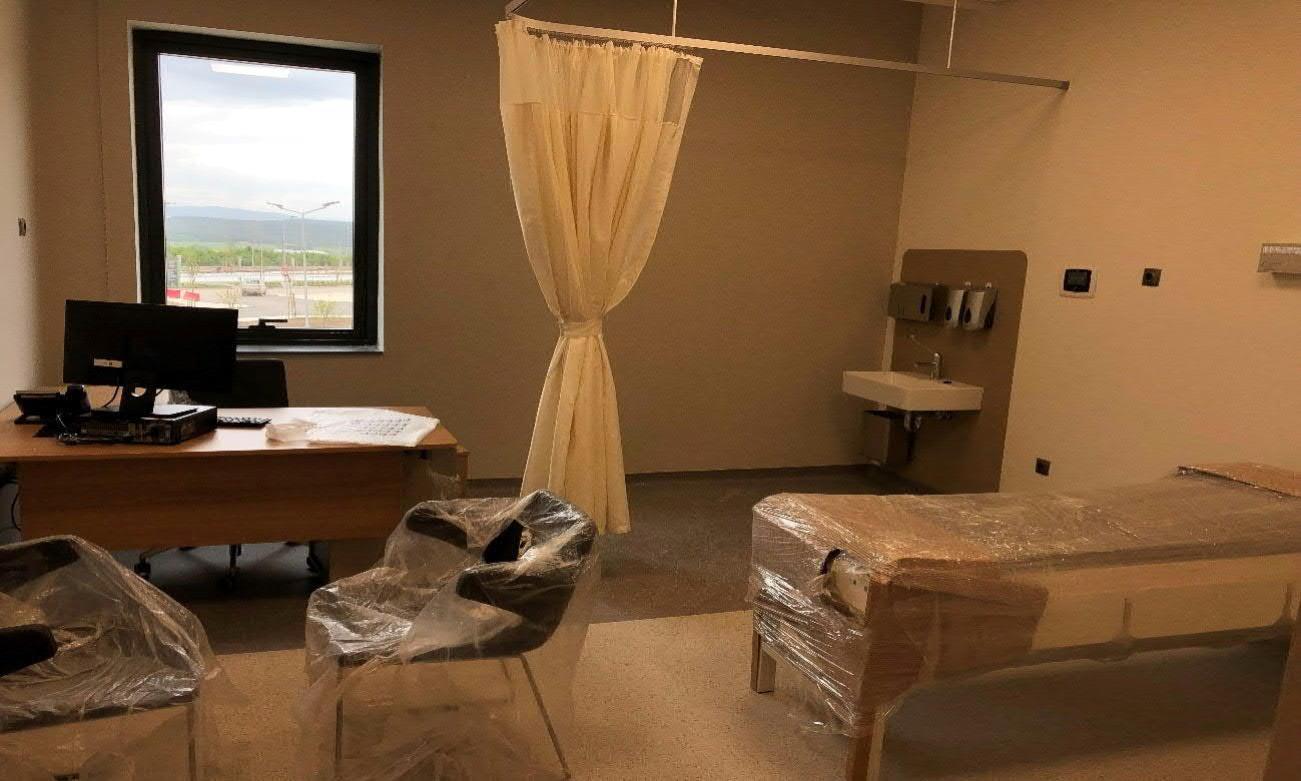
9 minute read
2 Operation Stage AMR Prevention Measures
After the construction phase, the healthcare buildings will be occupied by the healthcare personnel to provide health services and by Facility Management personnel to provide Hard and Soft FM services.
Typically a service agreement will be signed with the Facility Management (FM) Company. The counterpart of this agreement will vary depending on the Healthcare contracting model (PPP, Public, private). The service agreement will detail the scope of the work undertaken by the FM company. It is important to have adequate provisions in regard to Antimicrobial resistance in the service agreement as the FM Company staff would typically be involved from MEP equipment maintenance/ replacement to Soft FM services such cleaning, disinfection, waste, etc. The Service agreement should contain specific requirements or KPIs in regard to AMR or antibiotic stewardship.
Advertisement
Environmental and Social Action Plans (ESAP) and Environmental Social Managements Systems (ESMS) might be available in some projects where such plan and systems is annexed to the Service Agreement. Provisions in regard to AMR could be introduced to the ESAP.
It is also important to have an Infection Control Committee (ICC) established in the healthcare building to control and monitor the work, trainings and activities provided by the FM company staff and the Administration staff during the Operation phase.
To minimise the risk of infection in the hospitals, it is acknowledged that there needs to be systems in place to manage and monitor the prevention and control of infection during the operation phase. These systems may use risk assessments which consider the susceptibility of service users as well as any risks that both their environment and other users may pose to them.
It is recommended that the risk assessments, management and monitoring of the systems should be carried out by both the Healthcare personnel and by Facility management. Contractually, it is not usual to assign performance parameters to healthcare personnel such as doctors, nurses and administration personnel. However, performance parameters can be put on the facility management personnel to address AMR.
The Table below shows some requirements that could be required from the Facility Management Service staff.
