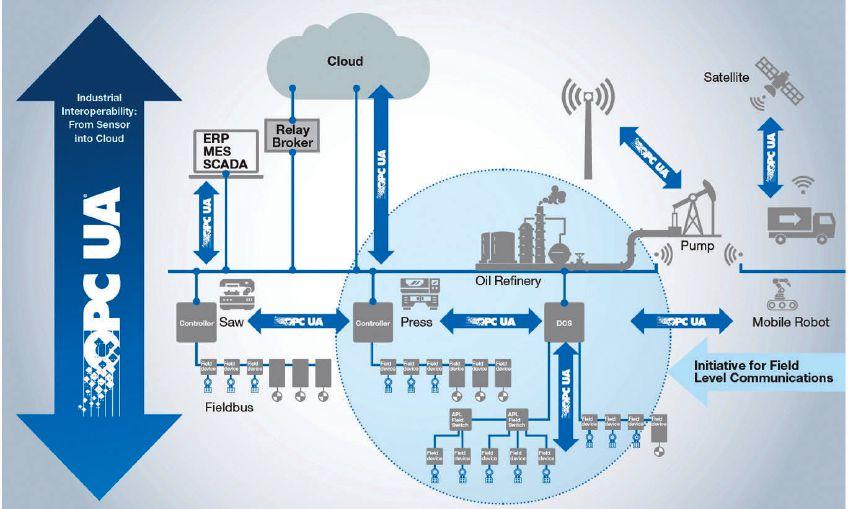
7 minute read
OPC UA: wider controller communications with TSN, APL
Peter Lutz, OPC Foundation
Advertisement
OPC UA uses Ethernet Time-Sensitive Networking (TSN) and Ethernet Advanced Physical Layer (APL) for controller-to-controller networking. Goal: interoperability.
OPC Foundation’s OPC UA (Unified Architecture) continues to expand, using Ethernet time-sensitive networking (TSN) and the Ethernet advanced physical layer (APL) and controller-tocontroller communications as part of planned standard industrial interoperability connectivity.
Two years after the launch in November 2018, the Field Level Communications (FLC) Initiative of the OPC Foundation has completed the initial Release Candidate for OPC UA-based Field eXchange (UAFX) for the “controller-to-controller” use case. This marked an important milestone in establishing OPC UA as a standardized industrial interoperability solution at the field level, taking advantage of key technologies, such as Ethernet TSN and Ethernet-APL.
The FLC Initiative published a 40-page technical paper detailing the technical approach and basic concepts for expanding OPC UA to the field level for the various requirements and use cases in factory and process automation.
At SPS 2018, in Nuremberg, Germany, the FLC initiative was founded under the umbrella of the OPC Foundation. As of March, 2021, 27 companies, including the largest automation manufacturers in the world, have joined the initiative’s steering committee, supporting it financially and with personnel and technical know-how. The common goal is to expand the scope of OPC UA down to the field level and to establish OPC UA as a uniform and consistent communication standard in factory and process automation (Figure 1). In the technical working groups, which are open to all OPC Foundation members, more than 300 experts from more than 60 companies are working to develop appropriate concepts and specifications.
Controller-to-controller prototypes
Work on the first version of the specification has made decent progress over the past year, despite COVID-19 restrictions. The basic concepts for the controller-to-controller (C2C) use case have been
Figure 1: OPC UA can operate as an integrated communication solution down to the field level. All graphics courtesy: OPC Foundation
Figure 2: Use cases for OPC UA are shown with the extensions for the field level (controller-tocontroller C2C, controller-to-device C2D and device-to-device D2D).
developed and incorporated into the first draft specifications. A first release candidate was completed in November 2020. Prototypes have been implemented to validate the draft specifications. A working group is developing test specifications, which are being converted into test cases for the OPC UA Compliance Test Tool (UACTT).
In a second version of the specification, the already developed concepts will be extended for controller-todevice (C2D) and device-to-device (D2D) use cases, so OPC UA can be used as a uniform and consistent means of communication across all automation levels (Figure 2). This opens up new possibilities, especially for different Industry 4.0 application scenarios and information technology (IT) and operational technology (OT) (IT/OT) convergence.
