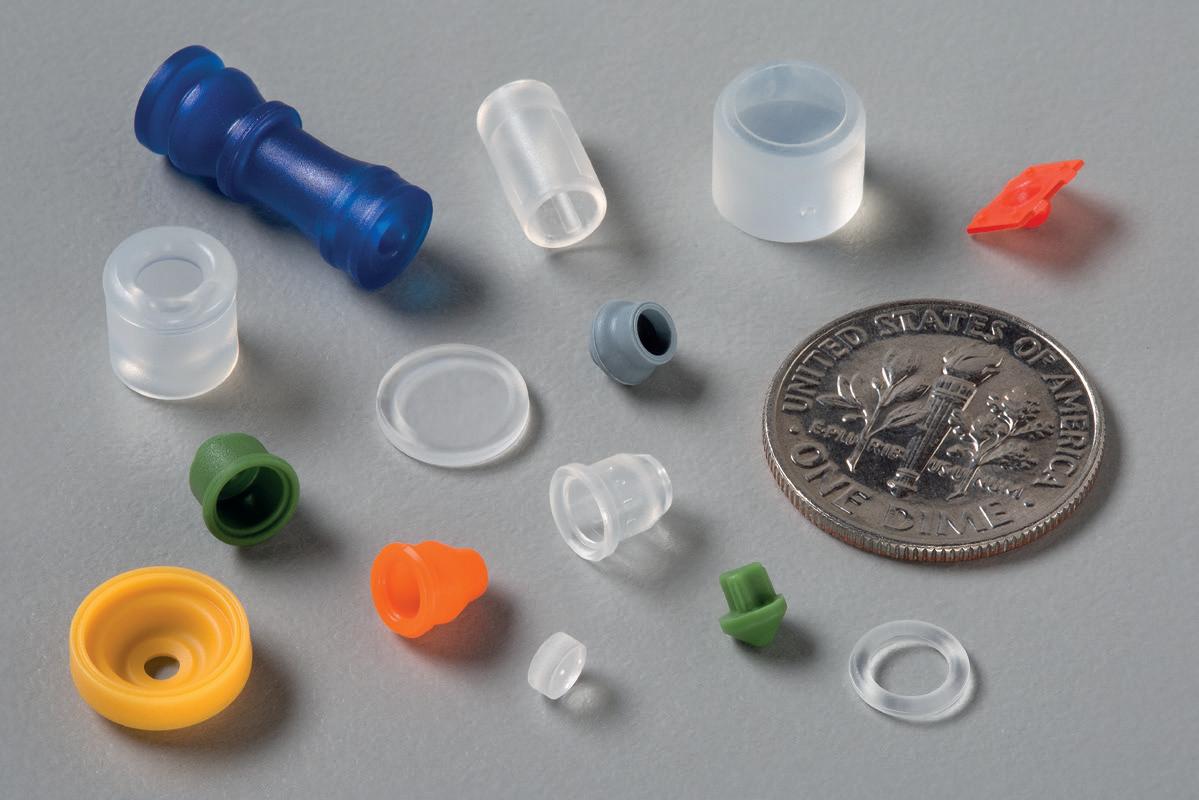
8 minute read
Micromoulding
from MPN EU Issue 68
by MPN Magazine
ROB CONNELLY, PRINCIPAL ENGINEER, TRELLEBORG HEALTHCARE & MEDICAL, EXPLAINS HOW PRECISION TOOLING, VALIDATION, AND SKILLED ENGINEERS MAKE MINIATURISATION POSSIBLE.
The demand for miniaturisation of silicone and thermoplastic moulded products for medical devices has heightened the importance of process validation, precision tool design, and skilled tool operators and engineers. According to Plastics News Research, advancements and miniaturisation in the medical device industry have improved healthcare around the globe, making treatments and monitoring of conditions simpler, less invasive, and more portable.
TAP INTO TOOLING AND PRECISION To miniaturise devices, components must become smaller. This signifi cantly increases the complexity of the manufacturing process and requires equipment, tooling and processes that promote a high level of precision. Additionally, experts should Design for Manufacturability (DfM) to shorten time to market, improve future production yield and ensure delivery of product in high volume.