Table 2: Recommendations (KPI) for Operations Phase No Subject KPI 1 Maintenance frequency of Ventilation system components. Facility Management Company would be usually responsible to keep Air vents, grilles and other ventilation outlets unblocked and keep it free of dust, grit, soil, film, cobwebs, scuffs and any other marks. A schedule/frequency for cleaning or maintenance associated with the requirement should be introduced. This is typically carried out on a annual basis. 2 Maintenance frequency of HEPA filters. Filtration performance may affect Indoor Air Quality (IAQ) in several ways. Poorly maintained filters with inadequate seals and breaches in the filter media promote the passage of contaminants into occupied spaces. This seriously affects IAQ in critical areas where clean environments are needed. Severely occluded particulate filters increase the resistance of airflow through the filters, affecting air
No Subject KPI supply rates. When filters are not changed according to the manufacturer’s instructions, the performance of the HVAC system is compromised. HEPA filters are designed to filter 99.97 percent of particles with a diameter of 0.3 microns. When HEPA filters are not properly maintained and tested regularly in biological safety cabinets, there is risk of contamination of the product within the unit or release of airborne pathogens into the occupied environments. A schedule/frequency for cleaning or maintenance associated with the requirement should be introduced. This is typically carried out on semi-annual basis. The HEPA filter maintenance should be scheduled and not reactive. 3 Maintenance of alcohol-based hand rubs at point of care. Periodical control of the disinfection stations should be carried out by the Facility Management Staff and the responsibility of the refilling should be defined and monitored. The responsibility should be defined in the service agreement made with the Facility Management company. 4 Using videos and posters to raise AMR awareness Showing patients videos on hand hygiene at the time of their admission could dramatically increase patients asking hospital employees to wash their hands and hospital employees complying with their requests. This responsibility should be defined in the service agreement made with the Facility Management company. Please see Figure 2.1. 5 Promoting hand hygiene in the workplace Hand hygiene is one of the keys to reducing healthcare acquired infections. Banners and flyers on the walls of the hospitals to remind the importance of hand washing for the prevention of multi-drug resistant infections and also to improve awareness and understanding of antimicrobial resistance could be introduced. Also, within the scope of encouraging practices; sending warning messages via information systems, rewarding successful employees, organizing special events with the staff to discuss about hygiene materials used, the problems they have and to have their suggestions. This requirement should be defined in the service agreement made with the Facility Management company. 6 Periodical Hand Hygiene training programs The FM Company should be providing infection control related training sessions. Trainings such as Hand Hygiene should be given periodically and the details should be clearly defined in the service agreement made with the Facility Management company. 7 Compliance of employees with hand hygiene rules should be evaluated Evaluations could be carried out in accordance with the following requirements: a. Observations to cover all patient care areas over a one-year period (including selected polyclinics). b. Observations in intensive care units could be repeated every quarter. c. The result of the observations should be analysed on a quarterly period. 8 Disinfection procedures should be defined Some of the following requirements could be defined in the service agreement made with the Facility Management company: a. The Disinfection materials used should be selected from an AMR perspective b. Practitioners should be trained on the use of disinfectants. c. In areas where high-level disinfectants are used, appropriate ventilation conditions should be provided. 9 Maintenance procedures should be clearly defined for ventilation systems in the Operating rooms, and ICU’s. The following performance tests could be applied for the ventilation system to prevent infection spreading: a. HEPA filter compatibility (leak test) b. Air flow and air velocity measurement c. Pressure differences and air flow directions between sterile areas d. Measuring system effectiveness (re-cleaning) e. Particle measurement
10 Periodical Infection control trainings should be provided to the Facility management company staff The Above test could be included in the Facility management service companies’ scope of work defined in the service agreement. The following trainings should be provided to all personnel (Facility Management Company Staff. Not the Administrations staff e.g. doctors and nurses) for the prevention of infections and should be included in the Facility management service companies’ scope of work defined in the service agreement i. Periodic cleaning of air conditioning and water tanks,
No Subject KPI ii. Prevention of Legionella-induced pneumonia, iii. Maintenance and replacement of HEPA filters (prevention of airborne infections), iv. Proper disposal of filters. v. Training for hospital infections. vi. Prevention of vector-borne transmission, vii. Preparing and complying with disinfection program viii. Prevention of hospital infections, ix. Implementation of hospital cleaning procedure and Infection Control Committee approved risk level cleaning plans, x. Prevention of contamination, preservation xi. Cleaning of transport containers, xii. Annual health screening. xiii. Classification of dirty laundry in separate containers, xiv. Use of protective equipment, xv. Food hygiene and safety trainings for the kitchen staff before start of work, xvi. Periodic nasal and stool cultures xvii.Protection from biological risks and prevention of contamination xviii. Protection of health personnel and patient against biological risks and prevention of transmission in Imaging Service applications xix. Cleaning, disinfection applications, xx. Defining sterilization steps, xxi. Keeping records and periodically validating. xxii.Preventing the risks of transmission in Physical Therapy Services, xxiii. Changing the towels, pillows and covers used by the patients for each patient. xxiv. Completion of waste trainings by waste personnel, xxv. Control of periodic hepatitis markers, xxvi. Annual health screenings, xxvii. Monitoring of immunization xxviii. training for blood-borne diseases. 11 Complaints relating to infection prevention (including cleanliness) According to the IFC guideline requirement, the Facility management company needs to have two type of Complaints recording mechanism, Company staff and Patients. 12 Infection Control Committee (ICC) Collaborating with the Hospital Infection Control Committee (ICC). 13 Compliance with ESAP and ESMS FM company plans, method statements and procedures should be in line with the ESAP and ESMS requirements. Source: Mott MacDonald
Photo 2.1: Polyclinic Room
Source: Mott MacDonald
The above Photo 2.1 shows a polyclinic room and it appears that a hand washbasin is present within the clinical area. This is appropriate rather than outside the room, for the prevention of multi-drug resistant infections because the Doctor is able to wash hands in the room in between patients and between undertaking procedures..
