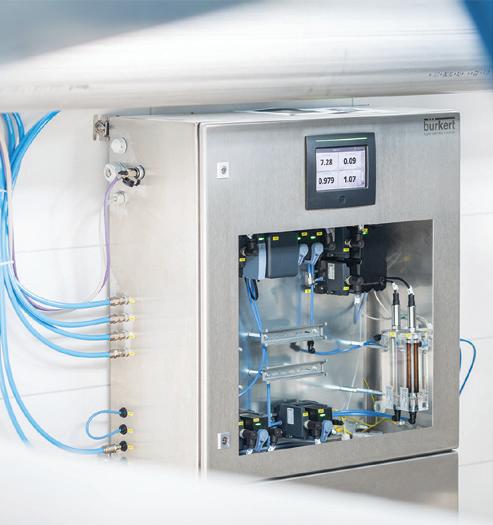
2 minute read
Controlling the iron content in water treatment
There are strict standards placed on the quality of water used for drinking and food production, and water with a high iron concentration can cause major issues including cloudiness and impaired taste. It’s therefore critically important that a treatment plant’s iron removal system is checked continuously – a process that can demand a great deal of time and resources.
An excessively high iron concentration in water can cause long-term sedimentation of iron particles in pipes and valves, which leads to a reddish discolouration of water. An iron concentration of 0.5 mg/l can be tasted by humans, but the actual limit value is 0.2 mg/l. If this limit value is exceeded, it needs to be dealt with immediately to prevent adverse effects.
Advertisement
TRADITIONAL PROCESSES
In conventional systems, iron removal is achieved using oxygen or chemical dosing. Iron dissolved in water is oxidised and precipitates as metal hydroxide, and then filtered out with quartz sand.
When it comes to the monitoring process, one turbidity sensor is used for each individual filter. However, monitoring individual sensors requires a large amount of time and personnel, as it is carried out randomly for each individual filter line with the laboratory or handheld photometer.
A turbidity sensor does not show if the iron removal process is running successfully or if it is working with the optimum amount of oxygen or chemical dosage.
In traditional plants, the filter load must be monitored at all times and each individual filter checked, so it is difficult to find the optimal backwash time. Each individual sensor must also be cleaned and calibrated regularly, making the entire process time-consuming and not cost-effective to the plant’s operation.
AUTOMATING IRON MEASUREMENT ANALYSIS
With any laborious and expensive process in the water sector, utilities are turning to automation to reduce manual monitoring and costs. Automated sensors are highly beneficial for iron content because it is something that must be observed constantly to prevent the limit value being exceeded.
Bürkert’s MS06 flow injection analysis (FIA) sensor cube for iron content and online analysis system is helping to automate the process of controlling iron content and turbidity in raw water. The MS06 sensor cube uses state-of-the-art flow injection analysis to quickly detect excessive iron values in process water, monitor the load status of filters and react accordingly – with just one sensor able to monitor multiple filters.
It analyses the iron content in cycles, operates fully automatically and has extremely compact dimensions. Its flow injection analysis requires only a few reagents, making it economical, and the barcode-based reagent detection prevents misidentification.
It works by using high-precision microfluidic components. A sample is taken from the flowing medium, and a reagent is added. Then the sample and reagent are pumped through the system and mixed – the reaction forming a specific dye. The iron content is then determined through the photometric analysis of this dye.
In addition to the iron sensor, you can integrate sensors for pH, chlorine, chlorine dioxide, ORP, conductivity and turbidity, and in combination with Bürkert water sampling, just one sensor unit – consisting of the aforesaid sensors – can monitor up to eight sample water lines.
For more information, visit www.burkert.com/en.
