
10 minute read
FORGING A NET ZERO PATH WITH GREEN CORRIDORS
FORGING A NET
ZERO PATH WITH GREEN CORRIDORS
Advertisement
By Lauren DeLorenzo, Assistant Editor, Mining Magazine
Governments and industry bodies are aiming for increasingly ambitious environmental targets, challenging miners to make drastic cuts in emissions in the coming years. But the key to achieving this could lie in creating a new green pathway in one of the most notoriously difficult areas to decarbonise – shipping.
Recognising the need for climate action, the mining and shipping industries are looking at ways to radically transform the way that commodities are moved around the globe.
Shipping is responsible for around three per cent of total global emissions, and a number of countries, including Japan, Australia, the UK and the US, have set goals of reaching net-zero emissions by 2050. The International
Maritime Organisation (IMO) has mandated a 50 per cent emission reduction for all vessels by the same deadline And in 2021, over 200 maritime organisations signed the Getting to
Zero Coalition’s Call to Action for Shipping Decarbonisation, advocating for the commercial deployment of zero-emission vessels by 2030.
The technology used to produce zero-emission fuels and vessels is close to being market ready, with many trials and pilot programs underway. Key technologies for transitioning the largest ships will be available by 2024.
But while zero-emission fuels are a clear and available solution, they are much more expensive than conventional fuels.
In fact, zero-emission fuels can increase the total cost of vessel ownership (TCO) by between 40 and 60 per cent. Implementing this fuel across a huge range and variety of stakeholders through the value chain would be incredibly difficult. The shipping industry runs through a complex chain of diverse stakeholders, and there is no singular system through which to implement this change.
Another challenge is that vessels have an operating life of 20 years or more. This means that if more carbon-efficient vessels are going to have a meaningful effect before 2030, then the industry would have less than a decade to implement zeroemissions fuels throughout the industry.
Whichever zero-emissions shipping solution is pursued, it must be deployed quickly and feasibly at an industry-wide scale, and at a lower cost than current operations.
What are green corridors?
The idea of a green corridor is to reduce coordination challenges while making a large-scale impact, bringing together a wide range of stakeholders into one simplified, more sustainable shipping ecosystem.
This means establishing a trade route between major ports that can support the integration of low-emissions fuel infrastructure and vessels between countries and along the value chain.
Ideally, this would have regulatory and legal support from nearby countries, which could provide low-carbon refuelling stations and other low-carbon infrastructure. Policymakers could enable green corridors with targeted financial incentives and safety regulations to encourage their use, and could consider incentives to lower the cost of zero-emissions fuel, which could in turn increase demand for green shipping.
Green corridors represent the opportunity for the industry to create a pathway for implementing zero-emissions fuels. They create a system for mobilising demand and sharing benefits along a more specific and limited group of stakeholders. This would involve relevant value-chain parties, such as fuel producers, cargo owners, vessel operators and regulatory authorities. Having these stakeholders on board would provide offtake certainty to fuel producers and send a strong signal to others to invest in zero-emission shipping, alleviating some of the risks.
Because it is limited along one corridor, the risk for these stakeholders would remain relatively low compared to a complete zero-emissions vessel overhaul, while also having a significant impact on cutting down global shipping emissions. Corridor-specific initiatives could be used to increase demand through pre-competitive coalitions. The creation of a transparent, standardised tracking registry could help stakeholders to better manage risk and reduce loss.
TCO, which is the cost of capital expenditure and operating expenses during the lifetime of the ship, rises significantly with the introduction of zero-emissions fuels. Alongside the added expense of the fuel itself, extra costs might also include the opportunity cost of lost cargo space for larger zero-emissions fuel tanks. This is a vital consideration when deciding the fuel type and shipping corridor – but green corridors share this risk along the corridor.
This system is expected to have significant spill-over effects in the reduction of shipping emissions through other corridors. Once the infrastructure for a green corridor is set up, it could also be used for shipping on other, adjacent shipping routes.
This is just one of the reasons that deciding on the corridor route is so crucial. Corridors should be selected for their ability to incorporate a viable fuel pathway, considering the availability of zero-emission fuels and refueling infrastructure for zeroemission vessels.
Corridors should be able to mobilise demand for green shipping, and they should look to be scalable and replicable in other parts of the world, making their value increase. Policy and regulations that affect the corridor should also be examined, as incentives and regulations will be needed to ensure appropriate safety measures and to narrow the cost gap associated with zero-emission fuels.
Finally, any proposed routes should involve stakeholders who are enthusiastic about aiding decarbonisation and willing to collaborate to explore new forms of cross-value-chain collaboration.
Mining companies are now looking towards several viable options to establish green corridors and lower overall emissions.
