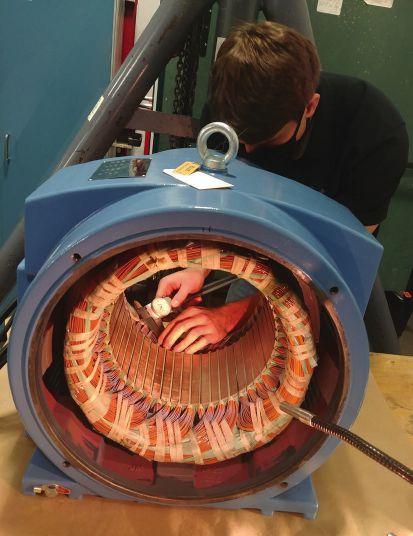
13 minute read
Motors and drives: Tips and tools for efficient motor management
Michael Lyda, Advanced Energy
Webcast presenter answers more motor management questions to improve process reliability and reduce energy costs.
Advertisement
Motor-driven systems account for about half of all electricity generated in the world and are likely the biggest energy users at your facility. Reducing energy costs by improving these systems can be simple with improved motor management practices.
In a recent Plant Engineering webcast, available in its on-line archives, Michael Lyda, motor and drive engineer, Advanced Energy Corp. shared his expertise with attendees. He discussed how to streamline motor management practices, quickly improve process reliability and reduce energy costs.
Following the presentation, Michael answered questions from the audience. Below are the questions, and Michael’s responses, that he was unable to address during the webcast because of time constraints.
The audience asked about purchase specifications and lifecycle cost analyses for electric motors, and operation and maintenance best practices. Variable frequency drives (VFDs) were also covered, including basic operation, energy efficiency benefits and potential applications.
Figure 1: In a typical client witness test at Advanced Energy, clients witness testing at the lab and multiple engineers participate. Images courtesy: Advanced Energy
Question: Please elaborate a bit on what you referred to as the life of the VFD.
Lyda: Like motor life, VFD life depends on both environmental and operating conditions. Keep the VFD in an ambient temperature within its specification. Keep the cooling vents unblocked. Make sure the fan works as it is supposed to. One thing to note on the VFD fan is that it may cycle on and off in operation depending on current draw. Higher current will cause the VFD heatsink to heat up more, so the fan may not be running at lower loads. There are also maintenance best practices to follow for your VFDs, and I recommend consulting the manufacturer on those.
Q: Please compare the lifecycles of induction and PMAC inverter-driven motors.
Lyda: Commercially available permanent magnet alternating current (PMAC) motors are relatively new in this market. Although the designs have been around for many years, they have typically been built by special order only. Many manufacturers will have them in their catalogs these days, but they can be quite expensive and have very long lead times. We have completed testing at our lab on some PMAC motors but only for efficiencymapping and not for lifecycle or reliability. I would also be interested in those results if test data is out there.
Q: Is there a software tool for efficiently figuring real power consumed by a motor?
Lyda: Most measurement devices should come with some type of software. We use Yokogawa high accuracy precision power analyzers in our lab with National Instruments data acquisition hardware and LabVIEW software. One meter I like to use in the field for metering and verification is a Fluke
COVER: Figure 2: Large dynamometer is used for testing. It is rated for up to 300 hp output at 1800 rpm. The motor coupled to the dynamometer in this photo is a 200 hp engine.
355. It will give you voltage, current and power factor. It is more expensive than a standard multimeter, but you can get real power data since you are acquiring the power factor also.
Q: We have acquired a 250 HP AHU that will be equipped with a VFD. Is there any maximum distance that applies from the VFD to motor? Also, do I need filters for the harmonics?
Lyda: For this specific application, I would recommend consulting the VFD manufacturer. They can best advise on cable length and ancillary equipment needed, whether it be a line filter, DC choke, load filter or other.
Q: What is the maximum cable distance between an ac motor and a VFD?
Lyda: This is all relative to the application. The shorter, the better, since longer cable lengths will lead to higher peak voltage at the motor terminals. Consult the VFD manufacturer on a case-by-case basis.
Q: What are the differences between a “motor management relay” and a “motor protection relay”?
Lyda: I have limited experience with these, but I think motor protection relay refers to a current overload relay that focuses on current alone. A motor management relay is more involved and may have capabilities to monitor current and voltage. Thus, phase sequence, overvoltage, undervoltage and voltage unbalance could all be monitored by this type of device. Advanced Energy has completed testing and research on two types of these devices in the past: phase monitors and overload relays. If you would like more information, please contact me.
Q: Should we consider service factor for calculation of overload?
