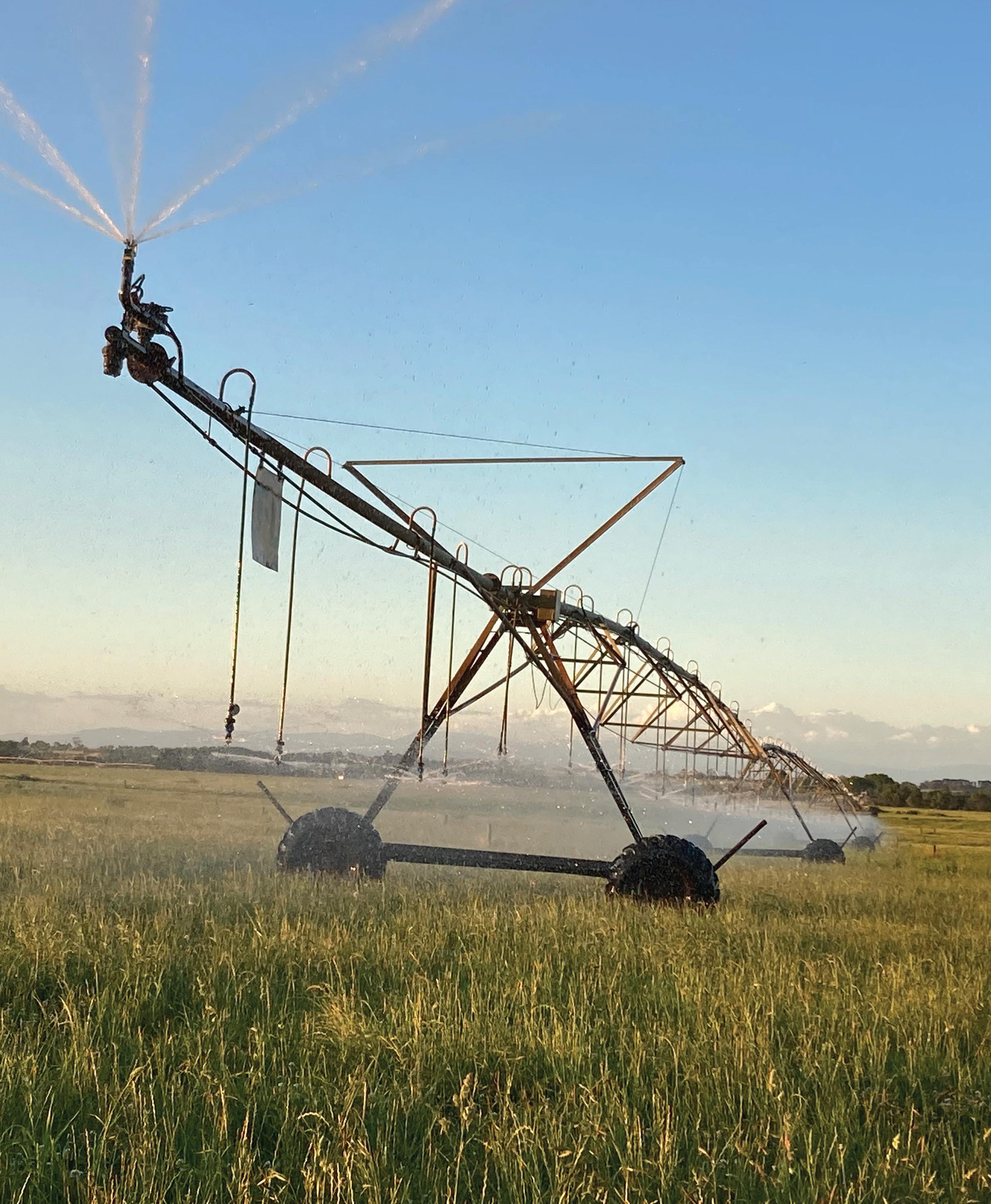
9 minute read
ENERGY TRANSITION
Sandra Jefford and Wilco Droppert own and operate Wilandra Farms, an organic dairy farm in the Gippsland region of Victoria. Despite the farm’s success, energy costs were high and irrigating the farm was a costly and time-consuming process, with irrigation and dairy operations using about 500,000kWh of energy per year. In an effort to reduce both the cost of irrigation and their carbon footprint, the couple embarked on a mission to generate their own power and upgrade their pumping system.
Sandra and Wilco moved to the Gippsland area in 2011 and began farming organically in 2016. Located at Clydebank, Wilandra Farms is a certified producer of milk, silage and hay and the property houses 380 certified organic dairy milk cows year-round.

