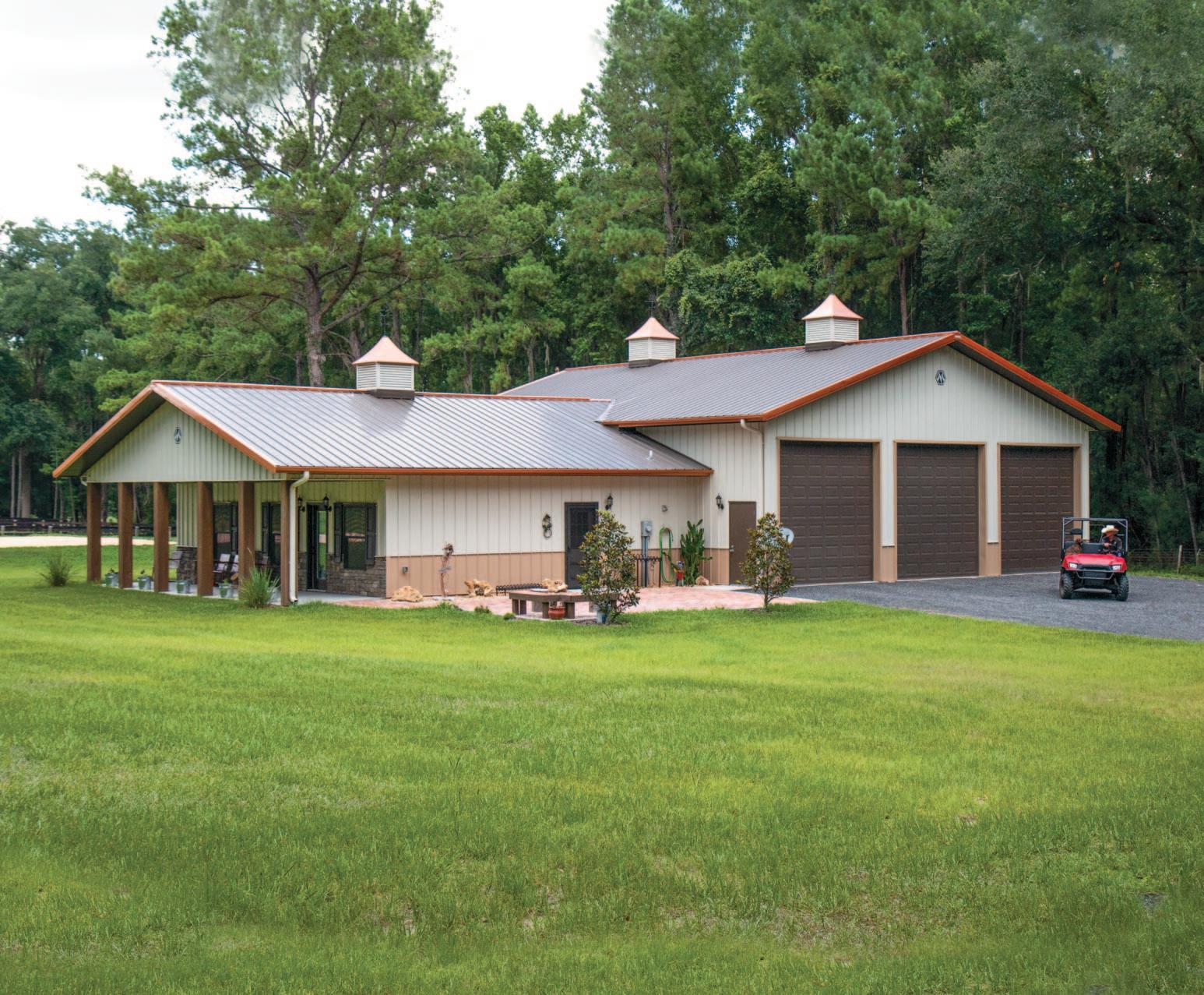

There are a lot of choices and building styles available for home construction. There are also many factors to consider when making a decision on who is going to build your next home.
