
10 minute read
We speak to a cross-section of industry experts to find out more about the Artificial Intelligence of Things and what it might offer in industrial applications
WHAT COULD THE AIoT OFFER INDUSTRY?
Control Engineering Europe spoke to industry experts to find out more about the AIoT and what opportunities it might offer in industrial applications.
Advertisement
The Artificial Intelligence of Things (AIoT) refers to the adoption of AI capabilities in Internet of Thing (IoT) applications. In simple terms, while the Internet of Things (IoT) is reactive, Artificial Intelligence of Things (AIoT) is proactive. The AIoT relates to the combination of AI and the IoT with the goal of achieving greater efficiency in complex operations – it looks to improve human and machine interactions and to enhance data driven decision making. AIoT also adds a ‘brain’ to the Cloud and the Edge.
Q: What effect do you think AIoT will have within the industrial sector?
Giuseppe Surace, chief product and marketing officer at Eurotech (GS):
AI technologies help companies to leverage the potential of the huge amount of data generated by devices, assets or ‘things’. Immediately sending all this data to the cloud or a data center would require an adequate infrastructure, which would be expensive to deploy and maintain, without taking bandwidth and latency issues into account. Bringing AI, machine and deep learning closer to the source of data can help businesses to provide a meaning to the data collected in the field to turn it into actionable business decisions.
James H. Chappell, global head of AI and Advanced Analytics at AVEVA
(JC): Fundamentally, as companies adopt AIoT they will become more efficient, reduce costs, and improve overall operations including accuracy and safety – and by reducing wastage and reducing their carbon emission during these complex operations they will become more sustainable. AI uses a wide variety of historical data
to analyse trends, and this can help streamline and improve processes.
Pete Sopcik, ADI OtoSense marketing manager at Analog Devices
(PS): AIoT is having a significant impact on several key areas in the industrial ecosystem – faster decision making; reduced infrastructure costs; and improved security architectures. Each of these benefits are driven by the ability of AIoT to deliver insights at the edge.
Q: In what sort of time-frame do you expect to see AIoT technologies being adopted in the industrial sector?
GS: AI is already moving to the IoT edge thanks to the advances in edge computing technologies. By connecting field devices to powerful edge computers, there is no need to send all the data to the cloud or data center, as it can be processed and analysed on site. Although we are still far away from seeing completely autonomous applications (like level 5 autonomous driving), there will be a consistent leap in the amount of data processed at the edge over the next 5-10 years.
JC: AIoT is already being used in the industrial sector, but it is still in its infancy. Predictive analytics uses supervised machine learning to understand an asset’s individual operating history and develops a series of normal operational profiles for each specific piece of equipment. When this is applied to the cloud it offers real-time operating data to detect the subtle changes in system behaviour that are often the early warning signs of pending equipment failure. And it’s becoming more sophisticated by bringing together cognitive technologies. For example, machine learning applied to various IoT data can detect when heavy machinery on a manufacturing line is not operating at its peak.
PS: We are already witnessing AIoT technology adoption in industrial environments. These are coming in the form of quality control applications such as monitoring end of line quality on finished goods. Customers are creating models of their assets coming off the production line and testing these assets to validate operation prior to shipping to customers. Such applications are paving the way for broader adoption of AIoT solutions that are more tightly integrated with the manufacturing ecosystem, optimising maintenance strategies, process control and manufacturing operations.
Q: How do you expect AIoT affect the control engineering function?
GS: Even though most AI training will still happen in the cloud, there will be a need to deploy trained models to optimise field applications, such as predictive maintenance and robotics. The challenge is providing AI models with the right data. As AI training and inference happens at a software level, the role of control engineers will be crucial to provide that software with quality data to improve the machine and deep learning models.
