
5 minute read
Flexible couplings – one size does not fit all
FLEXIBLE COUPLINGS – ONE SIZE DOES NOT FIT ALL WHY ARE THERE SO MANY OPTIONS? AND WHAT IS THE DIFFERENCE?
The primary purpose of any coupling is to join two shafts. Here we discuss linking a motor to a pump using a flexible coupling. Although rigid couplings could be used, flexible couplings both connect the two shafts and compensate for operating conditions like misalignment, vibration, load variations etc.
Advertisement
Flexible coupling types
Disc – Popular in the oil, gas and petrochemical industries. Often manufactured to API standards and available as standard, spark reduced or non-sparking. Long-lasting, allmetal construction with replaceable disc packs. High torques and good misalignment compensation. Maintenance-free. Jaw – Cheap and simple, used in lower-cost, non-critical setups. Replaceable rubber elements and cast iron hubs. Non-lubricated and normally disposed of rather than maintained. Older technology. Shear in place – Like Jaw but designed so the hubs are separated. In the event of an element failure, the driving hub disengages from the driven, spinning freely to avoid motor or pump damage. More expensive than Jaw initially but a better return in the long run with fast changeout of elements without the need to remove hubs. Grid – Toothed hubs are joined by a hi-tensile metal grid element. Higher cost but excellent torque transmission in a compact unit. Grease-lubricated, so they require some ongoing checks. All metal construction. Grid elements can be changed without the need to remove hubs. Gear – Gear teeth in the hubs engage with teeth in the housing/sleeve. Very high torque and excellent misalignment capability. All metal construction. Requires regular greasing and maintenance checks. Extremely high loads. Popular on larger, high torque drives. Rubber in compression – Hard rubber elements are compressed into pockets of the flex half of the coupling. High load and excellent at absorbing vibration (eg. diesel motors). Intrinsically failsafe so also popular on fire pumps (if the elements fail, the coupling will still drive). Good choice for variable speed drives. Tyre – Rubber tyre couplings are old technology, cumbersome and induce higher axial loads on bearings. However, the new technology using split urethane elements and variable spacer lengths, makes the “modern” tyre coupling one of the most versatile and economic of all of the above. Inert to water and resistant to many chemicals. Fast change out and excellent for non-standard DBSE length situations.
Choices, choices! So which coupling is “the right one”
The first step is understanding the parameters of your application. Speed, power, service factor, the distance between the shafts and any regulatory requirements (API, Atex, IECEx) must be clear before a selection can be made. Other factors like operating temperature, vibration and other maintenance requirements need also be considered. And of course, “overall” long-term cost. Be careful – price does not equal cost and with couplings, you get what you pay for.
Deciding which of these factors is most important to you is key to making the right design selection. And that’s where Drive Systems can help.
Drive Systems is a specialty supplier of power transmission equipment with a particular interest in couplings for the pump industry. We keep good stocks of all the above types of couplings in industry-leading brands. You won’t have to “settle” for a particular type of coupling just because that’s the only one we have on the shelf.
