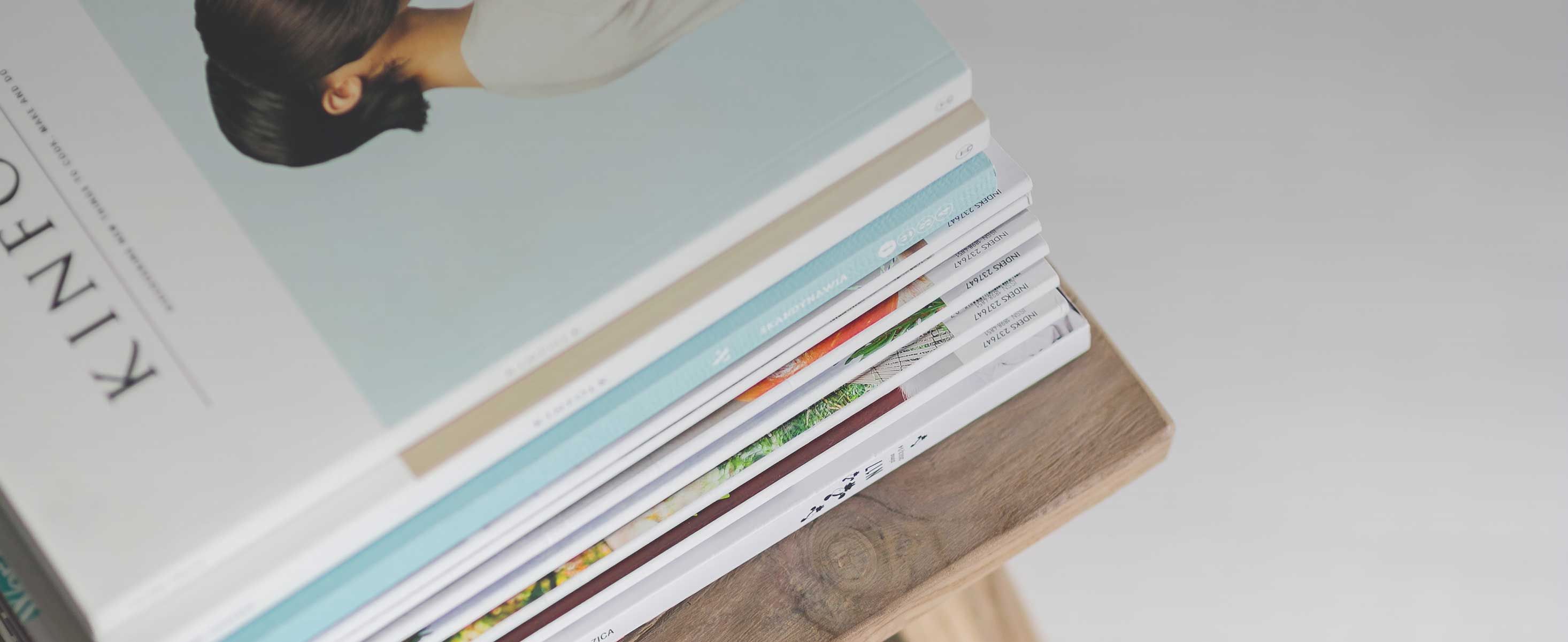
42 minute read
©Teaching and Learning Case Studies
Publishing
Jun Loh, Kulappurakkal Abdulrasheed Ambalavan
Moshood Olawale Fadeyi
Module instructor, case study designer and advisor, and story writing advisor
Engineering Cluster, Singapore Institute of Technology, 10, Dover Drive, Singapore 138682
Corresponding Email: fadeyi.moshood@singaporetech.edu.sg
Abstract
A case study research assignment was given to students in a module titled Construction Management using BIM to develop their understanding of how an unforeseen disruptor could influence construction management practice and the risk of (lean) waste occurring in a construction management work process. The disruptor of interest was COVID-19, and the assignment was done in groups of 2. Each group was required to centre their interview questions around their chosen company’s construction management practice before and during COVID-19 and after COVID-19 restrictions were lifted. The student authors of this paper, under the direction of the module instructor, wrote a non-fiction story as other students in the module. The student authors of this paper wrote a story on the journey a construction company staff went through to convince senior management of his company to invest in digital solutions to aid in the effective streamlining of their work processes to increase the value delivered to the company and all stakeholders of their projects. The module instructor gave the case study research assignment as part of a learning journey designed to invoke critical and reflective thinking that induces the learning needed to develop an educational experience in construction management value delivery. Self-reflections of the student authors on the learning journey suggest the aim was achieved. The students' professional capabilities improved, and they were ready to contribute the experience gained from the learning journey to the industry. This paper contributes to the educational experience development needed by students, industry professionals, and academics to improve value-oriented productivity in the construction industry.
Keywords: Construction management; Digital transformation; COVID-19; Value-oriented productivity; Applied learning; Storytelling
CHAPTER 1: IMPERFECTION
Morgan was a full-timer at XYZ Construction Pte Ltd (XYZ), a renowned construction company that dominated the construction industry with its specialisation in Civil earthworks and infrastructure projects. Morgan graduated from the National Technological University of Singapore, also known as NTU, and had completed a major in Civil Engineering with First Class Honors.
During his university days, Morgan was known for his passion for integrating digital technologies into his daily life, such as using drones to create a video montage for his graduation trip with his classmates and even infusing the use of Virtual Reality (VR) goggles for his Final Year Project (FYP). The FYP titled “Improving the quality of life of construction workers” involved the design of a solution to let construction managers feel the challenges that the foreign workers faced on the ground daily. However, after joining the workforce for the first six months, Morgan’s company (XYZ) and supervisors seemed extremely reluctant to incorporate digital technologies into the current work processes.
In the fast-paced and ever-changing environment in the construction industry, there was only so much Morgan could do as an individual to influence his seniors and colleagues to integrate digital technologies into the current workflow. Morgan felt very dejected, but he remained positive and understood the importance of going with the flow and management style of the company, as he knew that he still had a lot to learn from his seniors.
After working for several years in XYZ, Morgan was tasked to manage large-scale projects by the Ministry of Health (MOH) and Mass Rapid Transport (MRT) projects by the Land & Transport Authority (LTA). Right before COVID-19 hit Singapore at the end of 2019, Morgan was appointed Head of the Department of the Construction Project Scheduler at XYZ. He held a huge responsibility for all major project scheduling for XYZ.