With the success of the farm have come bumps in the road. The couple realised that the farm’s energy costs were too high, particularly in relation to irrigation – which was accounting for 70 per cent of the power used on the farm. They had been using a diesel pump to pump water from the dam to pivots, which was not only expensive, but bad for emissions and a huge drain on manual labour.
Sandra and Wilco opted to install two 37kW Caprari electric pumps to replace the diesel pump that was used to pump water from the dam to the pivots. This had many benefits for the farm – the pumps can be operated remotely via phone or computer, saving the pairmany hours each week from having to drive between pumps and pivots. The variable speed pumps also improve energy efficiency by ensuring that the irrigation system does not run when it doesn’t need to. For example, in 2022–23, the area was very dry from mid-December to late March – so the irrigation system needed a lot of grid power. The system was able to adapt easily to the change in conditions, resulting in very little peak price power.
“There's lots of benefits. We are saving at least 15 hours a week, maybe 20 hours a week in busy irrigation times because of the automation, because we don't have to drive to the pumps and the pivots anymore. We can stop and start things from a laptop.
“And we’re seeing big energy savings. January and February were extremely dry, so we pumped a lot of water. Even so, our cost of energy, the irrigation was only six cents per kilowatt hour. And so another advantage is with all the talk of the price of electricity increasing, we're quite nicely protected against that now because we don't need that much grid power,” Sandra said.
The couple also replaced two old, oil ring vacuum pumps with a lobe vacuum pump, resulting in less power demand and a far cleaner vacuum pump with no need for oil changes.
Investing in renewables
The farm’s soaring energy bills led the couple to pursue an energy audit. While the purpose of the audit was initially to lower costs, Sandra and Wilco realised that there were other benefits to upgrading and updating their irrigation equipment. The energy audit opened their eyes to the potential benefits of renewable energy – which could also save the couple hours of work every day.
“Our energy project started because of the big energy bills, particularly for irrigation. And it was after we'd had the energy audit done, we then started to look at emissions related to energy and then that set us on the track of looking at emissions further. It was really the energy bills that started the whole project,” Sandra said.
Improving pump efficiency
The energy audit revealed multiple deficiencies in the farm’s current equipment and areas for potential improvement. Sandra and Wilco pumped all their irrigation water from bores and the Avon River, traveling through lengthy pipelines. The audit uncovered two key pieces of equipment that would have far greater capacity if replaced – the existing bore pump’s motor was too big, and a 500m pipeline was the wrong diameter. These two improvements alone are estimated to have reduced power use by about 37 per cent at the pumping site.
The couple were also using a diesel-powered pump to pump water from the dam to pivots. Because the pumps and pivots were not automated, the couple were frequently having to drive between them – costing them valuable hours every week. The manual diesel pump was constantly working, not able to adapt to changing conditions, which meant that emissions were also much greater than necessary.
To lower energy costs whilst also investing in more sustainable solutions, the couple worked with Alternate Energy Innovations (AEI) in Morwell to develop a Renewable Energy Action Plan. They received funding through the Victorian Government’s Agriculture Energy Investment Plan to help with costs. So far, renewable infrastructure updates include the installation of 200kW of solar energy and 56kWH of batteries, with four 5kW wind turbines also in transit to the farm for installation – which has meant huge savings on the cost of electricity.
“We have dropped the price of power that we're using for irrigation down from 27 cents per kilowatt hour down to six cents per kilowatt hour this year. We've still got our equipment finance loan to pay off, but we've already been paying that off now for about two years, so we've only got five years. Then it's paid off, and we've got free energy generation. In terms of the total energy costs for irrigation, depending on the year and how much water we're pumping, we were spending between $80,000 and $100,000 on energy costs for irrigation,” Sandra said.
The investment in renewable energy enabled another big change – connecting the bore pump to solar energy. The farm houses solar panels facing north, east and west to maximise the amount of energy they can produce. Solar powers the pumps, and with the installation of variable speed pumps, energy efficiency has further improved by ensuring that the irrigation system doesn’t run when it doesn’t need to.
“With the bore, it's connected to solar power. Once we've got a low level of solar power early in the morning, that bore starts slowly dumping water in the dam. We are able to use a low level of farm generated power. The solar power is so successful, in future we will look at putting in more solar power because with it being so dry this past summer, we were using a lot of off-peak grid power, and in the future we'll try and replace a lot of that with farm generated power,” Sandra said.
Future bright for solar-powered irrigation
With many positive changes implemented, Sandra and Wilco are keen to continue with their renewable upgrades. One challenge the couple faced was with the installation of additional wind turbines. The couple expect to add two 15kW turbines to their existing stock of four – but due to a technical problem with the manufacturer in the UK, they are still waiting.
