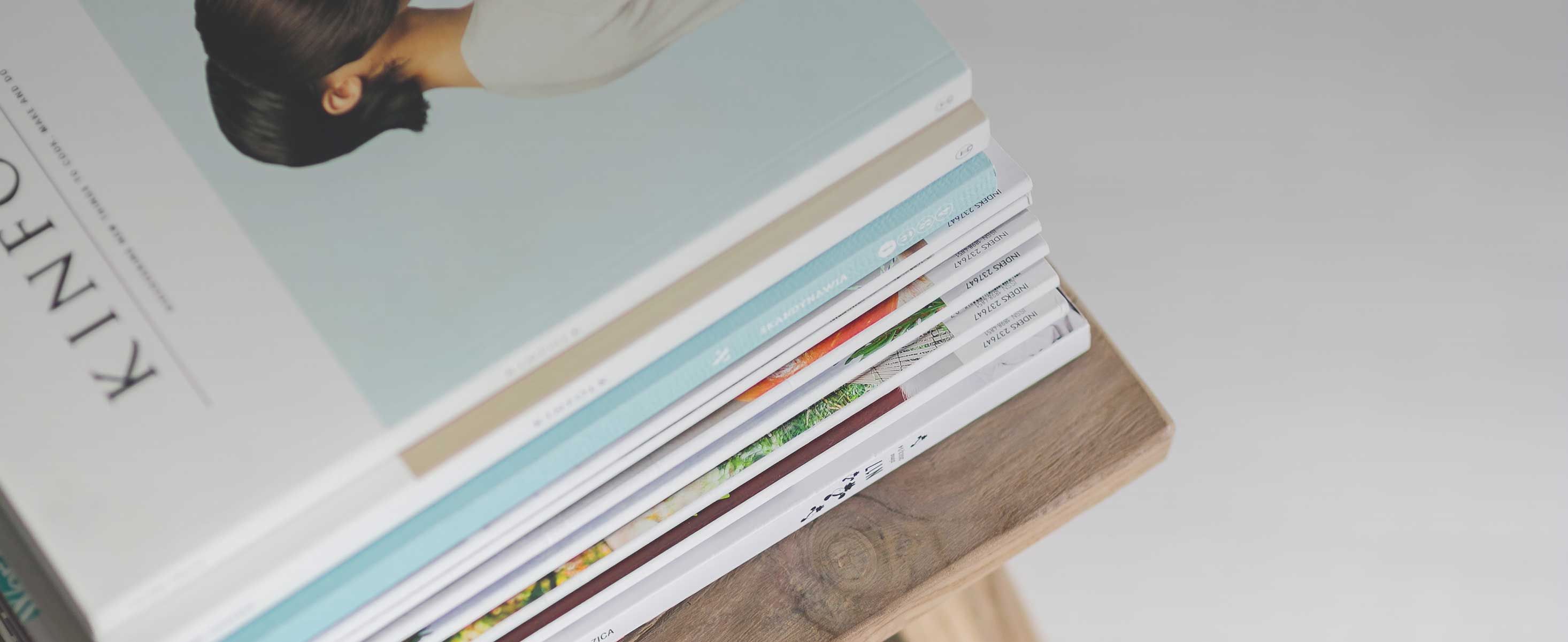
4 minute read
Think Again: Automated 3D printing Additive manufacturing
® 3010 Highland Parkway, Suite 325, Downers Grove, IL 60515. 630-571-4070, Fax 630-214-4504
Content Specialists/Editorial
Advertisement
Mark T. Hoske, Content Manager 630-571-4070, x2227, MHoske@CFEMedia.com Jack Smith, Content Manager 630-571-4070, x2230, JSmith@CFEMedia.com Kevin Parker, Senior Contributing Editor, IIoT, OGE 630-571-4070, x2228, KParker@CFEMedia.com Emily Guenther, Director of Interactive Media 630-571-4070, x2229, eguenther@CFEMedia.com Amanda Pelliccione, Director of Research 978-302-3463, APelliccione@CFEMedia.com Gary Cohen, Senior Editor GCohen@CFEMedia.com Chris Vavra, Web Content Manager CVavra@CFEMedia.com
Contributing Content Specialists
Suzanne Gill, Control Engineering Europe suzanne.gill@imlgroup.co.uk Ekaterina Kosareva, Control Engineering Russia ekaterina.kosareva@fsmedia.ru Agata Abramczyk, Control Engineering Poland agata.abramczyk@trademedia.pl Lukáš Smelík, Control Engineering Czech Republic lukas.smelik@trademedia.cz Aileen Jin, Control Engineering China aileenjin@cechina.cn
Editorial Advisory Board
www.controleng.com/EAB
Doug Bell, president, InterConnecting Automation, www.interconnectingautomation.com David Bishop, chairman and a founder Matrix Technologies, www.matrixti.com Daniel E. Capano, senior project manager, Gannett Fleming Engineers and Architects, www.gannettfleming.com Frank Lamb, founder and owner Automation Consulting LLC, www.automationllc.com Joe Martin, president and founder Martin Control Systems, www.martincsi.com Rick Pierro, president and co-founder Superior Controls, www.superiorcontrols.com Mark Voigtmann, partner, automation practice lead Faegre Baker Daniels, www.FaegreBD.com
CFE Media and Technology Contributor Guidelines Overview
Content For Engineers. That’s what CFE Media stands for, and what CFE Media is all about – engineers sharing with their peers. We welcome content submissions for all interested parties in engineering. We will use those materials online, on our website, in print and in newsletters to keep engineers informed about the products, solutions and industry trends. www.controleng.com/contribute explains how to submit press releases, products, images, feature articles, case studies, white papers, and other media. * Content should focus on helping engineers solve problems. Articles that are commercial or are critical of other products or organizations will be rejected. (Technology discussions and comparative tables may be accepted if non-promotional and if contributor corroborates information with sources cited.) * If the content meets criteria noted in guidelines, expect to see it first on our Websites. Content for our e-newsletters comes from content already available on our Websites. All content for print also will be online. All content that appears in our print magazines will appear as space permits, and we will indicate in print if more content from that article is available online. * Deadlines for feature articles for the print magazines are at least two months in advance of the publication date. It is best to discuss all feature articles with the appropriate content manager prior to submission.
Learn more at: www.controleng.com/contribute
Additive manufacturing
Sophisticated motion controls move 3D printing from design to manufacturing as use of metals progresses.