Morton Buildings utilizes a method known as post-frame construction. Post-frame is defined as an engineered wood-framed building or home that features large laminated columns instead of wood studs. There are multiple advantages to this method of construction:
›› Clear-span Construction. Using this method we eliminate interior load-bearing walls. The result is a truly open interior space for you to customize and finish based on your needs and design preferences.
›› Energy Efficiency. We offer an exclusive Energy Performer package which offers R-values that far exceed other traditional home insulation methods.
›› Virtually Maintenance-Free Exterior. Using our exclusive Hi-Rib™ steel for your roofing or siding ensures nearly zero maintenance for years to come.
›› Unmatched Structural Warranty. Experience a warranty like no other in the home building industry. All Morton buildings are backed by the strongest, non-prorated, and non-pass through warranty.
It is important to note that the planning process for a Morton home can differ from traditional construction. Obtaining appropriate financing and preparing a construction site are critical first steps.
The cost of a Morton home will vary depending on the your level of involvement throughout the process. Many of our customers like to act as their own general contractor for all interior finishing, where Morton provides the insulated shell and they handle the rest. This option can save upwards of 20 percent of the total finishing cost, making this an attractive option.
While our process is slightly different and often requires more homeowner involvement, it is often an optimal choice for many people seriously shopping for their dream home.
Strength.
Morton homes are engineered for your site and building requirements, which provides superior durability over other construction methods. The strength of post-frame buildings lies within the framing system, which forms a box with superior wind resistance. For our homes, laminated columns mounted to concrete slabs or foundation walls allow the structure to perform well under seismic loading conditions. Trusses sit in a saddle for double strength against wind sheer. A diaphragm action creates an effective bracing system that resists lateral forces. Even before we attach any siding, your Morton building can outperform many other structures.
Open Floor Plans.
Large clear spans allow you to maximize the space and function of your home. Clear-span construction eliminates the need for interior load-bearing walls, giving you the freedom to plan a floor plan layout that best fits your lifestyle. From a single-family home with room to grow, to a cabin that provides a low-maintenance getaway for you and your family, Morton Buildings constructs homes that meet your specific needs and style.
Efficient Construction.
You can begin post-frame construction nearly any time of the year, and once you begin, the amount of time it takes to get “under roof” for a post-frame building is approximately half what you would normally expect from other construction techniques.
The warranty is awesome and the service is good.” 4839
"You can make them [Morton buildings] look anyway you want
Randy R. • Rapid City, SD on the outside…
The difference between a good building and a great building is not only how it functions today, but how it looks, performs, and functions years from now. We can work with you to achieve any exterior look you desire. Roofing options such as Morton’s Hi-Rib™ steel or shingles are available to complete the look. Exterior finishes are almost limitless for your home, including no-maintenance Hi-Rib steel, vinyl siding, wood, and masonry.
Morton buildings age gracefully because we use quality products to ensure you have a building you can be proud to own for years to come.
Comfort.
We build comfort right into your building with a design that allows maximum insulation, air circulation, and condensation control. Energy-efficient components that save on heating and cooling costs for the life of the building include:
• Extra deep (15½”) truss heels that allow for extra insulation
• Our Energy Performer® insulation package, the industry benchmark for comfort and savings
• Walls nearly 9" thick; six of those are insulation
• Insulation that descends below the top of the concrete floor to increase efficiency
• A continuous vented ridge design to help protect your insulation from condensation and your building from leaks
Second and third generation owners will tell you Morton buildings look new after decades of use. From foundations to fasteners, every detail is designed for minimal maintenance. In fact, the reason we offer the industry-leading warranty is because our buildings:
• Use FLUOROFLEX® paints because they resist moisture and UV light
• Won’t corrode or rot because of treated wood, true stainless-steel screws and rust-resistant ring shank fasteners
• Stand strong against high wind and snow loads
• Control condensation and protect insulation from moisture and sagging
If we’re going to put our name on it, we’re going to make sure it’s done right. To control quality, we:
• Use unique designs, matched to your specific geography and climate conditions
• Manufacture our own products in the United States
• Personally deliver and unload your materials at your site
• Build using professional craftsmen who only construct Morton buildings
Morton uses prime steel manufactured at our own plants—pre-engineered, 26-gauge commercial quality Hi-Rib™ steel.