Photo 2.2: Surgery Preparation Area
Source: Mott MacDonald
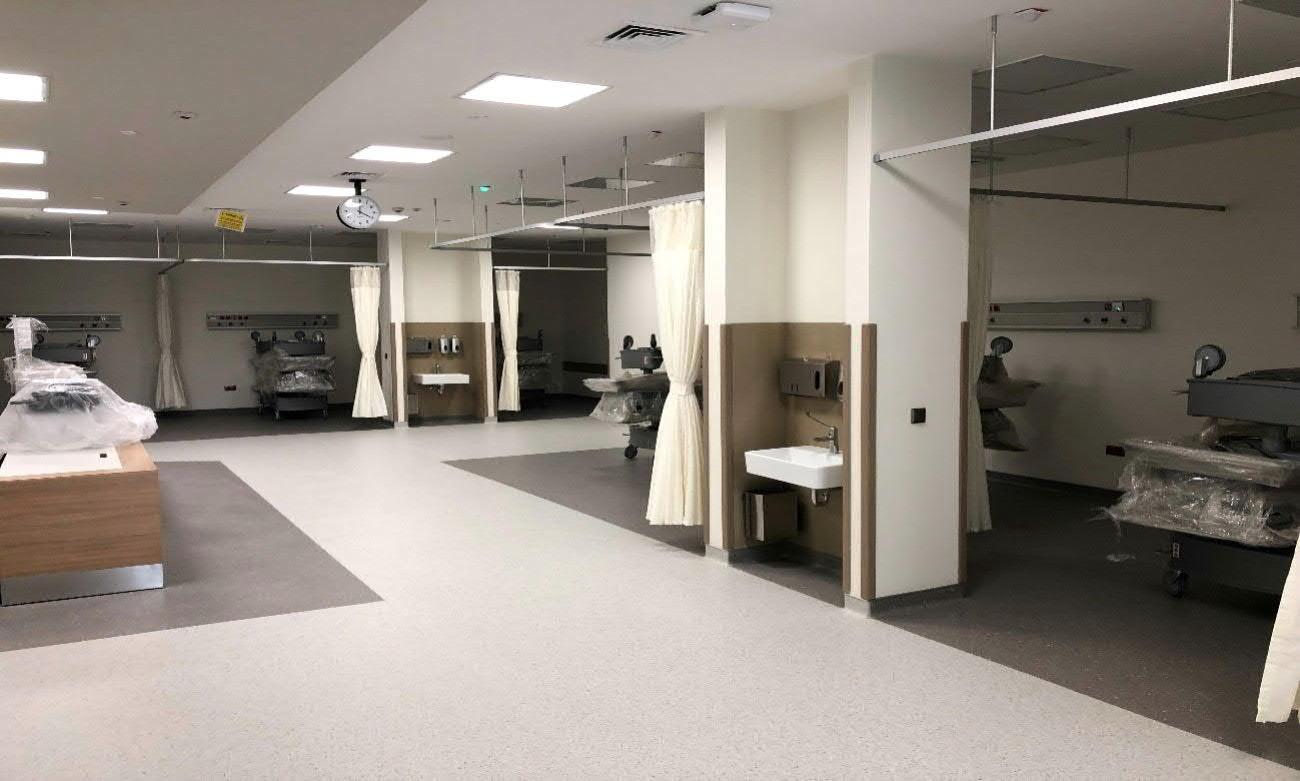
The above Photo 2.2 shows a Surgery Preparation Area and it appears that hand washbasins are present and readily accessible when moving between bed spaces, which is appropriate for the prevention of multi-drug resistant infections.
Photo 2.3: Intensive Care Units (ICU)
Source: Mott MacDonald
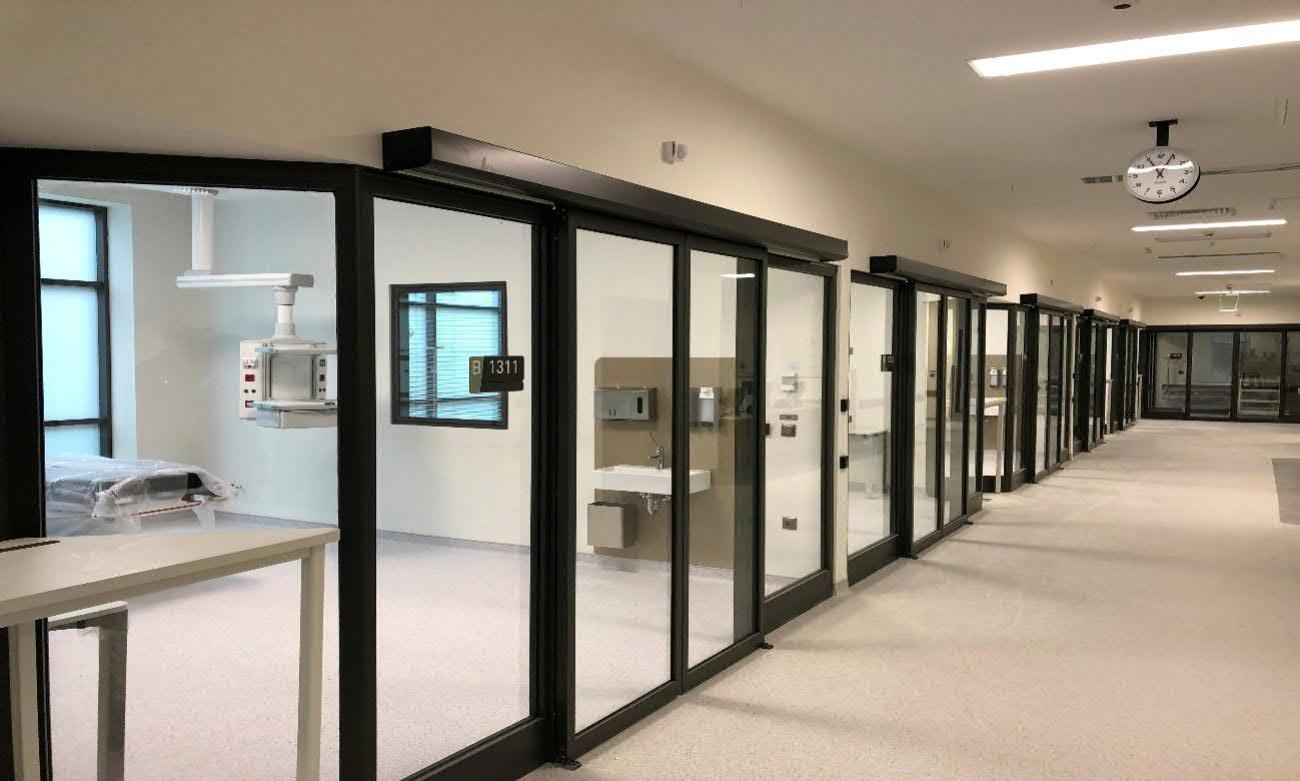
Photo 2.4 shows an Intensive Care Unit. Patients are nursed in individual rooms, with automatic doors, and hand washbasins are present in each room, which is appropriate for the prevention of multi-drug resistant infections. Additionally, the design means that despite the single rooms, patients can be easily observed and monitored by staff and the infection control measures do not hinder good clinical care. There is adequate space for patients and staff, and the area is uncluttered, which allows for easier cleaning.
