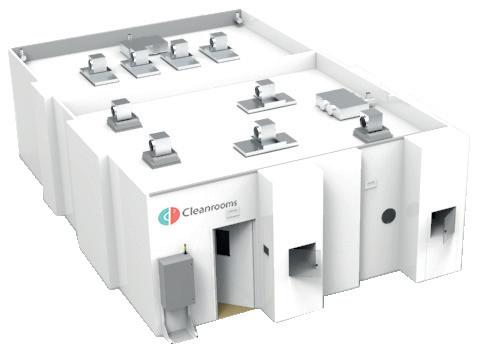
9 minute read
Quick and clean
from MPN EU Issue 58
by MPN Magazine
CONNECT 2 CLEANROOMS EXPEDITED THE DESIGN AND BUILD OF A TEMPORARY MEDICINES UNIT FOR NHS WALES’ NEW CENTRAL INTRAVENOUS ADDITIVE SERVICE (CIVAS).
During the first COVID-19 surge, the UK Government increased CCU bed numbers by 3-4 times. However, it wasn’t possible to increase the number of critical care nurses overnight. With an urgent requirement for specialists to cover more beds, ways in which CCUs could apply lean principles to generate efficiencies were explored.
One of the main activities that takes critical care nurses away from patients is making up their intravenous drugs. The Welsh Government therefore created a central manufacturing capacity to make the sterile injections for critical care to support CCUs. The new CIVAS temporary medicines unit can now produce up to 2,600 syringes per week. The MHRA determined that this process would need to be conducted in cleanroom facilities, so NHS Wales partnered with Connect 2 Cleanrooms (C2C) to fast-track a purpose-built facility, including GMP qualification from DQ to PQ. It was ready for inspection in just six months.
Paul Spark, Pharmacist at NHS Wales, said: “The company pulled out all the stops to begin with at design stage and the same urgency went right the way through the construction phase.”
CONSTRUCTION DURING COVID-19
Increasing the speed and safety of construction was a challenge for C2C’s site lead, Craig Druce, who said: “We brought in specialist subcontractors to install the more complex elements of the builtenvironment, such as the interlocking door and alarm system, at speed.”
With multiple teams working on the same build, greater consideration was given to planning the programme schedule and on-site organisation to ensure teams were kept separate. Working on a split level helped teams stay distant.
C2C used signage and hygiene stations to create a designated buildzone within the NHS facility, restricting access to essential personnel only. Druce added: “The forward planning and more detailed programme schedule supported a faster and more efficient COVID-secure build. We’ll continue to spend more time forward planning throughout 2021 and beyond ... On projects such as this, a shortened installation schedule is of great benefit to our clients.”
GMP QUALIFICATION
The GMP manufacturing environment is designed to diminish the risks inherent to sterile manufacturing, such as viable and nonviable particulates, as well as crosscontamination.
Joan Benson, C2C’s Regulatory Governance and Assurance Manager, said: “It is a GMP requirement that manufacturers control the critical aspects of their particular operations through qualification and validation over the lifecycle of the product and process. Our qualification process is therefore not an independent activity, but an integrated application of GMP practices.”
Design Qualification (DQ) documented and verified that the proposed design of the facilities, systems and equipment was fit for purpose.
Factory Acceptance Tests and Site Acceptance Tests evaluated any bespoke or customised equipment and determined the functionality before and after installation. Installation Qualification (IQ) then documented that the facility and equipment provided what was required.
Operational Qualification (OQ) demonstrated that the cleanroom would consistently perform and maintain the specified conditions, by using a series of challenges such as smoke visualisation testing. For the initial Performance Qualification (PQ), test engineers repeated what had been done at OQ but under load, rather than as built.
Complete system operation training ensured a simple client handover and NHS Wales now has a full O and M manual to ensure smooth operations.
A design for life
ANDALTEC’S EXPERTISE HELPED A MADRID-BASED NURSE DEVELOP AN EASY-TO-USE SYRINGE CONTAINER AND FOUND HER OWN BUSINESS.
Andaltec, the Technological Centre for Plastics, has participated in the development of an innovative syringe carrier device to be used by health workers in emergency and catastrophe situations. This tool, which has been devised by nurse Ana Cintora, is primarily a container that allows for syringes already loaded with medication for immediate or gradual administration to be correctly aligned and ordered.
The syringe carrier is a device unique in the market due to its numerous advantages: it is easy to clean, sterilisable in a microwave and allows for medication to be accessible, without being carried, leaving the health worker’s hands free to perform other tasks. Moreover, it is ergonomic and helps to increase efficiency when injecting medicines. The nurse behind this project came to Andaltec with her initial idea; since then, Andaltec has been involved in the whole development process, participating in the design, material choice and prototype manufacture, as well as carrying out the experimental tests on the syringe carrier’s prototype.
ALL ABOUT CHOICES
Andaltec’s technicians proposed some design improvements, such as placing the device on a belt upon which the container could be attached with a clip, making it capable of rotation, and enabling the possibility of placing it in parallel or perpendicularly to the worker’s body, so that it can also become a useful working table. The device’s inventor has also been advised on the most suitable material choice, polypropylene in this case, as well as on the cost of moulding and serial part manufacturing. Thus, it will be possible to market a low-cost and high-quality device.