JC: In order to get the most value from AIoT, it is important to understand what it can do today, and it is equally important to understand what it cannot provide. By matching business use cases to AI capabilities, companies can pragmatically leverage the power of AI in order to achieve maximum benefit with realistic and beneficial results. For example, a company having issues with unplanned operational downtime can leverage AI to provide early detection of issues based on the data provided by sensors they may already have in place. Furthermore, they can leverage techniques such as deep learning to provide forecasts of an asset’s remaining useful life in order to better assess situational risk. By following best practices and integrating AI intelligence into business operations – through the Cloud – companies can maximise the benefits and value of their investments.
PS: AIoT will play an important role in how control engineering impacts the industrial environment and adapts to new technologies that drive expanding capabilities. AIoT will drive tighter integration between assets and process optimisation. Faster decision times lead to better control. Analytics on each product – not just sample sizes – will deliver better insights and improved accuracies of the manufacturing and quality control processes that govern the industrial environment.
Control engineers will need to continue the integration of these connected devices and improved information into the industrial ecosystem while also playing a key role in ensuring that these analytics are appropriately applied and controlled to enable optimised, reliable and safe manufacturing conditions. Best practices and how to integrate these solutions to deliver optimal efficiencies must be considered to ensure this integration is effective and scalable.
Q: Can you offer any ideas for practical AIoT applications in the industrial sector?
GS: Predictive maintenance operations will benefit hugely from AI and AIoT. By collecting more and more data over time, maintenance processes will become increasingly efficient, leading to a consistent reduction of costs, with less waste and reduced downtimes. The more data that is used to feed a training model, the more efficient that model will become.
Another field of application of AIoT technology is robotics and machine vision. Robots and cobots make large use of camera inputs to perform their task. The more data can be processed and analysed in real time, the more their work will be efficient. This would enhance the quality of production processes, leading to better outcome, again with less waste.
JC: In order to get the most value from AIoT, companies need three primary things – a corporate culture that encourages and facilitates AI infusion into business processes; > p12
an understanding and trust of the power of AI capabilities; and an IT infrastructure that provides the underlying data requirements and processing power needed by AI – and that includes utilising a Cloud Platform. Without all three, barriers will inherently exist to achieving maximum success.
PS: Quality control is one application that is being addressed today in various forms. Whether it is monitoring pumps, compressors, sub-assemblies or final products such as refrigerators, AIoT is enabling new insights into the machine operation to address critical quality problems.
Bringing diagnostics directly to the critical equipment in the field is another key application for AIoT. Large assets, such as aircraft engines, wind turbines and vehicles, require service teams to go to the equipment in the field. AIoT solutions can deliver analytics at the asset in the field, leading to corrective actions that can be taken immediately. plus-circle
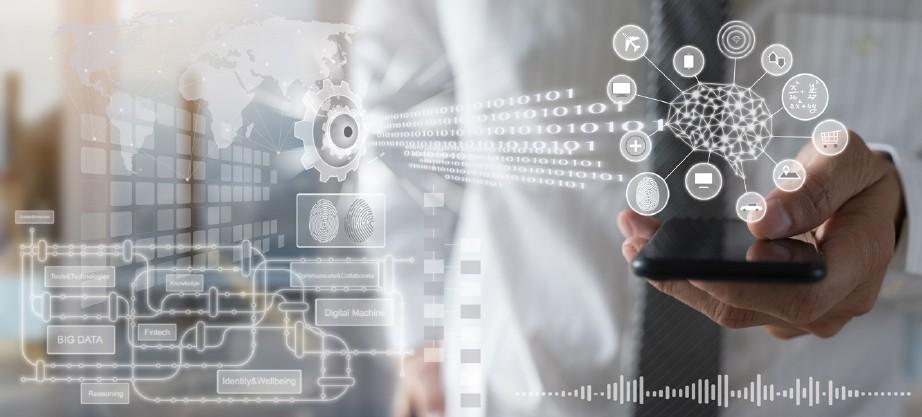
An enterprise-wide digital nervous system is finally emerging
While the Industrial Internet of Things (IIoT) may provide a theoretical opportunity within an enterprise to receive all the relevant information needed, it does not, by itself, make that practically feasible in a scalable fashion, says Hermann Berg, head of Industrial IoT at Moxa Europe.
