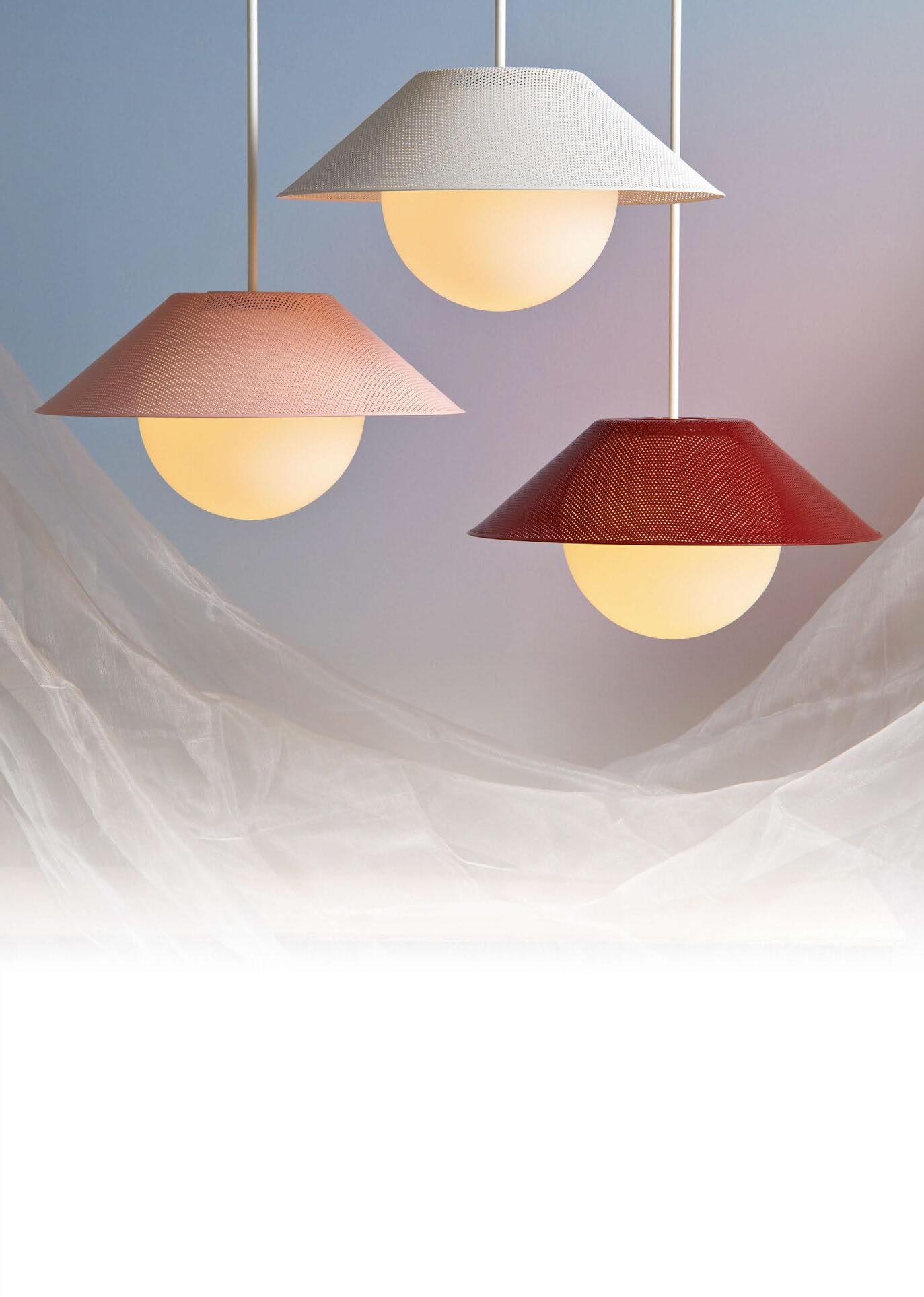
2 minute read
In Focus
from darc 50
Akoya
Mayela Mujica, Design Manager
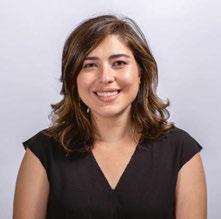
Rich Brilliant Willing www.rbw.com
What was the design inspiration behind Akoya? Akoya was named after the Japanese word for “pearl”; the shade shell proudly reveals a glass pearl bulb. When we first started the development of this product, we were looking at traditional light fixture construction methods using barrel spider fabric shades but flipping the script by making the lightbulb, which usually hides within the shade, the centre of attention. We took that inspiration and interpreted it as a cord/stem suspended pendant that displays beauty in simplistic geometric shapes. The first iterations were parchment paper shades then later transformed into a perforated shade, looking to use a material with different properties but still alluding to the original geometric inspiration.
