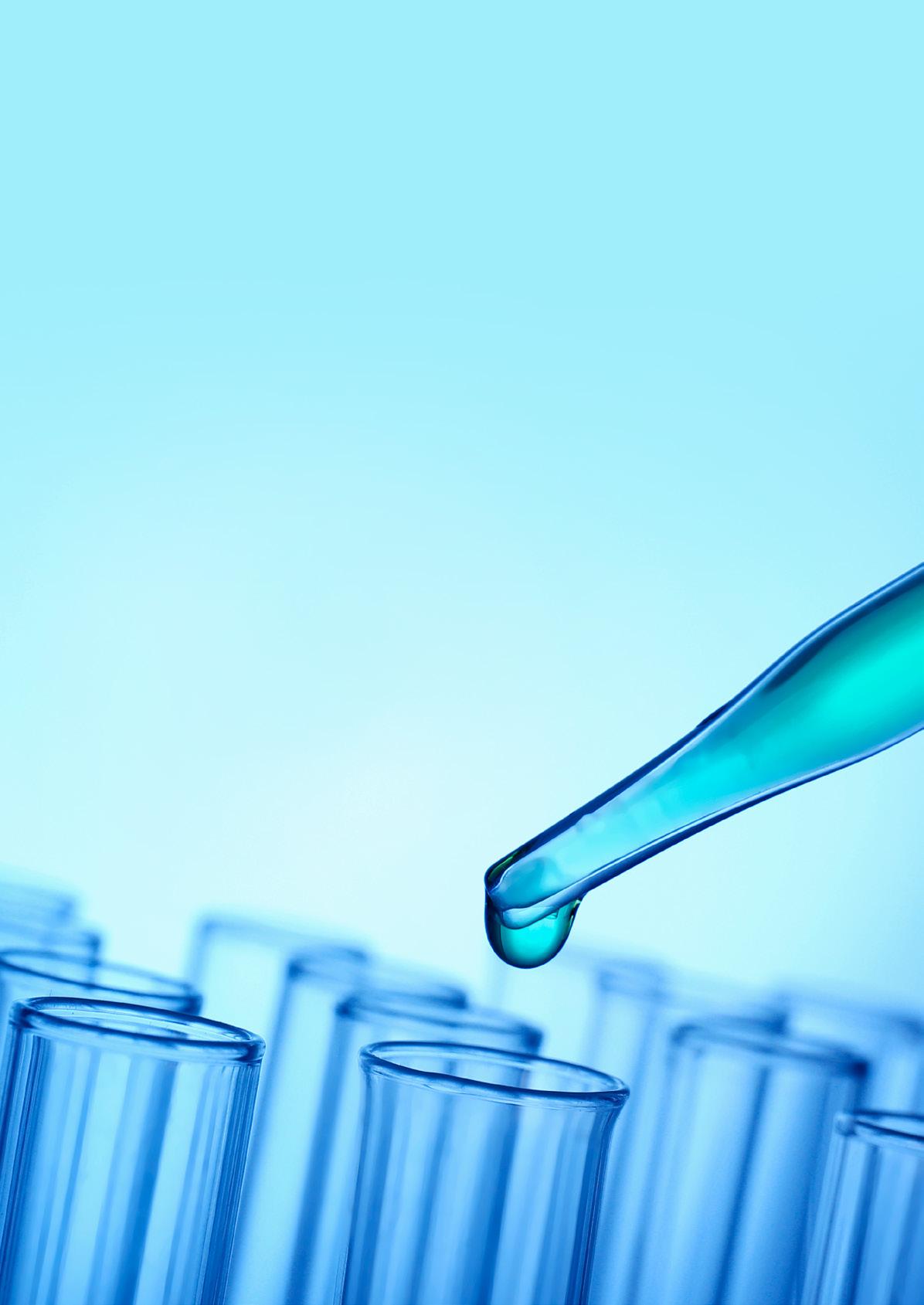
6 minute read
LOW-COST ADAPTABLE CATALYSIS USING NANOPARTICLE MESH
Catalytic processes – where a desired chemical reaction is sped up or enabled to take place in otherwise unsuitable conditions – are at the heart of modern industry, involved in over 80% of manufactured goods. But efficient and cost-effective catalysts are difficult to produce, particularly adaptable methods that can operate at the sensitivity and temperatures required by the UAE’s oil sector.
