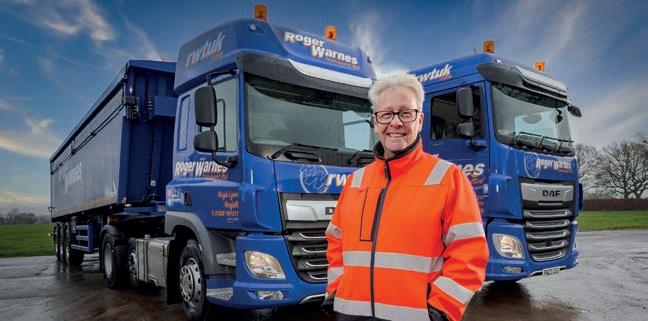
5 minute read
Tipping point
It’s not so long since tipping trailers were falling out of favour. Perhaps that’s a poor choice of words, since tipping trailer stability was one of the issues at stake. Apart from stability, the risk of touching overhead power lines and other obstructions was also contributing towards their decline in popularity.
Is the tide now turning? The replacements for tipping trailers were moving floor trailers and belt trailers –arguably a variation on the moving floor theme. Both designs could overcome the tipping trailer stability issue by doing away with tipping and using mechanical means to discharge the load, but there are also limitations on the uses of moving floor and belt trailers.
Advertisement
For bulk trailers, there are effectively three main areas of activity: construction, waste and agriculture. The UK economy has recently managed to avoid dropping into recession, but it has been ravaged by Brexit, Covid-19, former Chancellor Kwasi Kwarteng MP’s disastrous budget, the invasion of Ukraine, interest rate rises, inflation and rising costs. The economy has the jitters and when that happens, the construction sector is often the first to slow.
“The overall market is very buoyant,” says Ian Barclay, operations director of King’s Lynn-based Roger Warnes Transport, “although it does experience seasonal variations, tracking the agricultural and construction trends.”
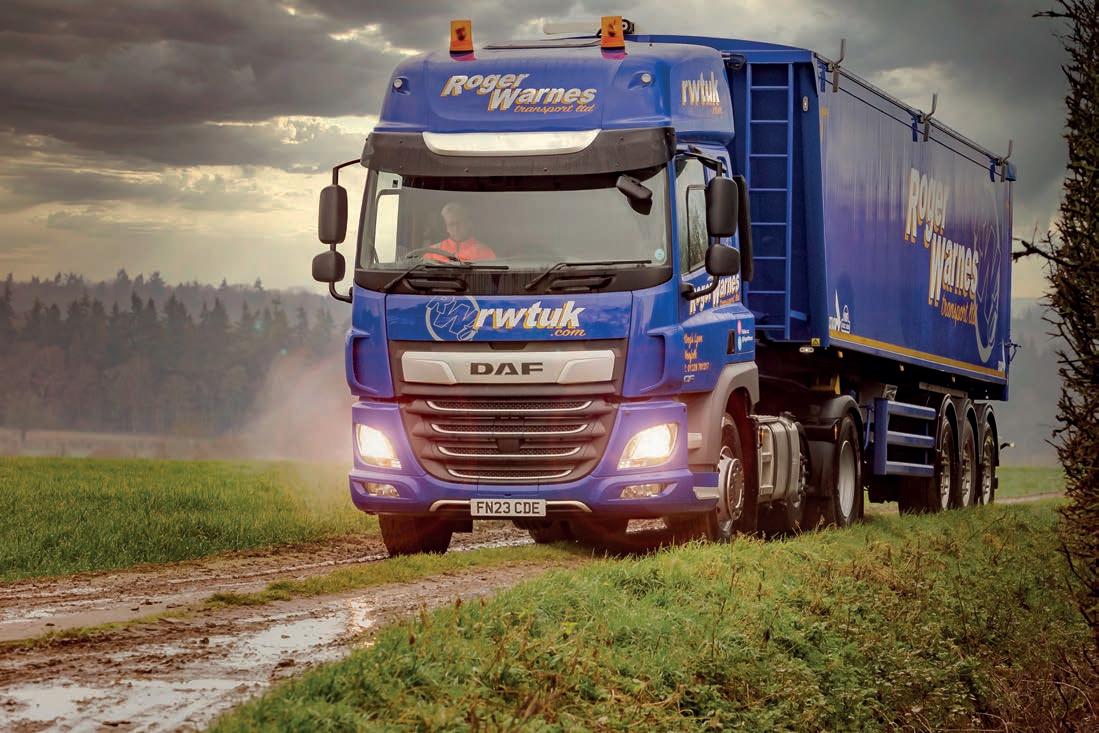
Barclay’s optimism is shared by Nigel Butler, MD of Weightlifter Bodies. “I’d say it’s pretty healthy. We saw a quiet period on enquiries in Q4 last year, but in Q1 this year it definitely picked up, we’re seeing more enquiries,” he says. “I think the balance of enquiries has shifted. The middle of last year was all about aggregate half-pipe tippers – that’s where all the demand seemed to be.
