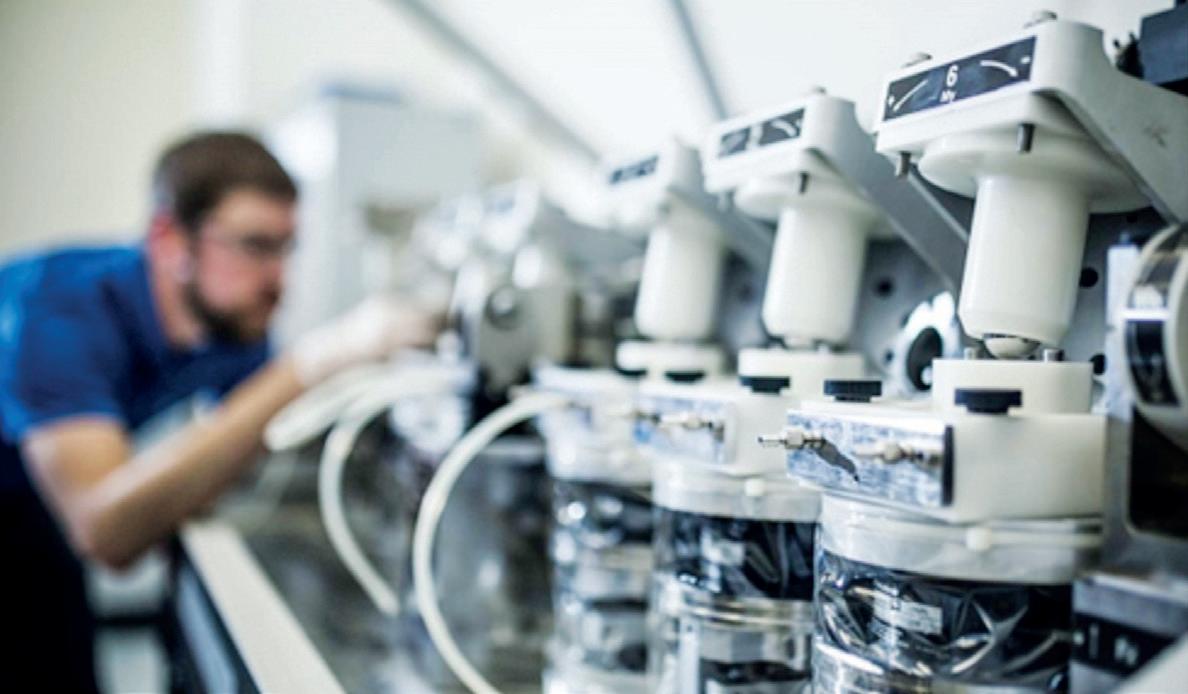
10 minute read
Industry 4.0
from MPN EU Issue 65
by MPN Magazine
INDUSTRY 4.0
NEIL BALLINGER, HEAD OF EMEA AT AUTOMATION PARTS SUPPLIER EU AUTOMATION, DISCUSSES THE CHALLENGES FACING THE SECTOR AND HOW RECONDITIONED AND OBSOLETE COMPONENTS CAN HELP.
Overcoming supply chain disruptions
in medical device manufacturing
The COVID-19 pandemic brought unprecedented challenges for the medical device industry, from skyrocketing demand for respirators and personal protective equipment (PPE) to staff shortages. Since the second half of 2020, another major challenge has been procurement. A combination of pandemic-related factors, sociopolitical instability and a major semiconductor shortage has led to an unprecedented supply chain crisis — a challenge that is particularly felt in safety critical sectors like medical device manufacturing.
Due to the extensive review process for each device, this sector usually needs long lead times for products to get approved and delivered, so even a minor disruption can result in major delays. This is the case for components used in the final products, but also for automation parts in core machinery on production and assembly lines. For example, equipment and processes will have to be re-qualified in case of major maintenance or substantial modifications to the production lines.
THE NEED FOR COMPLIANCE Medical device manufacturers must navigate an abundance of red tape to ensure regulatory compliance. For instance, compliance with the European Medical Device Regulation (EU MDR) is compulsory for companies that sell their devices in the EU. When it comes to a medical device manufacturing plant, the initial design of production lines needs to be validated by the relevant authorities, and almost every change on the line may require additional inspection and validation.
A validation master plan (VMP) outlines the necessary steps when qualifying a facility for producing medical equipment, as well as a detailed process for maintaining a qualified facility. By following a VMP, manufacturers can be sure that their processes will produce only conforming items.
