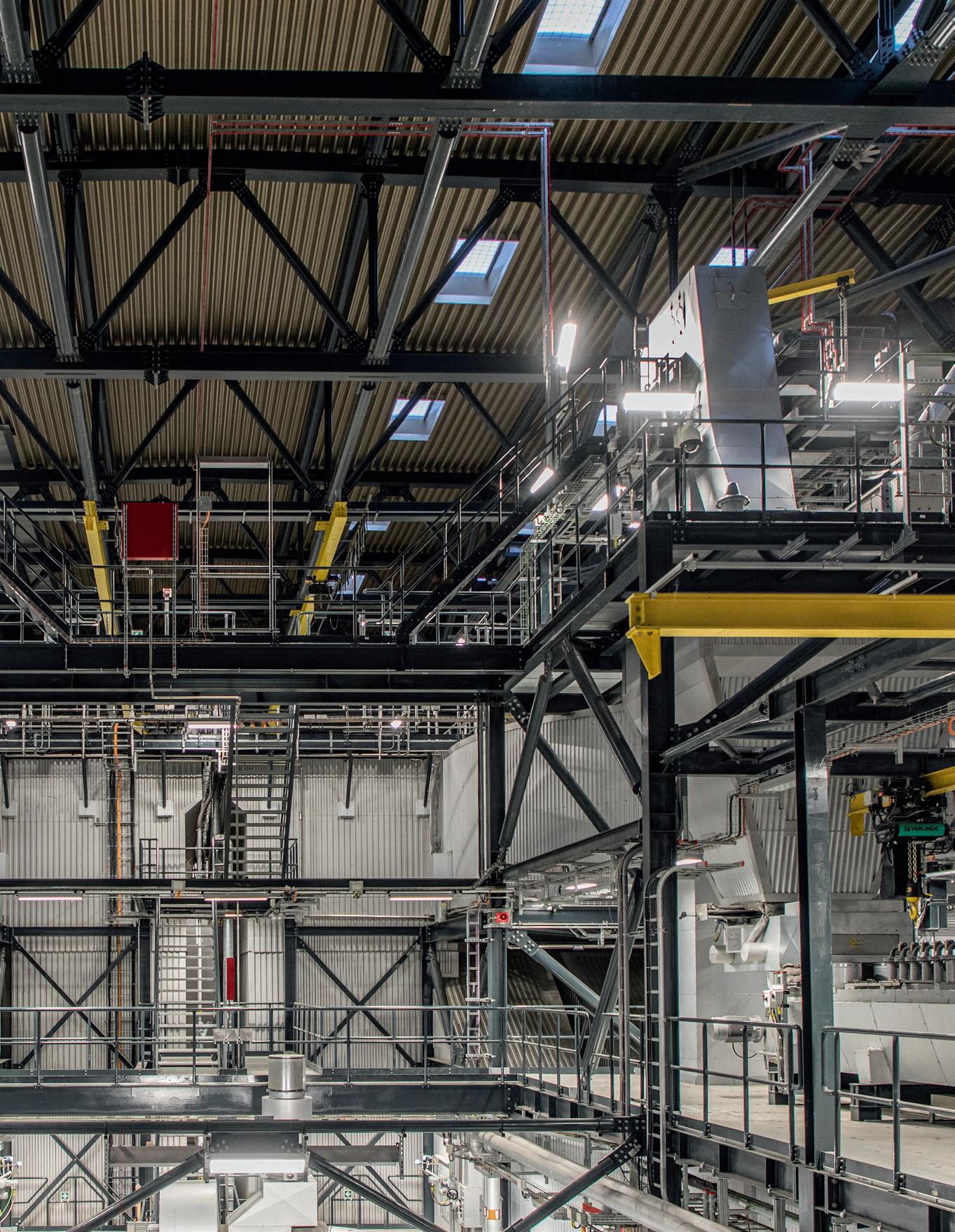
3 minute read
New unit for Amager Power Plant
ENERGY PRODUCTION
Designing as the project unfolds
Advertisement
In the capital region of Denmark, Amager Power Plant’s unit 4 was designed through a parallel process where design and development occur alongside the planning of the final project. A challenging job, where change management and 3D play a crucial role.
