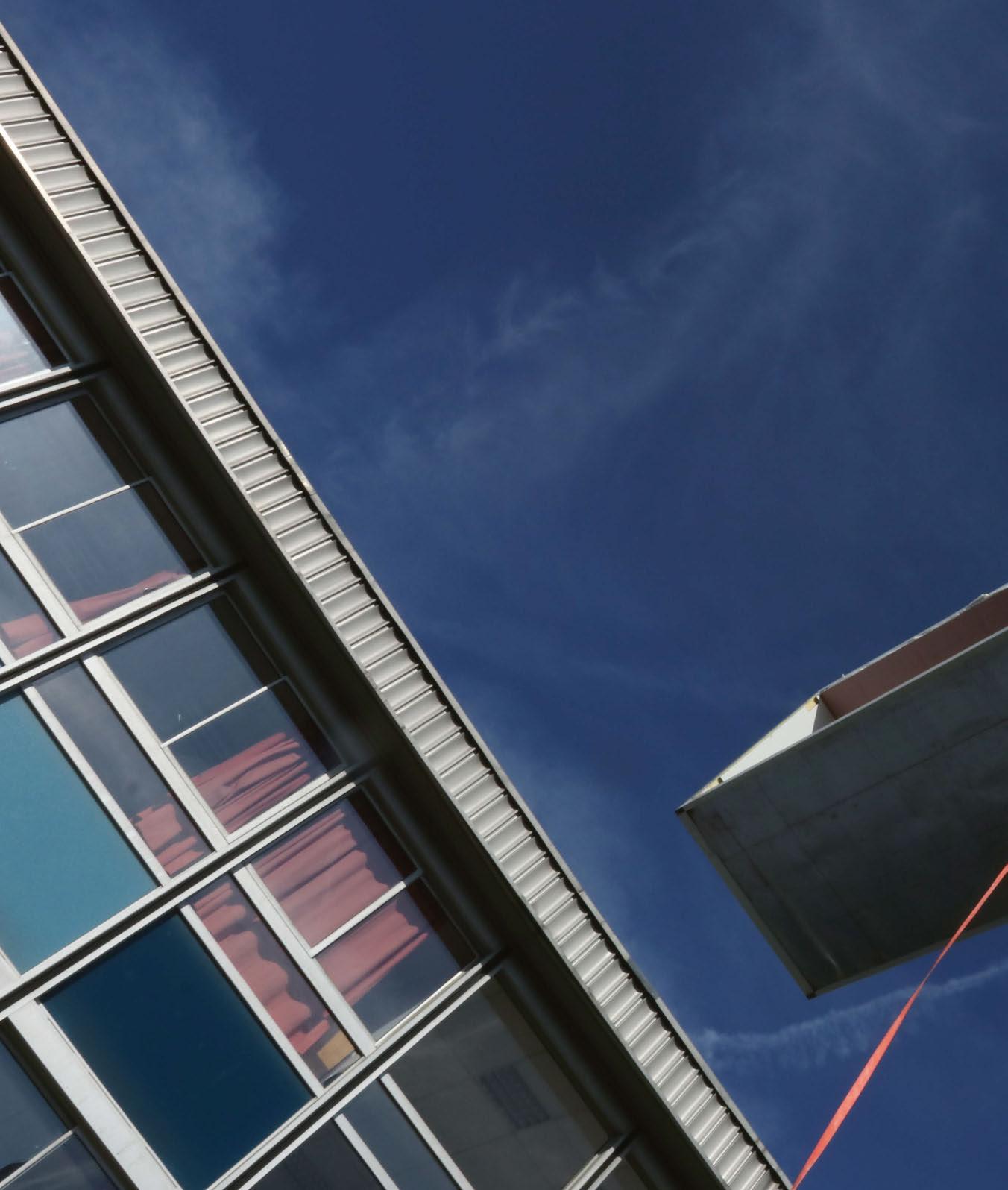
7 minute read
Build Back Better
from Sleeper 100
As the hotel sector strives towards more efficient and ecofriendly development solutions, modular construction could be on the rise in the years to come.