At the field level: System architecture
The extensions specified by the FLC Initiative are based on the OPC UA Framework (IEC 62541), which enables a secure and reliable, manufacturer and platform-independent, information exchange (Figure 3). Controllers and field devices support both, the connection-oriented client/server communication model and the publish/subscribe extensions, which are indispensable for communication at the field level due to the corresponding requirements for flexibility, efficiency and determinism.
Security mechanisms specified in OPC UA also are used, which, among other things, support authentication. Authentication involves data signing and encryption for transport, which can be used for client/server and publish/subscribe communication relationships.
The initial release candidate of the FLC initiative, completed in November, 2020, consists of four specification parts (OPC UA Parts 80-83) and focuses on C2C communication (controller-tocontroller) for the exchange of process and configuration data by means of peer-to peer-connections and a basic diagnosis: • Part 80 (OPC 10000-80) includes an introduction and provides an overview of the basic concepts for expanding OPC UA for communication with and at the field level. • Part 81 (OPC 10000-81) specifies the basic information model for controllers and field devices (automation components) and the communication concepts to meet the various use cases and requirements of factory and process automation. • Part 82 (OPC 10000-82) describes network services such as topology detection and time synchronization. • Part 83 (OPC 10000-83) describes the data structures for the exchange of information required for offline engineering using descriptors and descriptor packages.

Work on a safety specification for OPC UA (OPC UA Safety) also is very advanced. The first OPC UA Safety specification, based on client/server mechanisms, arose from a Joint Working Group with Profibus & Profinet International (PI), was adopted in November, 2019 (Part 15, OPC 10000-15). Revisions to the OPC UA Safety specification describe extensions for OPC UA publish/subscribe and the parameterization of safety participants. With the OPC UA
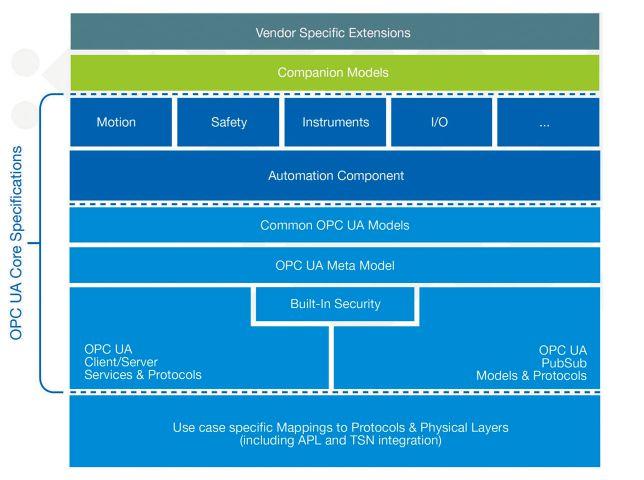
Figure 3: An OPC UA-based system architecture can include extensions for the field level.
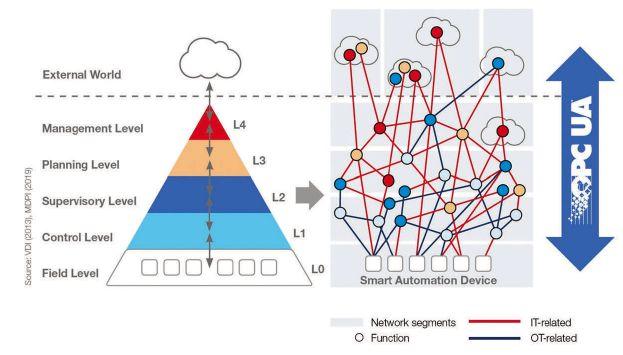
Figure 4: Semantic interoperability with OPC UA is shown from the sensor to the cloud.
M
More
safety concept, safe participants can be dynamically integrated into communications using a unique identification, even if a machine or system is in operation.