The iron ore Australia-East Asia corridor
In April, a consortium led by the Global Maritime Forum and including BHP, Oldendorff Carriers, Star Bulk Carriers and Rio Tinto signed a letter of intent to investigate the development of an iron ore green corridor that would connect Australia to East Asia.
The consortium will enable discussions between private companies and the public to explore the specific requirements for establishing the corridor.
Currently, the shipping routes which connect Australia to East Asia are responsible for more than 22 million tonnes of carbon dioxide every year, and establishing a green corridor here is expected to significantly reduce this number.
Although there are no current estimated costs for the corridor as of yet, the biggest primary cost is expected to be zero-emission fuels. The letter of intent identified ammonia as the most promising fuel option, and the consortium is looking to enable the rollout of ammonia-fuelled bulk carriers and regional bunker capacity in 2026.
Global Maritime Forum CEO, Johannah Christensen, said that the success of this green corridor route would rely on the collaboration of key stakeholders.
“Zero greenhouse gas emission pathways require the creation of a parallel value chain that involves new ways of working, new contractual relationships and drives the development of decarbonised fuel production and infrastructure,” Mr Christensen said.
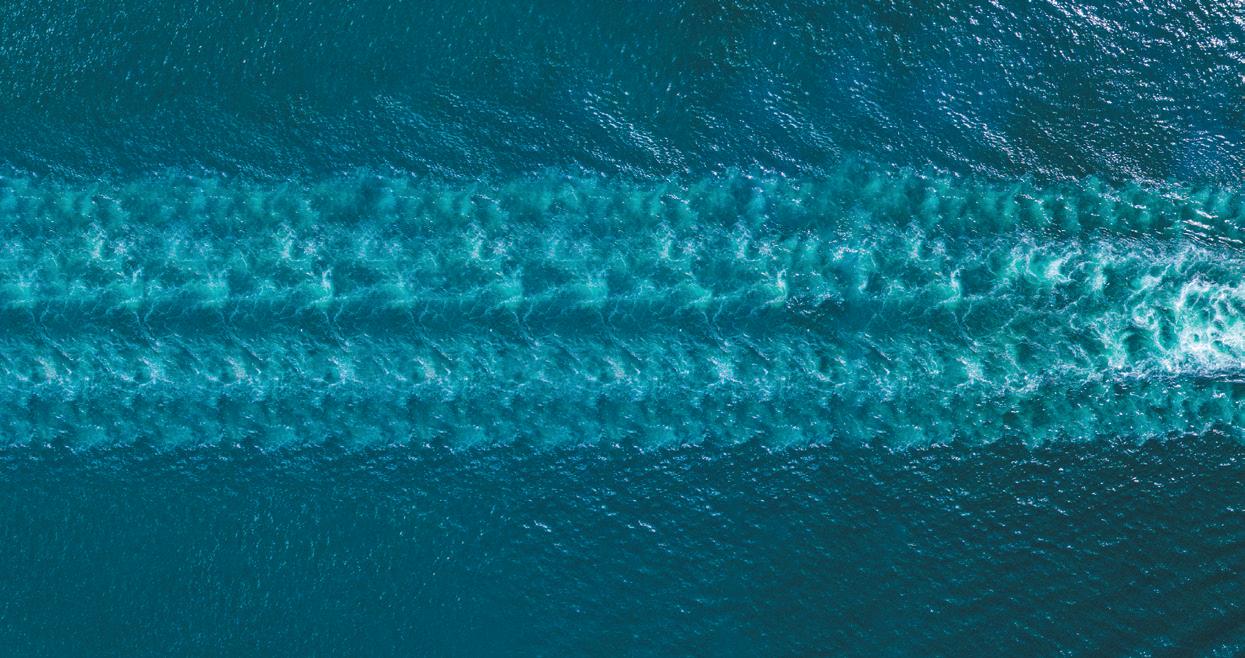
“This new iron ore green corridor collaboration is an important step towards enabling zero greenhouse gas emission shipping from both the supply and demand side.”
BHP Vice President of Maritime and Supply Chain Excellence, Rashpal Bhatti, said, “BHP’s membership of this green corridor consortium is testament to the importance we place on targeted exploration and partnerships in identifying pathways to decarbonisation for the maritime sector.
“As one of the largest bulk charterers in the world, we recognise this opportunity and have announced a number of partnerships across our value chain to seek to accelerate the process.”
Rio Tinto’s Head of Commercial Operations, Laure Baratgin, agreed that establishing the green corridor would be an important step in decarbonising the company’s shipping.
“This collaboration is another important step towards accelerating the delivery of our climate commitments on shipping, as part of Rio Tinto’s broader goal of net-zero emissions by 2050 and a 50 per cent reduction by 2030, and supports efforts in providing our customers and partners with sustainable value-chain solutions,” Ms Baratgin said.
