
6 minute read
An Intentional Space
The meticulously crafted workshop of Dano Harris
words and photos :: Kristin Schnelten
Dano Harris swings the hefty Dutch doors of his shop wide into the autumn afternoon, filling the quiet interior with soft beams of light.
The high half-doors clang to a stop and he dusts strong hands on a worn leather apron. “If I open the full door, I can’t get any work done,” he says. Curiosity gets the best of passers-by, it seems.
To the observant, Dano’s cordwood studio serves as a welcoming lodestar to the tiny village of Ceylon. Perched high on a hill at the edge of town, its exposed beams, steel supports and green roof are a masterpiece of old-world design and exceptional craftsmanship.
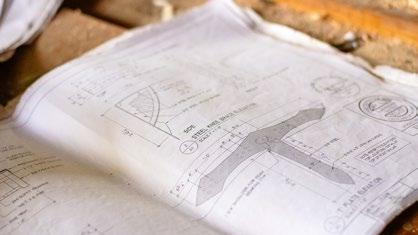
It’s a fitting home for Dano’s work. An artisan in both metal and wood, his skillset—and mindset—were key to the success of this calculated and protracted building process.
The workshop had its beginnings more than a decade ago, when Dano and his wife, Shannon, purchased the property next door to their century home. Over a five-year period, Harris slowly disassembled the existing house on the lot, stockpiling one window, brick and beam at a time.
While continuing to fill orders at a shop on his parents’ property, co-raise his now six children and spend winters working in recreational programming at Beaver Valley Ski Club, Dano still found time to research the intricacies of cordwood, timber and green-roof construction and draw up initial plans, later to be stamped by an architect.
He compiled lessons learned from prior shops to design the workspace and set a footprint that worked within property setbacks. “A lot of it was based on the size of the house that was there. Also the apple tree right there,” he says, indicating the soaring heirloom variety just feet from the handmade fire escape. “I couldn’t touch that. You can’t just buy an apple tree of that size and put it in.”
Such was his thoughtfulness throughout the project.
“The whole idea for this building was that it could be taken apart and reused in the future,” Harris says. “So I tried to use very few newer materials. On the roof I used a little bit of plywood just to smooth it out, and there’s a bit of insulation up there under the membrane. But other than that, I think everything could be reused. It’s all solid wood.”
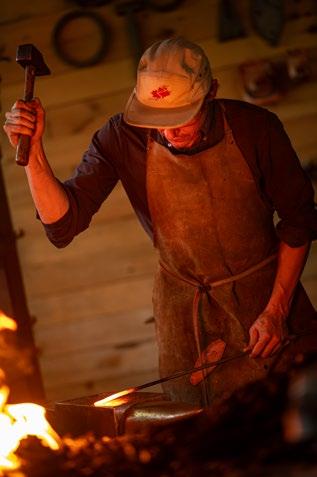
“All these old barns are coming down now, and the materials are being reused. Whereas, with newer houses, some of it’s recycled but really most of it is just garbage. Cordwood was a way not to use any insulation, and it was really cheap to do. It was just really high labour.”
Two years of labour, as it turns out. The majority of it provided by Dano and Shannon with help from family, friends and neighbours.
Ash and hemlock timbers from a local Amish mill were handgraded, pre-fit by Dano off-site, then numbered, disassembled, transported and hoisted into place with the help of his father, Don, and friend Cory Davies. What followed was the painstaking process of building the cordwood walls. In addition to cutting each split to an 8-inch length and meticulous stacking, the method requires precision measurement of the wood’s humidity level, and therefore timing is key.
Dano’s innate curiosity and natural teaching affinity spill into the retelling of this story as he calmly explains the specific ratio of sawdust and lime that fills the airspace between exterior and interior layers of mortar. Then he reaches onto a shelf to display the chisel he forged and turned on a lathe—the tool he used to notch every beam at every joint in the building.
“This is an old spring, pulled off a truck,” he explains. “And the handle is a piece of ash from the off-cut of one of the shop’s beams.”
As he pulls the chisel from its sheath, he says: “My grandfather is from Jamaica, and on his 18th birthday he shot a crocodile that was being a nuisance in the village. Afterward he had the leather cured and made into a suitcase. So I made this with the leftover leather from about 1938.”
When Dano returns the chisel to the shelf, he pauses to note that it and the circular saw next to it “pretty much made the whole building.”