This sets medical device manufacturers up for success, but also requires them to adhere to strict guidelines. For example, if a component fails and is in short supply, it cannot just be replaced with a compatible one — the same part will have to be sourced. This can become a regulatory nightmare if the component is obsolete and no longer produced by the original equipment manufacturer (OEM), or if the latter is impacted by supply chain disruptions and unable to produce and deliver as usual.
COPING WITH DISRUPTIONS In the short term, the best way to combat the negative consequences of shortages is keeping track of stock and increasing inventory whenever possible. On the other hand, investing in supply chain management (SCM) software can be a good long-term strategy to help track inventory, manage shipping, and keep updated on which stocks are decreasing the quickest.
It is hard to avoid obsolescence issues when manufacturing medical devices, but there are some steps manufacturers can take to minimise the impact. In the design phase, design engineers should carefully research the expected lifespan of the components they intend to use, as well as monitor how long these have already been on the market.
For manufacturers who are past the design stage, refurbished components can be a great way to source parts that perform like brand new ones, even when the OEM cannot deliver. An automation parts supplier that specialises in reconditioned and obsolete parts, like EU Automation, can help source the right product regardless of where in the world it is located. They can then ship it in record times, saving manufacturers weeks of costly downtime. However, this should be used in combination with other proactive obsolescence management strategies.
With disruptions continuing to impact global supply chains, manufacturers should take the time to implement a good obsolescence management plan. Failure to adapt to these challenging times could cost companies millions in unnecessary downtime and replacements.

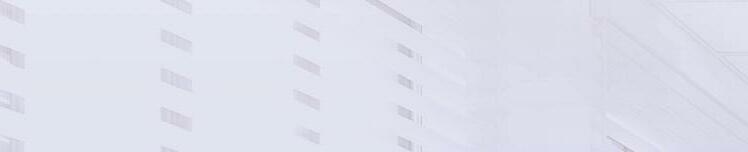
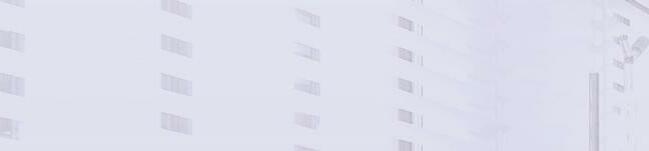
DIGITAL HEALTH
JOHN CHRISTIANO, DAVIS-STANDARD, GIVES AN INSIGHT INTO THE FUTURE OF DIGITAL TOOLBOXES.
A Digital Toolbox Full of Possibilities
Digital transformation impacts our lives daily. The multiple features on our phones, the navigational systems in our cars, instant access to information, live streaming of media into our homes; are just a few examples of how the Internet of Things (IoT) has changed the way we live and do business.
Manufacturing operations are extremely complex, which is why digital infrastructure has been slower to occupy this space. As a result, our industry looked inward to strengthen operational efficiency and profitability. Improvements focused on control systems for the factory floor through automated control systems that improve safety, reduce human interaction, strengthen local data collection using improved SCADA systems (Supervisory Control and Data Acquisition), and access equipment via the internet. These steps served as the initial building blocks for digital transformation within operations.
This movement accelerated as digital technology proved to be more reliable. Our industry realised the potential and initiatives gained traction. The fourth Industrial Revolution quickly gained popularity. The possibilities and advantages of Industry 4.0 spread around the globe, and today we have the Industrial Internet of Things or IIoT. The IIoT platform enables the development of new technology by leveraging information from existing control capabilities. Currently, line control systems can display and collect performance information, providing an interface for operating equipment. However, this presents disparate information that is difficult for operators to translate. New digital technology expands this platform by introducing a human factors concept of situational awareness to improve performance while incorporating preventative and predictive tools into our operations. This gives you instant data access, imagery, and connectivity not available with current systems.
The multitude of benefits realised through increased situational awareness provides you with a customised digital toolbox that will both simplify and amplify your operation.
Situational awareness is defined as developing and maintaining a dynamic awareness of the situation and the risks present in an activity. This is based on gathering information from multiple sources from the task environment, understanding what the information means, and using it to think ahead about what may happen next.
The three aspects of information processing include perception, understanding/interpretation, and prediction.
DIGITAL HEALTH
Perception or gathering of information directly using our senses of vision, hearing and touch, or indirectly through a complex control system involving HMI displays, and interfaces.