Morgan soon fell into the corporate cycle of purely listening and following his bosses’ instructions. He had forgotten the importance of trying to implement digital solutions in his department to ease the workflow and enhance the efficiency of his engineers and technicians.
As soon as COVID-19 hit Singapore, the construction company with the highest market share in Singapore took a significant downturn as they had little to no time to react to this sudden and deadly pandemic. Within days, all construction projects had come to a halt due to the widespread COVID19 virus. Construction workers were one of the most vulnerable groups as they resided in dormitories. In Singapore, a regular dormitory has 12 foreign workers staying in a 12-meter square room.
With little or no space to even move around the room, COVID-19 infection was inevitable for this group of people. Before Morgan could react to this COVID-19 situation, the Ministry of Health (MOH) had ordered a stop work and quarantine order for the construction sites with mass infection in Singapore. XYZ took a big hit from the mass infection of ground staff.
Morgan was under immense pressure as all his construction schedule, resource management, and budgeting were thrown off the bus within a short span of 2 weeks. There were projects that were due to be handed over to clients but were put to a stop. Morgan’s department had suffered from a loss of 2 million Singapore dollars within 2 weeks as they had almost 20 sites with 40 units of rented cranes and excavators.
Interest rates had rocketed to record highs due to the uncertainty of this COVID-19 virus, and the company wasted a lot of time waiting for instructions from its senior management on the next viable step to take. Time was ticking, and the company was under huge amounts of bank loans to sustain the expenses for the large-scale projects on hand.
On the other hand, the company headquarters was also facing the same issue with their CEOs, Chiefs, and principal engineers infected with COVID-19 and had to undergo a 1-month quarantine period. During these few weeks, the company's senior management, who was supposed to decide on the company's direction, lost communication as they were all under quarantine.
As the lone survivor in the company that had yet to be infected with the COVID-19 virus, the senior management gave Morgan a heavy responsibility to connect the team together in 24 hours by sourcing for solutions to allow them to conduct emergency meetings to combat the sources of waste that were caused by the COVID-19 virus. The waste in this context means consuming resources, e.g., time and money, with little or no usefulness delivered.
Due to the short period assigned to Morgan, he knew that to come up with an effective solution; he had to reflect on what could have been the root cause that might have caused the communication breakdown and what could have been done during his early days in XYZ. He immediately started to link his reflections to the possible sources of waste that might be contributed by COVID-19 that limited the level of usefulness that can be derived from the company’s invested resources. Morgan knew that without proper root cause analysis, he would be unable to develop an effective solution to bring communication within reach of his senior management team.
Morgan researched the COVID-19 virus and found out that it transmits through air and surface, but mainly through the air, making it spread very fast. All this boils down to one single source of transmission, physical human interaction. Morgan proposed the usage of the current digital platforms, such as group calls on landlines or WhatsApp.
Still, he was heavily reprimanded when the team could not share slides, shop drawings, project schedules, and finance data sheets on the above-mentioned platforms. As such, Morgan continued his journey to source a better digital communication platform for the team.
Morgan was 22 hours into his task and had 2 hours remaining. On the verge of giving up, Morgan came across an online platform named “Zoom”, a digital platform developed by a communication technology company in San Jose, California. Zoom can allow people to connect online with the ability to enable participants to share their screens, host meetings securely, and provide a stable and clear connection with a subscription rate. Under urgent circumstances, Morgan immediately subscribed to Zoom and proposed this solution to the senior management. They were all pleased and commended Morgan’s effort to source digital platforms to allow the team to communicate remotely without needing physical interaction.
CHAPTER 2: RESISTANCE
After this episode of sourcing for methods to improve connectivity among the directors and stakeholders with digital technology, Morgan strongly felt that there was a need to implement a change in the existing construction management strategies in terms of construction scheduling, resource management, budgeting, pre-construction work, managing of construction works, project handover, completion, and close-out methods before another major catastrophe happens.
As the company was still under immense pressure exerted by the persisting COVID-19 situation, Morgan started to burn the midnight oil to research possible proposals for digital transformation and technologies to combat COVID-19 and prevent possible revenue loss and disruption of operations in the company. After a week of in-depth research and sleepless nights, Morgan arranged a meeting with his direct reporting officer, Jon, who was the Chief Operating Officer (COO) and co-founder of XYZ.
Morgan started presenting on the slides that he prepared over the past few nights and started with a forecast of what might happen to XYZ if digital transformation is not implemented within the company in the next 3 months. Morgan further shared some findings on the sources of waste that COVID-19 can cause. Before proceeding, Morgan clarified that sources of waste mean those things that led to resources being consumed without getting usefulness or not at the level corresponding to the level of invested resources. He also noted that the examples he was about to give were tips of the iceberg on how the sources of waste exist in their construction management work process.
Morgan shared that the delay caused by COVID-19 had led to the consumption of time and other resources, without little or no usefulness (revenue) to the company and the usefulness the company could provide to all other stakeholders involved in their projects under construction. “The unnecessary consumption of resources during this delay is a source of waste called Waiting,” Morgan said.
Morgan continued by saying the value delivery to the company and all other stakeholders involved in their projects had significantly compromised due to delay caused by COVID-19, and the compromise could be deepened if nothing is done to reduce the extent of the delay. For context, he shared that waste could occur when the project is waiting for the management and project scheduler to provide the direction and schedule to the downstream workers, as time, money, and resources will still be consumed during this waiting period.
Morgan used the recent COVID-19 event as an example. Multiple projects stopped while the company was still paying bank loans, equipment rental fees, and construction workers’ wages while waiting for Morgan to source a viable digital platform for the management to communicate and make decisions. Jon, the COO, nodded silently and unanimously agreed with Morgan as he felt this experience first-hand. As Morgan noticed that Jon seemed to be slightly receptive to his argument point, Morgan gained more confidence in his presentation and moved on to the second point, which is transportation.
Morgan shared that the company has been spending much of the project budget to move workers in staggered hours and buses to worksites due to the Safe Management Measures (SMM) implemented by MOH. The unnecessary spending to move workers is a source of waste called Motion. He said workers had to stay at least 1 meter apart, and a regular bus that previously transported 48 workers per trip can only transport 12 workers per trip now. This is a massive fourtime increase in the overall transport expenses for the company.
