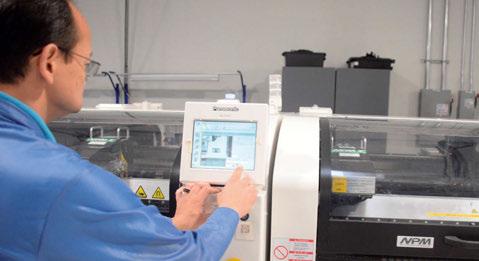
2 minute read
[New] WORKING THROUGH CRISIS
Words: Bob Boster Photo: Clear-Com
Following its acquisition by HME, Clear-Com implemented Lean, a continuous improvement approach where all members of the organisation can bring their informed opinions on how to improve things into a structured process to be incorporated into the whole. Lean tools were initially developed within the manufacturing disciplines but have gradually expanded to impact Product Development, Support, and various other back-office activities. Our parent company HME stays current on Lean through membership in the Association for Manufacturing Excellence and coordinates various activities through both dedicated team members as well as ‘Lean practitioners’ across a variety of departments within the business.
Since early 2020, we have turned to our Lean principles to address COVID-related challenges, first in keeping our Manufacturing and Product Development activities safely operational during the peak of active COVID-19 spread, and subsequently in addressing challenges to our ability to produce products due to extended lead times and staffing disruptions from mid-2021 until now.
These activities have included collaborative work between Manufacturing and Engineering to replace unavailable and/or discontinued products, reframing daily activities in the factory around an interdisciplinary crossfunctional team, and extensive and ongoing refinement of the manufacturing processes to best address ‘burst mode’ component availability. In parallel, our SAFe product development methodology, which is actively guided by Lean principles, has allowed our development teams to continue to innovate while still supporting the changes required by component replacement.
We even have a dedicated Director of Lean Strategies and Operational Excellence, Diem Lewis, who affirms that “one of the pillars of Lean is people capability development.
During the last two years, HME has enhanced our training offering to include skills such as empathy, flexibility and resilience for both employees and managers. Dedicating time and resources to develop or fine-tune these skills has helped our people navigate through the challenges the past two years have brought. When problems come up, employees show understanding and work together to work through the challenge at hand. We have witnessed improved communication and collaboration amongst our teams and are able to do things better than we have ever before.”
Our new VP of Engineering, Marco Lopez, agrees that “communication is the number one weapon to slay the pandemic monster.” With staff working remotely, our Agile development process was put to the test, but, Marco states, “I can confidently say it shined. Through the structured and streamlined touchpoints of daily stand-ups, bi-weekly sprint loading and reviews, as well as a more formal quarterly presentation of successes to our senior management team, we were able to maintain a high level of communication with all teams within our several development facilities across the world. “
Our Director of Program Management, Vincent Morency, adds that our Scaled Agile Framework enables close collaboration between Engineering and Product Management, and regular and preset planning windows offer the chance to track progress against our development roadmap and make necessary adjustments when new priorities or unforeseen challenges arise. “It’s not just about achieving development velocity,” he said, “but even more so predictability and consistency.”
Having seen how powerfully our Lean focus has helped us address some very significant challenges in the past few years, we are renewing our commitment to this paradigm moving forward. While the COVID-19 pandemic was the catalyst that made us focus more on
Lean manufacturing tools and techniques, this is not a transitory focus; rather, we are making a long-term commitment to future success.
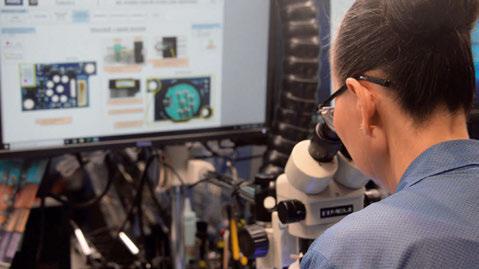
Customers may be unaware of the importance that Lean holds in the successful development, construction, and support of their products, but the quality, the innovative capability, and our ability to support them in the successful operation of their systems for years to come are standing on that foundation behind the scenes.
We believe that Lean tools and techniques play a powerful role in our success, and therefore in the successful operation of so many Clear-Com communications-enabled activities around the world. www.clearcom.com