Understanding information by combining this data from the production process or equipment with existing knowledge and experience from memory. Information gathered is given meaning. This includes developing an accurate and complete picture of the operation, better informing our decisions.
Prediction and projection into the future, which includes thinking ahead. This involves predicting what to expect as well as what not to expect.
Situational awareness provides context to the complex data that your team receives from your production environment. It helps your team interpret data, to make informed decisions that result in positive projected outcomes. It makes it possible to transition from a historical perspective of “running to failure” using post-failure analysis to a preventative and forward-looking system using real-time information from your process and equipment. DS Activ-Check is a custom-designed, cloud-based platform that improves the operator’s situational awareness to enhance extrusion production line performance and productivity. DS Activ-Check leverages systems and strategies offered by the IIoT to increase operator effectiveness, leading to reduced downtime, better product quality, and reinforced operator safety. The configurable platform engine uses analytical tools based on long-term cloud data storage along with process and equipment technology algorithms to help management and production teams identify and improve product quality and line efficiency.
The DS Activ-Check system continuously monitors production line equipment. The real-time operational data, including KPI (Key Performance Indicators) from the production line PLC or SCADA system, are sent to an edge server inside the plant. The edge server collects, buffers, and encrypts the data before sending the information on a secure Port 443 through a secure firewall. The server is located behind a secure firewall to prevent unwanted access.
The data moving on the secure Port 443 travels over the internet and is stored on the cloud. The cloud refers to servers or computers accessed over the internet and the software and databases that run on those servers.
WHAT ADVANTAGES DOES USING CLOUD-BASED MONITORING OFFER?
Information storage and access
Data collection and storage capacity is unlimited. Your valuable production data is securely stored and can be used in the future for comparing production performance between lines and plants, optimising production processes, and more.
Connectivity
You have the ability to securely monitor your production process from anywhere at any time. This is a force multiplier for your process, maintenance, and operations teams. They will be able to address issues before failure, eliminating lost production. They will be able to identify a specific issue and take corrective action quickly versus spending countless hours trying to determine a root cause. They can deploy maintenance tasks with all records of completion stored for future reference. They can collaborate and troubleshoot issues in real-time to prevent costly production downtime.
The data storage capacity for a typical SCADA system is limited to 180 days. After 180 days, the data is lost. A cloud-based system ensures your data is never lost.
Scalability
Production equipment can be easily added to the system starting from one line. In addition, production lines in the plant and from other locations, domestically and internationally, can be included. This is a very important feature for digitally transforming multiple locations.
Analytics running in real-time
The cloud platform provides the capability to continuously run software that analyses equipment performance. Using real-time data from your production process, software programmes continually monitor the performance of your operation and provide critical information to key players. This reduces or eliminates unwanted downtime and guides your decision-making with regard to preventative and predictive maintenance items.
As with any new technology, digital transformation is a journey that evolves and develops as it is implemented. The time to take that first step is now, that vital step that opens up a world of efficiency and troubleshooting possibilities for your medical extrusion and/or converting operation.
SPONSORED
Dedicated cGMP Facility for POROUS PLASTIC COMPONENTS
Porvair Sciences maintains a dedicated clean area for manufacturing Vyon porous plastic components for healthcare, pharmaceutical and life science products.
The Vyon white room provides a controlled manufacturing environment, dedicated to fulfilling the strict regulatory and cleanliness requirements for components used in their products. Within the white room we have implemented cGMP compliant procedures enabling us to achieve even tighter specifications for contamination-free components.
Drawing upon decades of knowledge in the manufacture of industry-leading porous plastics, combined with advanced materials expertise, Porvair Sciences has established a reputation for delivering outstanding components to OEM and laboratory customers worldwide. Proprietary to Porvair Sciences - Vyon is a highly versatile porous plastic which can be modified to give hydrophilic or hydrophobic properties or enhanced to achieve specific chemical and biochemical separations. Vyon can also be combined with other materials to create application specific composite products.
These and other desirable properties have made Vyon the porous plastic material of choice for healthcare, pharmaceutical and life science companies looking to produce filters, vents, bed supports and sample separation products with a competitive advantage.
FOR FURTHER INFORMATION PLEASE VISIT https://www.vyonporousplastics. com/process-chromatographybed-supports/, or contact Porvair Sciences Ltd on +44-1978-661144 / enquiries@porvairsciences.com.