Typical moulding tools and processes are not usually capable of providing the quality and precision needed for miniature devices. Therefore, it’s important to partner with a supplier that understands the complexities of micromoulding.
A robust micromoulding process starts with high-quality injection moulding tooling which will determine the quality of the fi nal product. All micromoulding tools, whether producing a plastic or silicone component, require a high degree of precision in tolerances and shut-off surfaces to precisely control the fl ow of material into the mould cavity. To achieve this level of quality, high-precision machining equipment is needed for mould fabrication.
In micromoulding processes, it is also vital to use equipment capable of injecting small doses of material into the mould cavity. Material doses or shot sizes of less than 1.0 grams are typical for these micro-sized components. Shot size control is critical for low viscosity Liquid Silicone Rubber (LSR) and is, therefore, a major focus with micromoulding equipment.
Without tight control over shot size, 5 to 10% of micro part cavity volume can easily “leak” from the mould cavity. This produces excess material around the perimeter of the part, commonly referred to as fl ash. In a larger, more typical sized moulded component, the size of a hand for instance, a small amount of fl ash is acceptable and can be removed in a secondary process. However, when a part is smaller than a pin head, the fl ash could be as large as the part itself, and fl ashless production becomes obligatory. This requires precision tooling, smaller injection units, better control of heat zones, and greater precision of injection units.
When working with a highly capable manufacturer of micromoulded components, more advanced capabilities, such as multicomponent injection
moulding, also commonly referred to as 2K, 2shot, or 2C LSR, are ideal. Involving the simultaneous injection of LSR in combination with technical plastics, this highly advanced technique allows the combination of parts within an assembly into a single integrated component, eliminating potential assembly failures and dead space in which bacteria can breed. However, it requires sophisticated tool and process engineering.
PUTTING VALUE IN VALIDATION In addition to high-precision moulds and equipment, robust process validation and measurement methods are also critical to ensure miniaturised components are manufactured within specifi cation. Validation of micromoulded components is challenging due to process control complexity and diffi culty in measuring, handling, and inspecting small features. For example, micromoulded parts are so small, static can literally cause the parts to fl y away during handling. Therefore, special handling and static-mitigation devices are necessary throughout the manufacturing process.
Automated grippers are generally too large when demoulding extremely small silicone parts, while ejectors are not suitable for silicone parts regardless of size. This is because of silicone’s propensity to fl ow into the clearance of an ejector system. Another alternative is using brushes to remove parts from the mould, but the tiny micromoulded parts stick to the brush itself, rather than release from the mould and “fall” into a container below. The solution is specialised grippers designed specifi cally for microsized parts.
Packaging also needs to be considered in the production process, since standard polyethylene bags are not practical for extremely small parts. The parts will statically stick to the surface of the bag and be extremely diffi cult to remove. Therefore, parts may need to be packaged in small hard plastic containers or on double sided tape, for instance.
Gauge repeatability and reproducibility studies play an important role in ensuring the measurement processes for micromoulded components. These tests measure accuracy of the measurement process and help ensure measurements are repeatable by a single inspector and reproducible by multiple inspectors. As parts or part features and their associated tolerances become smaller, measurement equipment and methods increase in complexity. Methods and equipment must be engineered to achieve minimal measurement error and demonstrate statistical process capability and control.
Experienced micromoulding manufacturers balance the trade-off s between increasing the number of cavities in a mould and the challenges of validating those additional cavities. Higher cavitation in a tool enables increased throughput and potentially lower costs. However, the additional cavitation increases the challenge of tooling and process control, which increases the complexity of validation. It’s also important to include in-process controls that enable components to be individually analysed by cavity.
EXPERIENCE IS CRITICAL FOR SUCCESS The precise nature of micromoulding demands consistency and a deep working knowledge of tooling, equipment, process and material science, and engineering. Experts are needed to understand the challenges and variations that exist in micromoulding to anticipate and mitigate challenges before they occur. Finding a partner with longevity in the medical device industry and a signifi cant depth of capabilities is invaluable for micromoulding.