How long have you been working on the new iteration for?
The development loosely started in November 2011 and the first version of the product launched in early 2013. After that initial launch there have been some major redesigns along the way, and the most recent iteration was released in October 2022. Akoya is a perfect example of the RBW values “Committed to Grow” and “Make it Awesome”. The original pendant, designed in 2011, was a parchment shade that half-revealed the illuminated pearl globe. Later on, the design moved to our iconic perforated shade. And most recently as a result of our push for sustainability and desire to provide our clients with even more technical capabilities, we took on a year long project to redesign the fixture using Design for Manufacturing methodologies with an added focus on carbon footprint. The result was a design with higher technical capabilities (increased lumen output, easier install, less weight), more efficiently manufactured with fewer components, an RBW LED board and with shades now fabricated in North America; we’ve also cut down our carbon footprint by manufacturing closer to home.
Can you you describe the design and manufacturing process for Akoya?
The design process was an iterative activity consisting of a rinse and repeat of sketches, models, sampling and cross-functional reviews. For the most recent improvements we used Design for Manufacturing methodologies and all the knowledge we have gained since the original development in 2011. The design is composed of a machined light module with a spun aluminum perforated shade and a hand-blown opal glass.
What was the most challenging aspect of producing Akoya?
Reaching our goals of technically improving the design while reducing the carbon footprint was an exciting challenge.
Achieving a crisp folded seam was a small detail that we are very proud of, with no seams on the side. This product is unique because it allows the clients to customise the shade to their desired colour while keeping the pricing consistent. This is only achieved because we thought of the design for assembly from the start by looking at the design holistically as part of a bigger picture within our sourcing and operational workflow.
What makes this pendant different to others available on the market?
Akoya has the ability to blend in or stand out depending on the materials the client chooses and the rest of the space. Like many products in our collection, there is a joy of exploration, the design looks great from afar but as you get closer it starts to reveal more details and layers, like the perforated pattern, the contrast of material between the opal glass and the metal shade and the seam at the edge.
Please describe the product in three words. Versatile, lighthearted, delightful.
Black Hole Extreme phenomenon
Black Hole Sound System
With the use of wireless Bluetooth technology, you can connect smartphones, computers, or tablets and enjoy your favourite music with a built-in speakers system.