Morgan said the company is currently pouring money and resources into the transportation of workers to various worksites without proper planning and consideration of the use of digital technologies to reduce the money invested in this process. He said there were also several instances on their construction sites when instruments, equipment, and materials were transported from storerooms, typically scattered around at the construction sites, to where they were needed several times unnecessarily. Sometimes, they were transported to where they were not needed and had to be transported back to stores to avoid damage. Unnecessary transport of inanimate objects, especially on a long distance, is a source of waste called Transportation and could be avoided with proper planning and effective communication.
Morgan shared that if there was proper planning with the aid of digital technologies, the company would have a smoother operation process and thus significantly reduce the chances of waste produced in this process. Jon scratched his head, immediately unmuted his microphone, and asked Morgan, “How?!”. Morgan rebutted confidently, “There is only one way to find out, which is to put me in charge of this digital transformation.’ Jon smirked and muted back his microphone.
Morgan said that waste due to motion also happened when workers in XYZ had to physically visit the store to manually tabulate the number of screws in the drawer every month. He said the amount of time required to count, tabulate, and update on paper records on the number of screws (of which XYZ has several hundred types of screws) has led to the unnecessary consumption of time to update and process the procured screws.
Morgan told his audience that the unnecessary time spent processing and updating the required information on the screws available is a source of waste called Over-processing Despite this unnecessary consumption of resources, errors in the information gathered still occur several times. Morgan said this source of waste is called Defect
Many times, for reasons beyond the project engineer's control, the project engineer always ordered more screws for a project than needed to make sure screws were available when needed. The store man had to find new spaces to store the screws. Furthermore, the store man had to spend two weeks confirming the order as the store man had to manually calculate the availability of the screws that the engineer requested.
Morgan said the source of waste, called Inventory, occurs when resources are consumed to manage acquired information, instruments, equipment, and materials that are not processed or acquired when it is not time to process them. Morgan said inventory waste is driven by the need to cover up the effects of an inherent problem in a process.
Morgan further said the unnecessary consumption of resources to deliver more screws than are needed, before they are needed, or faster than are necessarily led to a source of waste called Overproduction. Jon looked shocked as he was totally unaware of this issue happening on the ground.
Morgan further shared about the inventory management procedures of Antigen Rapid Test (ART) self-test kits, a newly implemented regulation that all workers must be tested and cleared of the COVID virus before entering the construction site. Morgan said he received feedback from his newly appointed ART manager, Rahman, that he was facing inventory issues as a lot of time is wasted managing ART kits
Rahman said these consumables come in different batches with multiple batch numbers, and he had to find new spaces to store them. Morgan told the audience that the MOH requires weekly updates on the number of ART kits required and used, with proper documentation and endorsement by the company. He said Rahman had to manually count the number of ART kits in the entire store daily as they come and go quickly.
Morgan shared that Rahman was appointed as the ART manager as he was a project coordinator for XYZ and had good connections with the ground staff and management. Morgan said Rahman was the only point of contact between XYZ and XYZ’s on-site construction workers. However, after being appointed as an ART manager for XYZ, all he had was sleepless nights counting and distributing ART kits to staff, and he did not have time to do his job as a project coordinator. Morgan said the poor usage of Rahman’s professional capability and time led to a source of waste called the Non-usage of talents.
Morgan said Rahman was on wits' end and came to share his opinion that if the company had implemented digital technologies to sort out store items and could tabulate automatically with technology, he would not be in such an undesirable state now. Morgan cautioned that before digital solutions can be adopted effectively, they need to have an eye on how to continuously design their construction management work processes to eliminate or reduce the causes of the sources of waste in the processes.
Morgan said the knowledge, understanding, and skills in designing effective work processes will guide us on what, why, where, when, and how digital solutions can be adopted and who can adopt them. "We need to know how to solve problems in our construction management work processes. Digital solutions cannot do that for us. The digital solutions, if adopted appropriately, can only speed up the rate of solving the problems in our work processes, reduce unnecessary consumption of resources, and maximise usefulness derived from resources invested in the process. Adopting digital solutions can be counterproductive if what is needed to adopt them effectively is not given due consideration." Morgan advised.
After hearing this situation that was experienced by the ground staff, Jon was left in silence and felt that as the COO of the company, he had zero awareness of what was going on the ground as his only concern and focus was XYZ’s future development and yearly financial statements.
After Morgan ended his presentation, Jon privately shared with Morgan the events that had happened previously to the company, which resulted in the strong resistance to change to embark on the usage of digital platforms in XYZ.
Jon shared that during the early stages of XYZ, XYZ did attempt to use cloud solutions to store confidential project information, drawings, financial statements, etc., on the cloud as XYZ’s stakeholders highly recommended enhancing the ease of access to documents and improving the efficiency of communication with both internal and external stakeholders.
Jon mentioned that at the beginning of using the cloud server database, it was revolutionary as it saved a lot of time, operating, and manpower costs for the company as project engineers from various projects would not need to manually search for contract documents, shop drawings, construction methods in the document room after this implementation. With a click, all the information required will be displayed, and all the stakeholders in the company were very satisfied with this new implementation until a sabotaging event happened internally.
Jon shared that there was an apparent data leak in the cloud, and XYZ’s highly confidential data, drawings, construction methods, client data, etc., has been leaked into the industry. Jon said the company suffered from heavy losses as they failed to ensure the safety and security of the confidential information that was submitted by the clients and had to pay for liquidated damage.
After that incident, the CEO of XYZ decided that since the company was unable to locate the source of the leak, they shall eliminate the use of digital platforms and technologies to prevent any future occurrence of such events. Therefore, till today, the company has been running on manual modes of operation in as many aspects as possible and is resistant to digital transformation.
After listening to what Jon said, Morgan let out a loud sigh and felt the same sense of dejection that he felt when he first entered the company. However, Jon reassured Morgan that senior management has heard and appreciated his words and will be well-considered for future improvement and developments. Morgan whispered to himself, “It’s now or never…”, as Morgan knew that the company would soon face imminent danger.
CHAPTER 3: REVELATION
By March 2020, 3 months into when the COVID-19 situation peaked, the virus was engulfing not only Singapore but the rest of the world. There were almost 400,000 confirmed cases worldwide, and 20,000 deaths (approx.), and it was increasing rapidly. By April 2020, the World Health Organisation (WHO) reported there were over 1 million cases of COVID-19 that had been confirmed worldwide, with an increase of more than tenfold in less than a month.
At this point, the senior management team members were racking their brains on how to keep the revenue stream coming despite the rapidly evolving COVID-19 situation worldwide. Some of XYZ’s clients were from the United States, so they could not visit the site in Singapore due to the mass lockdown and travel restrictions.