CONCLUSION Micromoulded parts are highly benefi cial in the healthcare and medical industry because they facilitate development of medical devices to improve patients’ quality of life, shorten hospital stays, and reduce healthcare costs. The requirement for quality and invasive surgical methods, and a larger demographic of ageing people are driving demand for miniaturisation. Device manufacturers should consider the critical elements of micromoulding - tooling, equipment, process controls, knowledge of materials, measurement systems, process and product validation, and overall engineering expertise - and partner with experienced moulders to ensure devices deliver the desired quality, consistency and patient outcomes.
ALEXANDER SCHMIDT AND MICHAEL DEGENER, PRODUCT DEVELOPMENT & TECHNICAL SUPPORT AT COVERIS, HIGHLIGHT THE THREE KEY ASPECTS WHEN DESIGNING SUSTAINABLE HEALTHCARE PACKAGING.
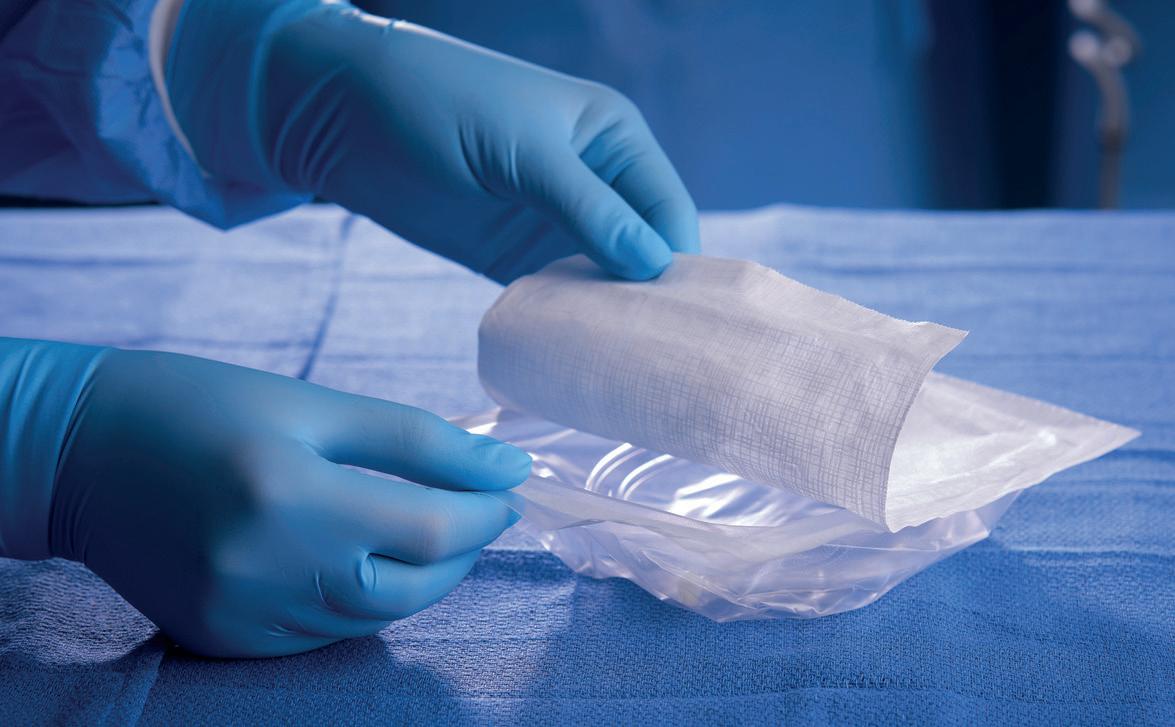
According to the Healthcare Plastic Recycling Council design guidelines, medical packaging producers are obliged to follow specifi c rules when designing packaging solutions for healthcare products. The key mentioned demands include switching to monomaterials whenever possible, allowing easy separation during the recycling process and minimising the use of adhesives and inks. The topic of packaging recyclability is just one aspect of the process, though. Another is the product safety, which must be safeguarded by the optimal choice of available sterilisation methods, and the overall packaging convenience for end-users.
