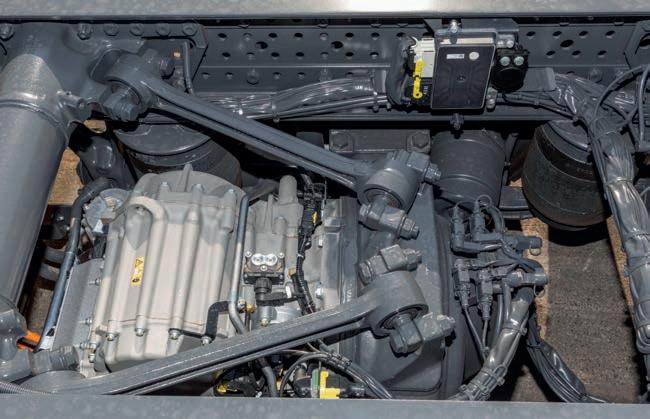
8 minute read
No time to waste
RCVs may seem a natural fit for electric power, but how simple is it to make the switch from diesel?
John Kendall gets the lowdown from industry experts
Advertisement
Who will go first? By that we mean which transport sector is likely to be the early adopter of electric power? With battery technology improving fairly rapidly, it becomes more feasible for sectors to make the switch, when the two “Cs” of cost and convenience eventually align.
On the face of it, the waste and recycling sector looks as though it could be a likely candidate here. Vehicles tend not to stray too far from base each day and return to the depot each night. Overnight charging at the depot looks as though it could satisfy many fleets, without the need to recharge during the day. Is that the whole story though?
Veolia will celebrate 30 years of involvement in waste collection services this year. The company is already operating fleets of electric vehicles involved in waste and recycling collection, following the introduction of electric refuse collection vehicles (RCVs) and others over the past year for Westminster City Council and Kingston Council.
“Over three-quarters of local authorities have declared climate emergencies and many are targeting net zero by 2030, so there is real impetus to transition to zero emission operations”, Gary Clark, Veolia’s UK fleet director told Motor Transport. “By 2030, we expect at least 10% of our fleet to be powered by electricity or alternative zero emission technologies. In 2030, we will also stop buying fossil-fuel-powered RCVs and by 2040 our fleet will be fully decarbonised.”
That’s a clear commitment from one of the largest suppliers of waste services in the UK. How does the picture look from a vehicle manufacturer’s perspective?
“We are seeing strong demand from virtually all our customers,” says Ross Paterson, head of special trucks at Mercedes-Benz Trucks UK. “They all want to do the right thing for the right reasons, but of course the vehicle itself is only part of the jigsaw. The charging infrastructure is obviously critical for the success of these vehicles and there’s lots of interest out there and lots of people talking.
“We are actively engaging with them, offering a consultation not only about the vehicle itself but also the charging infrastructure and route analysis, to see how it may or may not work for them. But one of the overriding things that I’m hearing at the moment is virtually all customers that we’re talking to are looking at e-trucks, particularly RCVs, but they’re asking the question or at least they’re of the mindset, ‘will it do the same as my current diesel truck does?’ So, will it go out in the morn- ing, do the full rounds, also go and unload somewhere else and get back to base on a single charge?”
Amy Carter, EV operations manager at DAF Trucks UK, points to some of the engineering challenges that electric RCVs present. “It’s a complicated build, of course, as it has always been with a PTO and significant power required for the compactors etc, so absolutely it does create some engineering challenges around electrification, particularly around range,” she says. “Having said that, I think local councils are very committed to reducing noise pollution in urban areas for example, as well as moving towards a carbon-zero future, so there is definitely an appetite for the vehicles.”
Gradual transition
Ulemco is a technology provider, offering a dual-fuel system mixing hydrogen with diesel and helping to reduce emissions from diesel engines. MD Amanda Lyne expects we will see a gradual transition to electric and zero-carbon vehicles over the next five to 10
Dennis Eagle Soars Ahead With Evs
Dennis Eagle was an early adopter of battery electric power for its RCVs and has won some significant orders as a result. It launched its eCollect early in 2021 – there are now over 100 in operation and the orderbook continues to grow.
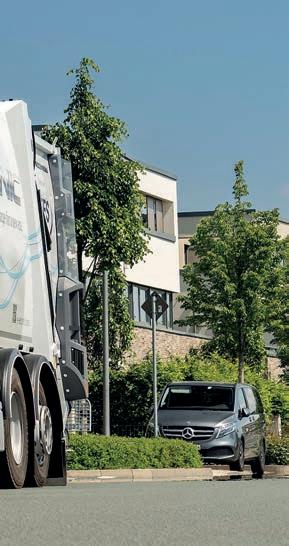
Some operators, such as Nottingham City Council, already had smaller EVs so they had charging infrastructure in place and were comfortable with this new technology. “They placed early orders and were able to hit the ground running,” the company says. “For others, there was an initial lag period. They were just as enthusiastic after trialling the vehicle but had to start from scratch with the infrastructure.”