These restrictions greatly impede the construction schedule regarding handing over, project closing, and defect clearing, as the clients were unable to physically visit the site for site inspection. Soon after, requests to use digital solutions by most clients came in as most of the clients, professional engineers, and consultants were either in quarantine or stuck overseas.
As XYZ was unable to produce concrete evidence with proper handover paperwork online to their clients from the United States due to the lack of proper digital copy documentation, the project was unable to close timely, and a lot of resources, time, and money were wasted in the process. The clients were not convinced that the project was constructed as per the design as there were too many uncertainties due to COVID-19.
Manpower and materials costs had greatly increased, and it was an open secret that construction companies were trying to cut costs by managing their manpower tightly. This might have led to comprises in the safety standards and eventually contributed to the highest amount of death rate in the construction industry in Singapore in 2022. The construction industry was desperate for manpower and took in any available foreign talents and disregarded the fact that some of them might not be competent enough to do the work as most of them were looking to earn a living to support their family in their hometowns.
Most XYZ projects faced a lot of rework and delays on handover as customers were not convinced and satisfied with the construction outcome. This has greatly impacted XYZ’s revenues as they were still on bank loans, and with the lean amount of manpower available, they were all mobilised to clear defects. After that, the senior management felt that the only way to maintain their revenue stream to sustain operations was to bid for new projects and allow the company to be exposed to new income streams.
As such, XYZ’s tendering team started to take on new projects as the CEO felt that COVID-19 restrictions should not hold them down, and they were already losing a lot of money. As the tendering team constantly sources new clients and projects, they managed to bid for a substantial number of new projects as most of the small and medium-sized enterprises (SMEs) construction companies were having the issue of lack of manpower and could not bid for new projects.
Morgan was at a loss for words when he had to manage multiple new project timelines and plan for scheduling, budgeting, resource management, and pre-construction works. Each task had multiple sources of hindrance that affected the effectiveness of mobilising resources to the construction site and delivering value to the company and other stakeholders of their projects. XYZ managed to bid for one of the major projects: the construction of a community hospital in Singapore.
As this project was large-scale, XYZ’s COO, Jon, was tasked to oversee the project from the planning stage to the handover stage. At the pre-construction survey stage, as the head of the project scheduler, Morgan reflected on the possible hindrance in terms of finance, access, services, permit, notification, pre-construction survey, and survey controls as he knew that the existing measures must be reconsidered due to the new regulations and restrictions that the government has set.
With all the above considerations considered, Morgan realised that the time needed for this construction was four times more than their previous projects. The budget required was projected to be 1.5 times more than the allocated budget. Morgan did further analysis and identified that most of the manpower and resources were invested in transporting manpower on-site to conduct physical site surveys, take measurements, monitor construction progress, and provide real-time updates to closely monitor the site situation.
Morgan thought that if XYZ had been receptive to his presentation and implemented digital solutions many months ago, the company would have been more prepared for such a major project on hand to increase the value delivery to the company and their projects' stakeholders.
Morgan presented the above information to Jon, and Jon was in disbelief. Jon knew that the company resources were stretched as they had projects that had yet to be handed over, new small projects, and this major project. The company was back in a dire situation as Jon only forecasted the project manpower and resources based on the past projects that were completed before COVID and did not have any references on the additional considerations and resources required for the current and new projects. However, it was too late for XYZ as the contracts had been signed, and if they were to forfeit any projects, they had to pay for liquidated damages to the client.
Jon told Morgan that the issue would be highlighted to the CEO, Kenneth, and discussed it with the senior management. After Morgan left Jon's office, Jon thought about the flaws of the company and possible digital solutions that were proposed by Morgan months ago. Jon felt a sudden enlightenment and saw hope through the end of the tunnel. Jon was really on the wits' end. He immediately called Morgan back and told him to directly represent the deck of slides he presented four months ago to Kenneth.
Kenneth was impressed by the analysis and solutions provided by Morgan and agreed to Morgan's request to put him in charge of the digital transformation of XYZ. Morgan was pleased and started on his journey to pursue digital transformation to change the company’s construction management process from the valuable lessons that were learned during the COVID-19 period. Morgan was on the road to salvage the dire situation that the company was landed in due to the reluctance of change.
CHAPTER 4: PURSUIT
Given the critical situation that XYZ was in, XYZ’s CEO, Kenneth, set up a programme in 2022 to achieve the following goals in all construction projects on a “4-year plan programme” under the company's “mission”.
Prior to the experiences and events that have happened to XYZ in the past two years, Kenneth finally decided to set the company’s goal towards the route of the digital transformation agenda of the construction sector with the following mission statement.
“To provide safe, reliable, and quality service by adopting innovative technologies and fostering a conducive, caring environment to grow our people to optimise their talents and achieve enhanced value delivery for customers”.
Morgan briefed Kenneth on how the Singapore construction market trends were compelling their company to switch to digital construction, as the uncertainty and complexities associated with the construction projects were increasing daily. Morgan emphasised that the COVID-19 pandemic has proved to be a catalyst towards this step as digitalisation in the construction industry is long overdue.
Moving towards this step, one of the recent achievements that XYZ Construction Pte Ltd obtained was that they were ranked as one of Singapore's Best Employers in the Year 2022 by The Straits Times. XYZ became a forerunner in business transformation through technology and digitalisation, it had invested hundreds of thousands in procuring system solutions to replace manual work and upskilling employees.
In many cases, several handover inspection-related meetings had to be cancelled and postponed due to the challenges and restrictions of meeting in person. As consultants and clients were transitioning to working remotely from home, the main challenge that they faced was the accessibility of the necessary information and documents for the project. This resulted in waste due to the additional waiting time required for the project engineers to send the project documents to consultants and clients for vetting and approval.
This has triggered Morgan to think of implementing a digital platform for accessing the submitted drawing and associated documents remotely rather than the physical verification at offices and sites, which consumes more time. Morgan also explored the possibility of using a digital platform to seek approval for a permit to work and requesting site inspection by uploading the required documents to the platform.
Morgan’s project team decided to gradually implement the digital application in major construction activities like Budgeting and cost estimation, Resource Management and Scheduling, Preconstruction works and Safe Working Environment, Managing Construction works, Inspection, and Project handover. On the road of pursuing digital transformation for XYZ, Morgan went full speed ahead and tried to overcome all adversities faced during the digital transformation journey.