Using the analogy of the human nervous system, Berg points out that the IIoT is missing the pre-processing of sensory information and sometimes the autonomous responses of a human body. He said: “The brain will not receive the information that the skin on your right hand is fine, but it will get notified immediately when the sensors in your hand signal very high temperature as a result of you touching a hot stove. And, even before that the central nervous system will have triggered the reflex to withdraw the hand, before the brain has started to take further action like finding water to cool your hand.”
Berg goes on to point out that in 2018 Gartner estimated that around 10% of enterprise-generated data is created and processed outside a traditional centralised data center or cloud. By 2025, it predicts this figure will reach 75%. So, clearly local processing and edge computing has already started – in particular in applications where bandwidth to the cloud is limited or costly – or privacy or latency concerns exist, but not only there.
A common category has been around since data logging started decades ago: protocol conversion, data cleansing and other pre-processing of raw data from sensors and other equipment to turn it into useful data for downstream systems. The importance of data preprocessing and cleansing has increased significantly as a result of more and more powerful machine learning algorithm. Put more simply – garbage in, garbage out!
For machine learning itself there are three important categories of data types that correspond to different types of hardware requirements:
Time series data: This is typically sensor and machine state data that requires accurate time stamps to derive insights from it, such as anomaly detection or predictive maintenance.
Audio: Speech recognition and event detection, for cycle counting or creating alarms, for example.
Video: Demanding neural networks apply deep learning for quality inspection and other insights derived from video cameras observing an industrial location.
For example, Moxa has seen high end artificial intelligence applications for video processing in manufacturing quality inspection scenarios and for autonomous mining trucks and outdoor patrol robots for power infrastructure, but also much less demanding local processing, based on times series data in manufacturing process optimisation.
“In most of these applications the IIoT and AI applications are not replacing the local control engineering function,” continues Berg. “IIoT and AIoT create transparency and make insights available across the company and beyond, while the current control engineering functions continue to govern the ‘local reflexes’. IIoT and AI trigger actions like anomaly detection, predictive maintenance, and starting recovery and optimisation tasks without delay, while the immediate ‘reflex’ is executed by the existing local control system.
Edge to Enterprise
Real-time operations management platform for supervisory control, SCADA and IIoT
In today’s competitive environment, you need to drive more performance from your assets, collaborate better and generate more value from your existing automation systems. All businesses converge on the need to maximize return on assets through operational excellence. Staying competitive means constantly finding ways to operate faster and leaner at the plant level.
AVEVA empowers organizations to operate their business in real-time and make smarter decisions - streamlining processes, optimizing operations and improving safety. Our solutions leverage data-driven visualization to increase operational efficiency, collaboration and eliminate value leaks.
AVEVA offers integrated software solutions that work in coordination with one another at every level of the business, from edge management to web-based HMI SCADA to the cloud. AVEVA’s Edge to Enterprise strategy offers native integration between every software in the portfolio.
Right Portfolio
Broadest and deepest portfolio of industrial software.
Right Licensing
Market’s first and only edge to enterprise subscription offer, enabling portfolio as a service.
Right Approach
Only portfolio offering responsive operations management interface (OMI) that automatically generates runtime visualizations, edge control and remote management of IoT edge devices.