“We've got four five kilowatt turbines here as a temporary measure, and eventually we expect we'll have two 15kW turbines, because there was a technical problem with the manufacturer in the UK. And then there's been a problem getting inverters to be compatible with the turbines. And I think this is just because turbines at this sort of scale are still very unusual and the inverter manufacturers are not putting the effort into making the inverters to match the wind turbines,” Sandra said.
The electricity grid posed another challenge for Wilandra. There is no smart grid at the farm, so electricity generated at the farm goes into the grid, which they sell to for six cents, but they then have to buy it back from the grid for 36 cents. The couple said the grid needs a system that allows them to allocate the excess power elsewhere, rather than across a range of separate meters.
The couple also had the intention of installing a microgrid. Microgrids provide energy generation and storage at a local level, which would have enabled the couple to generate, store and sell even more renewable energy. However, strict regulations around microgrid installation meant that the couple had to alter their generation and storage plans.
“We had hoped to run a controlled microgrid on the farm, but the regulations are such that that's just not possible at the moment. But if farms were able to use controlled microgrids, they could make much better use of the renewable energy that they're generating. It becomes more cost effective. And we could hopefully see more farmers installing renewable energy on their farms, but we need a change in regulation,” Sandra said.
Despite these challenges, Sandra and Wilco are optimistic about further renewable upgrades to the farm – particularly the installation of more solar panels.

“Like a lot of other farmers, we've got land that isn't the right sort of size and shape to put a pivot on. We've got a project just getting started to put in fixed sprinkler irrigation using surplus solar power at a particular bore site where we've got 50kW of power. That's underway, and in future we'll have another look at how much solar power we need, and we'll probably look at putting another pump at the dam, so that each center pivot has its own pump that's pumping out of the dam to a pivot because that'll make the automation easier. At the moment, we've got three pivots and they share two pumps.
“So there’s plenty to do - we just need a good strong milk price to enable us to keep going with all these improvements,” Sandra said.
The couple recommend solar energy installation for all irrigators, saying that the cost savings, coupled with the huge environmental impacts, are hard to ignore.
“I think particularly for any irrigators, if you are using grid power, it's really worth having a look at installing solar energy. Particularly if you've got a dam, if you've got the ability to pump into a dam and then pump out, you can get some massive benefits with solar power,” Sandra said.
To encourage other irrigators to move toward renewable solutions,the couple hosted a knowledge-sharing event in February 2023, titled “Smart Farm Power – Opportunities in an uncertain carbon future”. Participants attended presentations and then visited the farm to view the automated irrigation and renewable energy system, and other features of the Wilandra Farms regenerative farming system.
Sandra said she felt it was important for the dairy industry to unite on a progressive path.
“I think farms can play a huge role in reducing emissions, and a collaborative approach using microgrids could even reduce the need for transition lines – that’s our hope for the future and we’re excited to share the results of our project to inspire others,” Sandra said.
The pump industry relies on expertise from a large and varied range of specialists, from experts in particular pump types to those with an intimate understanding of pump reliability; and from researchers who delve into the particulars of pump curves to experts in pump efficiency. To draw upon the wealth of expert knowledge the Australian pump industry has to offer, Pump Industry has established a panel of experts to answer all your pumping questions.
In this edition of Ask an Expert, we will continue looking at progressive cavity (PC) pumps and how they can be utilised in the mining industry. PC pump experts are often asked if these pumps are suitable for the mining industry. In fact, PC pumps are very common on mine sites throughout Australia. For these pumps, this particular market sector would be on a par with water/wastewater as one of the most popular in Australia. Listing the various applications in detail would take up this entire issue of the magazine, so instead, below is a summary of the typical applications and key benefits of this pump design.