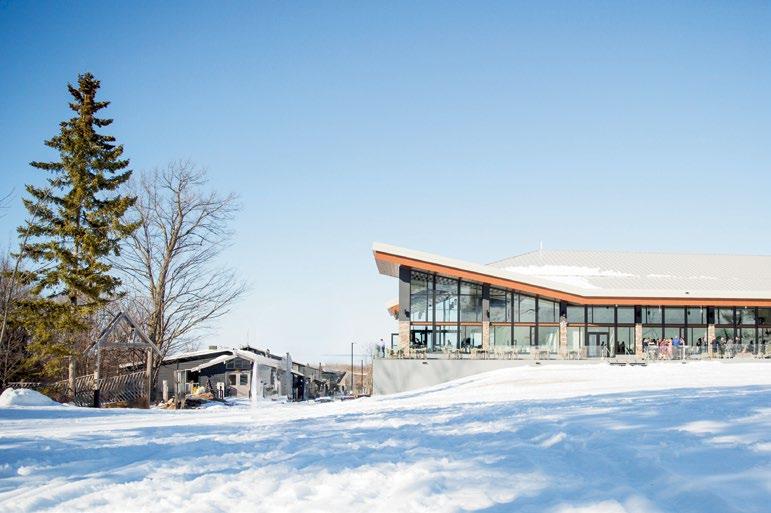
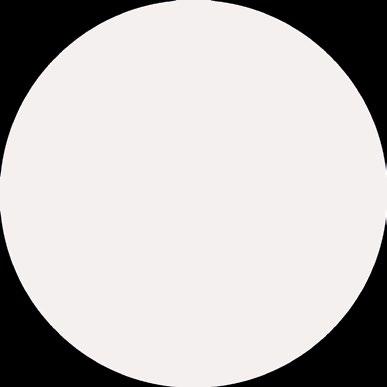
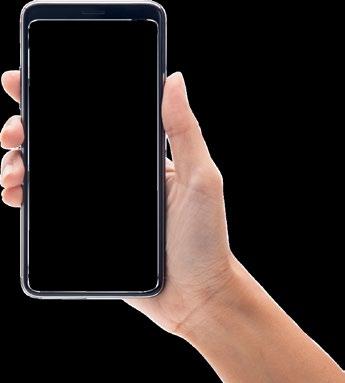
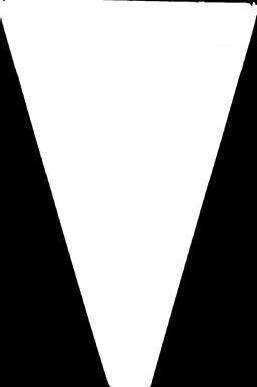
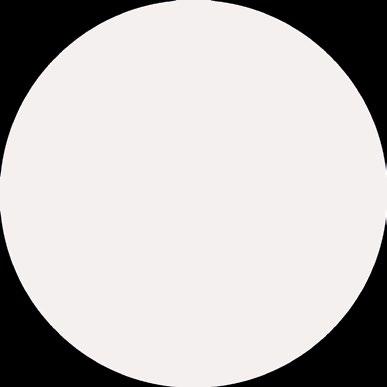


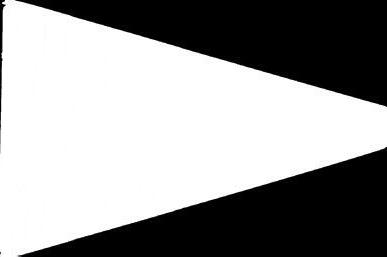

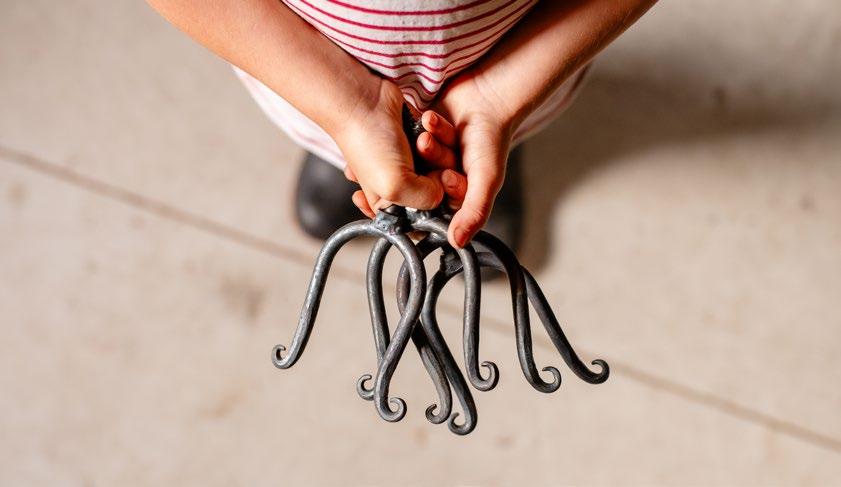

That adventurous grandfather took up woodturning in retirement, and was an early inspiration to a young Dano. Harris initially dabbled in furniture design, following in his parents’ designer footsteps, but discovered he found more joy in the hands-on process of making.