The eCollect runs entirely on electrical power from the vehicle battery packs. On a full charge, they work all day – typically collecting over 20 tonnes and travelling 60 to 80 miles – during which the battery charge falls from 100% to between 20% and 40%. Everything, from the vehicle’s drive system to the compactor, bin lifts and air conditioning, runs on electricity from the battery packs.

Westminster has recently ordered 40 eCollects, the delivery of which will coincide with the opening of a new depot where they will be charged by power from the South East London Combined Heat and Power facility (SELCHP). This plant generates power by incinerating waste – some of which will be transported there from Westminster by the eCollects.
“It’s a beautiful example of the circular economy and local authorities are increasingly focused on sustainability,” says Dennis Eagle. “Other operators are planning a slower, more measured transition and may still be buying new diesel RCVs up to the deadline.”
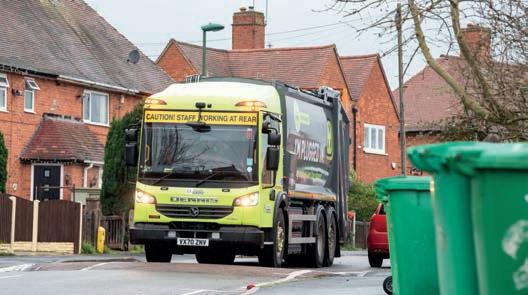

HYDROGEN: COMBUSTION OR FUEL-CELL?
Electricity can be stored in other ways than by using heavy and expensive batteries. One such method is to use a fuel cell, which can either generate electricity from hydrogen or produce hydrogen from electricity. The problem is that it is not particularly efficient at the moment and like batteries, fuel cells are expensive. The advantage for long-distance vehicles in particular is that the technology offers rapid refuelling in a similar time to that needed to fill a diesel tank.
RCVs are fairly power hungry, so could hydrogen fuel cells be an attractive alternative? Ulemco is looking at another option, which could yet become an alternative for commercial vehicles. Hydrogen is a combustible fuel, but since it’s not a hydrocarbon fuel, it can be zero-carbon if produced from renewable sources.
“There is significant interest in hydrogen-fuelled vehicles, as these offer solutions to the concerns such as better productivity (fast refuelling), and a more flexible match to existing operational processes, rather than specifically for either technology”, says Amanda Lyne, MD of Ulemco. “We think this is because many vehicle owners are not convinced that battery solutions alone will meet their needs.
“Customers ask us about all hydrogen options, including our dual-fuel approach, which they see as a practical option in the short to medium term for delivering carbon savings. We tell them that there are a few examples of fuel cell versions that can be trialled today, but they are quite expensive.”
“I think there’s a lot of interest in hydrogen per se, but fuel cells are a challenge because they are such a complex build in the first place and because they are technically a hybrid,” says Amy Carter, EV operations manager at DAF Trucks UK. “As well as having the fuel cell and hydrogen tanks, you also need a storage battery. On its own it isn’t adequate. So, for a vehicle that uses a lot of power, like a bin lorry for example, that’s going to need a fairly significant energy storage facility as well as a relatively significant fuel cell, and that creates a challenge for manufacturers.” years. “Some cities and municipalities will move faster than others, depending on their specific circumstances and access to finance,” she suggests. “It is still not clear that the versions seen today will technically deliver everything that is required of an RCV fleet – including breadth of duty cycle coverage (can they cover all the routes and duties that are needed in all locations and applications?), reliability, life-time durability and overall affordability.”
Lyne highlights the massive investment that will be needed in charging infrastructure too, a factor that is likely to be receiving close scrutiny from cash-strapped local authorities.
“The product is here now, with its breadth of capabilities increasing at a fast pace, meaning more and more operations can be accommodated,” says Martin Tomlinson, head of media and truck demonstration at Volvo Trucks UK and Ireland. “The adoption rate will be dependent on many factors including energy pricing (fossil and electric), societal demand, national and local legislation as well as infrastructure development, to mention some of the key influencing factors,” he argues.
Meeting power demands
RCVs tend to be power hungry because of the energy needed by the compactor, which compresses the waste to minimise the number of times the vehicle has to tip. Operators are used to completing their collection rounds, unloading when necessary, then returning to the depot. Will that still be possible without having to recharge or rely on an auxiliary power system to replace the PTO to drive the compactor?