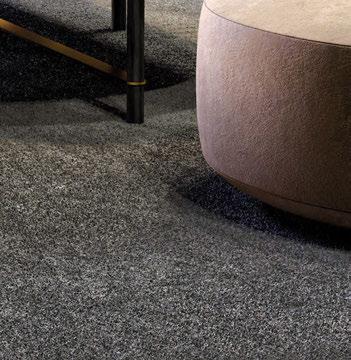
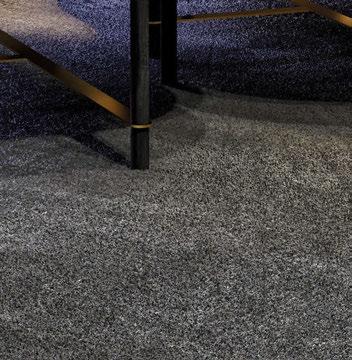
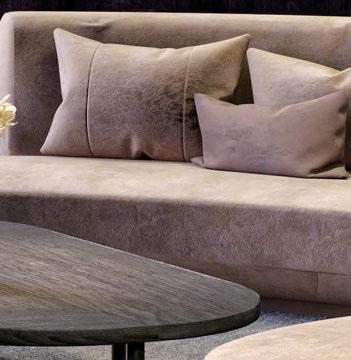
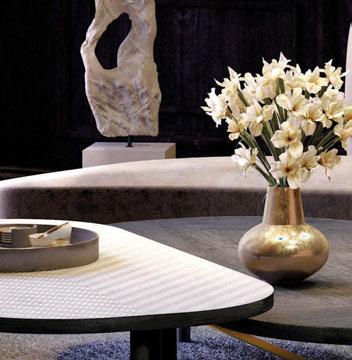
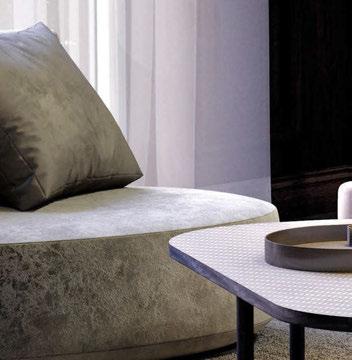
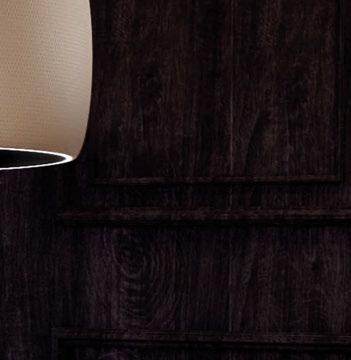
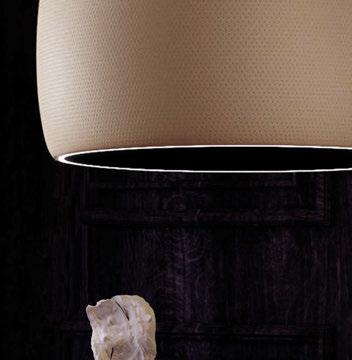
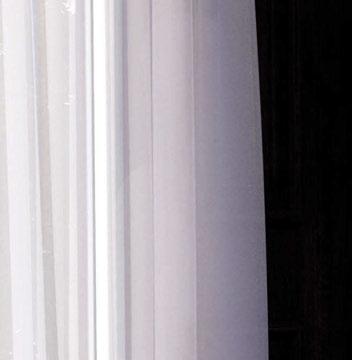
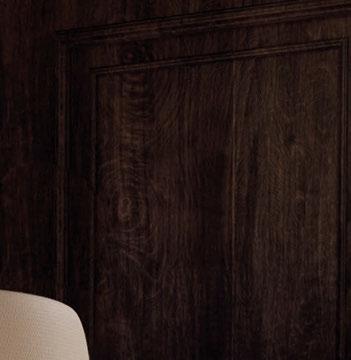
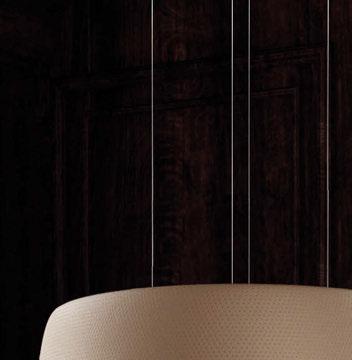
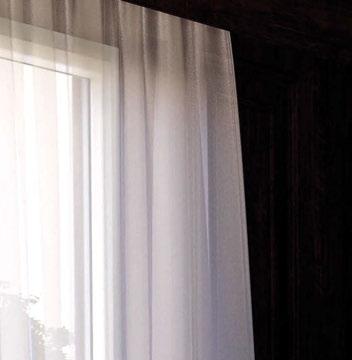