On October 26th 2020, Amager Power Plant’s new biomass unit was officially inaugurated. It is one of the largest energy projects in the history of Denmark, and it is the main reason coal has now completely been abolished from the capital’s heat production.
In preparation of this deeply complicated, massive power plant, parallel processes were necessary. The project design and preparation began before the power plant was ordered. There are several reasons for this approach, explains our Project Director, Sten Willer Christensen:
If we were to wait with design and construction until we had the final layout of the project, we would have lost a lot of time, and the building must, so to speak, exist before the machinery can be installed. Another reason you cannot choose the machinery from the beginning, is that in the years it takes to build a power plant from the ground up, technology will have progressed and become more energy efficient and environmentally friendly.
Sten Willer Christensen Project Director Energy Copenhagen
More scenarios than one Sten adds that the daily operating loss would have been enormous and saving a year of the lengthy construction process makes a perceptible difference. Consequently, it has been worthwhile to operate with different scenarios and continuously adapt the project. Some of the known factors included the approximate location of elements such as the kettle and the flue gas treatment plant. However, the designing engineers did not know the specific details regarding height and width, which connections or ventilation systems would be necessary, the load of the machines or other important aspects concerning the engineering design. Once the machines were chosen, additional detailed designs were necessary.
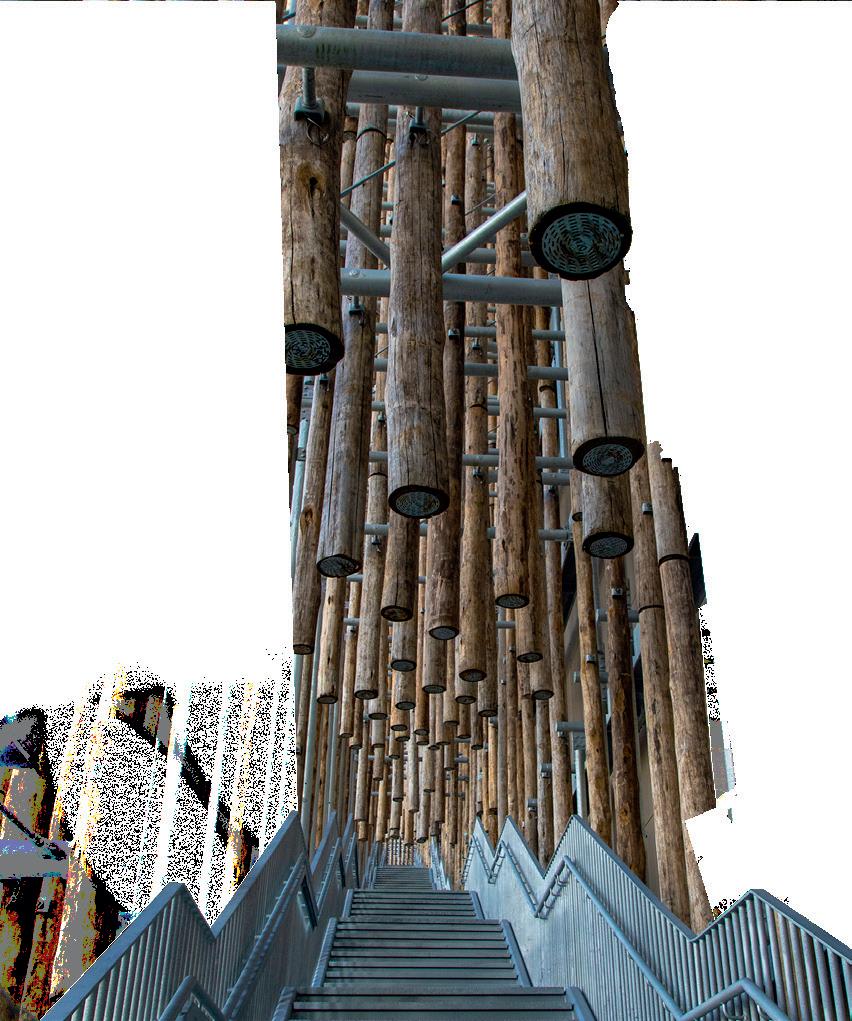
This is the world’s biggest biomass power plant. Machines of that size are not something that suppliers merely have in stock. The machines required adjustment and a lot of changes were made as we discovered new opportunities for optimisation. Thus, we have continued our tailoring of the building to a hardcore and deeply complicated machinery.
