
5 minute read
Potential effects of the economic climate on asset integrity
During the current economic climate, when it comes to budgets, practically every facility owner and manager has the same dilemma: doing more with less. When faced with shrinking budgets, it’s tempting to delay general maintenance, repairs, inspections and other operating costs to a future point where the budget available may be more favourable – or even postponing the tasks indefinitely.
Similarities can be drawn between the current economic climate with the economic crisis of 2008/2009 which saw budgetary constraints across the energy industry. The COVID-19 pandemic has doubtlessly challenged operating budgets, but it has also had a direct impact on human resources. There have been reports of worker’s shifts being extended due to the pandemic, which in some cases have been extended to as long as 12 hours a day for two weeks, allowing employees to work up to 86 hours a week compared to the 72 hours currently permitted.
Advertisement
In addition to allowing changes to shift patterns, the US Nuclear Regulatory Commission also allowed US nuclear plants to delay some inspections. Hence, when there is a challenge to an operating budget, maintenance and integrity related tasks are often reviewed as an option for cost cutting.
The major hazards for energy facilities are ever present – fire, explosion and the release of hazardous materials. All these hazards have the potential to cause a major process safety incident. The energy industry is a dynamic and rapidly changing industry but one with ageing infrastructure and increasing cost pressures as the available revenue from oil and gas sales declines. There is a risk that the dedication of resources towards asset integrity will be allowed to decline as a result of the changing economic factors currently present in the industry.
Shortfalls in maintenance and asset integrity related activities are often highlighted in investigation reports as a leading cause of process safety incidents. Some contemporary examples are: • On 23 October 2009, a large explosion at the Caribbean Petroleum Refinery in
Puerto Rico caused extensive damage to numerous petroleum storage tanks as well as damage beyond the refinery’s boundary.
The incident occurred during the offloading of gasoline from a tanker ship to the tank farm. The tank being filled overflowed, resulting in a vapor cloud release and subsequent explosion. One maintenancerelated cause was identified in the investigation report – a malfunctioning tank fuel gauge. The faulty equipment prevented workers from noticing that one of the tanks was overflowing before the fuel vapours
ignited. It was reported at the time that the level transmitters were often out of service, awaiting maintenance tasks. • Pipe rupture on the Crude Unit of the
Chevron Refinery in Richmond, California on 6 August 2012, resulted in a vapour release and explosion. Around 15,000 people from the surrounding area were treated for breathing problems and 20 people were admitted to hospital. The pipe was found to have been damaged by sulphidation corrosion. The key activity designed to combat this kind of failure is the implementation of routine inspections as part of a preventative maintenance strategy. In this case, recommendations for improvements were not followed-up.
Within the energy industry, there has been sizeable investment within asset integrity. This has resulted in improvements to physical integrity, progress in effective asset integrity management, awareness and performance. Many operators have found that by applying best practices in maintenance and reliability they can optimise asset integrity and reduce total maintenance cost.
The key to effective decision making when revising maintenance plans is to review the criticality of the systems. The definition of critical equipment may vary from organisation to organisation and if it is not formalised, there may be several interpretations of equipment criticality within a single organisation. If the assumptions used to assess what equipment is critical are not technically based, then different individuals will identify different pieces of equipment as being critical as the selections will be based on individual opinions and lacking consensus. As a result, the potential for equipment failure having significant safety, environmental or economic consequences may be overlooked.
The greater issue with deferred maintenance is that it only grows in scope – and cost – the longer it is prolonged. When repairs are delayed they can quickly become replacements. The longer that maintenance is deferred, the more components that are affected and the more costly that maintenance becomes. Run-to-failure is only a viable tactic in situations when there is little economic and no safety or environmental impact. The bigger the deferred maintenance number becomes, the potentially harder it may become to maintain the facility at an acceptable level of safety management. However, facilities that have implemented comprehensive preventive maintenance programmes have found that the operation of their systems is more reliable, and those systems also last longer.
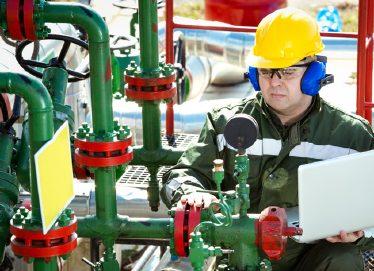
Deferral of maintenance tasks for energy facilities is not a new concept and there are often situations where tasks become postponed due to operating constraints. These factors could be because of the equipment not being made available for maintenance due to plant configurations or a turnaround being postponed for a year or more due to commercial drivers or increased confidence in the equipment. The key to safe management of postponing these tasks is for the use of risk-based tools for work prioritisation which has a defined clear responsibility for tracking overdue tasks to completion. An effective risk assessment may also provide the required evaluation of the effects of prolonging shutdowns and the effects on safety critical devices (such as pressure safety valve calibrations) must be considered.
Across the industry, there is a current trend of challenges to provide the skills, training and competencies required to deliver the high standards of asset integrity necessary in major hazard industries. The economic cycles in the global oil and gas industry have significant influence on recruitment and preservation of necessary competence. This needs to be recognised and effectively managed to ensure that the necessary skills base is always retained within an organisation, particularly during an economic crisis.
When the costs of process safety related incidents in the energy industry can be in the hundreds of millions, or even in the billions of dollars, it ought to be relatively simple to make the case that prevention is a far more cost-effective option. Decisions based within short term budgetary challenges should consider this fact.
About the author
Dr Jason Shirley is an experienced risk engineering manager within the high hazard process industries. He has had the privilege to view the operating practices across multiple energy installations throughout the Middle East and globally. Jason has 10 years of operations management experience within the energy industry. He has a strong background in sharing knowledge and best practice within the industry.
Image: Shutterstock