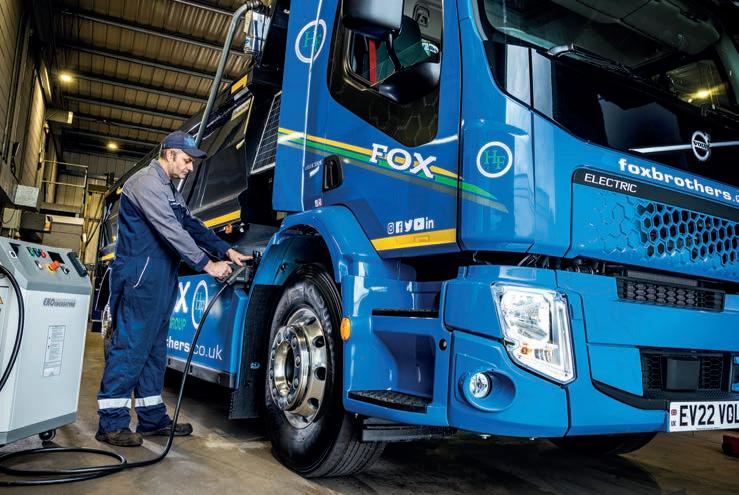
8 minute read
The cost of caring for electric trucks
facturer admits. That has implications for brake component wear.
Battery-electric powertrains may themselves need periodic attention, says Moon. The systems installed to monitor and control them may signal faults that have to be addressed, although there could be greater scope for over-the-air fixes – which do not require a workshop visit – with electric trucks than there are with diesels.
Advertisement
The heating and cooling systems installed to ensure that batteries are kept at an optimal temperature may go awry, and the batteries themselves could need an unscheduled intervention if individual cells start to fail.
“The batteries will deteriorate over the lifetime of the truck, with the possibility that cells will have to be replaced,” Moon says.
Comments a Volvo spokesman: “The parts that may need replacing will cost a lot more than oils and filters, which creates more risk for the manufacturer. Hence the lack of significant movement in R&M pricing.”
Warranty cover
Some of the major items that could require swapping are of course covered by the manufacturer’s warranty provided when the truck is new.
With fewer moving parts in an electric engine than a diesel, lower R&M costs might be expected. Unfortunately it isn’t that simple, as Steve Banner finds out
Hauliers planning to switch from diesel to electric trucks are doubtless expecting Repair & Maintenance (R&M) contract rates to come down with a bump.
With no need to drain engine lubricant or replace oil and air filters, and no emission control system to worry about, the cost of keeping a battery truck on the road will surely be cheaper than that of its diesel counterpart.
Apparently not. Suggestions that rates could be 30% to 40% lower for electric trucks are completely wide of the mark, says DAF marketing manager Phil Moon. “It’s more like 10% lower,” he observes.
Moon points out that electric trucks still have steering, brakes, tyres, wheels and suspension systems, and they all need attention from time to time. Like diesels, they are also subject to statutory safety inspections every few weeks to ensure O-licence compliance, he adds.
Scania points out that the regeneration systems fitted to electric trucks, which return energy into batteries that would otherwise be wasted, may help prolong brake life as the service brakes have to be used less frequently.
When they do need to be used, however, they will have to cope with more weight because of the burden imposed by the truck’s heavy battery pack, the manu-
HIGHER COST: Volvo says replacement parts for electric vehicles will be much more expensive than those for a diesel truck
DAF covers the batteries it fits for up to six years, with the assurance that at the end of the warranty period they will still give at least 70% of the performance delivered when they were factory fresh. The warranty can be optionally extended to eight years, says Moon.
Says Volvo: “We’re assuming batteries will be good for around eight years.”
The six-year battery warranty plus a three-year warranty on the rest of the vehicle means that the electric DAF LF 19-tonner recently purchased outright by haulier Campeys of Selby enjoys plenty of protection against expensive component failure, contends transport manager Harry Campey. The North Yorkshire company has taken it without an R&M contract, and Campey believes this approach makes sense.