Lyda: Service factor is meant for short-term overloading. If you run a motor at its service factor (e.g., 1.15 or 1.25) continuously, it will not likely last as long as it will at its rated load.
Q: Please address motor cooling fans on VFDs. What is the minimum speed before needing a separate fan motor to cool the VFD motor? Does installing VFDs impact plant power factor?
Lyda: This will need to be looked at for each application. Inverter-duty motors should have constant torque (CT) and variable torque (VT) ratings on their nameplates. As long as your load is within these limits, additional external cooling should not be needed. If operating the motor outside of these speed/torque ranges, the motor manufacturer should be consulted. Installing VFDs adds capacitance to the system, so if you have a primarily inductive load at the moment (i.e., a lot of motors), your power factor would likely be improved by adding VFDs. If your main loads are lighting, other capacitive sources or purely resistive sources, then VFDs will not improve the power factor, and could even make it worse.
Q: Will an over-dimensioned motor, driven by VFD, also exhibit a low power factor?
Lyda: Tough to say. A motor that is oversized for an application will generally exhibit a low power factor since the magnetizing current plays a larger role in the total current draw. However, when you add a VFD, the capacitance of the system is greatly increased, so the power factor will be increased across all loads. I am not sure by how much, though. We really could use some test data for a better answer.
Figure 3: Although many induction motors may be similar, the quality of the build will dictate reliability and life cycle. Motor build inspection analysis analyzes the quality of the motor build and make recommendations on potential improvements.
Q: If there is a redundant motor & pump installed, what is best practice for operating the backup motor/pump?
Lyda: Lead lag process is popular for this. If you have a redundant or standby motor/pump, you can alternate with the main to ensure even wear of both machines over time. Each of the motor/pump combinations can take a turn as the standby and then pick whatever time period you think is applicable, by week, month or otherwise.
Q: Do belt-driven motors need needle bearings as opposed to standard roller bearings?
Lyda: Needle bearings would typically be used for either very high-speed or very low-load appli-

Figure 4. When grid power is fed to an electric motor a clean sine wave is seen. Once a variable frequency drive (VFD) is added to the circuit, the capacitive nature of the VFD will lead to voltage and current harmonics in the system. This is a waveform taken at the input VFD terminals with a fully loaded electric motor connected to the VFD output (size unknown).
cations. They are more common in the automobile industry. For belt-driven motors, you should use roller bearings as opposed to standard ball bearings.
Q: Is it typical to see complaints of electrical noise (e.g., problems with controls, etc.) related to the deployment of VFDs?
Lyda: Yes, this can be quite common. This is one reason you should use VFD-specific cables for any VFD-to-motor connections. Most VFD manufacturers recommend this anyway, and the cables are more expensive than standard ones, but you can mitigate some noise issues by using them.
Q: How do we derate a motor for 115°F Texas ambient + 10°F inside a boiler room? (I need a 55°C motor, but they are not normally available.)
Lyda: I would think if you are running above the rated ambient then you should derate the motor temperature rise. In other words, if you had an Insulation Class F motor at 40o, the temperature rise should typically be 105o or less. Bringing the ambient up to 55o would mean the temperature rise should be derated to 90o or less. As far as derating the horsepower output, I have no idea. I think the manufacturer should give you advice on that. Here is one other thing that may work: If you are currently using a Class F insulated motor, upgrading to a motor that is Class H insulation may give you a higher allowable running temperature.
Q: My utility is supplying unbalanced phase voltages (5% at times). Any advice on how to convince them to fix this and what the cost of the present situation may be in terms of premature motor failure?
Lyda: Per the power purchase agreement, a utility should be held to a higher standard than 5% unbalance (most that I have reviewed state 2-3%). I would contact them directly to send a licensed professional to meter and verify the voltage at your facility. If they refuse, you will need to measure and verify yourself or hire a third party. If your motors are running at this high of an unbalance for long periods of time, it is definitely costing money in the long run. A common industry adage is “7% current unbalance for every 1% voltage unbalance.” At 5% voltage unbalance, it is likely that at least one of your three-phase line currents is well beyond the rated amount at each actual motor.
Q: For a 50HP motor, how much energy does the motor consume when running no load? Does it make sense to shut down the motor when it is not running? What about the wearing that comes from frequent restarts?
Lyda: At no load, a 50HP motor will likely still consume 1-2kW (at very low power factor). However, you likely do not want to shut the motor off completely if you have a frequent restart application. This is where a VFD and process control can really help you out. When a load is not needed, the VFD will slow the motor to stop, and when it is needed, the VFD can ramp the motor up without an extreme inrush current (like what happens at line-starting).