• 1" high arch-shaped ribs spaced 12" apart with two minor ribs between each—the strongest architectural shape for withstanding water and weight
• Rib height up to 33% higher and steel thickness up to 25% thicker than panels used by other builders
• Steel panels are not welded, but rather fastened with screws and nails that add durability
• Our steel has superior resistant to hail and external fire supported by the Underwriter’s Laboratory, which can translate into building insurance discounts for some customers
Morton homeowners not only comment on the beauty and flexibility of their homes, they are also impressed with the efficiency of a Morton home. Imagine saving on heating and cooling costs year-round. That’s exactly what Morton owners have found. Thanks to our exclusive Energy Performer® insulation system, your building will be well insulated and remain comfortable throughout all seasons. The Energy Performer system combines superior wall/ceiling insulation with effective ventilation for a comfortable, cost-effective environment.
R-Value is the standard measure of thermal resistance. The more difficult it is for heat to pass through the insulation, the greater the R-Value. Research conducted by various energy-related organizations resulted in mandated R-Values for ceiling and wall insulation in various parts of the country, depending on climate conditions. The Energy Policy Act of 1992 made these mandates law. Morton’s Energy Performer insulation system exceeds these R-Value recommendations.
Our walls are 9 inches thick compared to the standard stick-built stud walls that are 4-6 inches thick. The result is our insulation can be both wider and thicker.
Anytime there is a break in the insulation or wood, it compromises energy efficiency. Stick-built construction has stud walls 16 or 24 inches apart, resulting in more breaks in the insulation. Our homes are built on 7'6" columns for maximized energy-efficiency.
Polyethylene vapor retarder is installed in our homes to keep insulation dry and reduce infiltration and heat loss by creating a seal.
HVAC, electricity, and plumbing can also be run inside the vapor retarder without cutting holes or breaking the seal.
Standard stick-built construction runs the wiring through the studs, which further lessens energy-efficiency.
Fully ventilated attic provides condensation control, resulting in dry insulation, which is more effective.
Our 15½ inch truss heels allow full depth, blown-in ceiling insulation with a rating of R-38 or greater, with the option to add more insulation to obtain an overall average rating up to R-60, and air space for attic ventilation.
Here’s Our Construction Process At-a-Glance.
1. If financing, get qualified for a post-frame home construction loan
2. Identify your land purchase, associated costs, and specific code requirements and site prep needs (i.e. septic, electric, driveway, etc.)
3. Choose level of construction involvement, either by working with a general contractor or doing the interior finish yourself
4. Identify floor plan preferences, to determine exterior project costs with your Morton sales consultant
5. With final project costs determined, obtain final approval from bank
6. Review plans and sign contracts
7. Obtain required building permits and begin construction
Our most popular home offering is a one-story, insulated shell and no interior finish work or infrastructure development (i.e. roadways, land clearing, septic, well, etc.). This offering provides you the opportunity to be your own general contractor or utilize your own general contractor for the interior finish work.
When budgeting for your Morton home, there are three main budget factors to consider:
• The price for our crew’s part of the build–the insulated, lockable building shell;
• The price for interior finish work provided by you or your general contractor
• Any additional costs for infrastructure development.
The price for our part of the build generally ranges from $75 to $125 per square foot, but your build location, final design and size of home could impact the square footage cost beyond those ranges. For instance, snow load engineering and site conditions in the mountain regions adds to the complexity and cost of the build. Depending on how you choose to finish the interior, that could run you another $75 to $150 per square foot.
It is important to note that the planning process for a Morton home can differ from traditional construction. Obtaining
Assuming you already have property, the next step is to determine where on the property your home will be located. Morton Buildings will help through this process but some things to consider include:
›› Codes: Check local building codes for restrictions
›› Proximity to Utilities: Closer means less costly
›› Flat Site: Preparation costs can add up quickly if grading and fill are required
appropriate financing and preparing a construction site are critical first steps. If financing is required for your next home, this is a very important step with several things to consider. First, Morton Buildings, Inc. does not offer home financing to its customers. Most of our customers end up working with a local bank that they have a relationship with.