NO CONTRACT: Harry Campey of Campeys of Selby is counting on manufacturer warranties providing enough cover to make an R&M contract unnecessary

“OK, we’re taking a bit of a punt, but we haven’t got a radiator or a timing chain to worry about, never mind engine oil and filters,” he says. “As for the battery pack, we intend to keep the truck for 10 years and we’ll change the pack after five years.
“By that stage batteries should be available that are the same size as today’s batteries but offer double the range the way technology is going.”
Campey has been influenced in his approach by his experience with his used electric Tesla car. “I’ve run it for 18 months and all I’ve had to do with it is put it through its MoT,” he says.
With an expected range between recharges of 150 miles, the truck was about to be delivered at the time of writing. It will be used on pallet work in and out of York.
Moon says that battery health will in part depend on the approach operators take to charging.
“Ideally the battery should be charged at between 20% and 80% of its capacity to remain healthy,” he says. “The charge level shouldn’t drop below 20% or get up to 100%.”
When making the comparison between internal combustion and electric technologies it should not be forgotten that the amount of maintenance a diesel truck requires has fallen significantly in recent years, Moon points out. “These days we’ve got oil drain intervals set at up to 200,000km,” he observes.
Extended contracts
Electric trucks still cost significantly more than their diesel equivalents, so it is not surprising that operators plan to keep them for longer. This trend is reflected in the duration of the R&M agreements they are looking for, says Moon.
“With diesels it’s typically anywhere from two to five or six years,” he comments. “With electric models, however, it’s five years plus.”
Scania’s UK executive services director James Colbourne suggests that electric truck R&M rates are likely to be on a par with diesel rates at present, and possibly slightly higher. “We’re being very cautious in this area,” he states.
While key components are proving to be reliable so far, he reports, it’s still early days. If they do fail then repair or replacement costs are likely to be steep, because the benefits of mass production and the way it which it drives down prices have yet to kick in.
“At the moment we’re talking about a different cost base,” he remarks.
Dealers Must Invest For The Zero Emissions Transition
The cost of retooling the dealer network and training technicians to work on electric trucks cannot be ignored, says Scania’s UK executive services director James Colbourne, and this has implications for R&M rates.
For some years into the future dealers will be working with two technologies – battery-electric and diesel – as well as having to cope with biogas and potentially hydrogen fuel cell models, and they will have to invest in equipment and employees accordingly.
“As things stand technicians who are capable of working on electric vehicles are at a premium,” Colbourne comments. Diesel trucks will clearly be around for some years to come, but as their numbers decline technicians who can work on them may be at a premium instead.
“They will become the specialists,” he remarks.
One saving hauliers who switch to electric trucks may enjoy is a reduction in minor damage, suggests Andrew Scott, UK head of electric mobility and product development at Renault Trucks.
“From what we’ve seen, drivers of electric vehicles are always conscious of their remaining range and the need to preserve it, so they drive more carefully,” he comments. “As yet we’ve not got any data to prove that this is the case; but I think that’s a reasonable statement to make.”
The caution Scania is adopting is illustrated by its unwillingness to warrant the batteries it installs. “We’re covering them under our R&M contracts instead,” Colbourne says, an approach which clearly keeps R&M rates higher than they might otherwise be.