Words: Ben Thomas
From shorter lead times to lower building costs, greater quality control and reduced carbon footprints, there’s a list of reasons for hospitality brands to consider modular construction, the method in which a hotel is built room-by-room in a factory before being transported to site.
While many developers and operators have been slow to capitalise on the use of industrial prefabrication, CitizenM has been at the forefront of the movement for over a decade; the Netherlands-based group launched its first modular hotel in Amsterdam in 2008 with the help of Dutch design studio
Concrete, and since then has worked with the firm to add nine more modular properties to its portfolio, gleaning insight into the best practices along the way.
“Prefabrication not only enables faster construction and easier quality control, but also guides the architectural aesthetic of our modular locations,” says Chief Development Officer
Harold Reniers. “No matter how they’re assembled, CitizenM’s modular buildings are recognisable in their urban surroundings for their identifiably square units, clean lines and artwork on the façades.”
Another operator exploring this method is Yotel, which marked its entry into the modular landscape with Yotel
Amsterdam Noord in 2019. Having witnessed early success, the group plans to roll-out several more as part of its growth strategy, with the latest Yotel and YotelPad AnyTown models designed to allow for the adoption of the method. In addition, both assume a traditional frame and transfer structure for the
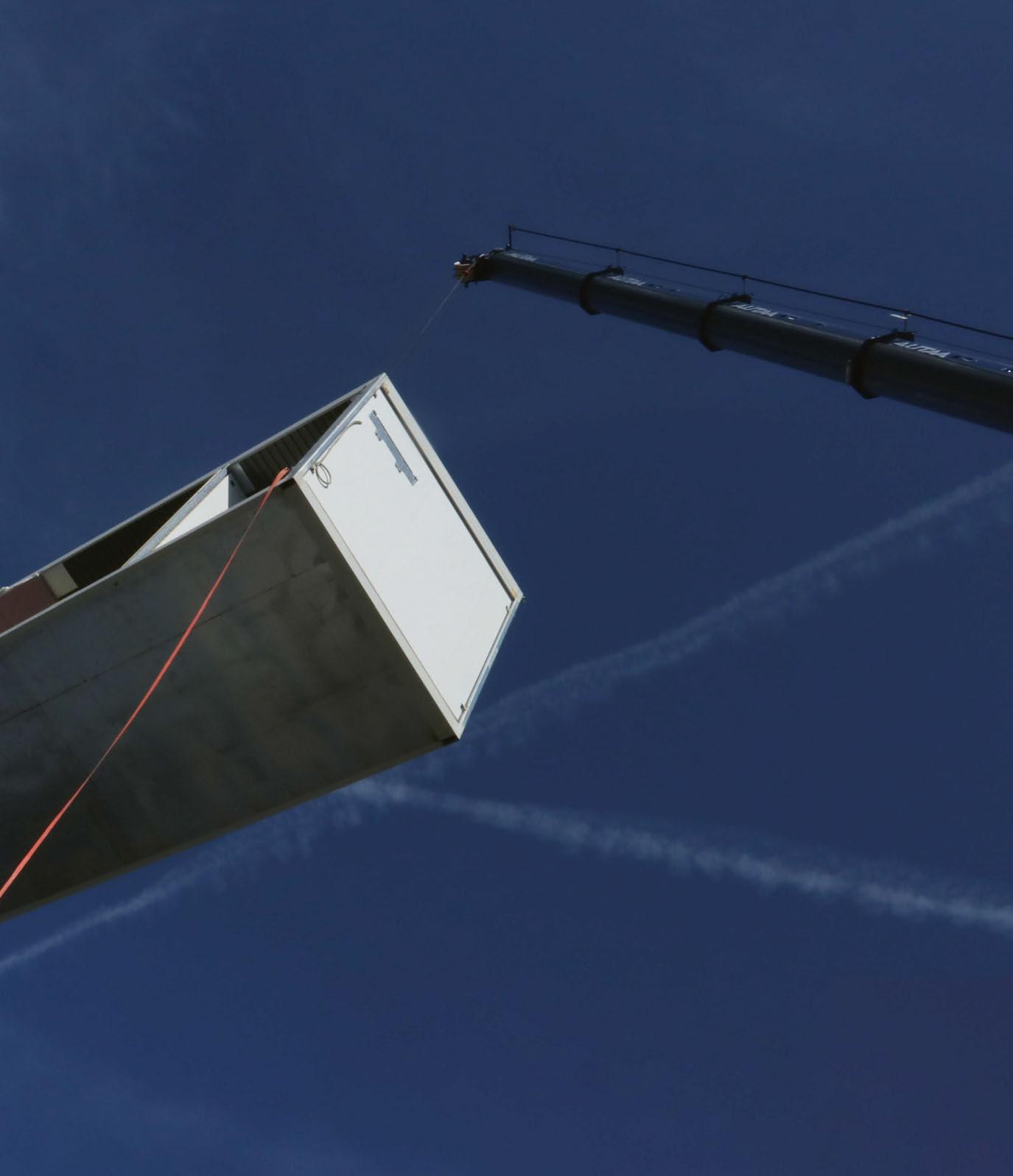