Photo 2.4: Entrance of a Patient Ward
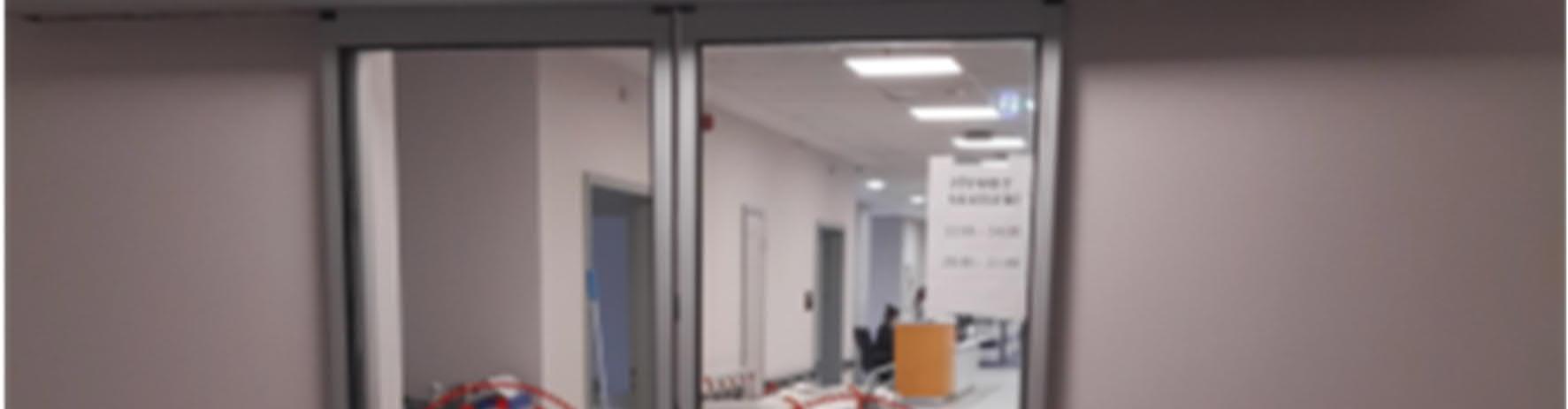
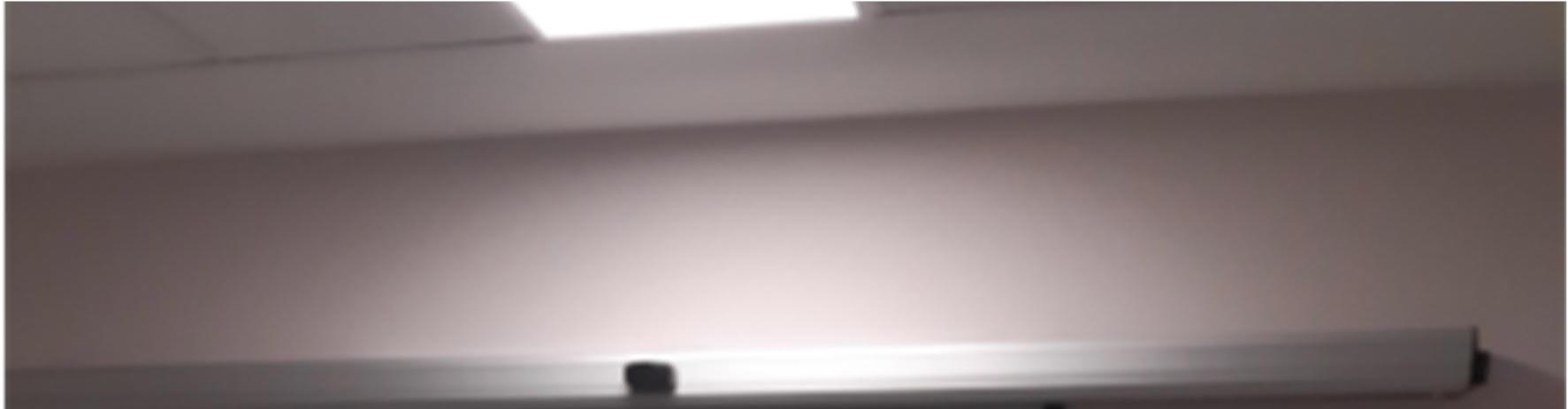
Source: Mott MacDonald
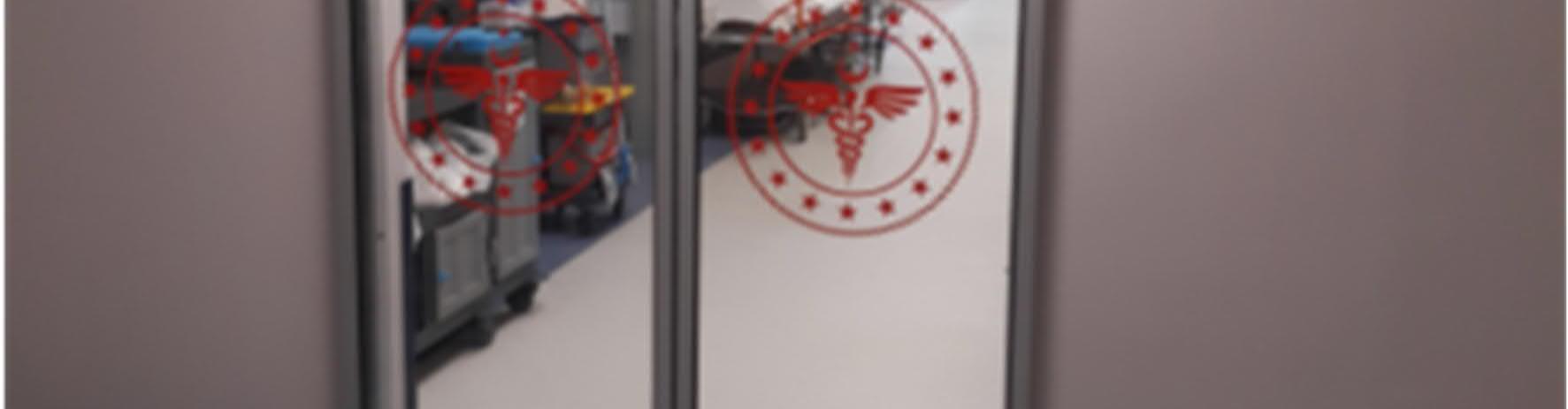
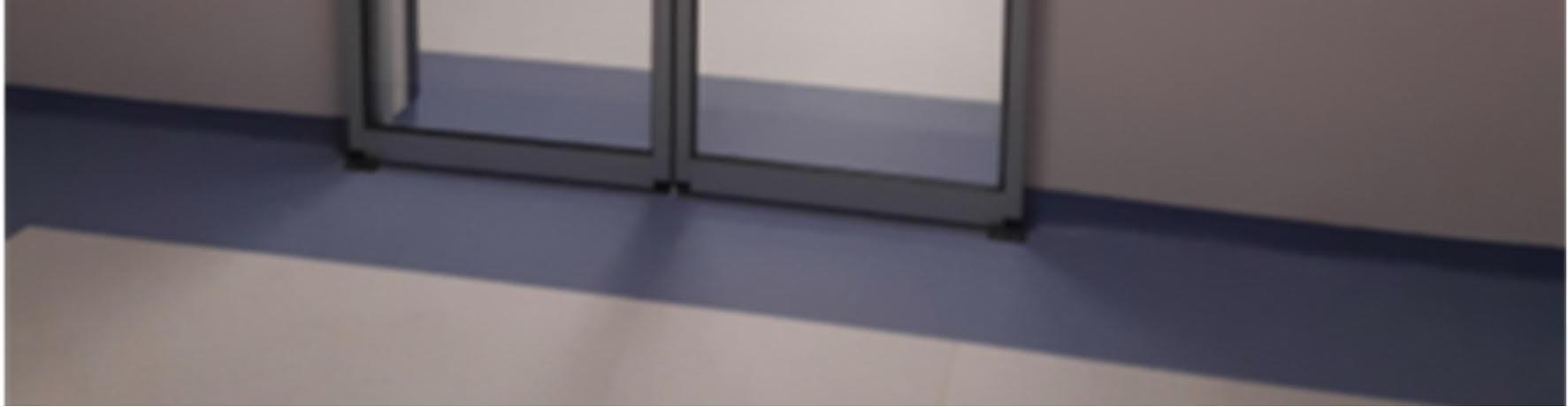
The above Photo 2.4 shows entrance of a patient ward. Although the doors are automatic, there is no sink or