CHAPTER 5: UNCERTAINTIES
Due to the negative impact of the COVID-19 pandemic on construction activities, such as delays in material delivery, shortage of materials, idling of resources, poor management of construction works, etc., Morgan and his company thought of implementing some strategies to minimise these negative impacts.
After having a few online discussions and meetings with the project team, Morgan and XYZ realised the approach for effective improvement would be through the effective implementation of digital solutions. Digital solutions would aid the effective usage of all available resources, thereby minimising anticipated wastages.
Despite spending time and effort on implementing digital solutions in site work, Morgan had always received an uncooperative response from the site team and almost failed to deliver. A few had succeeded in the initial stage, but the project team struggled to apply the digital technologies at a large scale. The site and office workers found it difficult to adopt more new technologies and showed the tendency to return to their old ways of working.
The following Morgan’s experience provides insights on the importance of reducing waste sources in the work process before implanting and for effective implementation of digital solutions. The experience occurred before, during, and after COVID-19.
Budgeting and Cost estimation: Morgan started to re-study the money required to take a construction project from start to end, including all associated costs and expenses that need to be spent during the building or construction process. Morgan worked with the quantity surveying and procurement department and attempted to forecast all costs in a construction project, also how to leave some buffer room in the budget to account for any emergencies or unexpected costs.
At some point, Morgan realised that he could not stay within the budget and identified that some of the project work was continuously going over budget. This might have been caused by failure to ensure that the projects stayed on budget and poor estimation of how much the project will cost. Morgan was aware that the consequences of bad cost estimation include compromise to the project's value-oriented profitability delivery, inaccurate distribution of resources, and bad decision-making because inaccurate cost estimations will result in inaccurate financial data.
Morgan's internal checking revealed a few notable reasons for the bad cost estimation of the project. Estimation processes were often justified based on experience and gut feeling due to various reasons such as lack of data or time. As would be expected, these estimation methods were subjected to human errors and biases, which interfered with the cost estimation accuracy. It was normal practice at XYZ to look into expenses incurred in a previous similar project while determining the project cost or budget. This way of costing is flawed, as every project is unique, so using different costing approaches and multiple project references for each project is good.
Morgan proposed to top management to train the quantity surveying (QS) and procurement department to use, learn and apply technologies like building information modelling (BIM) software, which can enhance the efficiency in generating accurate material quantities. By linking the generated quantities with cost databases, it would be easier to accurately estimate the cost involved in the project. However, as most of the existing QS and procurement department staff were of age, with limited to no technology literacy, Morgan was faced with a huge barrier to training the department to use the proposed BIM software.
Resource Management & Scheduling: Morgan used to get frequent feedback from subcontractors that the site was not ready for their respective work and always had other contractors working on the same location and needed to wait further, which caused the wastage of resources. Morgan then assigned some Deputy Project Managers (DPM) or Engineers on the spot to somehow arrange the site for the sub-contractor to mobilise resources and start their work. The client or consultants started to reject or cut down the submitted monthly progress claim and informed XYZ to amend the claims based on actual site condition and progress.
The client had been using their qualified site supervisors (QSS) or resident technical officers (RTO) to collect the site information per site condition and to find any discrepancies in site progress. Cutting down on the progress claim put Morgan in a difficult situation, as there were insufficient funds to release to various sub-contractors for their work claims. As a result, the sub-contractors started to complain to the headquarters and project director about this issue.
This made Morgan think about why there was insufficient actual site progress as projected during the planning phase, even though the planned resources were on site and activities had been carried out. After reviewing the actual site condition with the construction manager and planning engineer, Morgan understood that some activities were not aligned with the actual sequence of site works, resulting in two or three sub-contractors working at the same location.
Due to the limited space on-site, it would not be productive for two to three subcontractors to squeeze into one location on-site. Many subcontractors working in a limited space can cause defects in work done, delays in work progress and increase the risk of safety problems on site.
Morgan realised there were problems in certain areas of his project scheduling process, as it failed to capture or forecast the actual site condition for those activities that could have been carried out sequentially or concurrently. Morgan started to explore solving this repetitive issue and came to learnt about the application of building information modelling (BIM) software for project scheduling and sequencing.
Preconstruction works: Upon recommencement of site works after the circuit breaker (total shutdown by the government because of COVID-19), Morgan discovered the potential room for improvements for the project team in preconstruction works that were carried out during the initial stage of the project before COVID-19. New additional measures adopted in the construction site during the COVID-19 pandemic period had acted as an eye-opener to Morgan and the team to continue to follow the measures for subsequent projects.
These measures include the additional steps taken on categorising or zoning work areas, managing and deploying site workforces, deriving and reviewing site utilisation and site traffic management plan, evaluating available areas on site, and investigating and surveying existing elements and adjacent structural items.
Managing Construction works: COVID-19 and the subsequent circuit breaker revealed and exposed the outcomes of XYZ’s underlying causes of poor management of construction site works. The impacts of ineffective site management practices include the increment in construction cost, revenue losses, inability to complete the project within the scheduled time frame, and poor quality, quality, and safety of construction. The unwanted impacts also include an increase in the level of discomfort, inconvenience, and poor awareness experienced by stakeholders involved in the project.
Morgan realised that the essential causes of poor site management are the quality of the site management workflow design, lack of proper coordination, and poor communication. Morgan believed with good knowledge, understanding, and skills of how to eliminate or reduce these factors, using the right talents, the benefits inherent in digital solutions adopted for effective site management will be enhanced.
After gathering advice and information from clients, consultants, agencies, and contractors, Morgan proposed a programme for implementing proper site management practices, which includes providing sufficient training to project staff and conducting workshops about the new methodologies and digital solutions.
Morgan also recommended the installation of CCTV cameras to monitor the site works, using of drone camera to capture the site progress and to determine actual site condition, and safety alarming tools like noise meter, vibration meters, etc., which integrates with common communication platform applications like WhatsApp, SMS to notify stakeholders the various alert levels (i.e., High or low-level alarms for noise, vibration, etc.).
Inspection and Project handover: Morgan recalled significant delays in inspections and difficulty handing over the project were also reported, especially during the COVID-19 and post-COVID-19 pandemic. Due to the COVID-19 pandemic, all parties were transitioned to the new working format, which resulted in delays in completing inspections and the certification of works, especially for the consultant’s and client’s representative. There were many cases in which the various stakeholders were unable to stick to the initial timeframe to complete the certification of completed work.