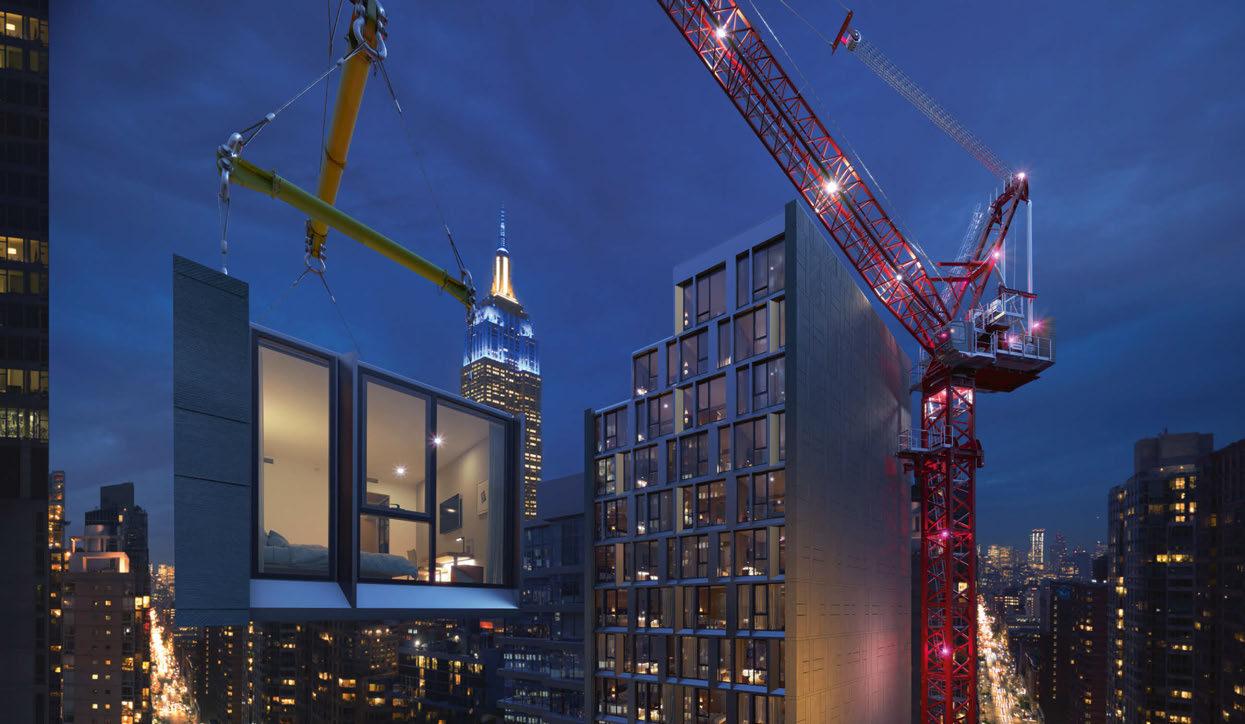
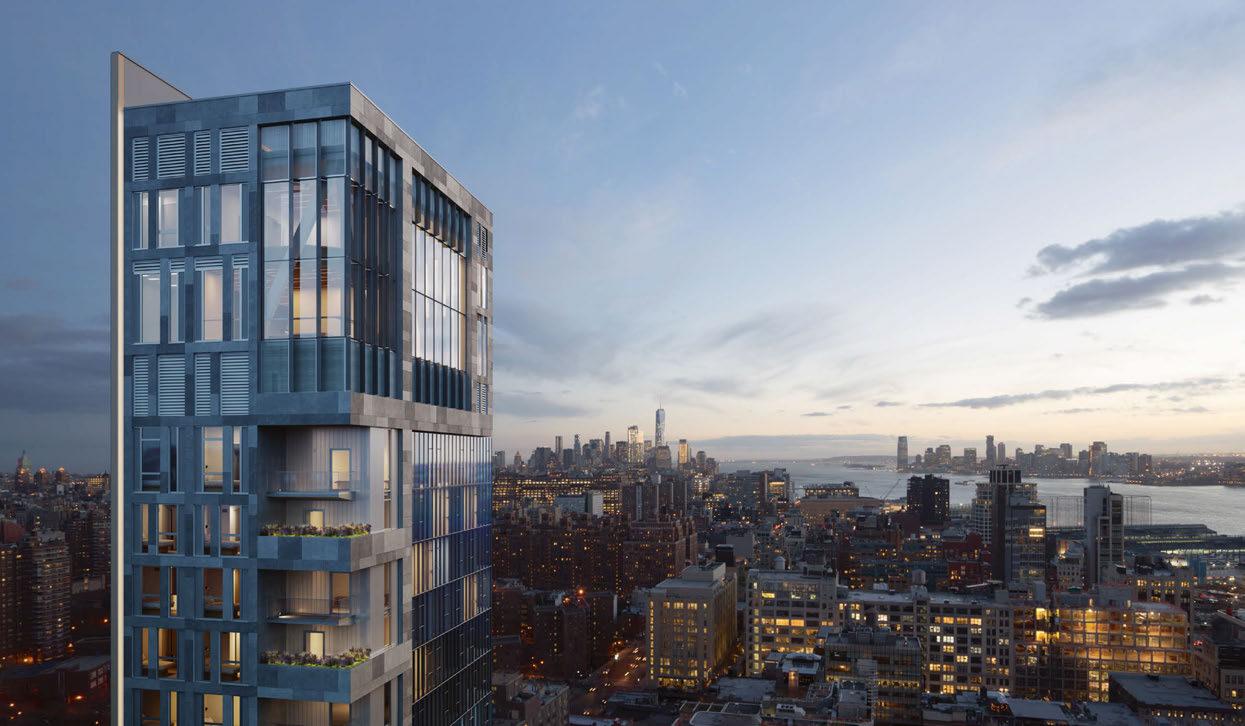
In New York, Danny Forster & Architecture has designed AC NoMad (top) – slated to become the world’s tallest modular hotel at 26 storeys – as well as Hudson Yards Autograph (bottom) in Manhattan “Prefabrication not only enables faster construction and easier quality control, but also guides the architectural aesthetic of our modular locations.”
HAROLD RENIERS, CITIZENM
ground-floor podium level, enabling flexibility over their front- and back-of-house spaces.
“We have always had one eye on modular construction – it aligns with our brand DNA of efficient and forward-thinking real estate,” reveals CEO Hubert Viriot. “It can also give our hotels a unique exterior aesthetic – something guests have come to know and love about us.”