hand sanitisation station, which may discourage staff and visitors from decontaminating their hands on entering the ward, which can be a risk for the prevention of multi-drug resistant infections.
Photo 2.5: Patient room
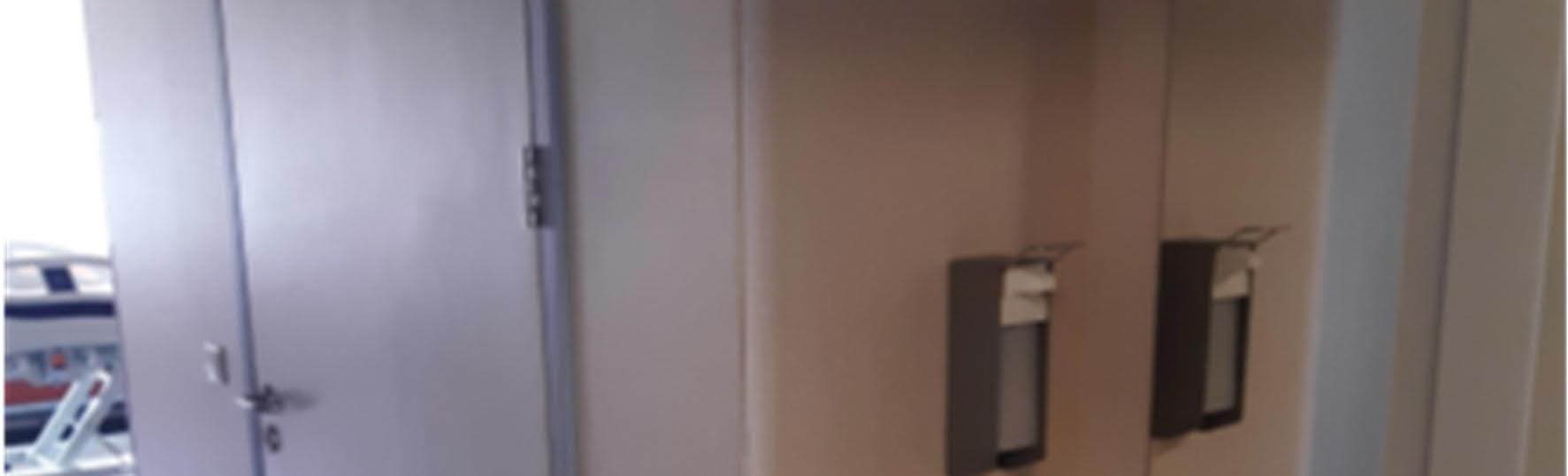
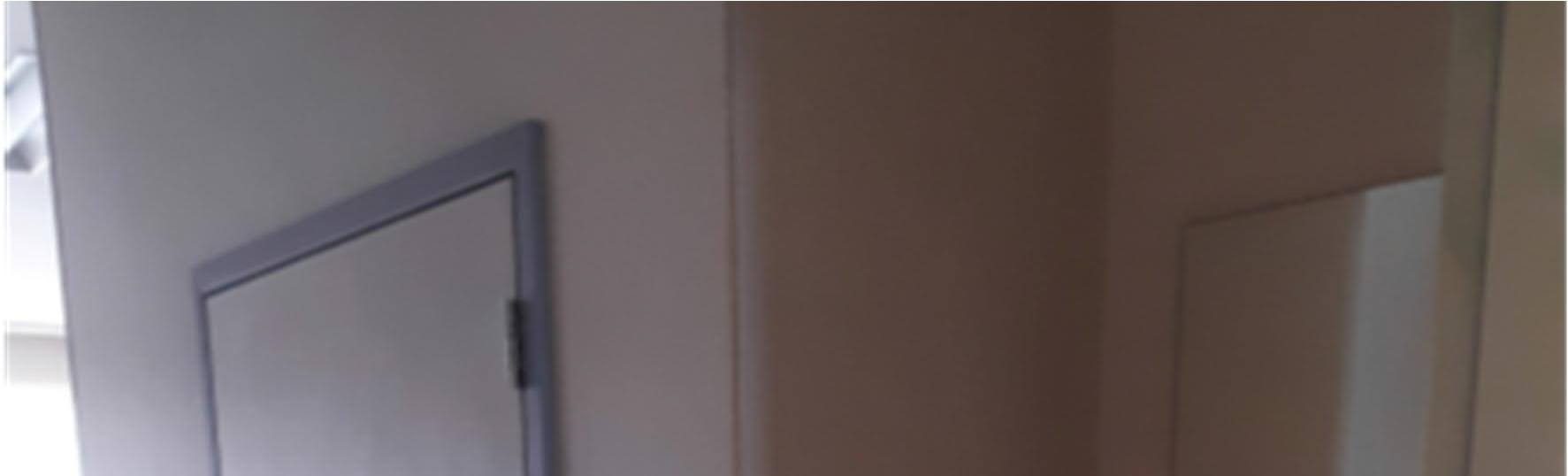
Source: Mott MacDonald
