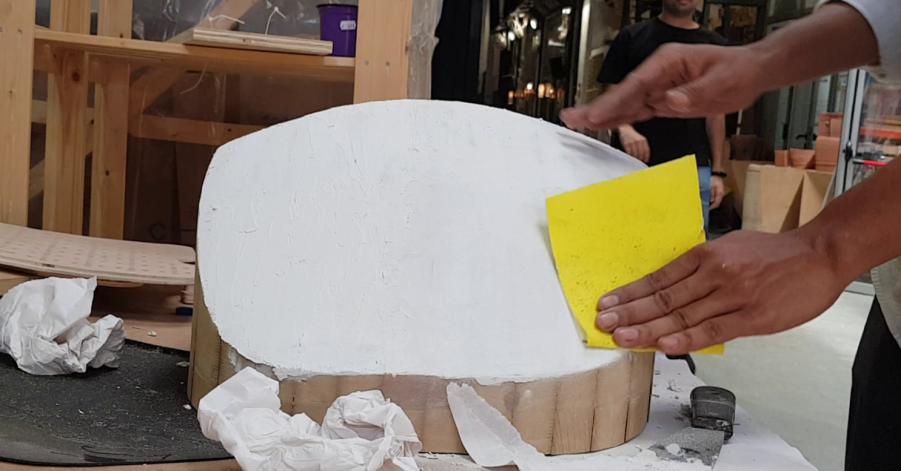
6 minute read
PRINTING ON A MOLD : SURFACE COAT3D
3D-PRINTING ON A MOLD : SURFACE COAT FOR DIFFERENT KIND OF MATERIALS TO STICK ON BUT ALSO EASY REMOVING
1. Putty on Mould We applied following putty to surface for the surface hardness, durability and smooth finish. Name : Masilla Tapagrietas Color : White
Advertisement
Process : Thin layer of paste applied on mold, it is lightweight material so easy to apply. its Dry quickly and helpful to fill the holes and marks on the mold and then achieved the smooth surface after sanding
Result : Its Smoothen the mold Surface but not suitable for printing, the hot Printed layer sticks to mold and make a mark on the surface.
Other Applications of the Putty : Indoor use on a lot of construction materials, cement, concrete, plaster, plasterboard, brick, wood, etc. even on old paint in good condition
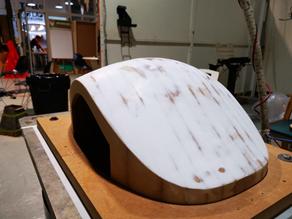
3D-PRINTING ON A MOLD : SURFACE COAT FOR DIFFERENT KIND OF MATERIALS TO STICK ON BUT ALSO EASY REMOVING
2. SPRAY PAINT The printing on mold did not worked properly so we shifted to another test which was spraying paint on the mold. Color : Black
Process :
1. 2. 3. We took a piece of MDF Board to apply the Spray Paint Wiped the Piece from cloths to clean of any dust. Applied first coat of spray paint and kept it for drying 5 minutes, then again applied 2nd and 3rd coat to get solid color and thick layer.
Result : Its Smoothen the mold Surface but not suitable for printing, the hot Printed layer sticks to mold and make a mark on the surface.

3D-PRINTING ON A MOLD : SURFACE COAT FOR DIFFERENT KIND OF MATERIALS TO STICK ON BUT ALSO EASY REMOVING
3. HIGH TEMPERATURE EPOXY GELCOAT Make : FORMX (Polyster Gelcoat)
It is an advanced epoxy gelcoat designed primarily for use in the production of high temperature moulds/tools for prepreg and resin infusion. EG160 uses a unique unfilled formulation which results in superior surface finish and polishability whilst still achieving excellent stability at service temperatures up to 160°C.
Color : Transparent and Black pigment Added
Process : Sand the MDF Board Mold which is already sealed with putty to create a mechanical bond with the gelcoat. thin. Next cleaned the surface and Applied gelcoat first coat on mold relatively
Result : Its Smoothen the mold Surface but not suitable for printing, the hot Printed layer sticks to mold and make a mark on the surface.
Key Features : • High temperature use up to 160°C • Suitable for prepreg tooling • Highly polishable • Superior surface finish • Simple brush application
Other Applications : • Gelcoat on moulds for prepreg manufacture • Gelcoat on moulds for high temperature epoxy infusion • Gelcoat on high service temperature epoxy components
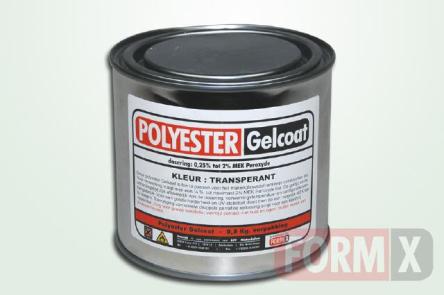
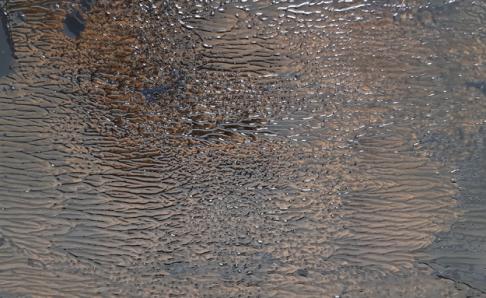