PC pumps are commonly used in the following mine types:
• Bauxite (also refined alumina)
• Coal
• Copper
• Gold
• Iron Ore
• Mineral Sands
• Nickel
• Shale Oil
• Tin
• Uranium
• Vanadium
• Zinc
PC pumps are also used by countless suppliers of mining equipment and chemicals for:
• Decanters and centrifuges
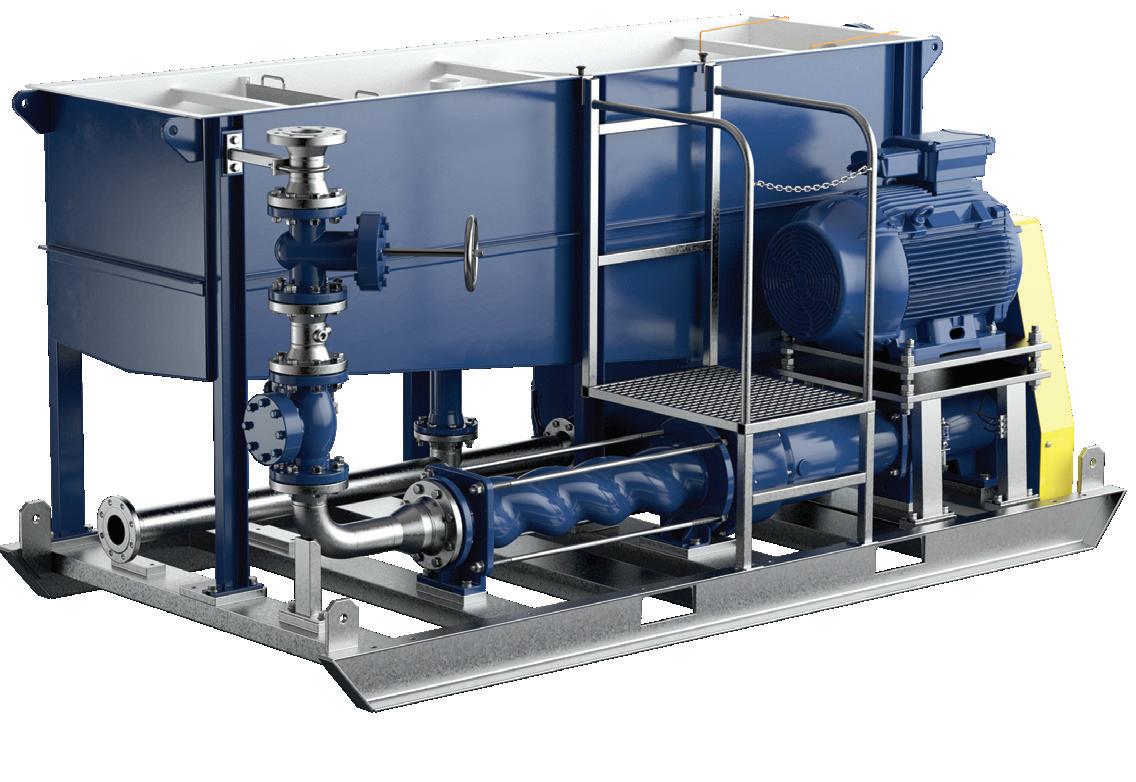
• Tunnel drilling equipment
• Flocculants
• Chemical dosing
• Liquid explosives
What are the benefits of PC pumps?
The properties of PC pumps that benefit the mining sector are:
• Self-priming
• Minimal pulsation
• Valve-less operation and flow control
• Reversible for back-flushing
• Flow proportional to speed
• No day to day maintenance required
• Versatile: can be installed horizontally or vertically and in virtually any position
• Minimal flow rate variation even with changing pressures
• Handle multiphase products (liquid and gas)
Common applications for PC pumps in mining transfer of mineral slurries
• Void back-filling applications
• Dosing of explosives
• Thickener underflow applications
• Centrifuge filling
• Chemical dosing
• Water treatment
• Cake transfer
• Leachate treatment
• Gland water supply
• Sludge feed to dewatering machines
Typical transfer liquids include polymers, sludge, slurries, grout, various chemicals and clean and dirty water.
Mine dewatering applications for PC pumps
This is one of the most common areas where progressive cavity pumps can be seen, usually installed on a transportable skid with collection tanks for incoming water, and usually incorporating some form of solids separation to partially clean the muddy, high sediment mine water. The range of progressive cavity pumps used for these applications is long due to the pressure generation required to pump from several hundred meters underground to the surface. There are now a number of companies that specialize in this application area, and occasionally new designs are developed that can provide significant benefits to users of this product range. Keeping abreast of these developments can certainly pay significant dividends for mine operators. More detailed information on specific design developments can be requested using the contact details at the end of this article.
Peter Vila, Managing Director of SEEPEX Australia, is a progressive cavity pump expert. He has been involved with pumps for over 40 years. Peter spent the first five years repairing pumps and the following 35 years in technical sales, 20 of which have been with SEEPEX progressive cavity pumps. For more information on progressive cavity pumps, please contact SEEPEX Australia on (02) 4355 4500 or at info.au@seepex.com
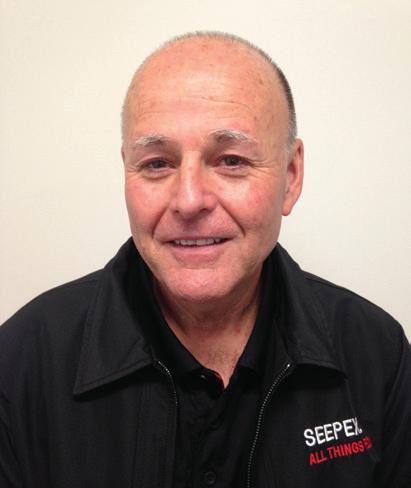