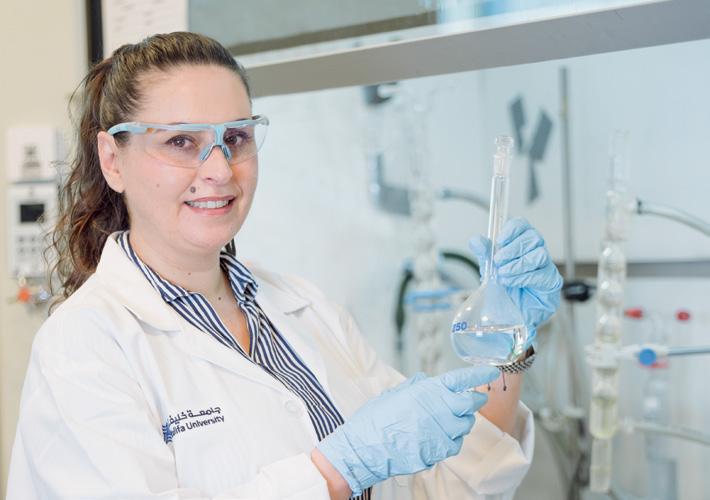
Advertisement
A team from Khalifa University (KU) has collaborated with researchers from Greek and American institutes to leverage nanotechnology to develop a method for making heterogeneous catalysts that are highly effective and specific, using common and low-cost chemicals. The project was led by KU Assistant Professor of Chemical Engineering Dr. Yasser Al Wahedi and jointly funded by the Abu Dhabi National Oil Company (ADNOC) and KU.
Of the three major types of catalysts – heterogeneous, homogenous, and autocatalytic – heterogeneous catalysts account for the lion’s share of industrial catalytic processes, making up more than 85% of all industrial catalysis. In heterogeneous catalysis, the catalyst material – called the active component – and the liquid, solid, or gas that is being subject to catalysis – called the reactant – exist in two different phases. An example of this takes place in your personal car. There, the harmful carbon monoxide gas produced by your car engine is run through a catalytic converter, which has platinum and other metals as the solid catalyst, to produce inert carbon monoxide.
A major challenge in heterogeneous catalysis comes from a trade-off involved in increasing the active component load in the catalyst and the rate at which it disperses through the reactant. The more active component added to a catalyst, the less it disperses through the reactant. In the past decade, scientists have turned to nanotechnology to overcome this challenge, which allows for tiny capsules of the active material to be suspended in an inert support structure with pores or openings between two and 50 nanometers in size. Think of this as a sieve, where the weave of the sieve has tiny particles of active component woven into it, which increases the surface area of the catalytic reaction to make it more productive.
This nanoparticle embedded mesoporous matrix (NEMM) has been trialed in previous studies, but only using low loads of the active component of around 10 weight-percent, as it has been difficult to maintain the active component particle size and dispersal rate in higher loads.
The KU-led research team has developed a method for preparing the active component material and then integrating it into a support structure that is most suitable for high temperature uses. They used iron oxides as the active component, and porous silica to create the support structure, which protected the embedded nanoparticles from damage from the high temperatures involved in the catalysis process.
“The inspiration behind this project was firstly to develop more sustainable catalysts/adsorbents based on more abundant materials like iron oxides rather than rare and costly materials, and secondly, to significantly increase the active component loading through a process of precisely coating the component with a ceramic material that is stable under thermal treatment while being penetrable. With this in mind, we chose to study a catalyst structure made of a sustainable, low cost, and abundant material – silica – and a method of coating the active component with a simple porous ceramic material,” explained Dr. Georgia Basina, a postdoctorate researcher at KU. She was the lead author of a paper recently published by the team in the leading international scientific journal Applied Catalysis B: Environmental. Her co-authors from KU included Dr. Wahedi, Assistant Professor Dr. Nahla Al Amoodi, Dr. Xinnan Lu, and research assistants Omer Elmutasim, Dina Ali Gaber, and Safa Ali Gaber. The team also included Professor Dr. Michael Tsapatsis, Dr. Balasubramanian V. Vaithilingam, and Dr. Dandan Xu from the University of Minnesota in the US; Prof. Dr. Michael A. Karakassides, Prof. Dr. Ioannis Panagiotopoulos, Dr. Maria Baikousi, Dr. Konstantinos Spyrou, and doctoral candidates Georgios Asimakopoulos and Eleni Thomou from the University of Ioannina in Greece; and Dr. Elias Sakellis, Dr. Nikos Boukos, and Dr. Vasileios Tzitzios from the Institute of Nanoscience and Nanotechnology NCSR Demokritos in Greece.
The project had three major steps. The first step was the production of iron oxide particles to the desired ultrananoparticle size of 20 nanometers and below. In the second step, the iron oxide nanoparticles were coated in silicon ceramic. The third step was to grow the porous silica support structure around the silicon-coated iron oxide particles, allowing the silicon-coated active component nanoparticles to become the cores of the support structure. The team then tested the NEMM developed through their innovative method to transform hydrogen sulfide into sulfur.
