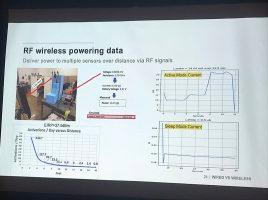
6 minute read
When it comes to cybersecurity we can hope for the best but must always prepare for the worst
WIRELESS SENSORS
ENERGY HARVESTING FOR SENSORS
Advertisement
Gathering data from wireless sensors is critical in the Industrial Internet of Things (IIoT) era. Various energy harvesting methods can provide power. Chris Vavra reports.
Awell-planned Industrial Internet of Things (IIoT) infrastructure can allow a small team of workers to do the work of dozens more by leveraging data from thousands of devices on the plant floor. This might seem daunting, but Will Zell, CEO and co-founder of Nikola Labs, sees this as the convergence of data and technology advances. Now, more than ever, workers have the ability to get a greater picture thanks to sensors attached to the devices on the plant floor.
“These sensors can provide data each day and see a picture that is being painted of what is and isn’t working in the plant,” Zell said in his presentation. ‘Wired versus Wireless for IIoT Solutions: The Pros, Cons, and Key Considerations,’ at Fabtech 2019 in McCormick Place in Chicago. “By leveraging sensor-based technology, you create a multitude of value.”
This is critical because unplanned downtime is costing manufacturers hundreds of billions of dollars each year. While companies are moving from reactive maintenance to preventive maintenance, Zell said the cultural shift can really take hold with the IIoT and improve automation and plant safety.
Some fear automation might be replacing workers on the manufacturing floor. Zell sees it differently. “The real challenge is how you change a maintenance team by installing sensors that can help the team without replacing them. Make them feel proactive. If this is executed well, a small team can leverage thousands of machines to do the work of dozens of humans,” he said.
Wired versus wireless
motors and drives operate. The most common challenge is the sensors have to be retrofitted onto the device because very few are installed with built-in technology. The equipment involved may be 20- to 30-years old.
Wired industrial sensors have continuous power and data reliability. Users don’t have to worry about transmitted information getting lost. The upfront costs for a wired sensor are high, and the sensors may be located in areas difficult to access.
Wireless sensors have emerged through the IIoT and are easier and cheaper to install compared to wired sensors. Wireless sensors have more limited data capture and require batteries. Battery life has increased, but batteries do need to be replaced. For a large facility, that could cause all kinds of problems for the plant team because thousands of sensors may need to be brought back up to speed.
Through energy harvesting IIoT can deliver maintenance-free wireless sensors through sources such as vibration, RF and light energy. Image courtesy of Chris Vavra. energy requirement than a pressure or temperature sensor. Zell believes that properly managing harvested energy, sensing and data communication is key to achieving a maintenance-free wireless sensor. He said: “Sensor platforms that have energy harvesting that can deliver data to IIoT systems.” Zell provided an example of RF wireless powering from a sensor over distance via RF signals transmitted from a transponder. From there, an RF harvesting chip receives the signal to regulated dc power. According to Zell, delivering IIoT at scale can be achieved with wireless Wireless powering energy harvesting. While there is a The problem can be alleviated through place for wired sensors, particularly ambient energy harvesting and radio for applications that cannot afford frequency (RF) wireless power delivery. downtime, the overall benefits of energy With energy harvesting, Zell said, the IIoT harvesting will provide more reliable can deliver maintenance-free wireless data at faster speeds at lower costs for sensors using vibration, RF and light manufacturers. plus-circle energy. How much energy depends on the data payload and sensor type. An Chris Vavra is associate editor, Control ultrasound or video has a much different Engineering, CFE Media and Technology.
NEW PRODUCTS
Better data collection from hazardous areas
SKF has gained hazardous area approval for its QuickCollect sensor, which collects vibration and temperature data. This new approval allows the sensor to be used in places that would previously have required a ‘hot work’ permit.
The certification opens up condition monitoring applications in a range of sectors, including petrochemical, mining and marine industries. It also brings digitalisation of data into hazardous areas, which up to now is a relative rarity.
The sensor is certified to both the international IECEx and European ATEX standards, for use in Zone 1 hazardous areas.
The QuickCollect sensor can be used in conjunction with SKF’s ProCollect mobile app which connects the sensor to SKF’s web-based software platform, Enlight Centre. Together, this creates a portable condition monitoring system, called SKF Enlight ProCollect, that offers direct access to SKF’s experts in remote diagnostic services.
The package is available as a subscription service, which is charged monthly or annually. This model allows SKF to tailor the package to the customer’s exact needs.
Non-invasive inspection of oil and gas separators
An optical gas imager from FLIR Systems is said to be safely and efficiently enabling oil and gas producers to undertake routine, non-invasive inspections in their oil and gas separators.
Separators are pressure vessels designed to separate a well stream into gaseous and liquid components. During this process, sand can build up in the heating element, causing damage to the separator. If this build-up is not noticed and promptly removed, it can result in the emission of flammable gases, costly repairs or catastrophic failure. Traditionally, oil and gas separators have been inspected by hand or cleaned out on a routine basis without evaluation. While this process provides basic maintenance, it does not provide the early detection required to identify mechanical or safety issues.
A variety of devices can be used to inspect oil and gas separators to verify tank pressures and liquid levels however, use of thermal imagers are one of the safest and most efficient solutions. The FLIR GFx320 optical gas imager can be used to visualise natural gas leaks and sand levels as the camera shows changes in temperature from sand versus oil, gas, and water.
The GFx320 is certified for use in Class 1: Division 2 or Zone 2 locations, allowing the user to get close to the unit for a thorough, but non-invasive inspection.
The use of the GFx320 for routine inspection of oil and gas separators is allowing tank pressures and liquid levels to be verified. It can also detect leaks from the separator, resolve anomalies to restore compliance, avoid adverse environmental impact, and prevent safety risks to equipment or personnel.
ATEX approval for ultrasonic clamp-on flow meter
Badger has announced new hazardous area certification to ATEX/IECEx Zone 2 for the Dynasonics TFX-5000 transit time ultrasonic flow meter.
The certification covers models measuring DN65 and larger, making the solution suitable for flow measurement in automotive, waste-water, oil and gas and other general industrial applications requiring hazardous zone approvals.
The ultrasonic clamp-on flow and energy meters are said to offer a versatile solution for measuring volumetric flow and heating/cooling rates in clean liquids as well as those with small amounts of suspended solids or aeration, such as surface water or raw sewage. Typical applications include water mains, reclaimed water, lift stations and booster pump stations in water and wastewater or the energy transfer of chilled water (cooling) and glycol/hot water (heating) in HVAC systems as well as produced water in oil and gas applications.
The TFX-5000 meter is intended for users seeking an accurate, reliable and affordable transit time metering device. It is available in a variety of configurations and can be selected with features suitable to meet particular application requirements.
By clamping onto the outside of pipes, ultrasonic devices do not contact the internal liquid which offers inherent advantages such as reduced installation time and cost, no limits on pressure or fluid compatibility.