Caption: a range of Vyon porous plastic components and products
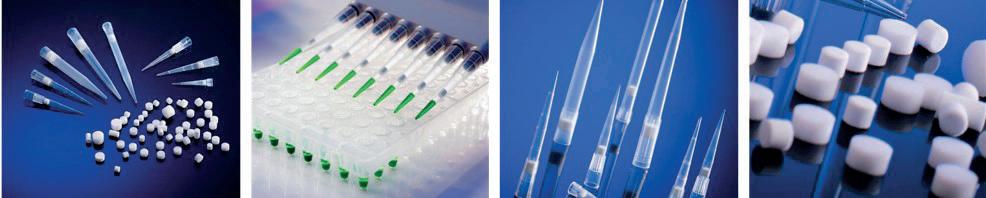
Precision Engineered Shapes and Sizes
From simple discs to complex shapes, Vyon® porous plastics can be converted from sheets and rolls to a wide range of custom configurations to ensure secure and long-lasting fit in the final assembled product. Combining decades of manufacturing expertise together with the flexibility and versatility of Vyon® allows Porvair Sciences to efficently produce custom, high quality components for medical, healthcare and life science applications. •Excellent edge finish •Cut-to-fit precision •Wide range of sizes and dimensions
Get in touch to create your custom Vyon® porous plastic component. Contact: enquiries@porvairsciences.com Website: www.vyonporousplastics.com
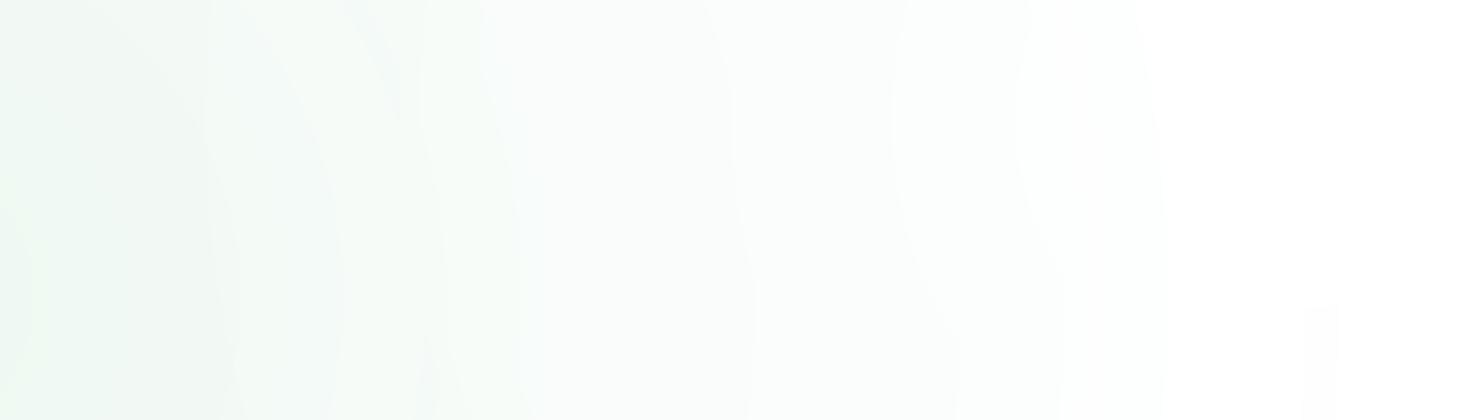
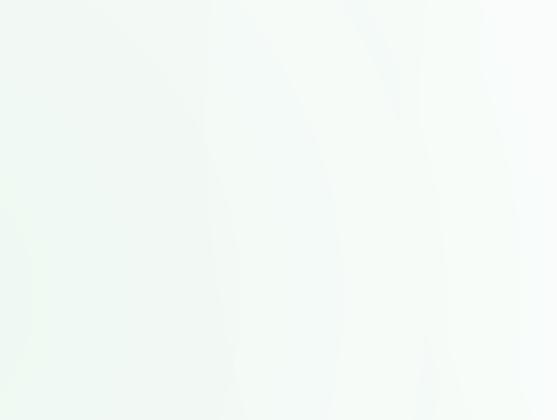