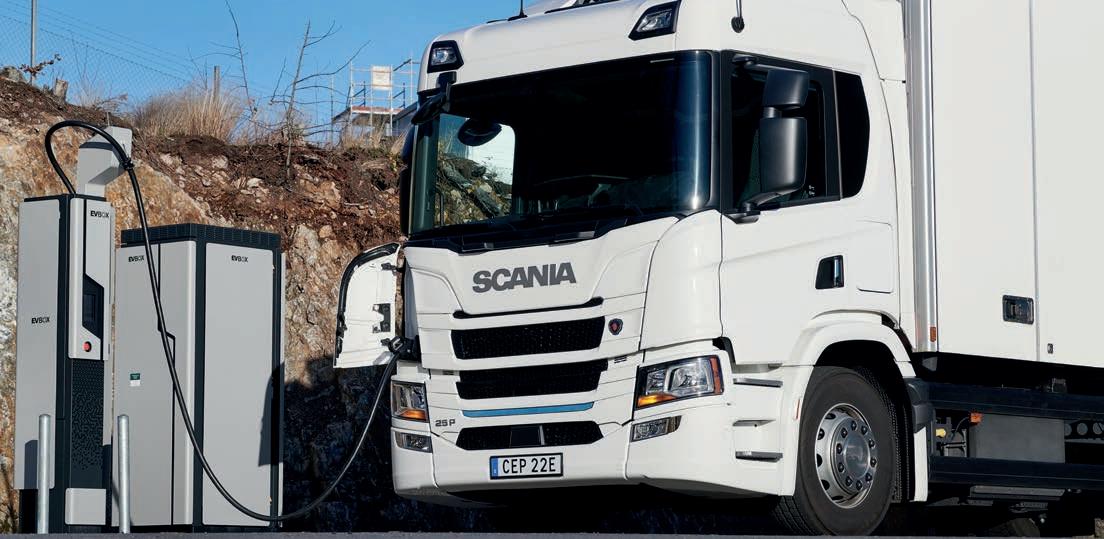
It is a stance that looks set to change as battery packs produced by Scania in-house become more readily available. The company has set up a battery pack assembly plant next to its worldwide headquarters at Sodertalje in Sweden, which will become fully operational this year.
CAUTIOUS APPROACH: Scania is not yet offering warranties on its batteries, but is covering them under R&M contracts
The good news is that rates should decline over the next few years as manufacturers learn more about the reliability of components and their maintenance requirements, he adds.
This is already happening in the car market, he points out, citing evidence from Scania’s car manufacturing sister brand Audi. Both Scania and Audi are part of the Volkswagen Group.
Any dramatic savings cited from mainland European sources so far as electric trucks are concerned need to be treated with a pinch of salt, Colbourne suggests.
As was pointed out earlier, the UK has regular statutory safety inspections of both electric and diesel trucks. They come at a cost, may trigger immediate rectification work and affect service and repair rates, regardless of the vehicle’s power source.
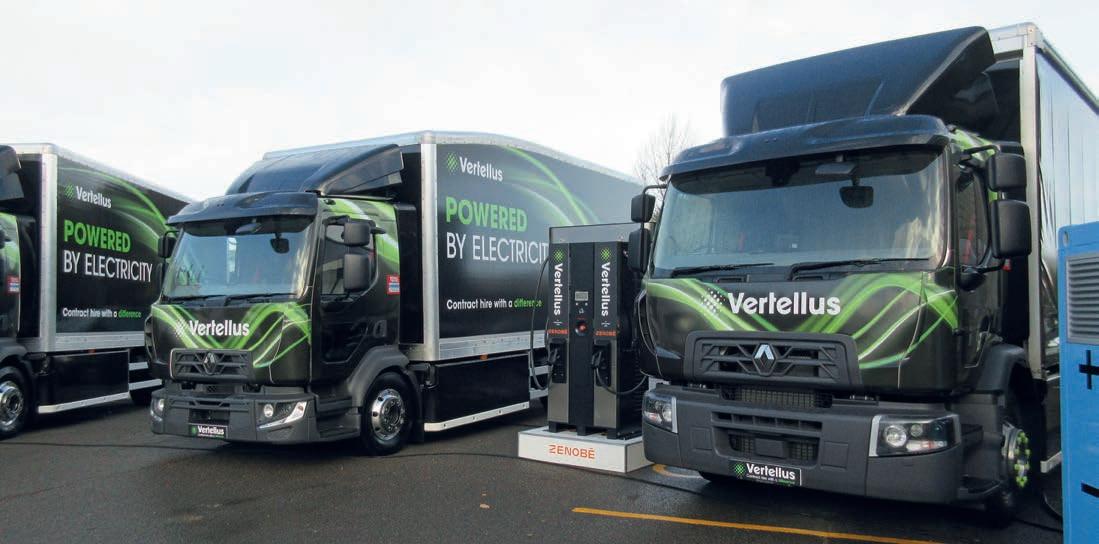
No such safety regime is in force on the other side of the Channel.