Q: At what point does a soft-start on a motor pay for itself? Is there a break point for applying soft starters based on motor horsepower?
Lyda: Not sure. I think this is facility- and application-specific, depending on incoming transformer size and frequency of motor starts plantwide. Soft starters can be beneficial if all you are trying to do is reduce inrush current. For real energy savings, spend extra capital upfront and install (and program) a VFD instead.
Q: You mentioned that an oversized electric motor is inefficient. Does a VFD overcome this inefficiency for load matching?
Lyda: For a variable load application, a VFD can be programmed to reduce the speed of the
motor while lower loads are required. Reducing the speed of the machine provides energy savings based on the affinity laws. However, if you are starting from scratch, the VFD and motor should match the necessary load as close as possible for maximum energy efficiency. Keep in mind, a larger motor will have higher magnetizing current than a smaller one. For instance, if you have a 5 hp application and use a 10 hp motor, you are not getting the efficiency you should be at only 50% load, and you’re getting higher kW usage due to the higher current draw.
Q: What will be the power factor when we measure at line side of the VFD?
Lyda: VFDs generally improve power factor of the system since the capacitance of the VFD “offsets” inductance of the motor and distribution lines. If the VFD is properly sized and the motor is running close to full load, the power factor should be high. However, not all VFDs are created equal. I have witnessed multiple VFDs over the years that show poor line side power factor.
Q: How do VFDs reduce motor life? Should motors with a specific insulation class be used with VFDs?
Lyda: There are many ways VFDs reduce motor life. I covered quite a few in the presentation. One way is by overheating the motor. From experience in the lab, when running a motor at 60Hz grid power and then running the same motor at 60Hz from a VFD, a 10° to 15° temperature rise is expected. I advise using at least Class F insulation, and maybe even Class H, with VFD-driven motors. Also, make sure the motor is inverter-duty.
Q: Are VFD manufacturers able to give the harmonics configuration to simulate the harmonic distortion reports for utilities?
Lyda: Harmonics will be greatly impacted by the size of the power supply at your facility as well as your incoming voltage. If a VFD manufacturer knows the size and impedance of your incoming transformer and your precise input voltage, they should be able to supply the harmonic content of their product. Consult the AHRI Certified list for VFD manufacturers if you want to see harmonic values submitted for actual VFD products.
Q: What is the definition of “short” with regard to cable length?
Lyda: Unfortunately, this is all relative. The shorter, the better in every case. NEMA MG-1 lists recommendations for dv/dt limits. Dv/dt is a better way to judge the VFD quality to a specific motor application than just cable length.
Q: Do you know of good general data for motor efficiency at various loads and speeds when driven by a VFD?
Lyda: Motor efficiency data with a VFD is hard to find, although we do this type of testing often in our lab. Unfortunately, most of the results are proprietary. If you look at the AHRI Certified list for VFD manufacturers, you will find system efficiencies that these manufacturers have submitted for their products with motors:
Q: Can a VFD be connected to any 3-phase motor with 3 leads?
Lyda: Generally speaking, yes. However, make sure the VFD matches the voltage, current and frequency ratings of the motor. Just installing a VFD into an application will not do much for you, though. I would advise the motor should be inverter-duty before using a VFD. It is also good practice to use shaft grounding and have at least a Class F insulation rating. Finally, the VFD will need to be correctly programmed after installation to verify you are achieving proper process control and desired energy savings.
Q: We are finding a large number of equipment sets that use multiple induction motors in situations that range from no load to
full load, applied in short time frames M
on a frequent basis. Metering shows terrible power factor, voltage irregularities, and undesired harmonics. Solutions that fit within the existing control scheme and physical spaces are a challenge. Any thoughts?
Lyda: Are you currently using VFDs? If not, this could offset some of the power factor and voltage irregularities while also keeping the inrush current of individual motors lower. Using one VFD to control multiple motors or using many VFDs and a programmable logic controller (PLC) are both options. ce More
ANSWERS KEYWORDS: motors and drives, KEYWORDS:
variable frequency drives, VFDs
Variable frequency drive (VFD) life depends on both environmental and operating conditions. The AHRI Certified list for VFD manufacturers offers advice on system efficiencies and harmonic values. A three-phase motor can be connected to a VFD, but the settings need to match. ONLINE Read this article online at www.controleng.com for about adjustible speed drives.
Michael Lyda, motor and drive engineer, Advanced Energy Corp. This article originally appeared in the January/February issue of Plant Engineering.
CONSIDER THIS
What challenges do you have with motors and drives and how do you overcome them?