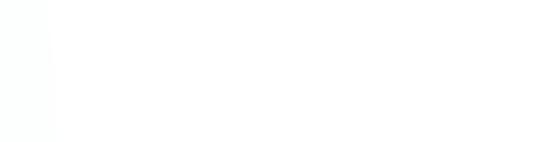
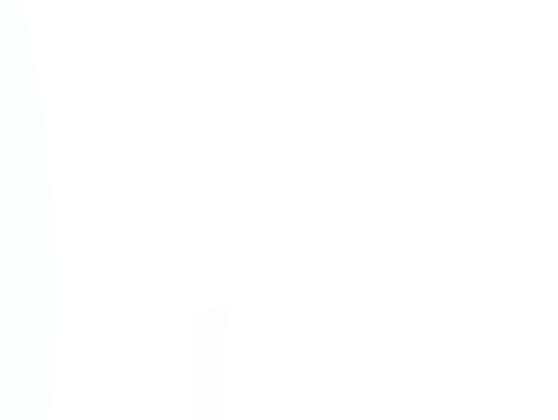
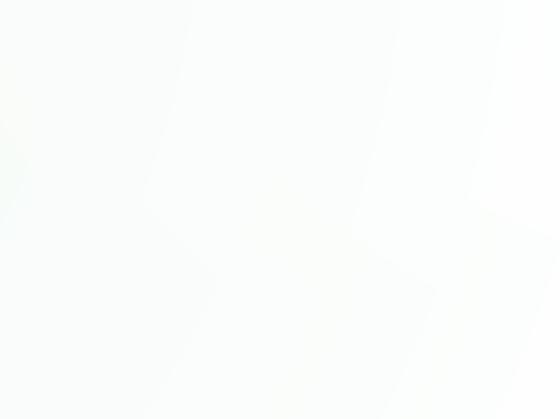
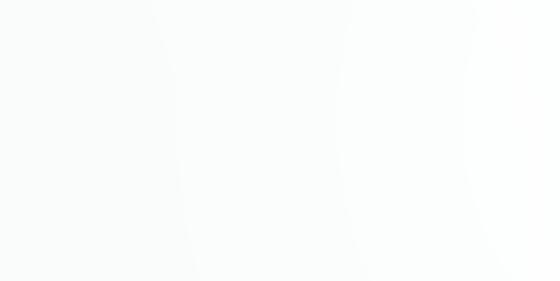
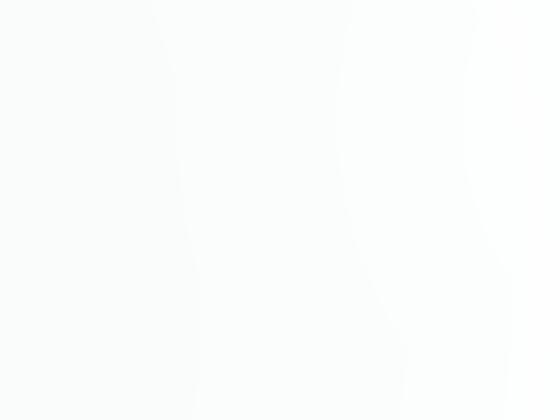
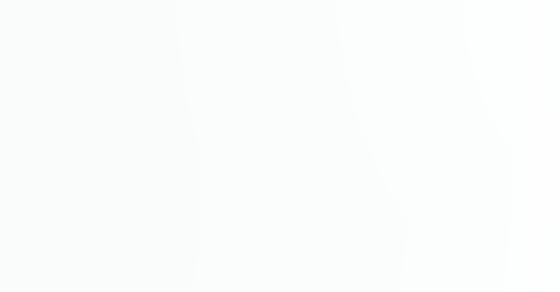
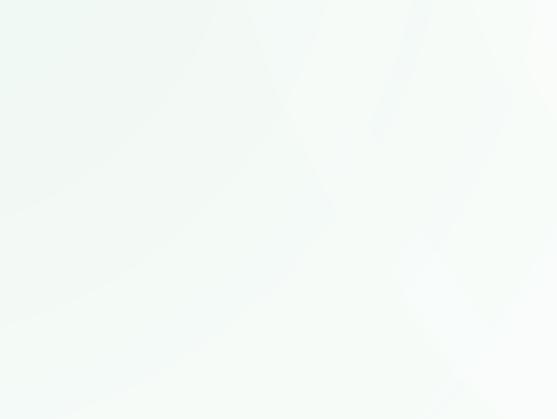
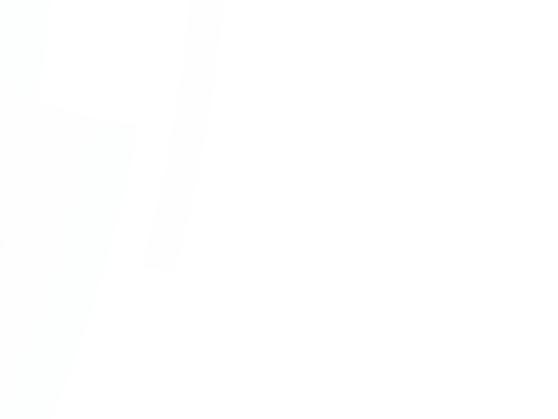
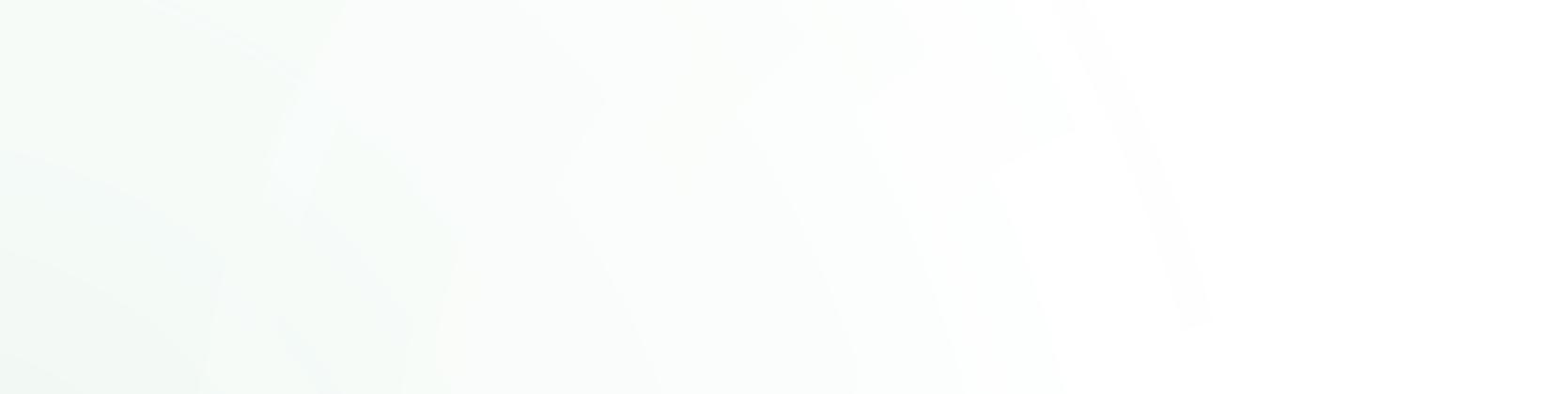
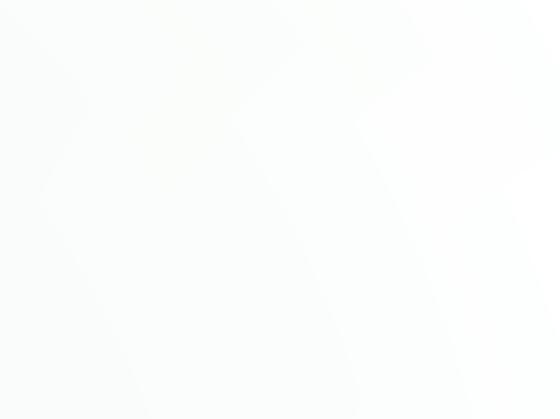
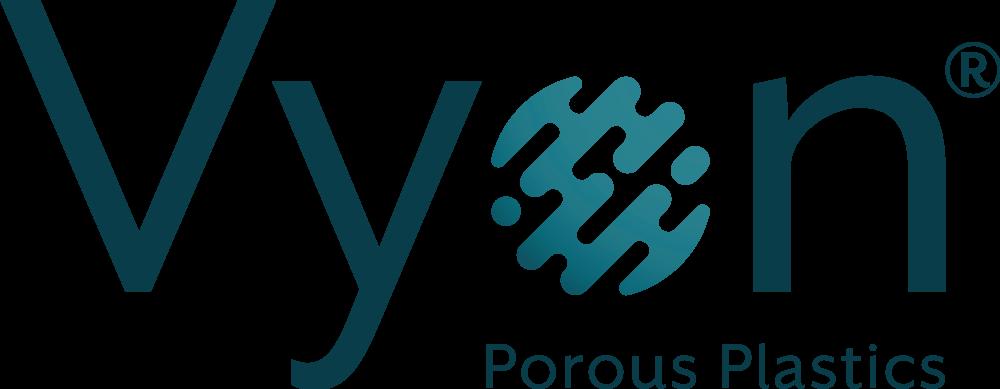