Progress also can be reported with regard to OPC UA Motion. A working group has been developing an OPC UA-based Motion specification since mid-2020. OPC UA Motion comprises the specification of motion control functions for various types of motion devices such as controllers, standard drives, frequency converters and servo drives. The FLC Steering Committee has agreed to base the work on the CIP motion and Sercos specifications and to adapt them to the OPC UA information modeling and system architecture, accounting for relevant Industry 4.0 use cases. As with OPC UA Safety, using existing concepts and specifications for OPC UA Motion accelerates specification work.
OPC UA with TSN, APL and 5G
TheOPCUAFrameworkistransport-agnostic and can be used with various underlying communication protocols and transmission physics. Ethernet TSN and the Ethernet-APL are considered by the OPC Foundation as important elements of the strategy to expand OPC UA to all use cases and requirements in factory and process automation and is part of the vision to create a scalable, industrial interoperability solution. By using Ethernet TSN, deterministic data transmission via OPC UA is facilitated, which is indispensable for demanding automation applications. In addition, TSN allows different applications and protocols to be operated using standardized hardware and a common network infrastructure. This enables convergent industrial automation networks to be implemented in which various IT and OT protocols can coexist.
An FLC working group is working out which TSN sub-standards shall be mandatory for OPC UA-based end devices and infrastructure components to meet the specified requirements for performance, flexibility and ease-of-use. The OPC Foundation has given a clear commitment to the TSN-IA (Industrial Automation) profile, which is being developed by the IEC/IEEE 60802 Working Group. For this reason, the OPC Foundation has entered into liaison agreements with the standardization bodies IEC SC65C and IEEE 802.1. Ethernet-APL describes a physical layer for Ethernet specially developed for the requirements of the process industry. Ethernet-APL enables data transmission at high speeds over long distances, the supply of energy and data via a common, twisted 2-wire cable, and protective measures for safe use in hazardous areas. Ethernet-APL may be used to enable OPC UA and other Ethernet-based protocols in the process industry. The OPC Foundation joined the Ethernet-APL Project in June, 2020 to develop and promote APL with other non-profit organizations and various industrial partners. Data exchange via OPC UA is not limited to wired or wireless Ethernet communication. Support for the 5G mobile communications standard is among OPC Foundation’s development plans. 5G mapping will be seamlessly integrated into the existing OPC UA architecture so all protocol and
ANSWERS profile extensions of the OPC UA FLC initiative can be used via Ethernet, Ethernet TSN, and, in the KEYWORDS: Industrial Ethernet, TSN, APL future, 5G. An OPC UA specification will allow controller-to-controller communications. Industrial automation interoperability The OPC UA (IEC 62541) framework, with Ethernet-APL and Ethernet extensions for the field level, specified by the FLC TSN also will enable controller- Initiative, in combination with underlying comto-device and device-to-device munication standards such as APL, TSN, and, in communications. the future, 5G, offers a complete, open, standard-OPC Foundation’s OPC UA also is integrating capabilities for motion, safety and 5G ized and interoperable solution. It fulfills industrial communication requirements and enables consiswireless. tency and semantic interoperability from the field CONSIDER THIS Interoperability among devices, controllers and level to the cloud and vice versa (Figure 4). With this approach, using various OPC UA companion specifications, information is made available with systems from the field to standardized semantics at the data source. the cloud will have enabling Consider the use case where a flowmeter offers technologies in OPC UA. standardized “OPC UA flow measuring data” when ONLINE the APL cable is plugged in. Servo drives also could www.opcfoundation.org/flc process standardized “OPC UA drive setpoints” and If reading from the digital provide standardized “OPC UA actual drive values” edition, click on the headline when the servo drives are integrated into a machine for more, including another graphic and links. network with Ethernet TSN. ce www.controleng.com/ magazine www.controleng.com/ networking-and-security/ ethernet Peter Lutz is director of the OPC Foundation FLC Initiative. OPC Foundation is a CFE Media content partner. Edited by Mark T. Hoske, content manager, Control Engineering, mhoske@cfemedia.com.