“That seems to have switched over the winter period. The construction market is a bit quieter while the agriculture market has bounced back. We would expect to be a bit busier on bulkers at this time of year anyway, because you’ve got harvest coming up from September onwards, so most of our enquiries have been around bulkers rather than half barrels.”
Graham MacMillan, UK MD of moving floor and tipper trailer manufacturer STAS, has had a different experience. He has seen the new bulk trailer market reduce quite a lot. “We’ve had a reduced amount of people asking for trailers and we’ve got a reduced amount of people actually ordering,” he says. “That’s down to many different things including uncertainty, volatility in the market, interest rates going up and people thinking prices are going to come down. People are being very careful and they don’t know what to do for the best.
“People aren’t building houses, so the stone and sand side is reduced. The aggregate side has slowed down. The grain side and agriculture hasn’t slowed down, but it somehow doesn’t seem as buoyant. People are holding onto their kit longer. Trucks run longer, trailers run longer, so you can sweat that asset more nowadays. People are using their original products for longer and deciding to repair them a bit more, rather than just selling it and buying new.”
Inherent stability was the big attraction for moving floor and belt trailers. “From a health and safety point of view it ticks all the boxes,” says Butler at Weightlifter. The problems appear to be on several fronts, though; cost principally, as Butler explains.
“I think what they quickly ran into, or what they certainly found when they got a couple of years into it, was that the capital costs were significantly more expensive and that doesn’t seem to have fallen as more volumes became available,” he says.
“The economies of scale don’t seem to be there and they’ve proved to be quite expensive to run. They need a lot of maintenance, so I think then there was a general move towards belt-type trailers, where there are fewer moving parts.
“They’ve proved to all intents and purposes to be equally as expensive, both to purchase and to run. That market just doesn’t seem to have any traction.”
More weight
You might think that as a manufacturer of tipping trailers, he would say that, wouldn’t he? STAS produces both tippers and moving floors, so MacMillan has a good understanding of both trailer types. “The reason the moving floor lost its way is because the trailer weighs about 2 to 3 tonnes more than a tipper. So, you’re carrying 2 tonnes less payload. It’s roughly £30,000 more expensive than a tipper, so you’re carrying less and it’s costing you more but also it wears out three times quicker.”
MacMillan makes this calculation because of the way the moving floor mechanism works and the way that the load passes over the various sections of it. He reckons new bearings are needed every three to six years, depending on the trailer’s working cycle and if that is neglected, the underfloor section will also need repairing.
Moving floor trailers are also not suitable for every type of load. “You can only do sand, stone, gravel and tarmac, but if you have a tipper, even an aggregate tipper, you can do glass, sand, salt and all these other things,” says MacMillan.
Barclay agrees up to a point. “For general or multipurpose moving floor trailers, it’s quite possible to offer a haulage service for everything from pallets, that would normally go on a curtainsider, through to some aggregates,” he says. “They are best suited to certain products such as wood chip, compost and other similar materials.