And it’s not just future-focused brands like CitizenM and Yotel pushing boundaries, as hospitality’s big guns are also making waves in the world of prefabrication; Marriott now has more than 30 modular hotels – including the under-development AC NoMad New York City, billed as the tallest of its kind in the world at 26 storeys – while Hilton has bolstered its modular portfolio over recent years with new openings from Garden Inn, Home2 Suites and Hampton.
Designed by Danny Forster & Architecture and named as runner-up at Radical Innovation 2019, where it was pipped to the post by Connectic – a modular concept from Cooper Carry that could be used to build a pop-up hotel in remote areas or help solve space issues in dense urban cores – AC NoMad is using patented technology that trains 3D cameras on each module at five different points during the construction process, meaning contractors and architects, as well as off-site stakeholders, can keep track of what’s taking shape.
ACCELERATED ASSEMBLY
So why is prefabrication becoming such a popular method within the hotel sector? One of its key advantages is speed, as preparation and foundation work can often be undertaken whilst units are being prepared.
This is certainly the case for experience-led hospitality group Habitas, which built on the success of its Tulum resort with openings in Namibia, Bacalar and AlUla last year. Having created its own factory in Mexico, Habitas is now able to manufacture rooms before on-site construction has begun, standardising several modules before flatpacking and shipping them to site, where they are assembled like Lego. As a result, the group achieves lead times of under 12 months – something it hopes to replicate as it expands to new locations in Mexico, Saudi Arabia, Costa Rica and Bhutan. “Traditional hotels follow a linear process that can take three to four years from concept to opening,” explains co-founder Kfir Levy. “By designing, manufacturing and developing our properties in-house, we’ve streamlined the process.”
For British architecture firm Studio Anyo, which uses a Modern Method of Construction (MMC) process – combining off-site construction with on-site techniques – faster build times are essential in the hospitality market. “Hotels are revenue-generating assets and every night they are closed is revenue lost,” says founder James Walsh. “MMC programmes can be up to 50% faster than conventional methods and mean a hotel can be open and earning much sooner.”
PROTECTING THE PLANET
Another benefit of industrial prefabrication is the more responsible use of resources, including a reduction of the time needed on site as well as lower waste and noise pollution levels.
According to Reniers, CitizenM’s modular approach offers plenty of sustainability rewards as it uses a parametric design procedure, which lessens construction waste to just 2%, down from 10-20% for a typical build. Shortened timeframes also lower carbon emissions, and when it comes to embodied carbon, analyses shows that modular methods outperform traditional techniques by 68%. The environmental advantages extend across the construction process, with fewer truck deliveries and speedier timeframes for crane work.
“Consumers are driving change, demanding more sustainable hotels but even if that wasn’t the case, these standards will be enforced by incoming legislation,” explains Walsh, whose studio employs a zero carbon and zero waste policy. “Investors want appreciating assets and brands want low-cost operations, so it is becoming the norm rather than the periphery.”
For Habitas meanwhile, the aim is to tread lightly without compromising design integrity and the guest experience. “We all need to be more conscious of the planet – it’s our responsibility,” Levy insists. “Owners and operators are being forced to change their development practices to foster environmental consciousness and more sustainable methods.”
DECISIONS, DECISIONS
Notwithstanding its efficiency and environmental benefits, modular construction does come with challenges, including the front-loaded nature of the design process, given that complex changes are off-limits once units have been produced. Adaptability and the creation of a unique DNA is another obstacle, with operators weighing up how they can mass produce modules without taking a cookie-cutter approach. In many instances, the solution is to ensure that while 80% of a project is repeatable, the remaining 20% is characterised by creative elements. And then there’s site constraints to consider, with modules needing to be easily manoeuvred into position, especially in heavily populated cities like New York and London.
“It’s important to flag that modular construction isn’t without its drawbacks,”
HUBERT VIRIOT, YOTEL
Having witnessed early success with Yotel Amsterdam Noord in 2019, the group plans to roll out more modular hotels using its Yotel and YotelPad AnyTown models
says Viriot. “Our experience has taught us that establishing relationships with best-in-class manufacturers is critical. We have also learned that modular needs to be assessed on a projectby-project basis – not every opportunity makes sense, with variables such as unique design and real estate constraints, financial feasibility, and transport and accessibility issues. Despite this, we are optimistic that with growing experience, we will get better at assessing these needs.”