Our experienced engineers will select the ideal coupling for your application based on what YOU need, not on what we’ve got.
A proud member of the Pump Industry Association, Drive Systems is an Australian-owned and operated company that knows your industry.
Drive Systems +61 (0)3 9796 4800 info@drivesystems.com.au drivesystems.com.au
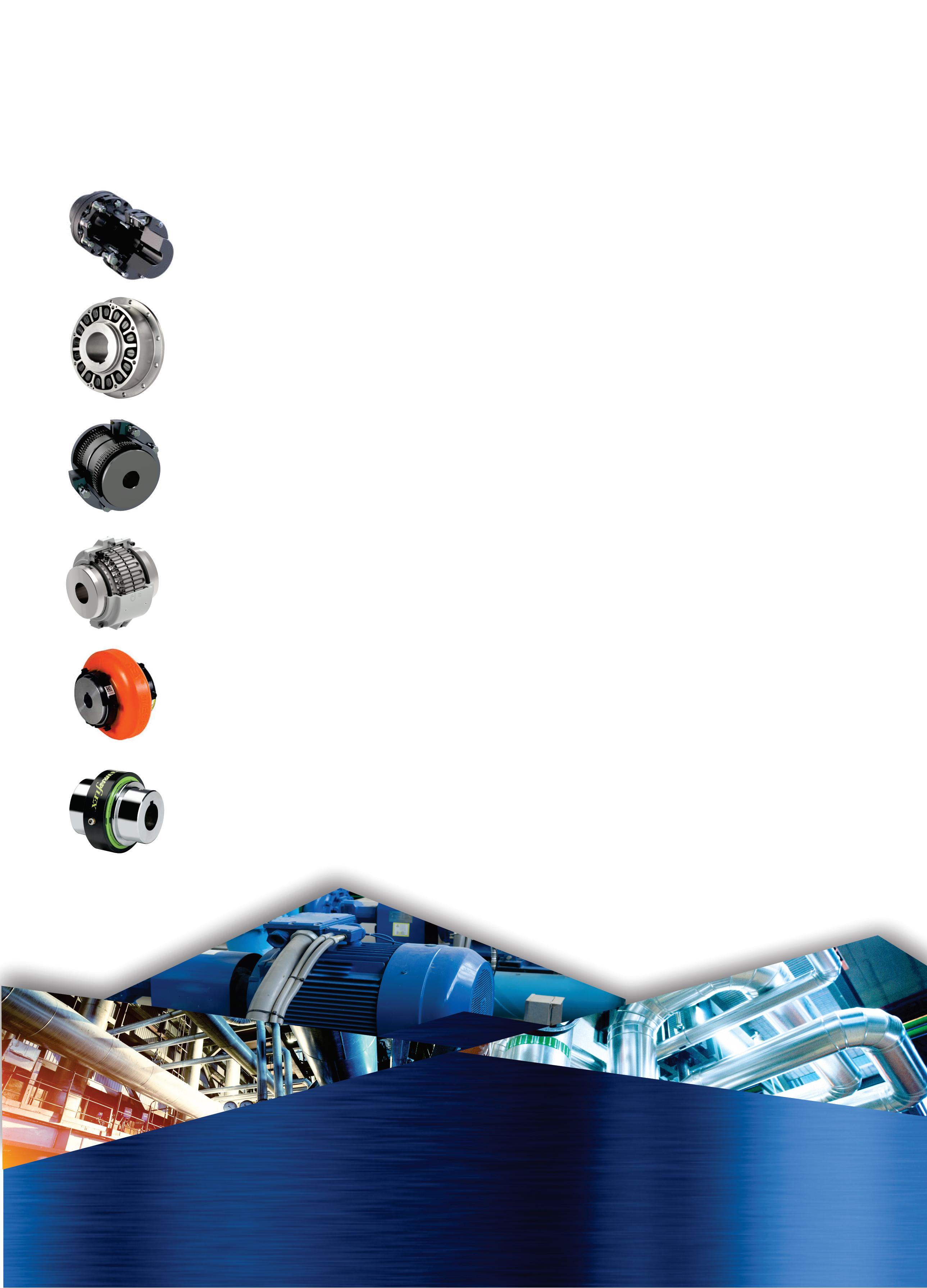
There are several factors to consider when choosing the right coupling to use in wastewater treatment to ensure coupling suits the intended application, including type of coupling, the material used and application purpose.
Particularly in sewer applications, couplings are susceptible to damage from water, chemicals, piping stress and other factors, which all impact reliability and durability.
Not every coupling will work well on any application, each type and material has different capabilities, benefits and limitations. Here is a breakdown of criteria and considerations that should be taken into account when selecting the right coupling.
Criteria to suit various applications
Couplings are designed to connect two shafts together – the pump to the motor – in order to transmit rotary motion and torque from one piece of equipment to another.
Other secondary functions can include accommodating misalignment between shafts, permitting axial adjustment, vibration dampening, and absorption of shock loads.
It is important to properly evaluate different coupling types and the materials used in their manufacture to ensure they are the right fit for a particular application.
Choosing the right coupling will make for an easier installation, help to reduce stress or fatigue on other parts of the driver, and avoid maintenance later on.
When evaluating a coupling’s application capabilities, certain criteria must be considered: • Motor horsepower and operating speed • Operating temperature • Space limitations • Misalignment handling requirements • Chemical exposure • Materials used for components • Type of driven equipment
Using these criteria can determine whether a coupling is effective, durable or powerful enough to suit a certain application, because not all applications require the same capabilities.
Couplings in wastewater treatment
In wastewater treatment, couplings can be used in specific applications, such as terminating or extending pipe runs, changing the size of the pipe or repairing breaks and leaks.
In particular, couplings are used in screening and multichannel oxidation ditches, which require specific considerations when selecting a coupling type and material.
For example, during filtering, excess material such as paper, plastics, rags and metal can clog screens and the processes to remove those excess materials can increase shock loads to the couplings and shafts.
Additionally, for multichannel oxidation, the ditches, mixer and aeration equipment must be used over larger areas, which results in higher misalignment capabilities.
Spills and overflows can also cause damage to the environment if the pumping equipment is not reliable.
A coupling used in wastewater treatment should be durable, malleable and water resistant in order to be effective and last the distance.
Selecting a coupling that best fits wastewater applications can save damage and maintenance costs in the long run, but doing so requires knowing which materials and types of equipment to use.