The caution Colbourne refers to, and the potential future decline in maintenance costs, is evidenced by Scania’s current approach to dealing with battery defects and the way it will change in the coming months.
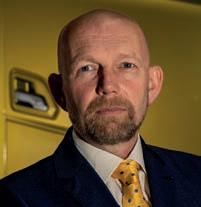
At present faulty battery cells go back to the manufacturer, but from early- to mid-2024 they will be repaired locally where possible and practical, he explains, which suggests a reduction in costs.
Scania initially plans to set up two or three battery repair centres of excellence in the UK. Repair support is likely to increase in three or four years’ time as the number of electric trucks in service steadily rises.
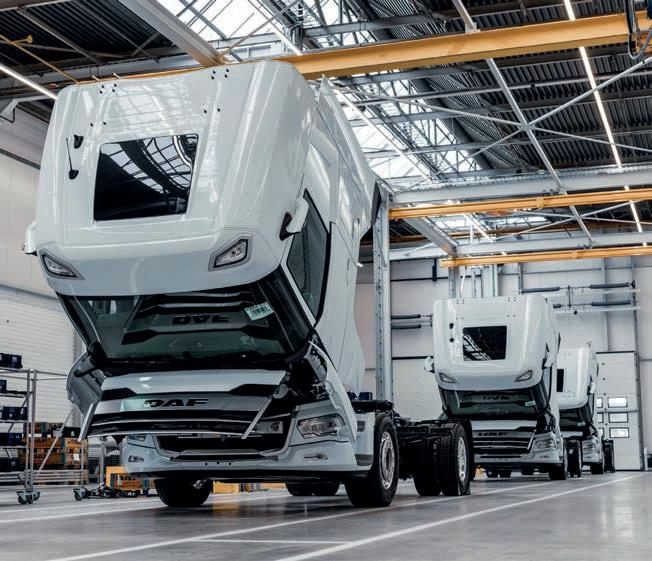
Repairing traction batteries is a skilled activity and, like any work on a high voltage electric truck, brings serious potential hazards if safety procedures are not followed to the letter. Some, though by no means all, existing workshop tasks involving electric trucks may require two technicians to be present – one doing the work, while another stands ready to step in if there is a problem.
“The idea that a technician will have to jump in with a hook on an insulated pole to pull a workmate away from danger in the event of an electric shock sometime causes amusement, but it’s really not that funny,” says one industry insider. “A shock if you accidentally chop through a live high-voltage cable is likely to cause serious injury and may prove fatal.”
If two technicians have to attend, then the wage bill doubles, and the time taken to check and double-check all the safety measures bumps up the invoice the customer finally receives.
“Everything has to be checked and verified in line with a fixed protocol,” the insider remarks. “You cannot and must not deviate from it.”
Beyond the batteries
Scania cites further instances of components that still have to be maintained no matter how a truck is powered; evidence that a complete transition from diesel technology to a truly all-electric vehicle still has some way to go so far as legacy manufacturers are concerned. Says UK technical engineering manager Steve Oakley: “Our electric trucks have still got an air compressor which has to be serviced every 12 months.”
A conventional drive axle continues to be installed, he points out, along with a two-speed gearbox which is married to the electric motor with oil required for lubrication and cooling. Transmission lubricants enjoy a long life, but do not last for ever.
Electric rear axles should make a difference but are not yet widely available. Volvo’s e-axle is unlikely to appear until 2025 or 2026.
Coolant is required for the battery pack too – indeed there may be as much as 100 to 200 litres of coolant on the entire truck – and it may need replenishing or changing from time to time.
