesting arose.
MPC technology today is pursuing continuous online adaptive modeling, but this overlooks the lesson industry has already learned from single-loop auto-tuning – if auto-tuning was not successful on a single-loop basis, it is not likely to be successful on a multivariable basis. Meanwhile, it adds yet another layer of ownership cost and complexity to MPC.
Local control network optimization
Real-time optimization has been another persistent source of MPC ownership challenges, so the valueadded proposition of deploying real-time optimization at the control network layer warrants new scrutiny.
Optimization within the control network layer is localized at best, encompassing a small handful of locally-available inputs. The vast majority of data inputs needed for meaningful process optimization reside throughout other process units, the business network, and the enterprise. In modern plants, the business production planning function is the natural locus of process optimization, not the control networks (Figure 1). Industry has also seen that only limited amounts of data, in the form of updated limits or targets, actually need to flow from the business layer down to the control network, which is accommodated by modern tools and connectivity.
The resources, complexity and maintenance to run massive model-based control and real-time optimization at the control network layer has largely proven incompatible with the mission criteria of industrial automation networks. In the control network layer, compact deterministic algorithms with minimal inherent maintenance and support needs are the desired characteristics for automation reliability, network reliability, and cybersecurity objectives. Deploying complex model-based control and optimization solvers with high ongoing maintenance and support burdens into the control network conflicts with these principles.
MPC is a core-competency
Figure 2 compares key aspects of the conventional MPC paradigm and an updated multivariable control paradigm based on industry’s lengthy experience. The updated paradigm has already been emerging by industry consensus, though commercially available off-the-shelf products as yet remain limited.
Many aspects of the conventional MPC paradigm are fundamental to multivariable control and will carry forward into the new paradigm, such as the concepts of manipulated variables (MVs), controlled variables (CVs), the matrix, limits and targets. At the same time, other aspects of MPC the industry has been accustomed to, such as plant tests, detailed models and real-time optimization, may disappear from APC going forward based on an updated assessment of their net pros and cons.
A central aspect of multivariable control is it becomes an industry core-competency, which is desperately needed, because industry can now see multivariable control is a core aspect of almost every process operation (ask any operator). This means multivariable control is as fundamental to successful process operation as good single-loop control.
Multivariable control must evolve into a corecompetency to move process automation to the next level. This is in the best interests of all APC and process operation stakeholders. ce
Conventional MPC paradigm
MPC is solved using relatively elaborate methods – detailed process models and real-time optimizers – leading to high cost and fragile performance.
Multivariable control is highly specialized, necessitating special budgets, planning and resources.
Benefits are large, but frequently fragile, especially in absence of continuous maintenance and support.
Real-time optimization resides in the control network, which may be inappropriate for automation reliability, network reliability, and cybersecurity purposes.
Applications are typically limited to “large matrix” applications, in order to meet the high cost threshold of MPC technology.
Updated multivariable control paradigm
Multivariable control is solved by automating the relatively simple and robust methods that have always been used by operating teams manually.
Multivariable control is a core-competency, falling within normal operating budgets, schedules, and control engineering resources.
Multivariable control brings the same inherent benefits as single-loop control – timeliness and consistency, fewer alarms, greater optimization.
Optimization results, to the extent real-time or periodic updates are necessary, are leveraged from the business layer solution.
Multivariable control is more affordable, agile and scalable, making it available for industry’s many “small matrix” applications, too.
Figure 2: Attribute table of model-based multivariable control versus updated multivariable control suggests why changes are needed.
Allan Kern, P.E., is owner,APC Performance LLC. Edited by Mark T. Hoske, content manager, Control Engineering, CFE Media and Technnology, mhoske@cfemedia.com.

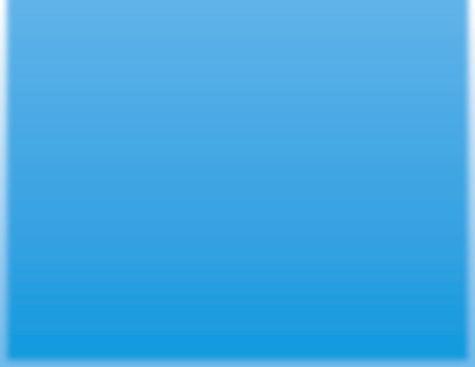

OPTIMIZATION – though not necessarily real-time optimization – is always a part of multivariable control. Multivariable control is a two-dimensional multiloop control strategy that does not aim for a single operating point. Instead, it aims to keep process operations within a twodimensional operating window, bounded by process constraint limits. Multivariable control also uses remaining MV availability (also known as remaining degrees of freedom) to pursue optimization targets to the extent possible within the window.
The vast majority of optimization target and constraint limit values are entered into the multivariable controller by operators and engineers, just like singleloop controller setpoints and limits. Where appropriate, some target and limit values may be periodically updated from the business layer optimization solution (Figure 1). Target and limit values also may be deter-
mined in “real time” by optimization solver programs deployed within the control layer in conjunction with multivariable control – this is known as real-time optimization within traditional model-based multivariable ‘ Real-time optimization conflicts with control network mission cricontrol technology (MPC). Control layer (that is “real time”) optimization made sense in the 1980s, teria; deterministic algorithms and when optimization tools in the business layer were minimum maintenance are impor- less automated and contant principles for network reliabil- nectivity between the begin to ity and cybersecurity.’ compare with layers was almost nonexistent. Today, control layer optimization cannot business layer optimization in terms of globality of inputs, sophistication of tools, and appropriate optimization time scales. Experience also has shown real-time optimization to be in conflict with control network mission criteria because deterministic algorithms and minimum maintenance are important principles for network reliability and cybersecurity purposes.
MONITOR VISCOSITY SIMPLY
SENSE MIXER MOTOR HORSEPOWER WITH UNIVERSAL POWER CELL
EASY INSTALLATION
• No holes in tanks or pipes • Away from sensitive processes
VERSATILE
• One size adjusts to motors, from small up to 150hp • Works on 3 phase, fi xed or variable frequency, DC and single phase power
SENSITIVE
• 10 times more sensitive than just sensing amps PROFILING A PROCESS
24
22
20 • Power changes refl ect viscosity changes • Good batches will fi t the normal “profi le” for that product
POWER DECREASE SHOWS BATCH IS DONE
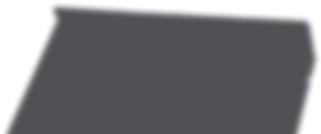
18
16 POWER SENSOR
CONVENIENT OUTPUTS
• For meters, controllers, computers 4-20 milliamps 0-10 volts
14
12
10
8
6
4
DRY MIX HIGH SPEED ADD LIQUID LOW SPEED
BEGIN HIGH SPEED MIX MIXER MOTOR
2
0
BATCH 1 BATCH 2 BATCH 3
CALL NOW FOR YOUR FREE 30-DAY TRIAL 888-600-3247