If you are planning to finance your home, we request you get prequalified for a post-frame home construction loan through your lender first to best determine any budget parameters and their loan options. Financing for post-frame homes can be more challenging in some cases. Banks, and more specifically appraisers, do not always consider post-frame construction a conventional method for building homes. It is important that your bank understands the type of home you are building and who you are working with. It is also important to tell them if you plan to use steel siding and roofing. Depending on the bank you are working with, this may impact the term or rates you receive. Also, it is important to note that the method for “finishing” the home and who is responsible for that portion of construction may impact the amount that some banks are willing to lend. Although financing can be a bit more challenging, we have found that with a little effort and involvement that favorable financing can be secured.
›› Other Considerations and/or Restrictions:
• Deed Restrictions
• Homeowner Association (HOA) Guidelines
• Aesthetics Requirements
Other than the structure itself, the selection of your site may have the biggest impact on the overall cost of your project. If you are currently looking to purchase land, be sure to speak with the local permitting authority first.
The cost of a Morton home will vary depending on your level of involvement throughout the process.
Many of our customers like to act as their own general contractor for all interior finishing, where Morton provides the insulated, lockable shell of the home and they handle the rest. This option can save upwards of 20 percent of the total finishing cost, making this an attractive option.
However, depending on your location, our sales consultants may have local general contractor referrals available for the interior finish work. It is recommended to discuss construction involvement options with your Morton representative.
In Step 1, you learned about the costs involved in your project and estimated square footage prices for budgeting. Based on this information, you should have some ballpark estimates of what your Morton home will cost. Also note, based on your level of involvement as explained above, the pricing and timeline may vary.
Morton Buildings does not have pre-designed and priced floor plans. To start gathering floor plan ideas, there are some available on our website at mortonbuildings.com, or other online resources. Once you have your desired floor plan, we will design the exterior plan for your home.
Each design is custom to your needs and pricing will vary based on a number of factors. Because of this it can take longer in some cases to acquire exact pricing on your design.
To finalize the cost to build the insulated, lockable shell for your home structure, we suggest the following:
1. Choose an existing completed project that you like with minimal modifications as a starting point for your design.
2. Provide Morton Buildings with your desired floor plan and budget parameters so the exterior design aligns with your style and budget.
Working with Morton, and potentially your bank, your funds and payment schedule will be verified. Once this step is complete the contracts can be signed.
This process will vary based on your selected level of involvement. You will only sign one contract with Morton Buildings. However, you may also need to arrange contracts with a general contractor or specific subcontractors. Also, it’s important to note that any significant changes to your project after this point will require a change order and this can affect the schedule of your construction.
This is where your home begins coming to life. The construction process and timelines will vary greatly based on the complexity of your project and the current construction schedules.
Our relationship with you doesn’t end once we hand over the keys. At Morton, we are committed to your ongoing satisfaction. We’ll handle all Morton Buildings’ warranty claims in-house. Unlike others, our warranties include Morton materials and labor and last up to 50 years.
Dimensions: 36' x 10' x 50'
Potential Living Area: 1,800 sq. ft.
Our traditional home offering is a one-story, insulated, lockable shell and no interior finish work. When looking at the home structure, the price for our crew's part of the build generally ranges from $75 to $125 per square foot, plus any site prep... Depending on how you choose to finish the interior, we recommend budgeting another $75 to $150 per square foot, plus any additional costs for infrastructure development.
Morton crews build the insulated, lockable shell of your home. This example features:
» 10' wide finished back porch with molded aluminum ceiling soffits and column covers
» 8' wide finished front porch with molded aluminum ceiling soffits and column covers
» 1' finished overhangs with vented sidewall overhangs and continuous vented ridge
» Wainscoting and protective liner
» Gutters and downspouts on all sidewalls
» 4/12 roof pitch
» 8–vinyl double pane, Low-E glass windows
» 2 Steel entry doors with 9-lite windows on top half
» 6" thick blanket insulation (R-19) uncompressed on all exterior walls with 2" x 4" nailers spaced 16" OC ready for customer’s interior finish
» 7/16" OSB under roof steel with ceiling ready for customer’s interior finish
» .019 Hi-Rib™ steel on all sidewalls and roof with FLUOROFLEX® 1000 paint system
» Building wrap under Hi-Rib steel
» Fully erected on your prepared site with no overhead or underground obstructions*
» Full Morton warranty
Ranch Insulated House Shell with 2-Car Attached Garage
Dimensions: 36' x 10' x 45' & 30' x 30'
Potential Living Area: 1,600 sq. ft. with attached 900 sq. ft. garage
For instance, when looking at the building alone, a 2,000 square-foot ranch-style home with no attached garage would be approximately
Morton crews build the insulated, lockable shell of your home.