“All of Veolia’s electric refuse collection vehicles have a PTO that is powered solely by electricity,” explains Clark. “They have enough power to fulfil a standard refuse round. Powering ancillaries directly from electricity leads to increased efficiency gains.” This is because the energy does not need to be converted; instead it comes straight from the battery as electricity to drive the compactor.
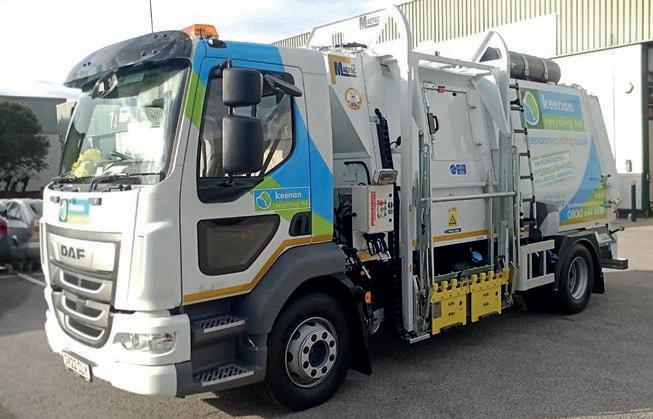
“The e-Econic has got an e-PTO as standard,” says Paterson. “The bodywork that would be fitted on an e-Econic will run off the chassis’ batteries. We’re not looking at external fossil fuel-driven powerplants on the body or anything like that.
“We predict at the moment that the power that’s available will be suitable for at least 90% of the current refuse collection vehicles that are in operation across the country. There will always be the exceptions, but again I come back to our consultation.
“How many bins are you lifting every day? What’s the average weight of the bins? What’s the mileage of the vehicle? Where do you actually empty the RCV? How far do you have to drive to empty it? All are hugely critical factors in the test to ensure the vehicle is specified properly for the customer.”
DAF offers its electric 26-tonne GVW FAN chassis with up to five battery packs, which would provide a total of 525kWh of power capacity on the truck. “When you consider that the average bin round for a council is less than 50 miles, we’ve got over 400km to 500km range on that truck”, says Carter. “There should be plenty of power to operate that compactor through the entire route. It’s a challenge, of course, because it adds extra weight to the chassis.”
Tomlinson has a similar view. “The devil is in the detail,” he says. “Some routes can be accommodated by BEV, some cannot at present. We will work with customers to achieve their goals; however, our preference is to power the superstructure/onboard equipment via batteries. The feasibility of our chassis to complete a particular route is completed using a piece of analysis software, which removes the guesswork from the process.”
Countdown to zero carbon
There are still 11 years to go before all new 26-tonne GVW chassis will need to be fitted with a drivetrain that does not produce carbon emissions. A lot will happen in that time. This will most likely include battery prices reducing further, an electrical infrastructure that is better suited to vehicle charging and more clarity on the role that hydrogen will play as a potential energy medium.
■ To find out more about the latest RCV technology, why not register for your free ticket at this year’s Road Transport Expo –roadtransportexpo.co.uk – and come and talk to key manufacturers about your business needs
The speed with which change will take place will be determined partly by the running costs of BEVs compared with diesel-powered vehicles. If battery prices continue to fall it could hasten the point at which the whole-life costs of a BEV fall below the whole-life costs of an internal combustion engine vehicle. “A diesel RCV consumes an enormous amount of energy and doesn’t travel very far every day,” Paterson points out. “So many variables play a part in that, of course, but from my perspective it is the ideal scenario for the total cost to be comparable with a diesel.”
For Lyne, hydrogen combustion looks like an attractive option. “When comparing with diesel, from a capital cost perspective, we believe that hydrogen combustion will have a greater chance of being cost comparable than fuel cell or electric,” she says.