Consultants and clients registered their concern to Morgan that there may have been work done without adequate independent supervision during COVID-19 and post-COVID-19 period since there were restrictions to site staff entering the site. Consultants and clients did issue guidance to site staff or inspectors, which ensured that they should not be signing off-site works based on remote inspections or photographs. However, the number of inspections of projects has fallen significantly during this period, which means that defects are less likely to have been identified during the handover stage.
This eventually led to unwanted rework during the defect liability period (DLP) when the clients picked up the defects and requested rework. This has further contributed to the unwanted manpower and resource usage for XYZ during the COVID-19 period. Amidst all the uncertainties that Morgan has faced, he was determined to be steering XYZ towards their goal, which is the “4year plan programme”.
CHAPTER 6: TRANSFORMATION
The introduction of the company’s “4-year plan programme” together with circumstances caused due to the COVID-19 pandemic, has forced Morgan to rethink traditional construction practices and to embrace digital technologies or new methodologies to adapt to the new normal and for the future. In addition, the Project Director, Aaron, called Morgan to follow-up on actions being taken for the implementation of digital technologies or new methodologies.
Morgan recalled a telephone conversation with the Project Director, Aaron
Aaron: Good morning, Morgan. I wanted to talk to you about implementing digital construction methods or new methodologies for our value delivery solutions. I know this was something we talked about before, but I wanted to see where we are at with it. We need to present a detailed implementation plan to our bosses very soon.
Morgan: Good morning, Boss. Yes, the implementation of new construction methods is something we have been exploring for a while now. I have done some research and have identified some potential solutions that could work well for our company.
Aaron: Nice. That’s great to hear. As I asked before, did you manage to find the potential benefits of implementing new construction methods or digital solutions? Remember, it must be attractive and convincing to our bosses.
Morgan: Well, one of the biggest benefits is increased efficiency. With digital solutions, we can automate many of the manual processes currently slowing us down. This means we can complete projects faster and with fewer errors. Additionally, we can use data to optimise our processes and improve our decision-making.
Aaron: Hmm, sounds good. Are there any challenges we might face while implementing the new construction methods?
Morgan: One of the biggest challenges is the upfront investments. The new methods require new technology, software, and training or workshops. We would need to invest in these things before we could see the benefits. Additionally, there might be resistance from some of our staff who are used to working in their traditional ways.
Aaron: Noted. So…How do you propose to address these challenges?
Morgan: For the upfront investment, I have arranged a discussion with the planning department to create a detailed cost-benefit analysis outlining the potential return on investment (ROI). This would help us to justify the proposed investment to the bosses. As for staff resistance, we could provide comprehensive training programs to ensure that everyone is comfortable with the new technology and understands the benefits.
Aaron: Okay, let's get started on that. Thanks for the update, Morgan.
Morgan: Thank you, Boss. I'm excited about the potential of new construction methods for our company.
Morgan embarked on a transformation journey for XYZ and was nourished by the experiences that the COVID-19 pandemic had taught him. Morgan spent weeks on various construction projects to understand the pain points the ground staff faced before, during, and after COVID-19 to better ensure that the digital transformation would be a smooth sailing journey.
After months of blood, sweat, and tears, with assistance and collaboration over multiple departments, Morgan transformed various key departments, implemented new planning considerations and digital solutions/ platforms, and created new initiatives for XYZ. The following transformation was achieved.
Construction of temporary quarters for workers nearby the worksite
As part of the introduction of the new methodology, Morgan’s Project coordinator, Rahman, strongly suggested arranging workers’ accommodation near the work site as they had done during the COVID-19 pandemic period. During the COVID-19 pandemic, the company had constructed temporary quarters (CTQ) for accommodating workers involved in that specific project to avoid the spreading of COVID-19 virus among the workers due to mixing them with workers from different worksites at their dormitories.
Apart from lowering the possibility of the virus spreading, Rahman believed that having separate workers’ accommodation near the worksite could bring several other benefits to the project. Upon implementation, Morgan personally observed an increase in productivity, as workers did not have to travel long distances to get to the worksite and wouldn’t become tired and stressed easily. Nearby accommodation reduced travel time, and workers were well-rested and fresh when they reported to work.
Rahman shared with Morgan that the workers started to have better team bonding when staying together in the same accommodation, and they developed stronger relationships and a sense of togetherness. These changes improved teamwork on the worksite, leading to a more efficient and productive construction process, mutual understanding, and better communication.
At the same time, Morgan recalled his conversation with the transport coordinator, Kumar, where he mentioned that commuting workers over long distances daily increases transportation costs and adds to the overall project expenses. By providing nearby accommodation, XYZ had a great reduction in transportation costs, and Morgan was able to keep the project within the planned budget.
Enhancement of IT cum digital department
Initially, the company had decided to use BIM software (like Revit and Naviswork) only for site construction works, such as creating 3D models to produce combined service drawings and to understand and provide more information on available space to install the building services. This was due to various reasons like limited budget or resources where the company had only limited funds to implement BIM throughout the entire construction project. So, they prioritised its use for sitework.
Another reason was the lack of awareness and expertise. The company did not have the necessary expertise or training to use BIM effectively for all aspects of the project. They focused on using it for the areas where they had the most knowledge and experience. There were also some situations in which the project had a tight timeline. Therefore, the company decided to use BIM only for site work, allowing them to complete that part of the project more efficiently.
As part of implementing the 4-year plan programme, based on demands from various upcoming new projects (mentioned in contract specification as mandatory) and requests from newly appointed Engineering staff, the company decided to enhance the BIM application to various departments of the company, such as planning department, estimation, and procurement department, design and construction department.
To implement this, XYZ reorganised the existing IT department by introducing a new digital department for better and enhanced operation. XYZ provided in-house training to all departments on using and applying BIM software by engaging authorised training companies.
Planning Department: In the planning department, the use of BIM software helped to visualise projects by creating 3D models of the projects’ elements, which assisted them in better planning and scheduling process by providing a better understanding of the project and allowing for more accurate sequencing of activities.
This department also started to study creating 4D schedules by adding the timeline of a project element to 3D models. This move helped them plan and schedule effectively. This was because they had better visualisation of their projects’ timelines and the ability to identify and eliminate potential scheduling conflicts before the conflicts contributed to waste in their projects’ workflows.
Estimation and Procurement department: For this department, BIM software was used to generate accurate quantity takeoffs, which helped estimate and schedule the materials required for the project. BIM software was also used to ensure that materials were ordered and delivered on time, which can help to avoid delays and keep the project on schedule.
Design and construction (D&C) department: In the D&C department, BIM software was used to create 3D models also allowed the engineers and contractors to coordinate their designs and identify potential issues by analysing possible clashes between different building elements before construction began.