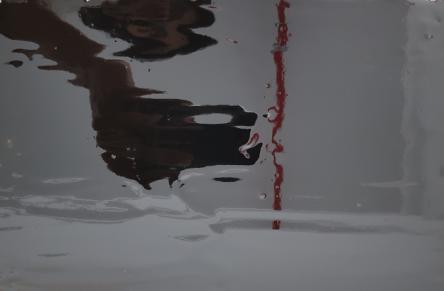
4. POLYURETHANE TYPE 1 :
Make : EBALTA (MG 321 FR / Comp. A+B) The EBALTA MG 321 FR is a ultra-low viscosity casting resin that yield castings that are bright white/ivory and virtually bubble free. Vacuum degassing is not necessary. It offers the convenience of a 2A:1B, 3A:1B, 4A:1B by volume in different Working and cured times as per the specific purpose.It can be colored by adding pigment or after getting dried. Fully cured castings are tough, durable, machinable and paintable. They resist moisture and mild solvents.

Ebalta MG 321 FR is processed on a two-component low pressure device. After grinding with a sand paper , grit 280, the surface can be varnished with a commercial lacquer. For better adhesion we use putty coat.
Color : White / Ivory
Process : It is essential to stir component A before use, as the additives tend to sedimentation. Component B has not to be stirred. Weigh or measure both parts accurately and assemble in a clean and dry container and mix for 30 to 60 seconds. For the mixing cup, used PP plastic cups. Avoid contact with moisture as this will cause foam formation of the resin. After mixing apply it in 1 - 3min as per the volume proposition before it get dried.
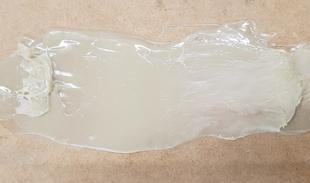
Result : It has working and curing time very less, is an easily pourable, thin-flow polyurethane cast resin that is suitable for mold to achieve the even and finished surface for material to stick on it but also easy removing. . its high heat resistance so does not create problem while extruding material on to surface.
Multiple Test with Different Proportions 4a. Test 1 with Proportion 3 : 1 4b. Test 2 with Proportion 2 : 1 4c. Test 3 with Proportion 4 : 1

Pros : ● ● ● ● ● Cons. : ● Low viscosity - captures excellent detail - no degassing necessary high heat resistance Resin cures to a bright white/Ivory finish It can be sanded, drilled, sawed and - after degreasing - painted Cured castings are strong and durable and resistant to moisture and mild solvents.
Working time and cured time is very less where the mix ratio is equal or lower, difficult to apply on surface after 1-3 min. Depending on the ratios In higher ratio, it take time to dry.
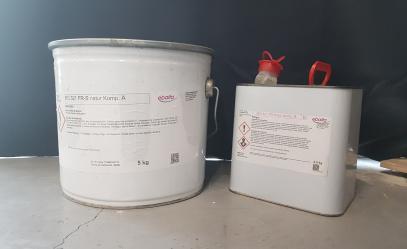
5. POLYURETHANE TYPE 2 :
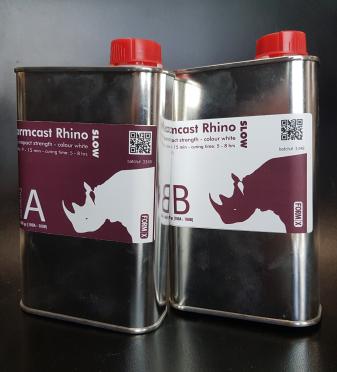
Make : FORMX (FormCast Rhino) The Form Cast RHINO liquid plastic is an ultra low viscosity resin with ivory color. When properly used it will yield strong, detailed and bubble free castings. Vacuum degassing is not necessary. This resin may be mixed with various fillers and dyes. Cured castings are strong and durable and resistant to moisture and mild solvents. They can be sanded, drilled, sawed and - after degreasing painted.

Color : Ivory plus black pigment added
Process : Stir the individual components well before use. Weigh or measure both parts accurately and assemble in a clean and dry container and mix for 30 to 60 seconds. For the mixing cup, used PP plastic cups. Avoid contact with moisture as this will cause foam formation of the resin. After mixing apply it in 9 - 15 min before it get drying.

Result : FormCast Rhino is an easily pourable, thin-flow polyurethane cast resin that is suitable for mold to achieve the even and finished surface for material to stick on it but also easy removing. . its high heat resistance so does not create problem while extruding material on to surface.
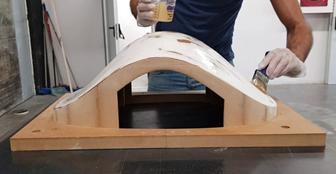
Benefits : ● Cured castings are strong and durable and resistant to moisture and mild solvents. It can be sanded, drilled, sawed and - after degreasing - painted, its Compressive Strength is 47 ± 5 Mpa as per EN ISO 604 Standard and E-modulus 1000 ± 100 Mpa as per EN ISO 178. Short demoulding time and heat resistance, Heat Stability (HDT) 84 ± 3 ˚C . low viscosity
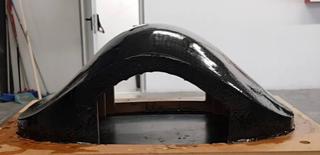
Other Application : Form Cast Rhino is suitable for industrial use such as making foundry patterns, core boxes, vacuum forming tools, mold surface top layer finish and prototyping of all the scale and complex shapes. Typical uses include the manufacturing of prototypes, models, sculptures, decorative articles, anatomical models etc.