Additive manufacturing continues to progress with 3D printing of metal using sensors, advanced motion controls and logic by moving quickly from designs to part manufacturing. Think again about how additive manufacturing can improve manufacturing processes.
Nissan accelerates assembly
Automotive manufacturer Nissan integrated 3D printing into its production process at the Nissan Barcelona factory using BCN3D, a Spanish 3D printing manufacturer. By printing some parts in-house with 3D printers, Nissan has cut the time of designing, refining and producing parts from one week to one day and slashed costs by 95%. Nissan is printing 3D materials in plastic and is trialing metal, according to BCN3D.
Nissan created 700 3D printed parts as of June. Carlos Rellán Martínez, manager of maintenance and engineering facilities at Nissan Motor Ibérica Zona Franca, Barcelona, said: “Outsourcing tools to a mechanical supplier was 20 times more expensive than 3D printing the same parts. The wait for tools went from a week down to one day.... We have paid off the investment in the printers very quickly.”
Cummins expands 3D metal
Cummins Inc. announced in May it is finalizing its first production part using a new, high-precision 3D metal printing technology called binder jet, a “significant milestone in the company’s additive manufacturing and Industry 4.0 journey.”
Additive manufacturing of the lance tip adapter, a critical emissions component in Cummins engines, provides a lighter-weight design, improved geometry for fluid and air flow, and eliminates cross-drilling complexity. Tim Millwood, vice president of global manufacturing at Cummins, said, “We’re on the cusp of being able to leverage a broad range of additive technologies to print the parts we need, using the right technology and at lower costs and increased speeds.” Cummins and GE Additive are developing third-generation binder jet technology, for higher throughput, improved quality and lower cost.
Additive ... minus a 3D printer
Contract manufacturers Addman Engineering and Wagner Machine Co. are offering 3D manufacturing services with high-value metal parts, without purchasing a 3D metal printer than can cost well over $1 million. Advanced motion controls, real-time sensing and monitoring, and quality assurance add value to machines. Velo3D, maker of additive manufacturing machines, cited Wagner Machine CEO Kurt Wagner as saying, “We recently had a customer ask us to make a brazed assembly that was impossible due to space constraints and other requirements. We suggested 3D printing, which was their original plan, but other 3D printing companies they consulted said the part would be impossible to print due to thin walls and pressure requirements.”
Mark Saberton, Addman CTO and founder, said, 3D printing gives “our customers the freedom they need to design the next generation of spacecraft and turbomachinery without compromising their designs for the sake of manufacturability.”
MIT helps 3D cement printing
3D printing with cement for building and construction markets has MIT researchers looking cement hydration at a molecular level to help. Work includes the MIT Concrete Sustainability Hub. ce
Mark T. Hoske, Content Manager
M More INSIGHTS ONLINE photos, BCN3D video: See ONLINE photos, how the Nissan Barcelona factory uses 3D printing to manufacture final parts and prototypes on an assembly line.