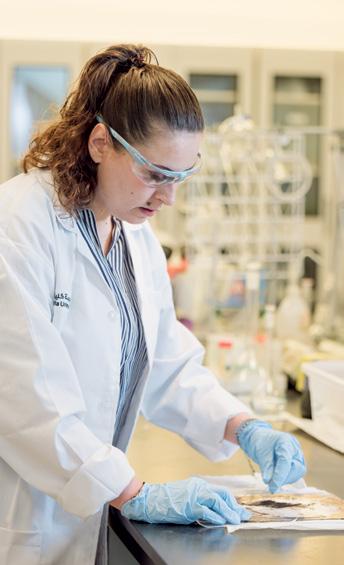
Hydrogen sulfide occurs naturally in oil fields and is a byproduct gas from the oil desulfurization process. The gas is corrosive, flammable, and toxic to humans, which is why it must be treated before use or release. Where large amounts of hydrogen sulfide are produced, it is run through a catalysis
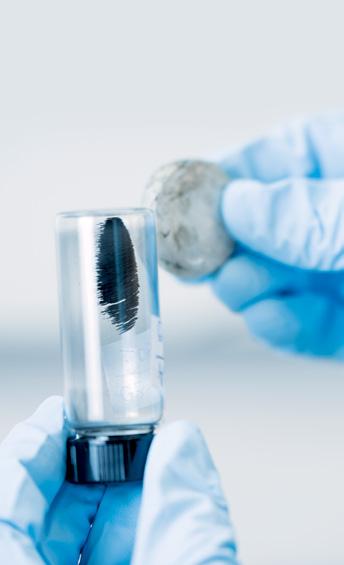
process to transform the harmful gas into sulfur, which is used in many processes and products, like fertilizer, matches, fireworks, and fungicides. The standard industry catalytic processes tend to be high-energy processes that require high loads of catalysts.
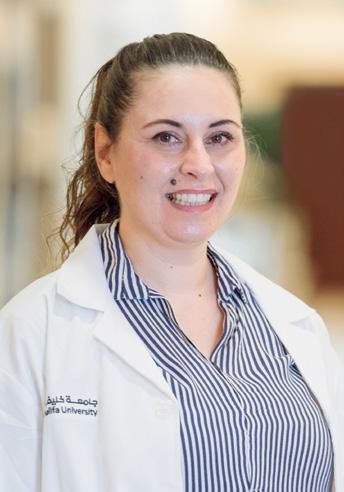
“When subjecting hydrogen sulfide to our catalytic system, we found that the most effective result occurred when the catalyst silicon-coated iron oxide particles measured between five and seven nanometers, with the active iron oxides making up 57 to 73 weight-percent of the structure. This type of catalyst achieved 100% conversion and higher than 90% selectivity towards sulfur,” Dr. Basina revealed.
In catalysis, selectivity and activity are two of the most important factors for effectiveness. Catalyst activity refers to the catalyst’s ability to increase the rate of reaction. Catalyst selectivity refers to the catalyst’s ability to selectively produce specific results through the reaction. The current technologies used to treat hydrogen sulfide require 10 to 100 times more mass than this catalyst to achieve the same level of selectivity demonstrated by the NEMM process. An industrial plant using the innovative NEMM catalyst could achieve reductions of 10 to 100 times in its size and energy footprint, while achieving the same performance.
Explaining the most noteworthy findings from the project, Dr. Basina said: “The achieved loadings of active components reached up to 82% by weight, while their size, morphology, and phase were completely controlled. In addition, the suggested synthetic approach can be extended to several catalytic systems. It is also remarkable that the high active compound loading and stability of these systems were able to be achieved with abundant and low-cost materials, which helps guarantee the sustainability and viability of the process.”
This means that the methodology they developed can be easily applied to other active components and mesoporous material, giving the project a much larger potential impact than just the one demonstrated hydrogen sulfide to sulfur use.
“The technological impact of our catalytic systems research is diverse. These catalysts are able to provide a drastic reduction to the volume of a real industrial process, which in the UAE could directly benefit ADNOC, the UAE’s major oil company. In addition, the more efficient handling of the toxic gas byproduct hydrogen sulfide that we demonstrated, shows that our innovation can improve environmental wellbeing globally and support the UAE’s goals relating to environmental preservation,” Dr. Basina asserted.
The next step for the collaborative NEMM project is to apply their methodology to the development of new industrial and sustainable catalytic systems. The methodology also needs to be scaled up, from the small lab-based processes to the substantial loads required for industry.