“When we consider the running cost of the vehicle over a five- to 10-year period, that’s when we really start to see that move towards parity,” reckons Carter. “I expect within the next five to six years to see parity with diesels, not just in the municipal sector, but across the board.” ■
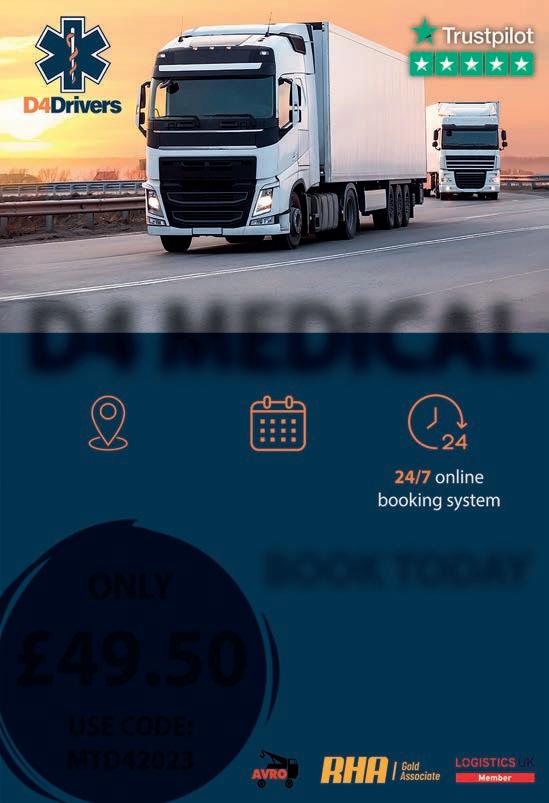

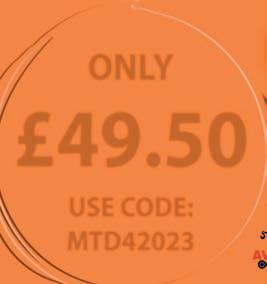
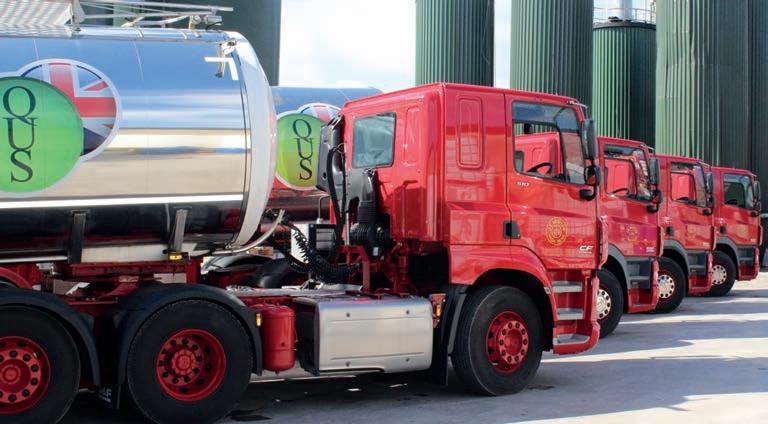
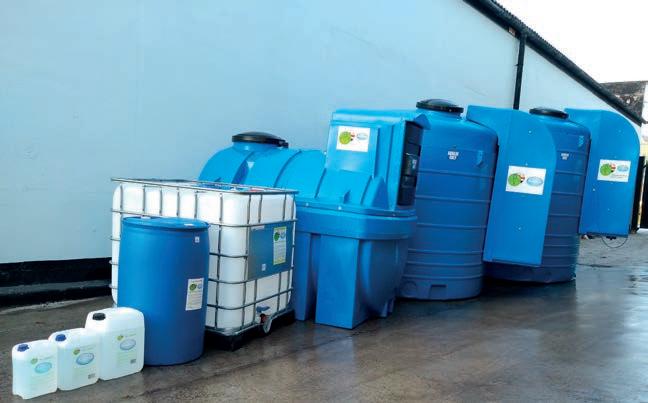
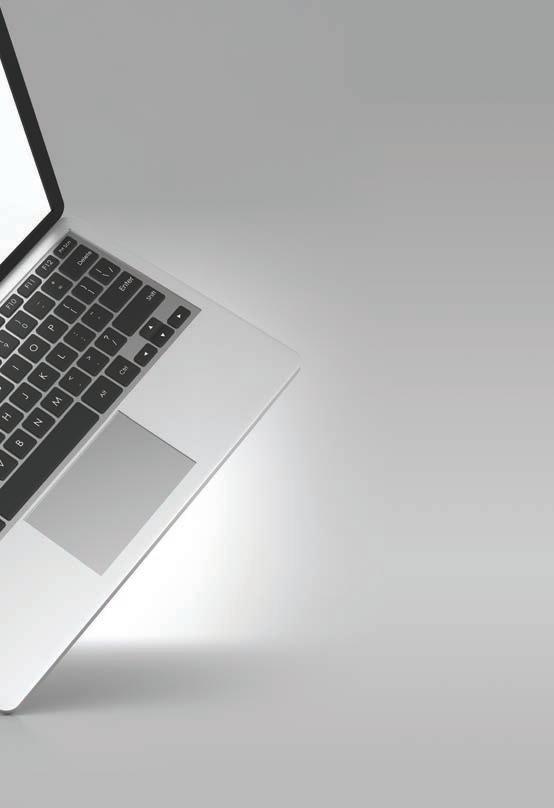