Cintora said that she decided to launch this project when she realised there was nothing like it in the market: “Up to now, it was necessary to carry the medication, which needs to be loaded and accessible, in a tray or in our pockets, but carrying syringes in a pocket isn’t safe and the tray implies having at least one hand busy. Besides, the syringe carrier can be cleaned and sterilised after each patient, which makes it a very safe system.” Cintora highlighted how the help provided by Andaltec brought her idea to life, as the Technological Centre’s intervention has enabled a much more complete device. “Andaltec has guided me through the whole process and they have suggested very valuable improvement measures that have been very helpful to develop the product,” she added.
GETTING IT TO MARKET
Once the device is completely developed and its successful industrial scale production has been ensured, Cintora will be establishing a start-up company, for which she is currently looking for investors to help market the product. Her goal is making the product available in Spain during the first semester of 2021. Mari Ángeles Pancorbo, Technician in Andaltec’s Projects Area, added that this project is proof of the way Andaltec can help entrepreneurs turn their ideas into a viable product: “This is a very clear example that R&D investment is indeed very profitable, as we offer comprehensive support that allows entrepreneurs to realise a product ready to be marketed.”
Andaltec has also brought its extensive experience to other products for medical applications, such as a device to avoid tearing during childbirth, developed alongside a researcher from the University of Jaén. The Technological Centre for Plastics has also created 3D models to prepare doctors for surgeries, and is currently executing the PoliM3D Project, intended to obtain active polymers designed for 3D printing in medical applications.
A CUT ABOVE
MARTIN FROST, UK SALES MANAGER, TELSONIC UK LTD., DISCUSSES THE PRINCIPLES AND BENEFITS OF THE CUT’N’SEAL PROCESS, WHICH HAS SEEN A GROWING NUMBER OF MANUFACTURERS INCORPORATING THE TECHNOLOGY.
The Cut’n’Seal process uses ultrasonic energy to cut or punch out a range of thermoplastic and synthetic materials whilst time sealing the edges. The process can also join the individual components to a secondary item. Capable of cutting and joining a range of substrates, the Cut’n’Seal ultrasonic process is a mature, well-established technology used in a number of applications in filtration, garment, medical, wound care and healthcare products.
There are many items manufactured from multiple layers wherein it is essential that the finished item has no frayed edges, loose threads or does not delaminate in use. In certain cases, and in addition to the aesthetics and integrity of the product, there are also instances wherein the ultrasmooth edge produced is an essential attribute for items which will come into close or constant contact with the skin.
The Cut’n’Seal process is capable of meeting all these requirements, which is why the technology is being adopted by manufacturers across multiple inductry sectors.
Examples of where the Cut’n’Seal process has proven to be indispensable include the highvolume manufacture of labels, wound care products, feminine hygiene products and filter pads used in respiratory support machines for patients suffering from sleep apnoea. In addition, the flexibility of the process means it can be incorporated into a wide range of manufacturing technologies.
TYPICAL REEL/REEL FED IN-LINE SET-UP
For high-volume products, the typical configuration would be a reel-fed indexing system wherein pre-laminated multi-layer material is passed between the sonotrode(s) and anvil(s). The individual pads, which have been both cut and sealed, are then pushed through the anvil by pneumatically operated plunger mechanisms and collected in tote boxes, ready for packaging. The skeletal waste of the original material is then fed onto a separate reel on the output side of the machine. This configuration, depending upon product design and reel width, allows for either single or multiple products to be produced in each cycle.
Changeover between product types or shapes is achieved by simply changing over the sonotrodes and anvils, and if required, adjusting the position and/or pitch of the tooling. Telsonic’s Cut’n’Seal technology is capable of achieving cut cycles of between 140/170ms representing a very small part of a machine’s overall process and index time.
PICKED BY ROBOT
The Cut’n’Seal process is also easily integrated into systems where robots are being used. For example, the robot removes the cut and sealed pads from the anvils and loads them into intermediate trays prior to presentation into filter housings further upstream.
Another Cut’n’Seal configuration often employed is that of twin headed systems, but offset sonotrodes and anvils. This utilises wider web substrates where two smaller pads can be produced in a tandem cycle whilst optimising material usage. In a configuration such as this, the reel-fed material is typically between 100-150mm wide and between 100-150gsm in thickness. The typical throughput for a system such as this would be a total of 60 pads per minute, dependant upon material type and thickness.
The rapid rise in the demand for surgical type face masks, initiated by the COVID-19 pandemic, brought with it a significant increase in the the number of UK companies diverting their resources to manufacturing these products using automated systems. Telsonics’ ultrasonic technology with the Cut’n’Seal process is used to produce cut and formed mask types such as K95/N95 and FFP2/ FFP3 variants.
DUAL, OFFSET SONOTRODES AND ANVILS
The quality, consistency and short cycle times of the Cut’n’Seal process, combined with the ability to easily configure and integrate the technology to suit individual applications, are just some of the key drivers behind the increasing uptake. In addition, developments in wound care technology with new materials, new feminine hygiene products, plus the demand for increased production of PPE have together opened up a wide range of new applications for this process, which also adds value by delivering a superior finished product.