“Finding the perfect material to fill every mile is very challenging and, of course, they are a high capital and maintenance cost. Securing the correct level of ➜ 18
STANDING FIRM: SAFE TRAILER UNLOADING
“To be honest, 99% of tippers go over because of one reason – the driver,” says STAS UK MD Graham MacMillan. “If you get a bad driver, he will turn it over on the first load. If you get a good driver, who loads his trailer properly, that trailer will not go over, because the 1% that go over are to do with metal fatigue, poor loading or something breaking.
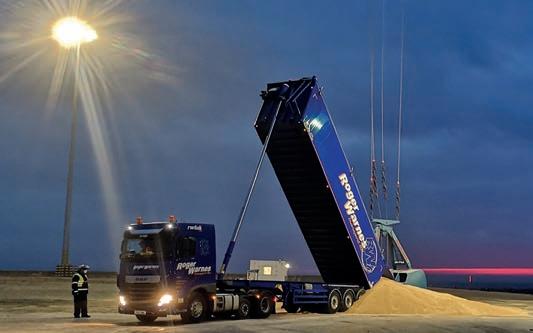
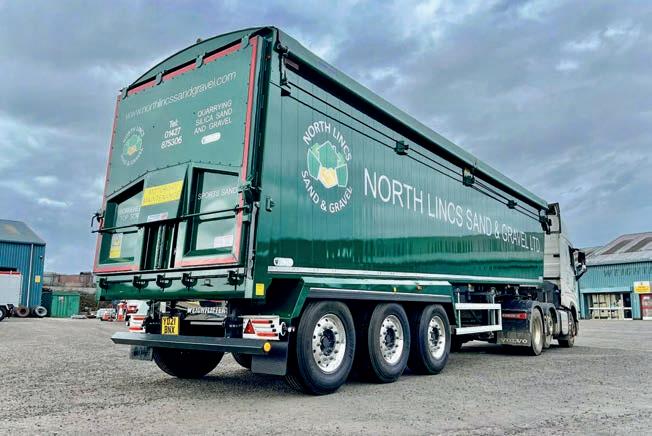
“Fatigue affects trailers that are probably over 10 years old. The reason they suffer fatigue is because steel normally rusts, or if the floor wears away that weakens the monocoque construction, so that’s where it then splits.
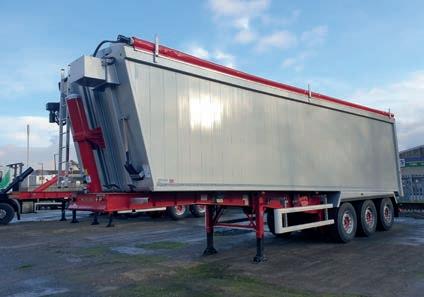
“If you put all the load on one side and you tip it up it will go over. It’s physics. But if you load it with most of the weight in the back of the trailer and then you put another dollop where the landing legs are – you don’t put anything at the front – then when you tip up, the actual weight of the pivot point is at the back. It’s trying to tip itself for you. So by doing that you’ve got more weight at the back, which gives more stability on the back end. When you’ve got weight at the front, that causes the front to rock.
“With tar, when you’re going down the road, you’ve got cold air to the front of the trailer. You should never fill the load at the front, because you get cold air hitting hot product, which will cool the
THREE AMIGOS: The bulk trailer market generally covers three sectors –agriculture, waste and construction – which all tend to be affected by economic concerns and seasonality. With a renewed eye on costs, many operators are looking at the increased payloads and greater longevity of tippers over moving floor and belt trailers tarmac and cause it to set. My advice for tar is to get a trailer that’s longer than you need. Say, a 9m trailer instead of an 8m trailer and load it with nothing in the front corners. So when you tip, it’s not cold in the front, it will come out. By doing that you’re making it safer.”