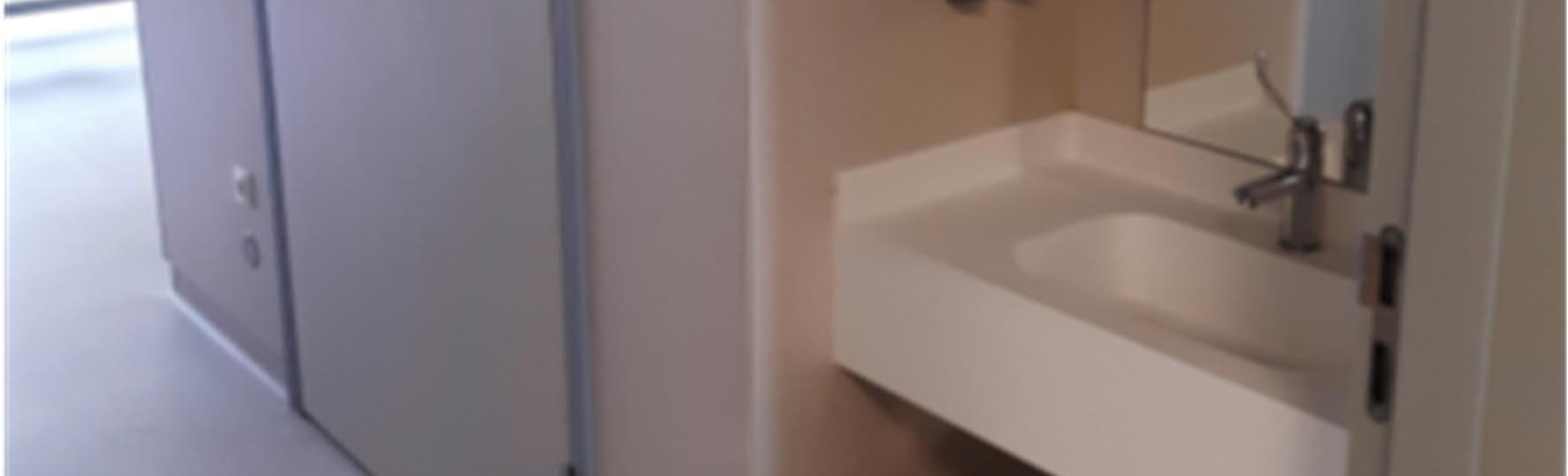
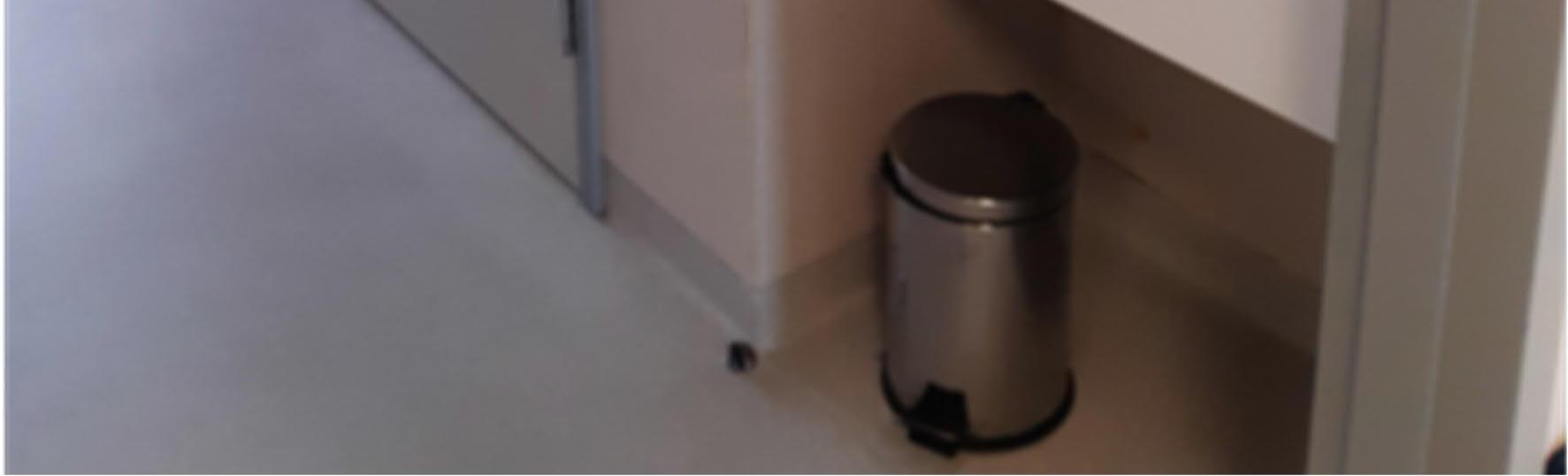
The above Photo 2.5 shows entrance of a patient room and it appears that a hand wash basin is present which is appropriate for the prevention of multi-drug resistant infections. The tap and soap dispenser are elbow operated, which reduces cross contamination.
