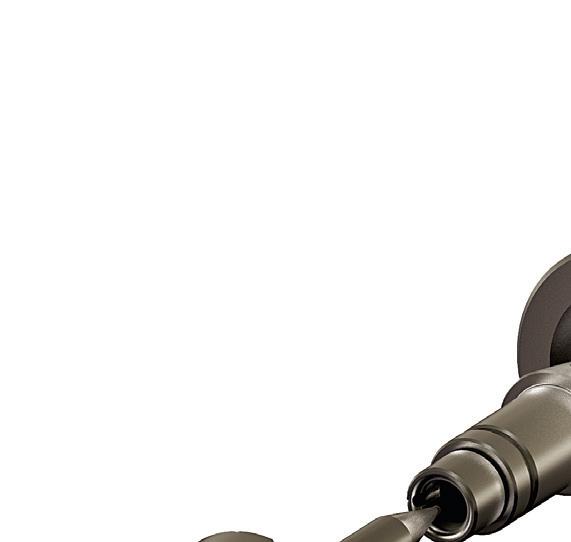
5 minute read
Digital spy
from MPN NA Issue 19
by MPN Magazine
ACQUISITION UPDATE
https://tekni-plex.com
Material science and manufacturing technologies specialist Tekni-Plex Healthcare has acquired precision extrusion manufacturer Johnson Plastic Group (JPG) as part of a strategy to expand the company’s patient care solutions platform.
Located in Mexicali, Mexico, JPG provides complete extrusion solutions into a variety of medical device applications for interventional and therapeutic procedures.
The acquisition expands Tekni-Plex Healthcare’s medical device capabilities and broadens the division’s global footprint. The transaction also brings the company closer to its key customer base in Mexico and the Baja region, as well as leveraging JPG’s expertise across TeknoPlex Healthcare’s entire global customer base and healthcare end markets.
Chris Qualters, CEO of Tekni-Plex Healthcare noted: “The addition of JPG continues to build upon our innovative patient care solutions platform centered on material science and process technologies.”
EXPANSION UPDATE
www.guill.com New extrusion crosshead features patented single-point concentricity adjustment
Guill Tool & Engineering has introduced a new extrusion crosshead that uses micro-fi ne adjustment screws for precise concentricity adjustment. The precision of concentricity reaches 0.008” or fi ner per revolution. This single point concentricity adjustment is a unique Guill innovation for the extrusion of thin-walled and precision ID/OD medical tubing. One adjustment bolt controls 360° of adjustment.
Features of the Micro Medical crosshead include a patented cam-lock defl ector for quick changeovers, with a residence time of one minute at .5 lb/hr material fl ow, optimized usage with extruders measuring ½” and ¾”, and a max die ID of .250”.
In addition, the new crosshead off ers great fl exibility to its users — it accepts both vacuum and micro-air accessories and is ideal for pressure and sleeving applications. Fluoropolymer designs are also available.
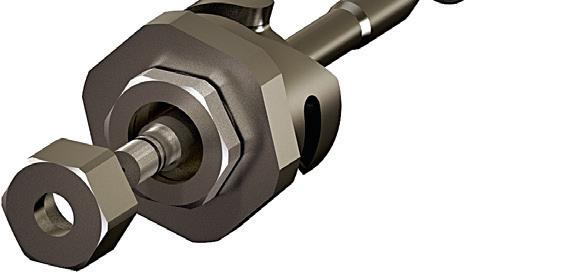

www.raumedic.com
Cleanroom manufacturing expansion on the cards for Raumedic
Medical technology company Raumedic has announced plans to expand the cleanroom manufacturing facilities at its US headquarters in Mills River, NC, by February 2022. The additional state-of-the-art cleanroom will be used for new product lines, bringing in new techniques and creating further job opportunities at the North American headquarters and production facilities.
“Growth is the key word for describing our fi ve years in Mills River,” said, summing up the current situation. In 2016, the ISO Class 7 cleanroom production facilities covering 13,000 sq. ft. were built on an empty fi eld in the Asheville area. Now it is occupied with the business the company has developed.
Raumedic serves international medical device companies distributing insulin pumps, surgical equipment, or catheters, for example. “The advanced equipment and processes that will go into the new space will help us to remain ahead of the curve. With automated assembly cells and robotically augmented molding presses, we are able to produce high-quality medical technology solutions in the mainland US and remain competitive,” explained Martin Bayer, president and CEO of Raumedic.