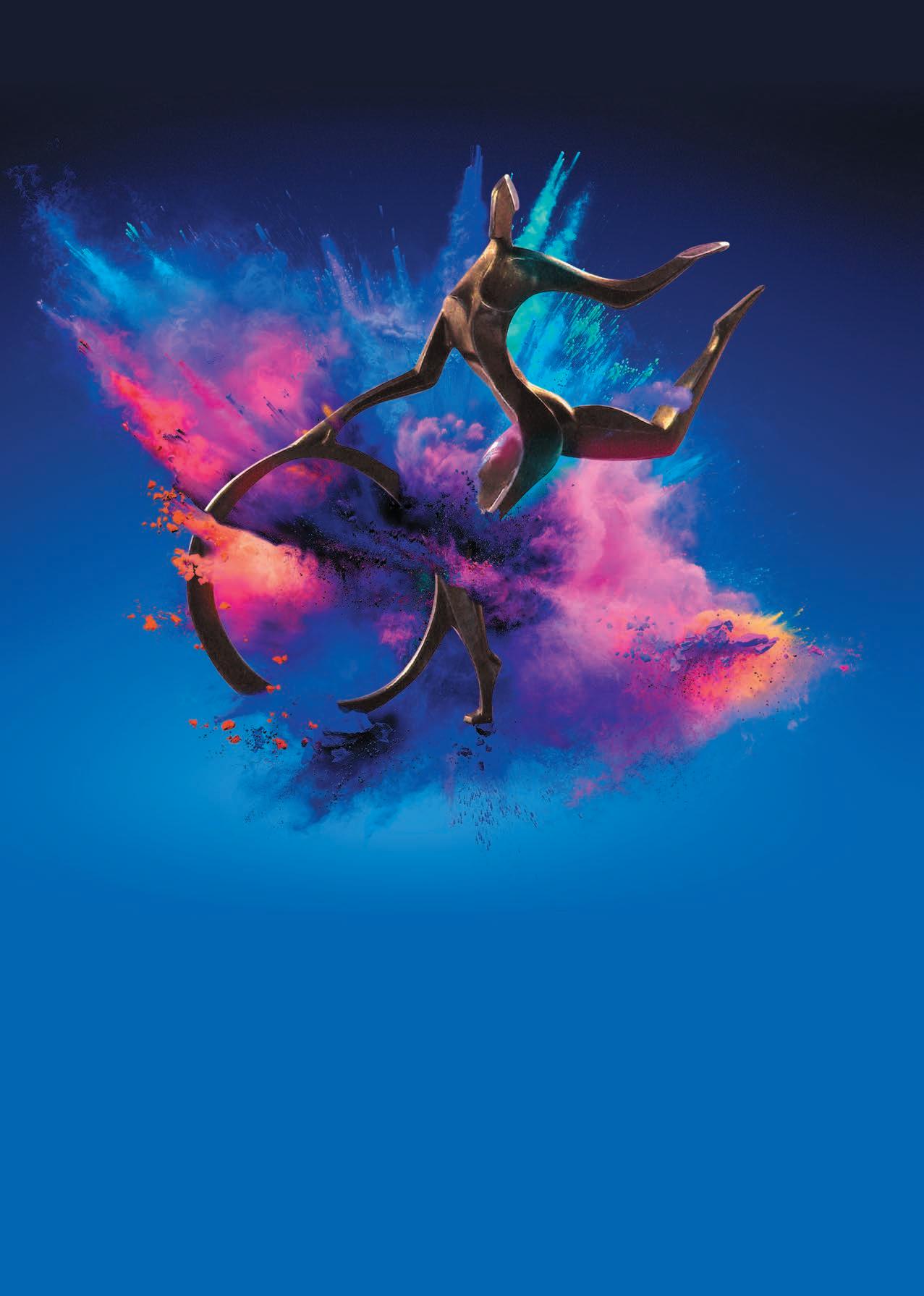
Haarjeev Kandhari acquired tyre retreader
Vaculug in 2018, and has invested heavily since. He tells Steve Hobson why doing the right thing is more than a matter of good business sense