Walsh agrees that experience is crucial, adding that most issues with modular projects are caused by lack of know-how: “Developers need to appreciate that because the programme is faster, design decisions are earlier and fixed, so the risk profile is different to a typical build.”
FUTURE FORECASTS
As the industry gets to grips with prefabrication, Levy expects to see more work done in the field and less in a centralised factory, with popup workshops and mobile facilities reducing logistics and transportation needs to streamline the process even further, while CitizenM is dedicating time to present the benefits of modular methods to authorities, with its next modular hotel, a 226-room development in London Victoria, slated to open later this year.
From an architectural viewpoint, Walsh expects a well-funded manufacturer to enter the market with a semi-automation process that will drive the industry forward through lean systems. “AI tools connected to parametric design are being developed to assess sites and these will be tied to production software, bringing with them new levels of efficiency.”
On a lighter note, and potentially providing developers with a source of inspiration for their upcoming ventures, the Lego Group will soon be adding a hotel to its modular city collection. Celebrating 15 years of sets from the line-up, the three-storey model comprises over 3,000 pieces and is furnished inside and out with a lobby, terrace, art gallery and penthouse suite. There’s also mini-figures to staff the property, including a bellboy, receptionist and barista. If Lego’s new addition is anything to go by, then modular construction could be on the rise as the hotel sector strives towards more efficient and eco-friendly solutions in the years to come.
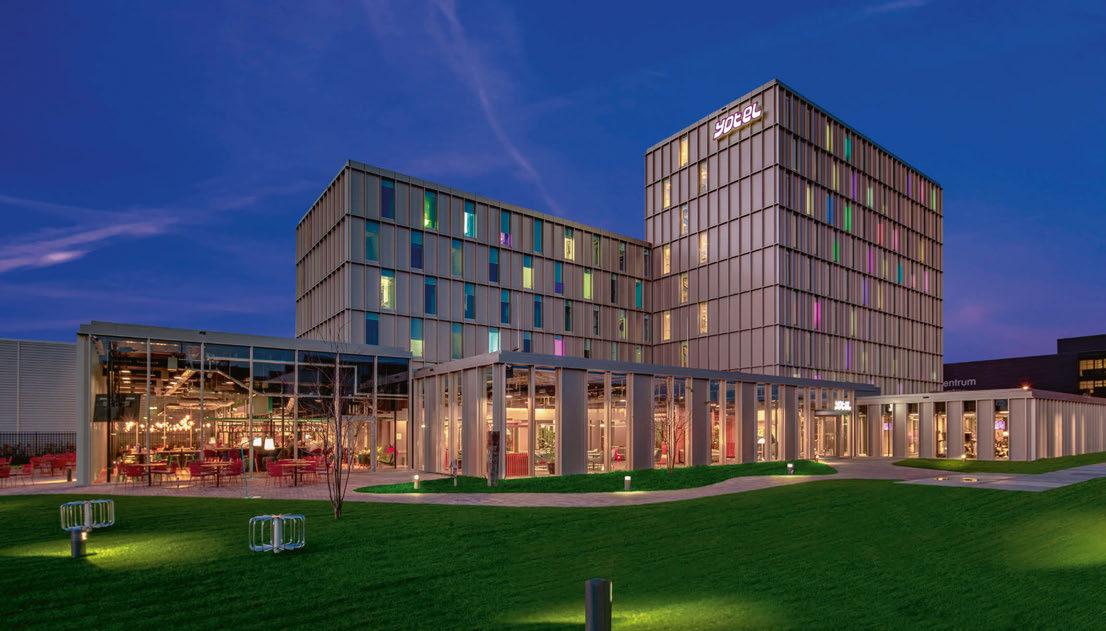