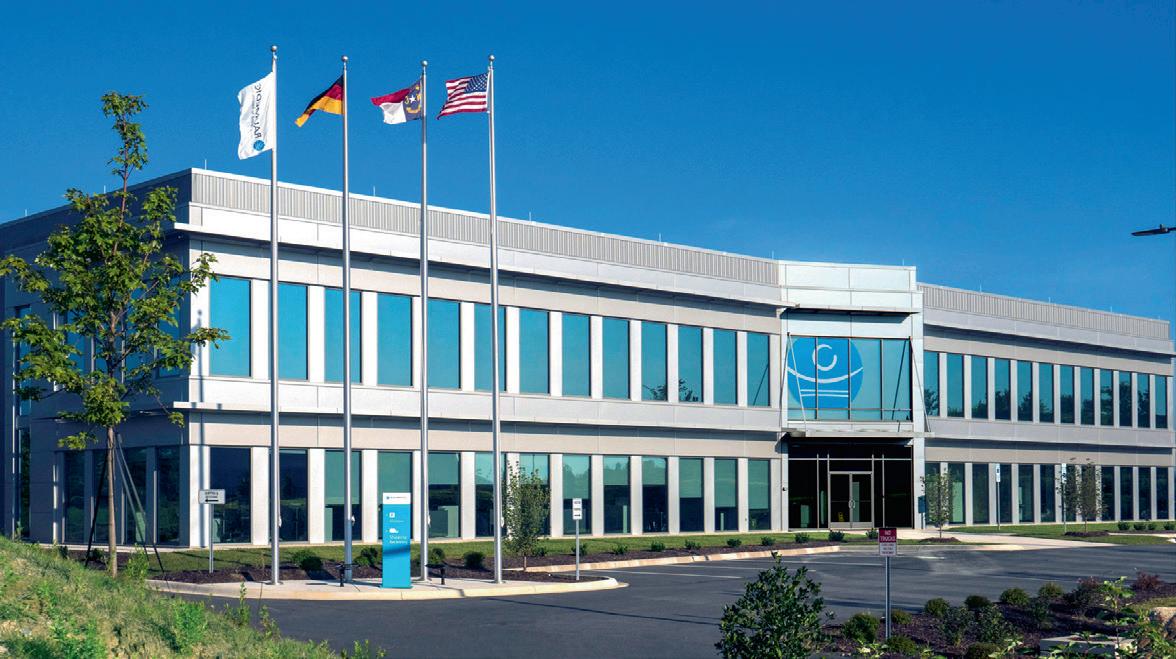
www.dymax.com Autoclave-resistant adhesive that also protects electrical components
Rapid curing materials and equipment specialist Dymax has extended its MD line of adhesives for medical device assembly applications with 1040-M. Designed to be autoclave resistant for more than 100 cycles, the new adhesive offers extremely low water absorption (0.5%) making it ideal for surgical tools and devices that are subjected to numerous instances of sterilization, including autoclave or STERRAD (plasma). This material also works well as an encapsulant, protecting critical sensors and electronic components, where moisture ingression may be of concern. The material cures quickly upon exposure to broad-spectrum UV light and is LED curable at 365 nm wavelength. 1040-M successfully bonds to a variety of substrates including stainless steel, aluminum, glass, PP/PE, and PCB, and is especially suited for encapsulating RFID chips, sensors, and other electronic components found on medical devices, tools, and vials. 1040-M meets the requirements for ISO 10993-5 cytotoxicity, is formulated without IBOA, has a durometer hardness of D60, and viscosity of 775 cP. The product is a solvent free, RoHS-compliant material, making it a “greener” choice compared with one- and two-part solvent-based epoxies currently on the market.
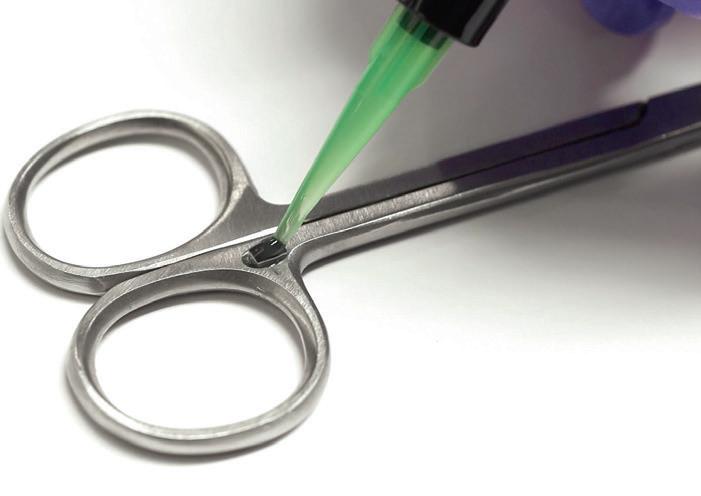
PRODUCTION UPDATE
www.csptechnologies.com
US GOVERNMENT AWARDS APTAR $19-MILLION CONTRACT FOR DOMESTIC PRODUCTION CAPACITY
Aptar CSP Technologies, part of AptarGroup, has been awarded a $19 million contract from the US government to support expanded domestic production capacity for the company’s proprietary Activ-Film technology, which is used to protect and ensure COVID-19 test kit integrity and accuracy.