This example features:
» 8' wide finished front porch with molded aluminum ceiling soffits and column covers
» 1' finished overhangs with vented sidewall overhangs and continuous vented ridge
» Cultured Stone Wainscoting and protective liner
» Gutters and downspouts on all sidewalls
» 4/12 roof pitch
» 8–vinyl double pane, Low-E glass windows
» 2 Steel entry doors with 9-lite windows on top half
» 6" thick blanket insulation (R-19) uncompressed on all exterior walls with 2" x 4" nailers spaced 16" OC ready for customer’s interior finish
» 7/16" OSB under roof steel with ceiling ready for customer’s interior finish
» .019 Hi-Rib™ steel on all sidewalls and roof with FLUOROFLEX® 1000 paint system
» 2-Raynor LuxeVue residential garage doors
» Building wrap under Hi-Rib steel
» Fully erected on your prepared site with no overhead or underground obstructions*
» Full Morton warranty
$150,000 - $250,000 for the insulated shell only, and can run ad additional $150,000 - $300,000 for interior finishing. And then keep in mind any additional costs for land purchases, site preparation, infrastructure development, and specific build requirements based on you location. Sample Floor Plan
A 4/12 roof pitch is when the roof rises 4 inches for every 12 inches of horizontal run.
Morton’s roofs are designed for long-term good looks, and they’re available in a variety of colors and roof pitches. To enhance the style and function of your building, explore the many available options such as: a roof extension to create a wraparound porch, gable dormers for a traditional look, or a welcoming entry porch, to name a few.
In addition to Morton’s Hi-Rib™ steel roofing, you can also choose shingles or tiles for your building’s roof. These roofing options are a great way to achieve a custom look for your home.
From traditional, low-maintenance Hi-Rib™ steel in a variety of colors, to brick, HardiePlank® or HardiePanel® and cultured stone, you choose the siding that best fits your style or your building’s surroundings.
Wainscot is both a practical and aesthetically pleasing element to add to your building’s exterior. It allows for different color schemes and breaks the vertical lines of your building’s walls. Several options are available for wainscot including: Novabrik™, masonry, Hi-Rib steel and stone.
Overhangs work with functional cupolas to provide even more ventilation in your building.
Gutters and downspouts keep the sides of your building clean by directing water away from the building. They also reduce corrosion, erosion and condensation around your building. Our heavy-gauge aluminum gutters and galvanized steel downspouts are finished with FLUOROFLEX® 1000 paint in a variety of colors to match or accent your building.
Add natural lighting and improve the ventilation in your building by including windows. We offer a premium line of Pella® windows with double- and triple-pane glazing options.
Raised-panel or open-louvered 12" or 15" vinyl shutters enhance the beauty of your building and are available in a variety of attractive colors to match or accent your building.
Walk doors for your Morton home are a matter of personal preference. The material used and looks can vary greatly based on your budget. As a general rule, doors can range from a price as low as $500 all the way up to several thousand. Whether you’re looking for a basic steel door, or a high-end wood or fiberglass door, Morton has relationships with several manufacturers to ensure you get the right door for you at the right price.
Dormers and porches extend the character and functionality of your home. Porches can provide additional shelter and can also be a great place to sit back and relax. Various styles and sizes are available.
There are different options for adding a garage to your Morton Buildings home. Each style of garage connection has a different look and functions differently. If a detached garage better suits your needs, your sales consultant can quickly create a proposal for that as well.
That cost will increase based on the complexity of the attachment to your home and the features you choose to add to the garage.
With company-owned construction centers strategically located throughout the United States, there’s a Morton Buildings sales consultant nearby to serve you. Find your local Morton Buildings construction center at mortonbuildings.com/locations, for pricing information and to receive additional detailed information about our buildings.