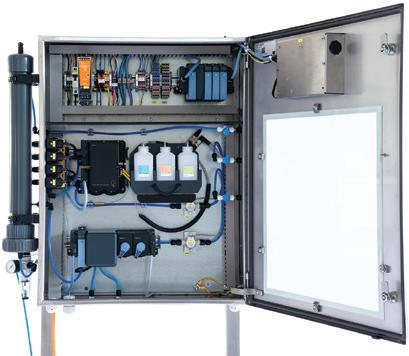
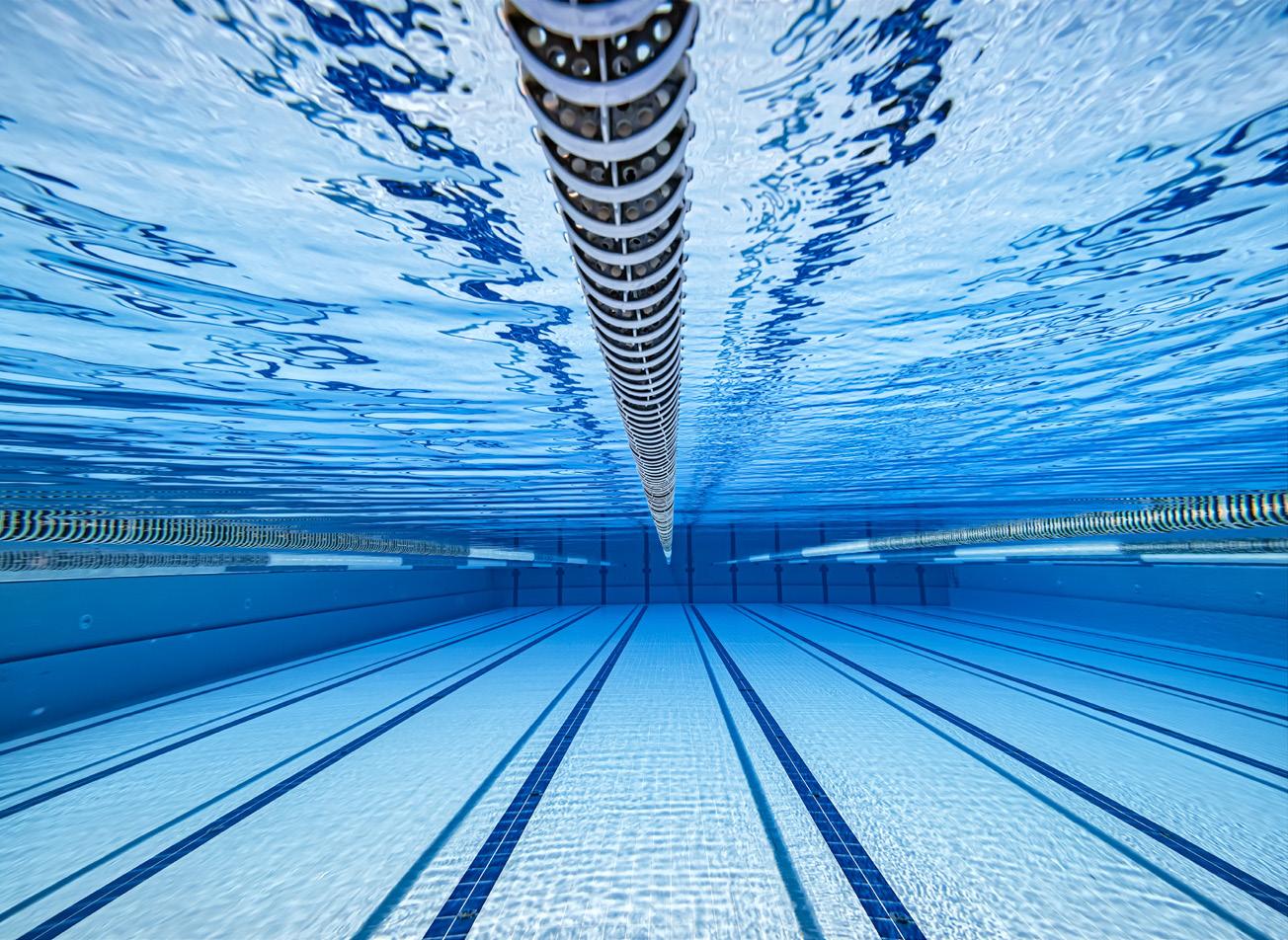