Photo 2.6: Nurse Station
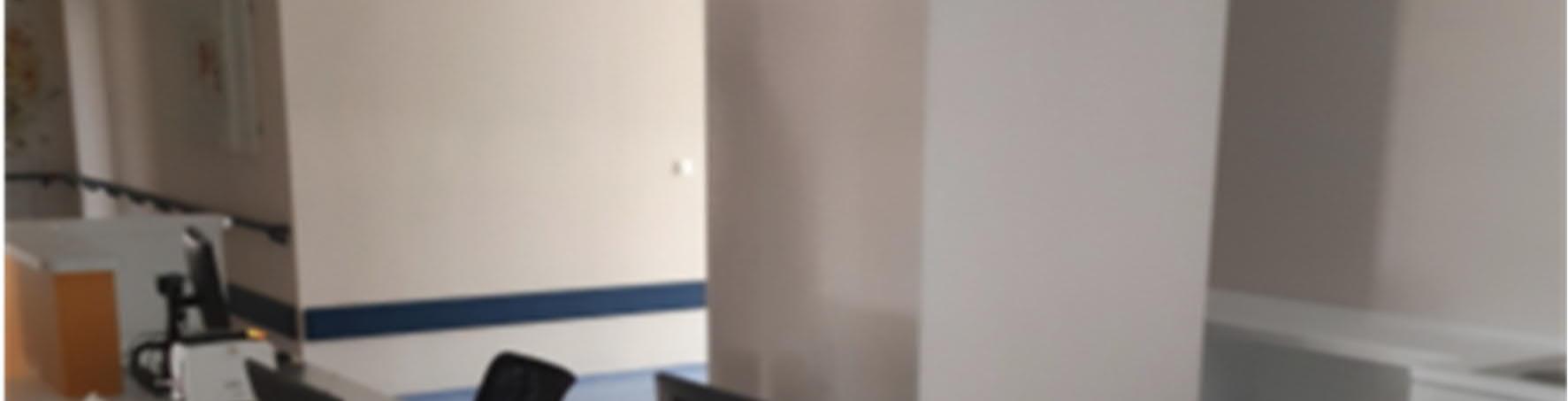
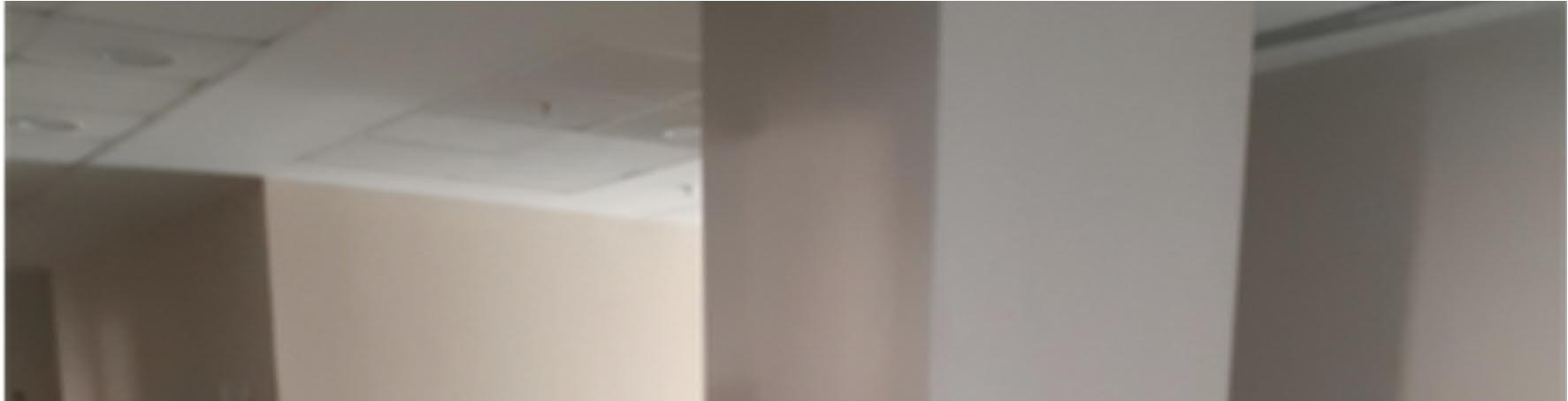
Source: Mott MacDonald
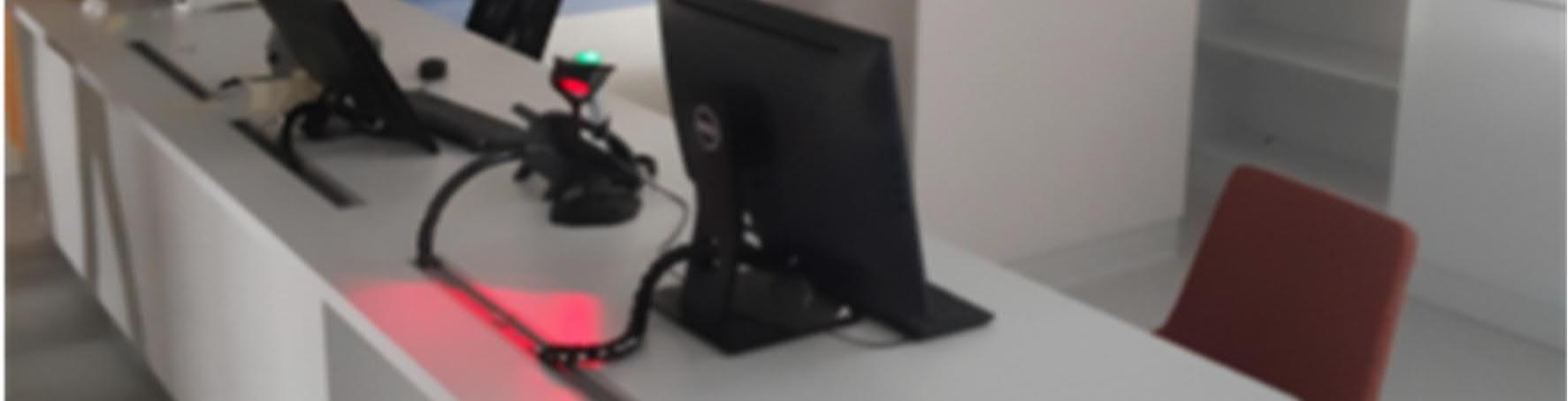
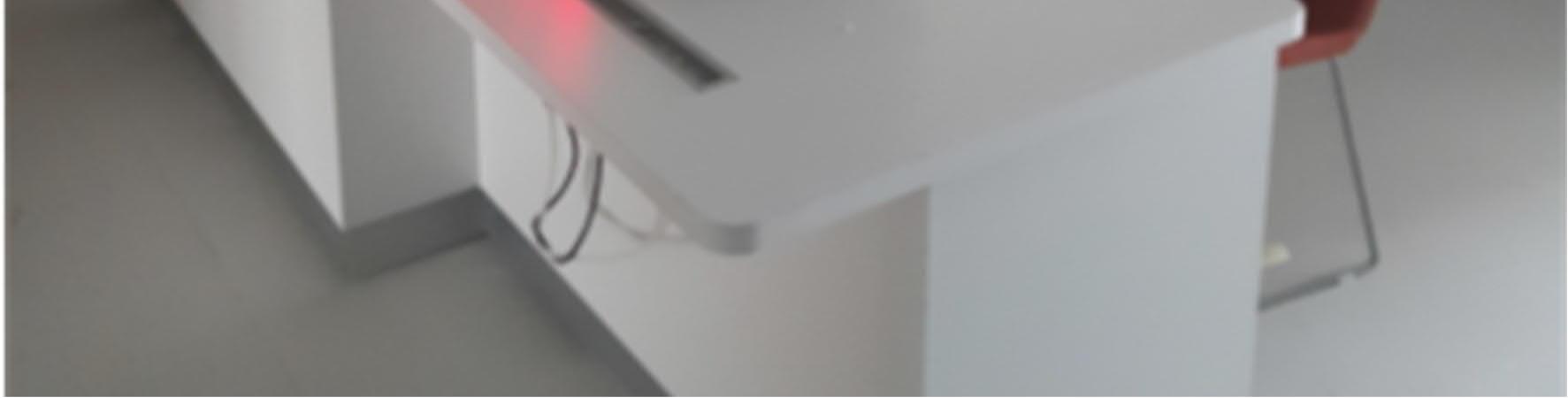
The above Photo 2.6 shows a nurse station and it appears that hand disinfection stations are not present which can be a risk for the prevention of multi-drug resistant infections.