This move essentially helped in the accurate sequencing of construction activities by creating a virtual construction schedule that shows the order in which construction activities should be completed. In addition to the BIM application, the project team installed CCTV cameras (with playback and recording functions), especially at high-risk activity locations, for remote monitoring of site works.
The company also began using drones for site inspections and monitoring. This technology allowed them to gather data and track progress, providing real-time information to the project team. With this information, they could make better decisions, reduce waste, and improve overall project efficiency.
Introduction of digital platform (Novade) for Permit-to-work system and for site inspection
As part of the digital transformation plan, Morgan implemented a digital cloud-based platform called Novade software during the COVID-19 pandemic period in 2021, which was before the implementation of the company’s 4-year plan programme, for applying Permit-to-work (PTW) and for inspection of site activities.
After the implementation of Novade, with the help of the Safety officer, Bala, Morgan started to explain to the senior management team the benefits of using Novade for applying PTW or an EPTW system that the company has achieved so far. Safety officer, Bala, provided a brief definition of the PTW system – “It's a safety management system that helps to control work activities that are hazardous or have the potential to cause harm. A PTW system provides a written record that identifies the work to be done, the hazards involved, and the safety precautions that are needed to be taken.”
Morgan then briefly explained why the company switched to an E-PTW or Novade system from the traditional paper-based application system. With an E-PTW system, they were able to streamline the entire PTW process from start to finish. It allows them to automate the creation of permits, send them electronically to the relevant people and monitor progress in real-time. This also helped eliminate the need for manual data entry, filing, and tracking, saving time and reducing possible errors.
In terms of accessibility, this system allowed the authorised personnel to access the system from any location at any time. This means that work can be authorised, checked, and monitored remotely, thus reducing the need for physical interaction. Finally, Morgan proudly announced how the system is environmental-friendly. Morgan said the system eliminates the need for paper-based permits, helps reduce our carbon footprint, and allows them to move forward in achieving sustainability goals.
Morgan expressed his feeling of satisfaction in extending the usage of Novade software for arranging site inspections with consultants or clients. He emphasised that it was very helpful in arranging site inspections in the construction project in several ways, as Novade enables site engineers or supervisors to schedule and assign inspections to the appropriate RTOs and ensures that the right people are on-site at the right time.
Morgan said it helps them to streamline the inspection process, allowing RTO or inspectors to complete their tasks efficiently and accurately. He further said the Novade platform allows construction managers to easily record observations, upload photos and generate reports, ensuring that all relevant information is filled up.
"Overall, Novade software provides us with a centralised platform for all inspection data or PTW, making it easy to access and share information across the project team. This ensures that everyone works from the same data set, substantially reducing the risk of miscommunication or errors." Morgan shared. Upon hearing this presentation by Morgan and Bala, the senior management team gave a standing ovation and was very pleased with the achievements and outcome of the first pilot of XYZ’s digital transformation.
XYZ had come a long way from only using traditional methods before COVID-19, realising the importance of digital transformation during COVID-19, and finally emerged as a digitally transformed company after COVID-19, with Morgan leading XYZ's digital transformation.
Morgan managed to turn the tide by using the COVID-19 pandemic as an opportunity to “digitally transform” the senior management’s traditional mindset on adapting new methodologies and digital construction technologies. With the help of COVID-19, the senior management accelerated the adoption of digital transformation, and Morgan continued to lead the transformation with the available digital solutions and platforms readily available in the market.
-The EndCOMMENTS FROM THE MODULE INSTRUCTOR
The classroom training on construction management using BIM and the self-learning 4D BIM assignment given to all students in the module learning journey provided the knowledge, understanding, and skills needed to conduct the case study research, analyse, and gather information from the case study research to write their stories. The story presented in this paper is an example of stories written by students in the module in groups of 2. Students applied the knowledge, understanding, and skills gained from the classroom training and self-learning assignment to provide insights through storytelling on how construction management practices can be improved to improve value-oriented productivity
Outputs of the self-learning 4D BIM assignment by the student authors of this paper can be found in the link. All the students in the module did well in the individual self-learning assignment. Many of the students, including the student authors of this paper, had not used the BIM software (Navisworks Manage) before taking the module. The learning materials the module instructor provided to the students started their research and self-learning, which led to their knowledge, understanding, and skills in using the software.
All the students in the module successfully completed and demonstrated the learning outcomes below. Self-reflections of the student authors in the appendix section of this paper showed examples of how the designed module learning journey positively impacted the professional capabilities of all students who registered for the module titled Construction Management using BIM.
• Interpret the role of integrated digital delivery (IDD) as a construction process management strategy for improving productivity in construction.
• Generate 4D BIM construction planning schedule.
• Appreciate technical and leadership skills needed to enhance productivity in the construction industry.
• Work effectively in teams by demonstrating an awareness of the varying roles within a group and the ability to choose the most appropriate role.
• Reflect upon the work of others, past and present, and relate their ideas to planning, coordination, and control of the construction process to form considered judgments about sustainable construction.
• Appreciate problem-solving skills.
Acknowledgements
The name of the company and characters involved in the real-life story reported in this paper were changed to make them anonymous. The support of the interviewee and his construction company in conducting the case study research is gratefully appreciated. The support of the Singapore Institute of Technology in providing a conducive environment for applied learning which motivated this research, is gratefully acknowledged.
APPENDIX: Self-reflections of the student authors
Student Reflection 1
“This module was delivered in a very enriching and interesting manner by Prof Moshood. Before attending this module, I did not know there was a method to measure value and invested resources in terms of Quality, Quantity, and Safety. It was definitely an eye-opener, and I learned a lot from this module. As I am currently working in an organisation, I believe that I will be able to practice the teachings through applied learning during my daily work.
In a short span of 13 weeks, I managed to learn and understand the construction management process, the experience of using a Building Information Modelling (BIM) software Navisworks, creating a video tutorial, and writing stories and reports. It was actually my first time recording my own video tutorial, and it was an interesting experience as I did not have any knowledge of video editing. This further taught me that one must have the capability self-learn any new software or tools, even though you have no prior knowledge or experience, and if you are able to self-learn new things without any help, you will be invincible. During the self-learning journey, when I was learning to use Navisworks, I met many obstacles as it was my first time using this software. Thankfully, there are Navisworks tutorials on Google, YouTube, etc.. This self-learning journey has not been easy but seeing the outcome of writing a report and video tutorial, I am able to understand the software a lot better.