A meandering career path led him from woodturning to metalwork, and most of his time is now spent with the latter medium, most often as a blacksmith, and the forge and its imposing chimney are the centrepiece of the shop. Unsurprisingly, those chimney bricks were salvaged—some from the former house, others from various sources, including an old school in Flesherton.
Steel supports, which Dano designed with an understated flourish, bolster interior beams. And each frame joint is secured with enormous plates that echo those same lines, the curve of which is replicated again in the greying beams of the carport. Steel foundation flashing consists of off-cuts and scrap. High windows capturing indirect light were sourced from a single Kijiji find.
Everything here is intentional.
With added illumination from the half-open doors, Dano shuts off the overhead fixtures and fires up the forge. The natural light is key to his blacksmithing work; he has to pay close attention to the colour of the metal as it heats and cools.
It’s that exacting attention to detail, along with thoughtful planning and mounds of patience, that created this piece of art masquerading as a shop. If you’re interested in checking it out, please call ahead—Dano needs to get some work done.
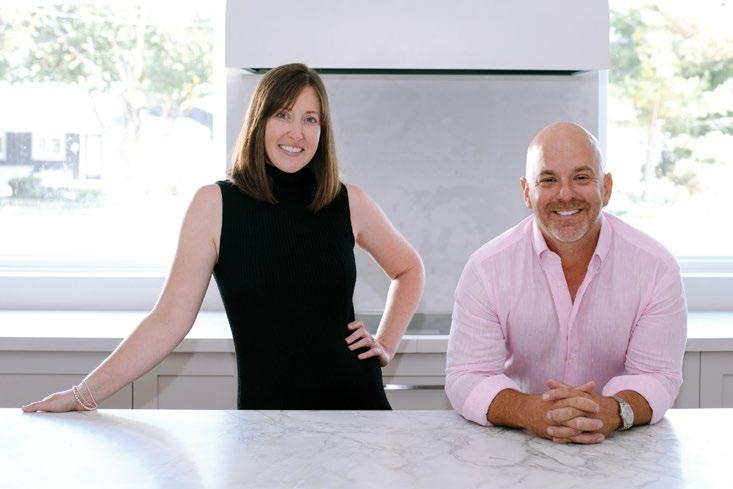

120
905.845.1561
WWW.CORBETTS.COM
INFO@CORBETTS.COM
@CORBETTSSNOW roottofruit.ca
WHETHER YOU’RE CHASING A PODIUM OR A FRESH LINE, CORBETTS IS ALONG FOR THE RIDE.
The best gear selection across Canada from all your favourite brands.
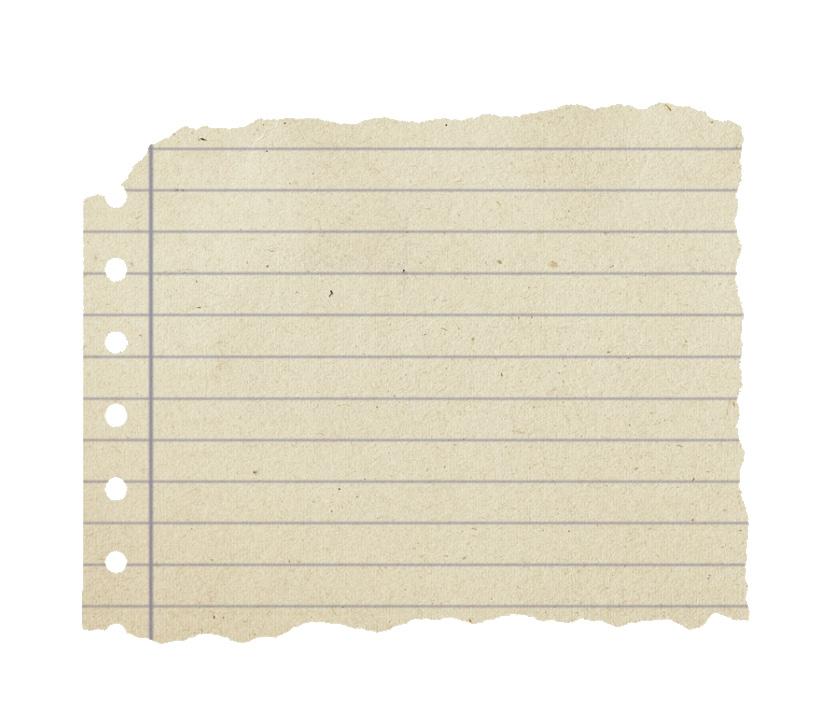
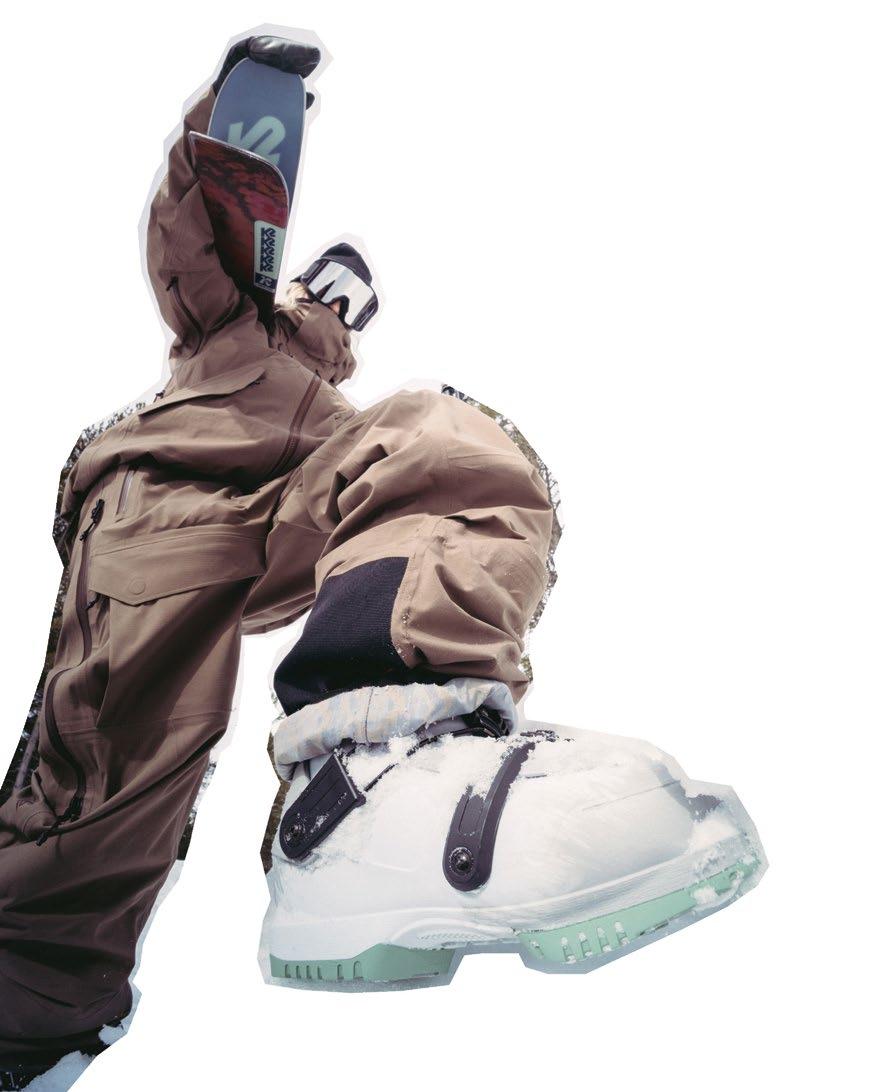
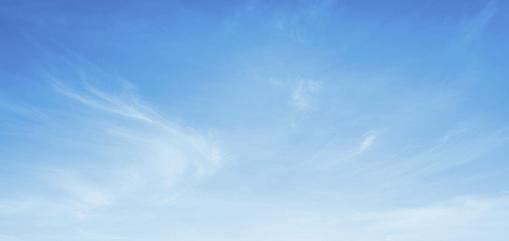

Try one of our many varieties of Activated Turmeric Elixirs & Syrups to sip, warm, cold, or get creative and kick up your favourite beverage.
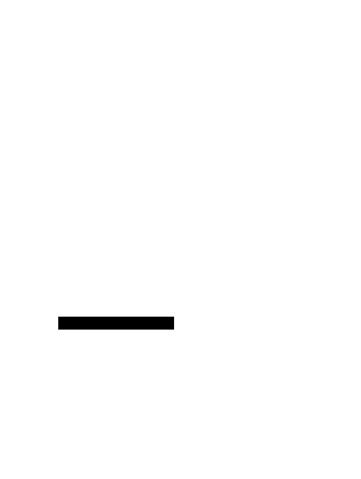
JOIN US IN CLARKSBURG ON THE EVENING OF DEC. 6 FOR SOME CUSTOMER CHEER
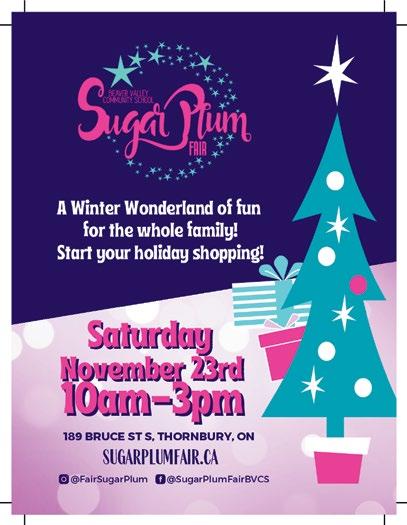