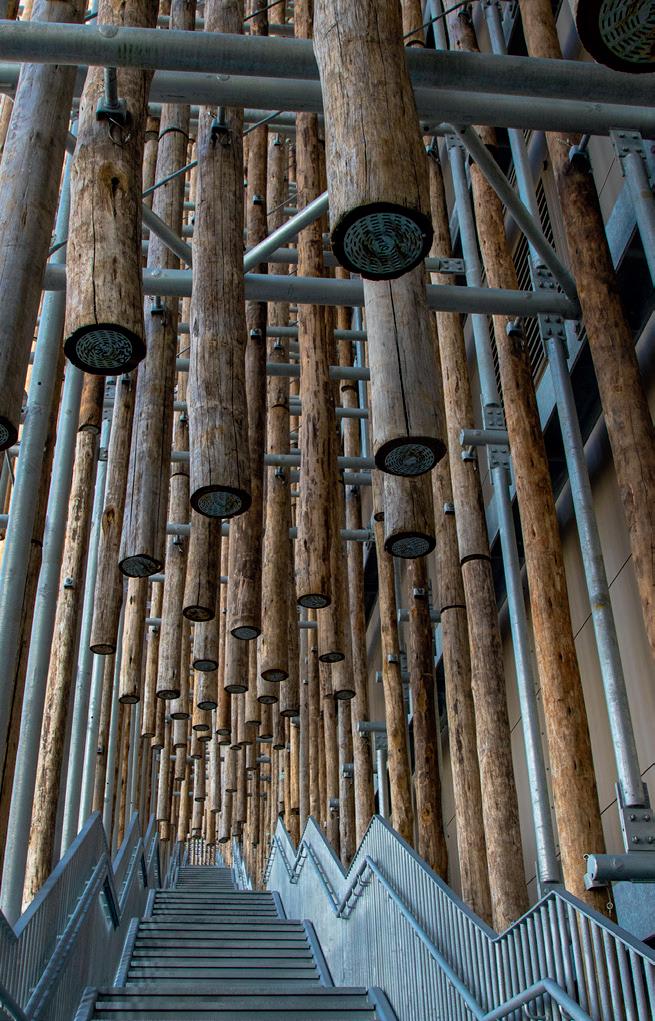
Change management in 3D As one might imagine, this process required an efficient way to gain a complete overview. Because the design has been adjusted over time, the team followed a great information-bearing time schedule with milestones for the project data delivered to the supplier. The detailed plan continued to grow and change management was an important discipline. Naturally, Sten made use of his many years of experience as project manager from other great energy plants such as CopenHill. However, digital tools certainly also made a difference.
3D is the key. Because changes happen constantly, you have to look at the consequences. When one channel moves or a container is enlarged, you have to know what to move where in terms of beams and galleries etc. While you need to keep in mind that the power plant will also subsequently require maintenance.
Therefore, MOE was in charge of an aggregate model that gathers all the supplier’s models in one in order to conduct space management and avoid potential collisions.
Commissioning At the very last stage of the project, MOE had commissioning specialists stationed on site. Because the design was not settled beforehand, function testing, programming and practical commissioning occurred gradually as the project progressed.
As engineers of the construction work, MOE was responsible for installations that work to support the plant. This includes ventilation, cooling and handling of operational wastewater.
From the stairs leading to the roof of the facility, the energy production is visible.