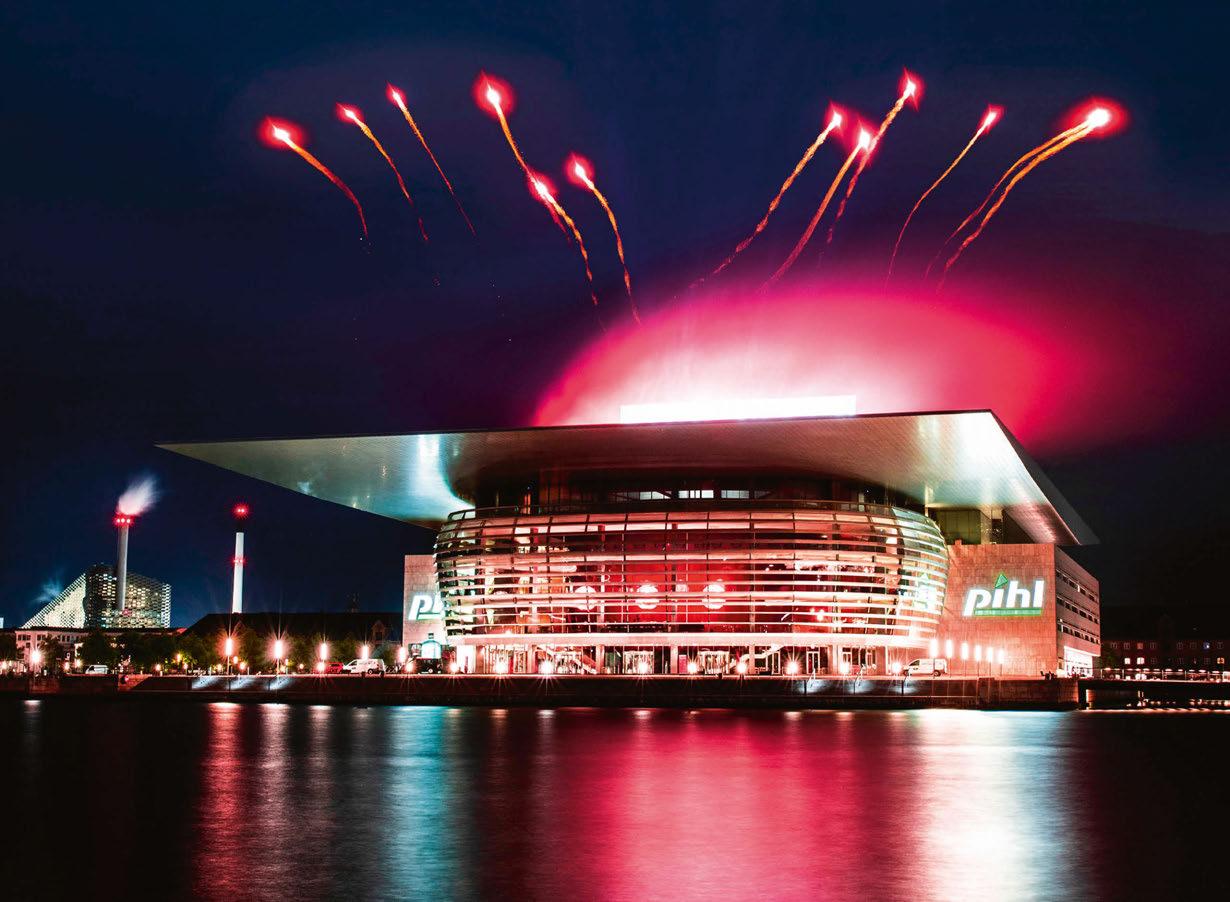
4 minute read
CovidHagen
COVIDHAGEN
DPA Soundco provides audio infrastructure for an ambitious 24-hour stream on the roof of the Copenhagen Opera House. Project Manager, Ally Kerslake, reflects on the undertaking…
Over the past few months, we have seen exponential growth in streaming culture in the world of live music as well as the level of production that has gone into a number of fantastic shows. However, last month the city of Copenhagen played host to an event that took the content to a whole new level – the roof, to be exact.
Hosted on top of the iconic Copenhagen Opera House, CovidHagen, was created to entertain the Danish public who, at this time of year, would usually be looking forward to several months full of festivals. The goal of CovidHagen was to produce a 24-hour stream, all of which was performed from the roof of the building.
Brought in to provide the audio infrastructure for the project was DPA Soundco. Sound Engineer and Project Manager, Ally Kerslake spoke of his experience. “The project as whole had some quite challenging, unique and historic elements,” he began, not least created by the fact the performance was to take place on the roof of such an iconic building. “This posed many challenges as the only way up to the roof to load in was a small elevator. Then through an even smaller stair entrance onto a roof with no real access save to do inspections from time to time and certainly not to have any kind of concert production.”
The second challenge was that the vision from the very beginning was to create a ‘stay at home festival’ that would provide 24 hours of nonstop content to be streamed on Twitch. “Crewing and safety was always a priority for me during the planning stage,” reflected the Project Manager. To manage the workload, the show was run by two, 12-hour shift teams, comprising: an audio project leader, broadcast operator, monitor operator, and operator/system alternate for breaks. Also on the roaster for each shift on the roof was a RF Tech, stage tech, stage alternate and an audio trainee.
DP A Soundco provided a full audio package comprising an RF and amp station on the roof with all Shure Axient and PSM1000, CODA Audio CUE TWO Bi-Amped wedges, CODA DJ booth/sidefills and all mics and stands.