The highlight of this module was taking up the challenge to write an 8-thousand-word story on how COVID-19 impacted construction management practices. I never thought I would be assigned to write a report in a story form as this would truly allow my project teammate and I to really understand and reflect on the difficulties the construction sector had faced during the COVID-19 period and how did they overcome the challenges faced.
Our report was sectioned into 6 chapters, and my teammate and I decided and agreed that we would each write 3 chapters of the report. The first 3 chapters, Imperfection, Resistance, and Revelation were written by me, and the subsequent 3 chapters, Pursuit, Uncertainties, and Transformation, were written by my groupmate. The biggest challenge we faced was thinking about how we could merge the 6 chapters as it was drafted by two people with different beliefs, ideas, and knowledge. However, we managed to overcome that challenge to the best of our abilities by meeting each other on weekends to discuss the story flow and planning for each chapter. With 2 authors, we will be able to cross-check each other and make sure that the story can flow and connect the story together. Without each other’s contribution and effort, it would have been impossible to write this story.
Throughout this module, Prof Moshood really made me self-reflect constantly and thinking how to ask the right question during our weekly lectures. I was actually enjoying and looking forward to classes on Tuesday nights despite having a long and challenging day at work. I look forward to being able to join Prof Moshood’s classes again in the future, and I will remember his teachings by heart. Thanks Prof!”
Student Reflection 2
“As a part-time master’s degree student and full-time M&E engineer, I found the lecture on the Module of Construction Management using BIM very informative and insightful. The module lecture and associated tutorials covered a wide range of topics related to construction management, such as project planning, scheduling, cost estimation, managing construction work, and quality control. It has also provided a vast knowledge and relevance of the Integrated Digital Delivery (IDD) scheme in the current construction industry and engaged the class in thoughtful discussion of Artificial Intelligence enhancement together with IDD. The lecture provided a comprehensive overview of construction management, including the different phases of a construction project and the various roles and responsibilities of the different stakeholders involved in the project. The lecturer also discussed the importance of effective communication, collaboration, and leadership in managing a construction project successfully.
One of the outstanding qualities I experienced during this lecture was the lecturer’s style of class interaction and questioning of each topic discussed. During the lecture on this module, the lecturer encouraged class interaction and questioning by asking open-ended questions where the students were allowed to share their opinions, experiences, and provide feedback and guidance. By encouraging the students to ask questions and share their experiences, the lecture has created an environment that promotes active learning and participation. The sharing of real-world examples of construction projects and their management, for example, a Youtube video on the construction of Marina Bay Sands followed by its class interaction, extremely helped me relate various theory concepts to practical applications. This style of class interaction and questioning has helped me to stimulate the ability of critical thinking by encouraging me to analyse, evaluate and apply the concepts being discussed..
As an M&E Engineer, I often work with multiple disciplines or services, such as electrical, mechanical, and plumbing systems within the project. I always focused on the system individually. The tutorial, like self-learning of Naviswork Manage, helped me see the M&E services as an integration of these multiple disciplines, which turns into a single model, making me think critically about how the different systems interact and affect each other. Reflecting on my self-learning experience, I can say it was a challenging yet rewarding experience.
As a beginner in using this software - Navisworks Manage, I must say that it was an extremely helpful piece of software that is comparatively easy to use and efficient in the application. Learning Navisworks Manage triggered me to approach construction projects from a different perspective, M&E Engineer’s as well as a builder’s perspective, and educated me on how useful the application of digital tools or software in a construction project are.
At the beginning of my self-learning journey, I set some learning goals for myself, such as understanding the software's basic features like sectioning, third person viewpoint, redlining & commenting, and identifying & generating clash reports. But going forward, I started to explore other functions like Quantification, Timeliner or 4D scheduling, and Presenter, Animator, and Scripter, which were significantly useful in project planning, scheduling, and resource management. I tried to achieve these learning goals by using a variety of quality learning resources, including online tutorials, instructional videos, and user manuals. I also took advantage of the support materials shared by the lecturer for the assignment, and I asked for help on some online forums when needed.
Self-learning helped me to achieve a good understanding of Navisworks Manage, as I used this tool to work through my job-related project problems and tried to find solutions on my own. This has led me to gain some level of mastery in applying this software and increased my confidence in using it. Overall, self-learning of Naviswork Manage was a valuable experience that taught me the tool's technical features and some important skills such as self-motivation, perseverance, and resourcefulness. It also allowed me to better understand project management skills or techniques, which will undoubtedly benefit my future studies and career.
Conducting an interview with construction as part of case study research on how the COVID-19 pandemic influenced their construction management practices has helped me deepen my knowledge and understanding of the latest technologies, practices, and trends in the Singapore construction industry. I strongly believe that this knowledge can be applied to my other courses, projects, or even research areas in the master’s programme. Through the case study research, I have personally observed that I can develop some practical skills such as data collection, analysis, interpretation, and presentation.
In the case study research, I understood that the COVID-19 pandemic has had a significant impact on the construction industry in Singapore, with disruptions to material delivery, labour shortages, and increased safety measures leading to delays in construction projects. The closure of construction sites during this period caused delays in project timelines and increased costs for contractors. To address these challenges, company were instructed to implement safe management measures to ensure the safety of workers and to increase the use of digital technology to reduce the reliance on physical labor, and even the Singapore government has introduced various measures to tackle the issues, including providing financial assistance to affected businesses
I observed that the COVID-19 pandemic has accelerated many companies to adopt digital tools in construction by highlighting the need for remote monitoring and coordination, virtual site visits, contactless processes, and safety monitoring. Even though some web-based project platforms like Novade and digital meetings like Skype and BIM have all existed for quite a while, the progress in using them and exploring the practical application took more time. As a result of the COVID-19 pandemic, companies started to invest more in digital technologies to improve efficiency, reduce costs, and enhance worker safety.
The case study research with the interview with management personnel shows that there has been an increase in the use of digital tools in construction projects over the last 1 to 2 years, and experienced both benefits and challenges for the project team with all types of digital tools that especially BIM, digital project platforms (Novade) and digital meetings. The primary benefits were that using tools increased time efficiency in project management and facilitated effective communication. However, there is less personal contact with project team members and other challenges with getting project staff to the same use of the tools. To increase the significance of the benefits and decrease the negative consequences, the project management team must implement a leadership style approach focused on the human side, with more follow-ups, structure, and routines. More technical knowledge about digital tools is also beneficial to the project management