The company’s Activ-Film technology is seamlessly integrated into diagnostic dipsticks and lateral flow cassettes to protect diagnostic tests from moisture or other environmental degradants that can affect test integrity and result accuracy. The material leverages Aptar’s proprietary 3-Phase ActivPolymer platform technology to provide broad spectrum, custom-engineered protection delivered in a variety of configurations. The technology is formulated to adsorb a specific amount of moisture and other compounds at a customized rate, creating a consistent microclimate throughout the supply chain.
The contract provides for procurement of equipment and machinery needed to increase production of Activ-Film material at Aptar CSP’s Auburn, Alabama plant. Completion of this effort is expected in early 2023.

talking POINT
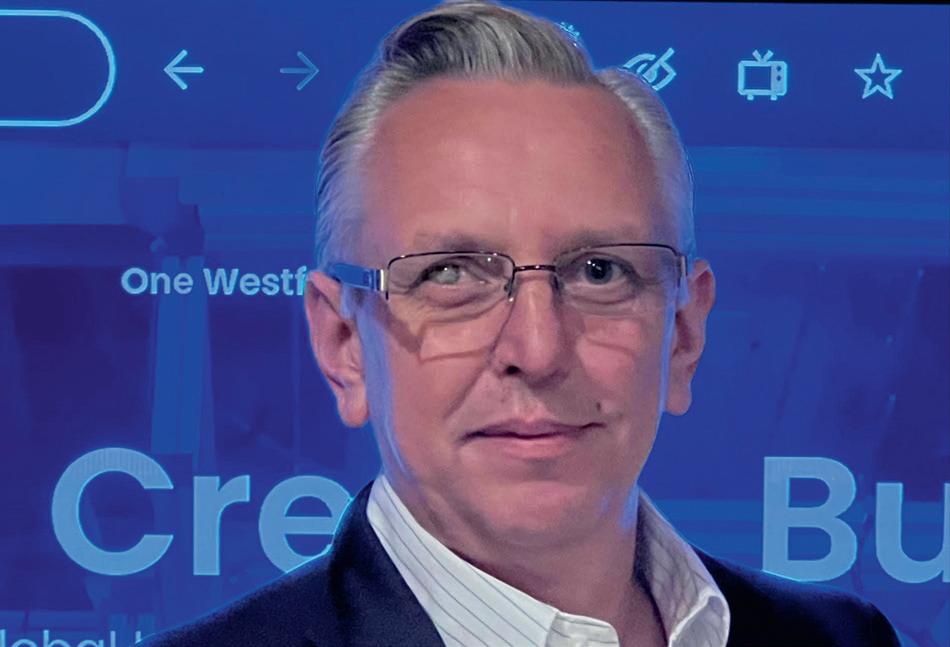
www.westfalltechnik.com Mark Gomulka, CEO, Westfall Technik
As the company’s new CEO, what is your vision for Westfall?
To be the premier contract manufacturer in the medical and packaging space. Four years ago, no one had heard of Westfall Technik. Today some of the world’s largest OEMs take advantage of our fully integrated solutions from design and prototyping through Westfall’s IDG Design Group, to tooling and automation, molding and micromolding, to assembly and kitting. Our passion for this business will continue to drive us forward, and our vertically integrated model will allow for speed-to-market on some of the most complex programs that our customers demand.
What’s new at the company regarding the medical plastics space?
During the past 12 months, we’ve installed over 40,000 sq. ft of medical cleanroom manufacturing space and more than 40 new electric injection molding machines. We’re seeing many more requests for wearable drug-delivery devices — from insulin pumps and insulin monitors to auto-injectors for immunotherapies. Westfall is ready with capacity to meet that demand as our medical customers drive technology into their devices.
How do Industry 4.0 concepts feature at Westfall?
From our ERP to quality systems, we use our cloud infrastructure to manage our business as a whole. From predictive maintenance using smart sensor technologies to a cloud-based quality management system that spans our entire manufacturing eco system, we have developed and connected all the components of our manufacturing operations. We capture the critical points of our processes to make real-time decisions across the entire enterprise.