Australia-Japan iron ore route
The consortium intends to further the development studies of the 2021 Getting to Zero Coalition report, The Next Wave: Green Corridors, which urged the sector to reduce its emissions, and suggested that green corridors could be key to transitioning to low-carbon solutions. The pre-feasibility study analysed the potential impact of an Australia-Japan iron ore green corridor.
The Australia-Japan route is one of the largest dry-bulk trade routes in the world, moving 65 million tonnes of iron ore annually. An estimated 75 per cent of the iron ore was shipped directly from the Pilbara region to Japan, with the remaining 25 per cent including stops at other ports. In 2019, ships carrying iron ore between Australia and Japan produced approximately 1.7 million tonnes of carbon emissions.
The report found that this route has a strong potential to be a first-mover green corridor, with growing momentum among stakeholders to decarbonise this route. Around 90 per cent of the iron ore exported from Australia to Japan is mined by companies that have announced net-zero commitments. This includes three major mining companies – Fortescue Metals Group, which has committed to net zero for Scope 3 emissions

by 2040, and Rio Tinto and BHP, which have committed to net-zero 2050 targets, including shipping-related emissions. For major mining companies, downstream transport can represent around 20 per cent of pre-processing Scope 3 emissions, and decarbonisation along green corridors could drastically reduce that number.
An Australia-Japan green corridor would capitalise on Australia’s increasing capacity for green ammonia and green hydrogen production, with plans to build 30GW of hydrogen electrolyser capacity by 2030. The world’s largest green energy hub, which will eventually produce green hydrogen and green ammonia, will add another 50GW of capacity in Western Australia. Many of these production hubs are planned near iron ore production sites and ports. Investors would have a secure supply and could benefit from cost advantages when exporting through these hubs.
This route would leverage the existing political collaboration between Australia and Japan, with one of the main appeals of the route being the willingness of stakeholders and a favourable regulatory environment. Depending on the regulations and incentives in the corridor, the report estimates an end-to-end annualised TCO gap of between 50 and 65 per cent, compared to a fossil fuel-based vessel.
However, new partnerships between miners, fuel producers and vessel operators could bolster demand for green shipping along the corridor. Evolving the partnerships into new institutional models, like joint ventures, is one way to mitigate first-mover risk. Stakeholders could also reduce costs through using innovative systems to share costs, and policy mechanisms could also help to bridge the gap. The report estimates that if a contracts for difference mechanism was implemented, it could bridge the cost gap between $250 and $350 million.
This report included three primary bunkering (refuelling) stations in North West Australia for zero-emission vessels travelling on the route. Port Dampier, Port Hedland and Cape Lambert would be the three Pilbara hubs. There is a possibility of bunkering at other low-cost ports along the route (such as in Singapore or China), but this would incur an additional cost.
Based on favourable production conditions, the study found that green ammonia was the best choice for an enabling regulatory environment and for getting willing stakeholders on board. Fuel production for the planned 41 zero-emission iron ore vessels would require an estimated 1.7GW of electrolyser capacity, calling for an estimated capital expenditure of between $3.7 billion and $5.2 billion. These costs would include electrolysis, hydrogen storage, the ammonia production process and the investment costs for renewable electricity.
For the consortium, the next step is to jointly assess green ammonia supply, bunkering and first-mover support mechanisms. Ultimately, the aim is to develop a framework as an initial step towards actual implementation of a green iron ore shipping value chain.

Alternative green corridor routes
The report also studied a number of alternative route options, including a Brazil-China iron ore route. This route is much greater in distance, and so it was found to have a significantly higher impact on lowering overall emissions.
However, for this reason the route was also much more sensitive to increased fuel costs along the corridor.
An Australia-China route was also explored, but the study found that, from a regulatory point of view, the Australia-Japan route was much more feasible, with engaged and willing stakeholders. However, successful implementation of the Australia-Japan route could have spillover effects for a potential Australia-China route, given that some stakeholders in Australia and along the value chain would overlap. This would further accelerate decarbonisation pathways for miners who are exporting on other, adjacent routes.
The challenges ahead
The Australia-Japan iron ore green corridor will need coordination between a number of industry groups, as well as from governments and fuel suppliers that are involved. Although the route is still in very early planning stages, it is already attracting attention from big miners who are looking to cut down emissions at scale from their operations.
The pre-feasibility study highlights the potential impact of a green corridor, and its role as a potential stepping stone towards transitioning the industry.
Green corridors could further the momentum around decarbonising shipping as an industry, and prove that demonstrable systems can be put in place through coordinating stakeholders and deploying that system at scale.