“The power of both the CUE TWO and APS systems was perfect to fire through the windy conditions on the roof,” said Kerslake. He also
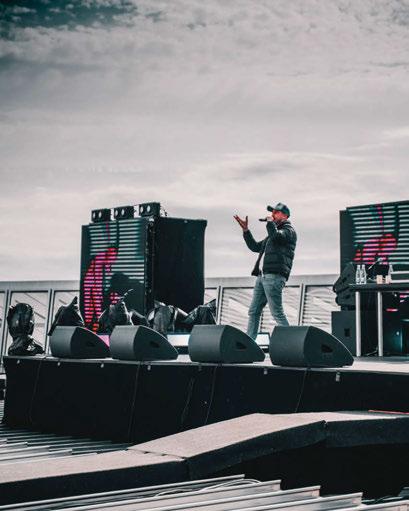
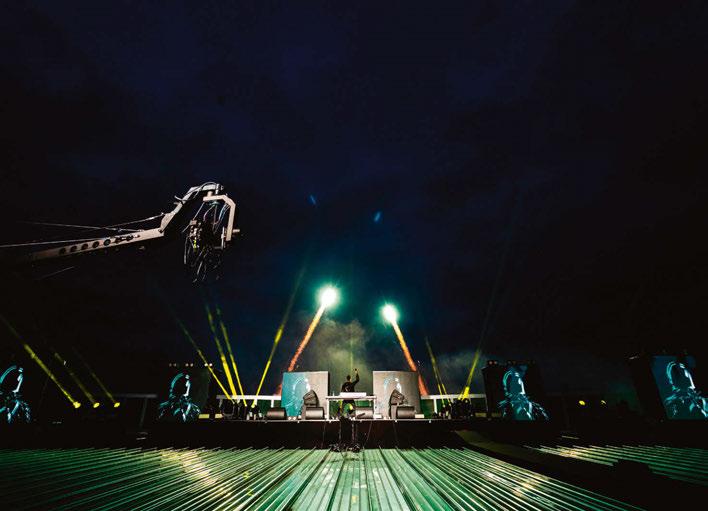
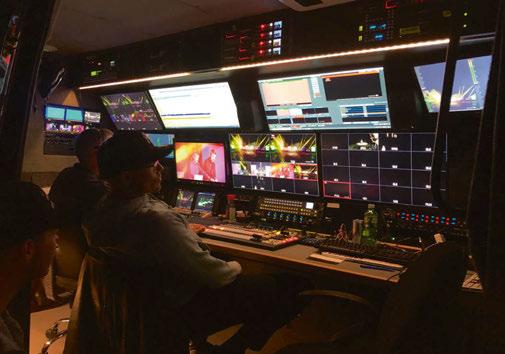
expressed that due to the fast changeovers, the light weight of the CUE TWOs “definitely helped”. “It’s the lightest 15in, three-way wedge I’ve come across and the crew onstage were certainly glad of that after 24 hours. We didn’t have a single issue of tonality throughout the whole production and actually had multiple artists asking if we could provide the same solution for future tours.”
A fully DiGiCo Optocore Fiber system with back-up analogue took care of all I/O. Kerslake explained: “This was situated on the second floor of the building in a makeshift control room with low-latency LED screens and split-screen program feeds so the operators could get a feel of what was happening many floors up on the roof.”
In the control room, there was a DiGiCo SD10, which handled monitor control with wired Shure P9HW. Wedges for the control room were a stereo pair of Biamped CODA Cue 2. The broadcast sound direct to the OB via AES and Madi was taken care of via another SD10 with a Custom DPA Soundco Waves system rack comprised of two Waves SoundGrid Extreme Servers and the new Waves super rack also running Tracks live for recording. Waves WLM Plus Loudness Meter played a major role in keeping the levels at a constant to the OB feed.
“Lastly, a DiGiCo SD12 took care of the host mics between change overs,” stated Kerslake. “The SD12 also handled all comms routing matrixing and analogue back up to the OB on a split, so if ever the fibre loop
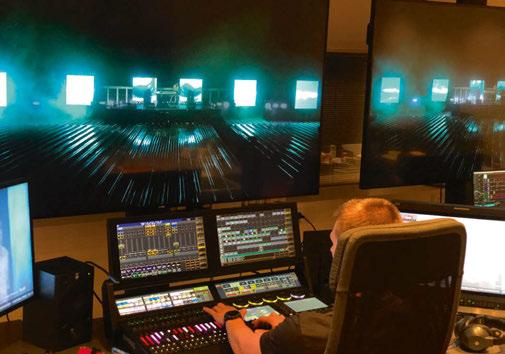
of main show consoles were to have any issues it would always be possible for the hosts to stay live to OB for ‘padding’.”
Obviously, due to the current global situation, the organisers of CovidHagen wanted to ensure that everyone was safe during the performance. This saw the crew take certain measures such as a workstation on the roof with a full disinfection setup. A full-time engineer was required to maintain this, along with being in charge of wireless management through Shure’s Wireless Workbench and Showlink for the show and also for the many TV press that would come with their own RF throughout the production.
“We h ad over 50 acts play over the 24 hours with multiple artists in each,” stated Kerslake. “We had 25 Shure Axient HH transmitters and 20 PSM 1000 IEMs had to be cleaned thoroughly between each use. Each artist had their own wind screen to prevent passing the wireless and each of our techs had their own screen for checks.”
DPA Soundco also put its two 3D printers to work prior to the event to make custom motorola changing stations for the 80-plus radios for production staff and security provided by DPA. RF mic holders were also made in house. TPi Photos: DPA Soundco www.dpasoundco.dk