Partner with AVEVA to accelerate your IIoT transformation
AVEVA’s portfolio delivers value across all aspects of the business with complete transparency of information – from design, to operations and maintenance – in a hardware-agnostic manner
2 Million 100,000+ 20+ Billion
licenses installed
sites worldwide operating parameters
10+ Trillion
industrial transactions/day
12+ Petabytes
of data stored/year
Find out more at aveva.com
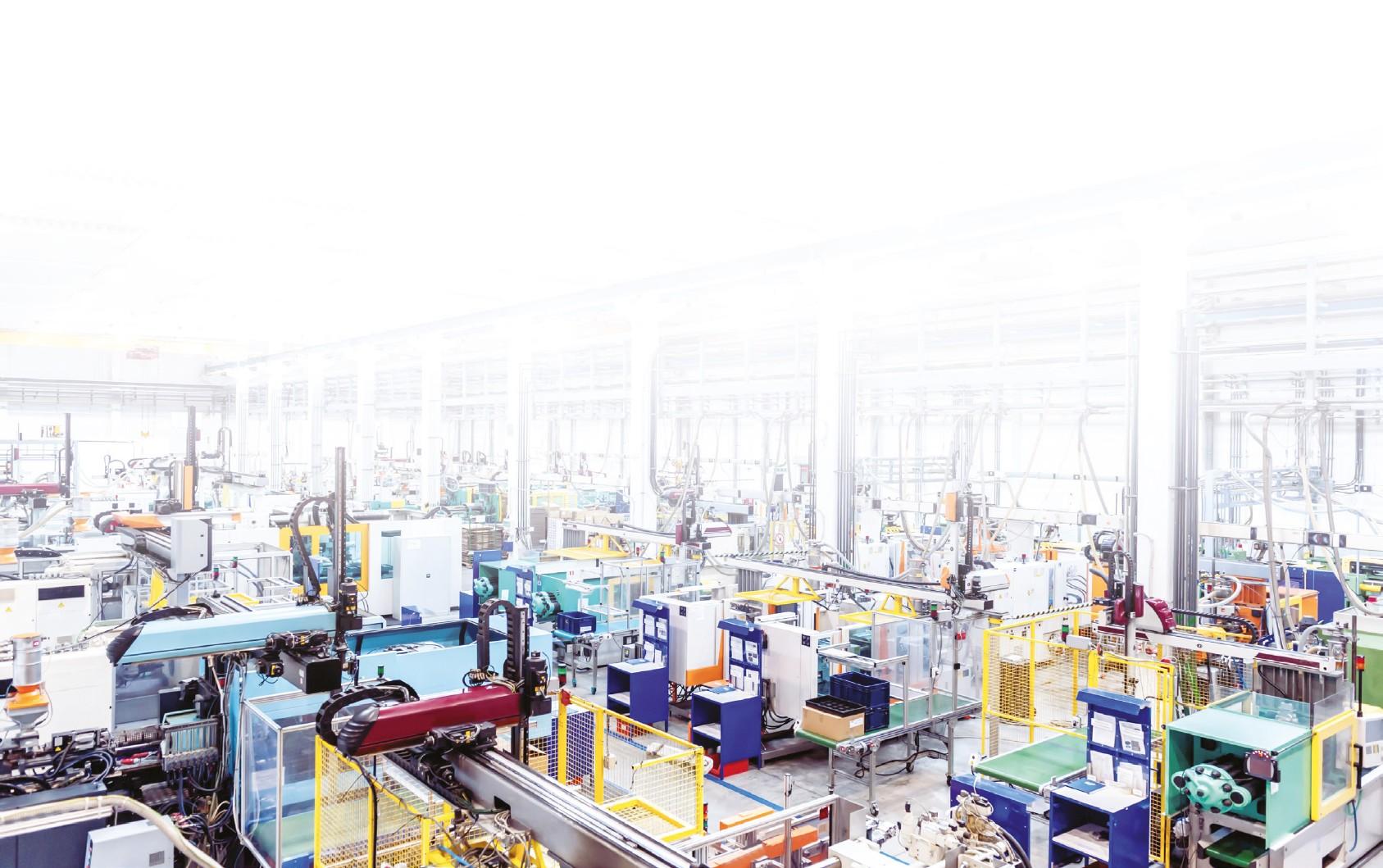