SUSTAINABLE PACKAGING MATERIALS AT THE FOREFRONT
“At Coveris we take sustainability very seriously and focus on developing monomaterial solutions that off er up to 90% recyclability. The unquestionable benefi t of mono structure is the fact that the material can be added to the recycling circle and reused, if necessary, to produce a new material”, explained Alexander Schmidt. A good example are the packaging solutions recently introduced at Compamed trade show: the Formpeel T fi lm, designed for bulk medical devices, and the Flexopeel T pouch fi lm, both based on 100% PE material. Besides their sustainable benefi ts, they also allow easy processing on all conventional FFS lines, low re-shrinking and improved puncture resistance compared to standard PE. These solutions also perfectly fi t with Ethylene Oxide (ETO) sterilisation, as well as X-ray and gamma irradiation. The advantage of monomaterials versus multi-layered structures was confi rmed by Institute Cyclos-HTP, which proved in its research that monomaterial solutions can help save up to 48,000 tonnes of packaging waste.
OPTIMAL STERILISATION FOR EVERY MEDICAL PRODUCT
Once the sustainable packaging material is chosen, the healthcare companies need to select the optimal type of sterilisation to enhance their product protection. Coveris off er packaging systems that provide microbial barrier, long-term stability, good performance during transport and work with three diff erent types of sterilisation: high temperature (steam), ETO gas or irradiation (gamma or X-ray). However, due to diff erent product needs, not every sterilisation type can be used. For example, surgical instruments are usually sterilised using high temperatures (up to 134 degrees Celsius) from steam autoclave. This type of sterilisation is not only environmentally safe but also very cost-eff ective, reliable, and fast. Still, it is not adequate for heat-sensitive materials, like syringes or tubes, which are sterilised using chemicals instead, like ethylene oxide gas. Although it safely eliminates bacteria in low temperatures (up to 60 degrees Celsius), it is a long and expensive process (can last up to 18 hours to complete) and may leave toxic residues than can contaminate the environment. For single-use products like implants, gloves or IV systems, Coveris suggests gamma and X-ray radiation. “This method allows sterilisation even in lower temperatures from 30-40 degrees Celsius, comparable to using gas, takes usually less time to process (up to few hours) and is technically simpler and more cost-eff ective.”, summarised Michael Degener.
CONVENIENCE TAILORED TO INDIVIDUAL NEEDS
An equally important topic in designing the optimal medical packaging is usability, which can be enhanced by adding easy opening features, improving resistance to external factors or simplifying identifi cation of the contents. Additionally, the optimal packaging needs to eliminate potential contamination during its long-term storage. This can be achieved by hermetical sealing that ensures microbial impermeability. Flexopeel fi lm solution, for example, can off er up to 10 years of product shelf life, depending on individual product features. Last, but not least, a truly convenient medical packaging should allow fast identifi cation of the content. “This can be achieved by adding colour indicators, like in our Medipeel pouches and tubes, that reduce the timeconsuming application of labels. An alternative solution is a transparent pouch or bag that allows immediate identifi cation”, added Degener.
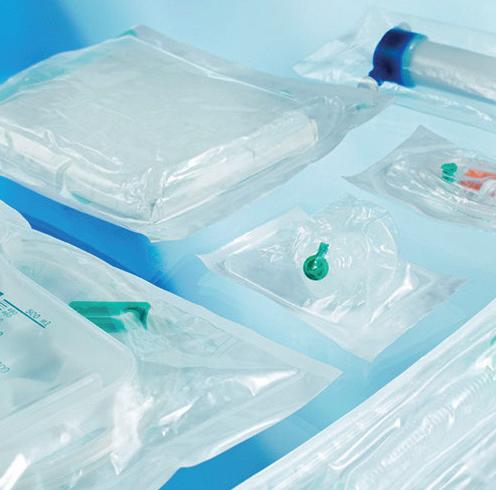