
4 minute read
Hydraulic modelling of Flusher units
The Flusher is an innovative system that utilises the potential energy from the flow within the sewer to clean it. This outline is extracted from a case study undertaken by Atkins Global to assess the effectiveness of the Flusher units theoretically, using infoWorks CS.
The Flusher units have been simulated in InfoWorks CS using the Real Time Control (RTC) functionality. The assessment has been undertaken on an example 225 sewer prone to siltation at four separate locations. The sewers where silt occurs have been laid at gradients of less than 1 in 300, while the average gradient of the whole branch is approximately 1 in 120. The study investigated the effects of locating the Flusher unit at five locations in the system and assessing the results.
Advertisement
Under a dry weather flow, the greatest increase in velocity occurs immediately upstream of the Flusher unit and within the first 500m downstream. However, the units are responsible for an increase in peak velocity for up to 4km downstream. Furthermore, the increased velocity would be repeated for every operation of the Flusher unit which could typically be more than 50 times per day depending on the characteristics of the catchment.
It was predicted that the Flusher will operate approximately 64 times in a day under dry weather flow conditions, therefore improving flow conditions by eliminating silt build ups.
The steps in assessing the benefits of a Flusher: • Review historic and ongoing jet cleaning costs • Undertake a hydraulic performance assessment of the location • Consider the effectiveness of various Flusher locations • Assess potential upstream surcharge risks • Evaluate downstream benefits • Develop a monitoring plan
A cost-benefit analysis can be completed once the above information has been sourced, assessed and evaluated.
FLUSHER II
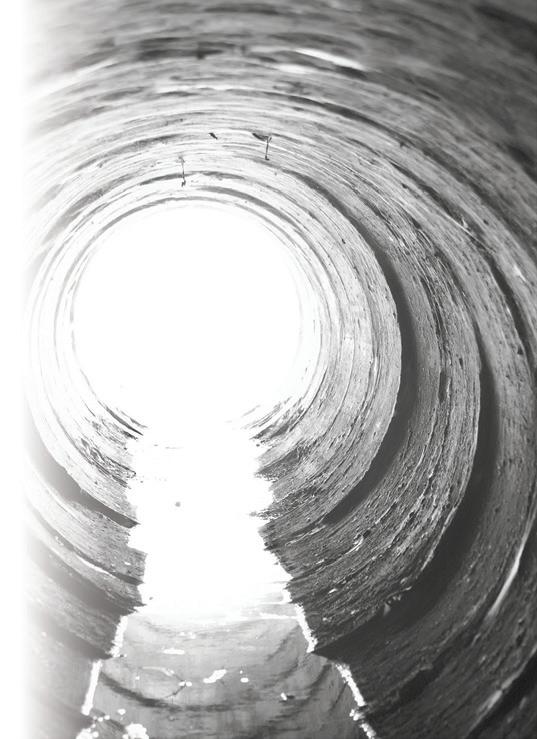
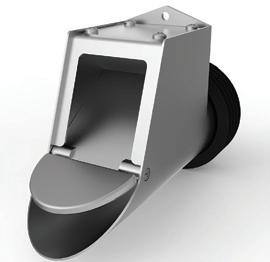
A passive gate device for controlling and maximising hydraulic flow in sewers
• Reduces operational costs – No more water jet sewer cleaning – No more Silt & Debris removal – Less surcharge & blockages
• Installed in Maintenance Holes – Easy to install – Easy to maintain – For DN150 to DN450 sewer pipes • Resistant to rag jamming and blocking • Inherently “fail safe” during storms • Data Logger and Telemetry Module – Know what’s happening and when
+61 418 691 989 6/58 Box Road, Taren Point NSW 2229 Australia enquiries@aussietrenchless.com www.aussietrenchless.com
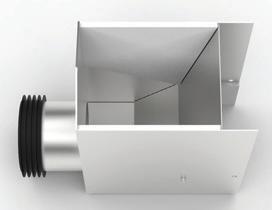
Interflow announces game-changing solution for water mains: RediFlow®
Industry leader in pipeline infrastructure, Interflow, is excited to announce the launch of RediFlow®, an advanced Pressure Water Main Renewal System that takes efficiency to the next level.
As thousands of kilometres of asbestos cement pipes reach the end of their service life across Australia and New Zealand each year, asset owners are seeking low impact, affordable ways to renew their water infrastructure.
A company that continues to push the boundaries of pipeline innovation in pursuit of meeting its customers’ water infrastructure needs is Interflow. Working with researchers, specialists and engineers, the organisation has developed a game-changing water main renewal system called RediFlow® . This methodology combines exclusive Titeflow® H112 and patented Infrastop® technologies into one synergistic process, providing an ‘all-inone’ package for renewing ageing water main pipelines.
How RediFlow® works
Traditional shutdowns using network valves are disruptive, impacting hundreds of customers at any one time. Rediflow’s Infrastop component can greatly reduce the number of impacted homes by isolating only those pipeline sections specific to the works being delivered.
Infrastop® is a temporary under-pressure fitting that immediately stops flow within a watermain. It only requires a small excavation and can be rapidly installed and operated within 90-minutes, without interrupting supply to consumers upstream. With Infrastop® in place, Interflow’s Titeflow process then installs a new tight fit HDPE pipe into the host pipe. This snug-fitting technology uses H112, an internationally recognised, high quality, high strength PE100 compliant resin that is specifically designed for pipe applications.
The Titeflow pipe is towed under tension through a static die, reducing its diameter and allowing it to pass through the host pipe. Once it is in place, the pulling load can be released. The liner pipe increases in diameter, fitting tightly inside the host pipe.
The liner is then connected to the main, new service tappings are installed, and the Infrastop® plugs are removed, leaving the offtake in place and the community’s water supply ready to use.”
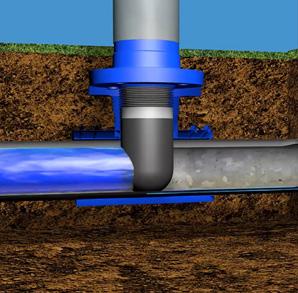
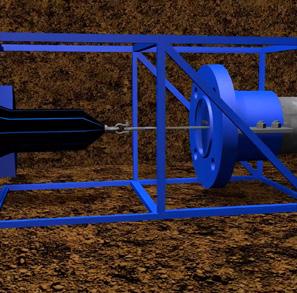
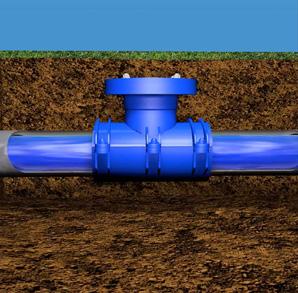
Learn more about how Interflow is solving their customers’ problems at interflow.com.au