Figure 2.1: Posters to encourage hand washing
Source: Web
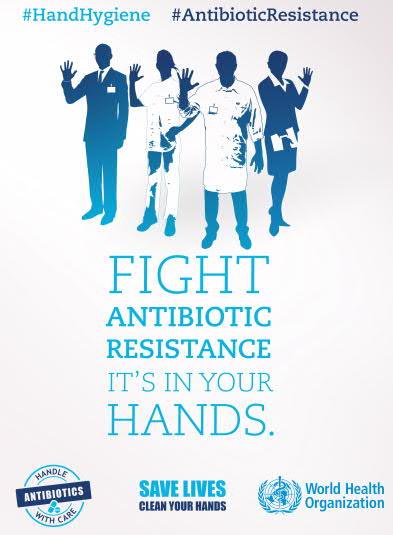
Figure 2.2: Typical Operating room HEPA Filter application
Source: Web
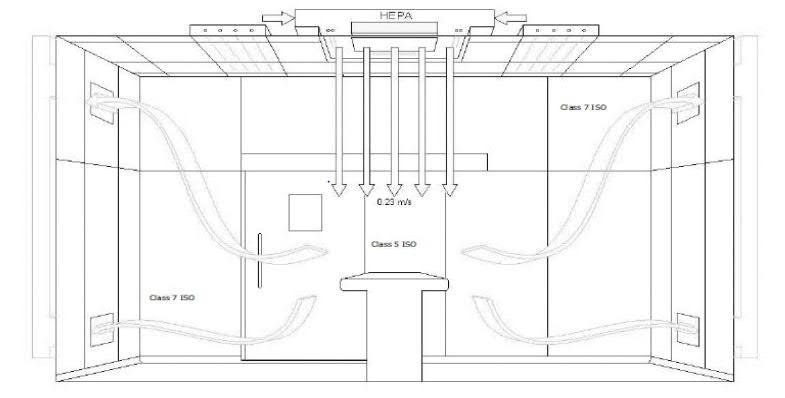
Source: ASHRAE-170- to be used during defining design requirements.
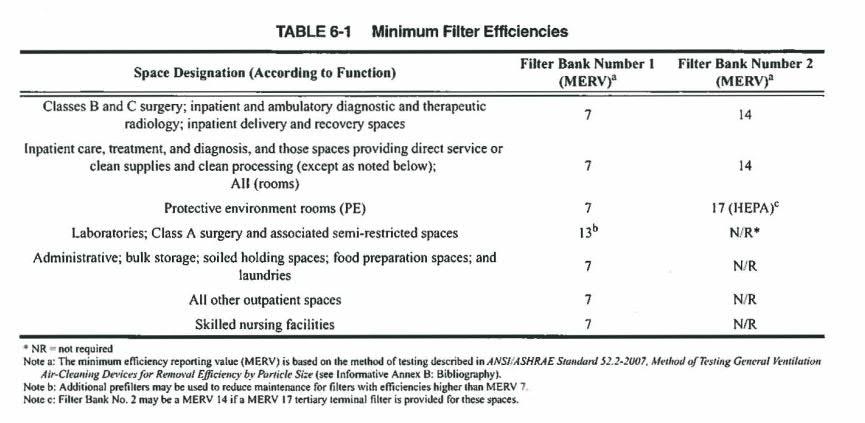
24 January 2020 14
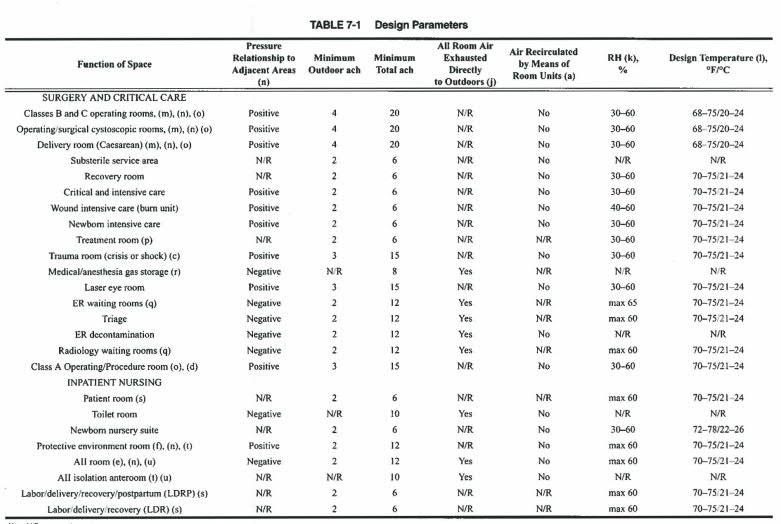
Source: ASHRAE-170- to be used during defining design requirements.