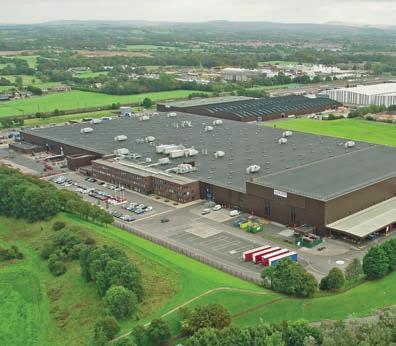
4 minute read
SPOTLIGHT: LEYLAND ASSEMBLY PLANT High-tech innovation is at the core of vehicle manufacturing at the historic Leyland assembly plant
CENTRE OF
EXCELLENCE
Advertisement
SPOTLIGHT : LEYLAND ASSEMBLY PLANT
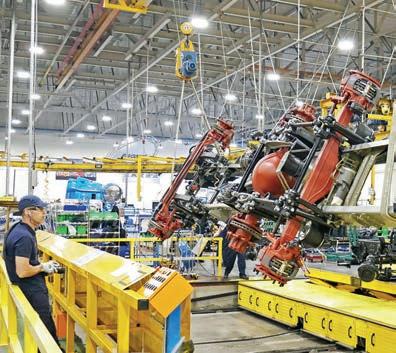
Leyland Trucks might be an historic name in vehicle manufacturing – but high-tech innovation is woven into its DNA
WORDS: RONNIE HITCHENS
Many commentators have lamented the demise of the British truck industry. But while many famous names have disappeared, in Lancashire at least, the heart of truck manufacturing in this country still beats strong.
Leyland Trucks still proudly carries the name of its home town, tracing its origins back to 1896 and counts fth generation employees on the payroll. This is no heritage business reliant on a nostalgic customer base to keep it aoat. Leyland Trucks today is a global leader in the automotive industry.
Almost one in every three trucks on UK roads is built at the Leyland Assembly Plant (LAP): a true UK automotive success story. And it’s been recognised too, most recently with the Queen’s Award for Enterprise. With the end of the Brexit transition period on the horizon, its location on this side of the Channel may make it even more critical to UK operators, ensuring the supply of vehicles and parts they need to keep the UK economy on the road.
STATE OF THE ART The LAP was heralded as a worldleading facility upon its opening in 1980. As part of Paccar since 1998, Leyland Trucks builds DAF vehicles for markets across the world. In fact, it is thought to be the only production facility to produce the entire range of trucks, of any one brand, on a single production line and under one roof. The single building, which covers 16 acres of an 86-acre site, houses the production facility, ofces and the Paccar Parts Distribution Centre (PDC).
Leyland has a proud history for sure, but the company now plays a vital role in developing new technologies. The team of engineers is responsible for the design and development of the entire LF series and specic CF models, and is playing a key role in the development of DAF zero-emissions solutions. Latest is the battery powered LF Electric, which was showcased in 2018 and is expected to commence eld trials shortly.
Continuous investment in the building, manufacturing processes, and, above all, the people, means that the LAP remains among the most advanced in the industry. Production boasts the world’s rst robotic truck chassis paint booth, with ‘dancing’ robots intricately choreographed to ensure every chassis variant receives precisely regulated paint coverage – it’s a sight to behold.
A 1,000-strong workforce has the latest state-of-the-art technology at its ngertips – literally; every chassis is accompanied on its journey from

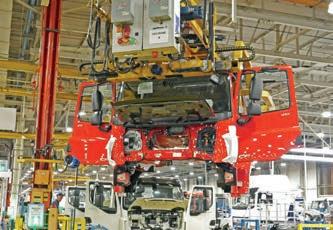


chassis-rail to completed vehicle with a set of electronic work instructions that identify every part and every task.
PEOPLE POWER The most essential components of the LAP are undoubtedly its people. Individuals are encouraged to put forth ideas on how to deliver quality and ef ciency improvements. The methodology works; LAP has picked up the Paccar ‘Chairman’s Award for Quality’ nine times in 17 years – a coveted title among the nine global Paccar production facilities that vie for the title. A team from LAP was hand-picked to advise on the build and commissioning of Paccar’s newest facility in Brazil in 2013.
MIX AND MATCH Vehicles produced at Leyland are many and varied. “It’s not unusual to see multi-wheelers nose-to-tail with LF lightweights and XF tractor units,” says operations director Peter Jukes. “In fact, we schedule it this way to balance the workload.
“Finished vehicles are destined for customers in the UK and around the world. All DAF LFs are produced here, together with the vast majority of righthand-drive CF and XF models. Last year, we built 19,500 trucks with 7,000 exported to 51 different countries – the balance of 12,500 vehicles going to UK operators.”
BODY BEAUTIFUL This same in-house capability extends to Paccar box and curtain-sided bodies that have been designed, manufactured and installed at the LAP since production started in 2007.
Each year, 1,000 Paccar-bodied LFs and CFs are produced. The 10,000th
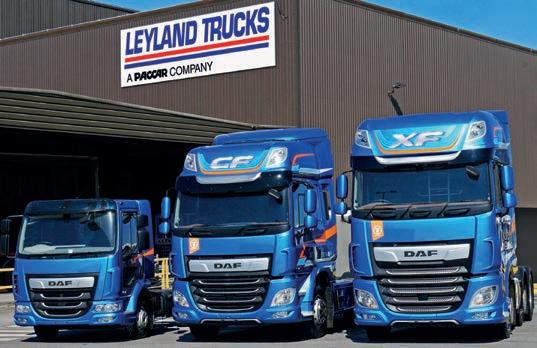
Paccar-bodied vehicle was only recently handed over, making Leyland one of the UK’s largest bodybuilders.
PARTS DISTRIBUTION CENTRE The Paccar PDC is located alongside the main production area and is supported by a second building for large and slow-moving items.
“Our parts team live and breathe rst-time pick rates,” says PDC manager Neale Handley, “Managed Dealer Inventory, or MDI, ensures 95% of our parts orders are available on the dealer’s shelf. If the dealer does not have the part, they can order from here up to 6pm, we’ll deliver overnight and it’s ready for the next morning. This takes availability to almost 99%.
“It’s impressive, especially when you consider there are over 200,000 parts lines including our TRP all-makes, trailer and consumables range.”