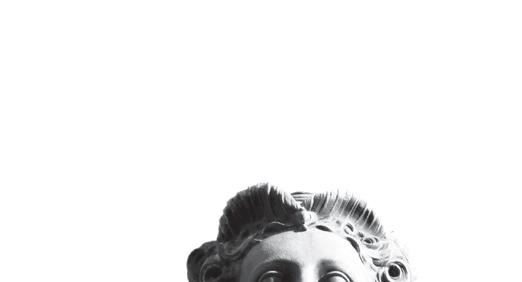
9 minute read
Extrusion
from MPN NA Issue 23
by MPN Magazine
DANIEL MIELERT, HEAD OF PRODUCT DEVELOPMENT FOR INJECTION & DOSING DEVICES AT RAUMEDIC, DISCUSSES THE FUTURE OF DRUG DELIVERY FROM DETAILED COEXTRUSION TO A COMPREHENSIVE SOLUTION
Extruding the TRUTH
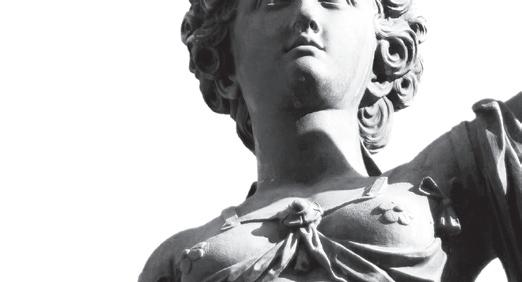

COMPLEX REQUIREMENTS, USERFRIENDLY SOLUTIONS
Process engineering know-how and materials expertise are crucial to any project from the beginning. For the past two years, Daniel Mielert has led a team of eight in customer drug-delivery projects, an important market for the medical and pharmaceutical industry, in part because more than 537 million people worldwide now suff er from diabetes. As human life expectancy increases, so does the incidence of many chronic diseases. In hospitals, nursing care or home care, subcutaneous administration of medications is increasingly used where people need long-term or permanent drug therapies such as insulins, heparins, cytokines, interferons and immunomodulators, EPO or allergen extracts for hyposensitization. Subcutaneous drug administration is considered to have few complications and to be gentle on patients.
A VERSATILE PRODIGY FOR MODERN DRUG-DELIVERY SYSTEMS
Coextruded tubing has a minimum internal diameter of up to only 0.1 millimeter and is indispensable in many drug delivery systems. Depending on the application, it may have layers introduced during manufacturing — a process known as composite tubing extrusion — to improve the functionality and safety of the injection system. Here, the outer layer connects the coextruded tubing to other components of the fl uid outlet such as the needle insertion system, reservoir or pump unit. The tubing and all connecting joints must withstand pressure of up to six bar. The inner layer is inert, thereby ensuring marginal interaction with the drug throughout the product’s life cycle. Properties like these make coextruded tubing an important component of the fl uid outlet, the heart of any drug delivery system. Raumedic not only designs and adapts the tubing for individual systems, it also intelligently combines various manufacturing processes.
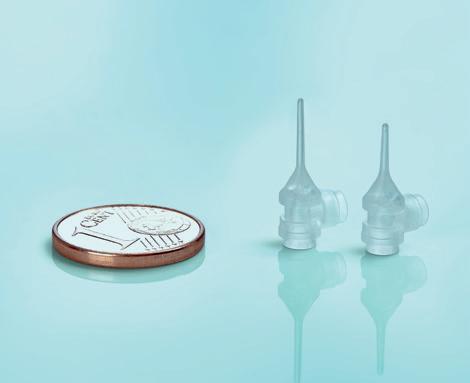
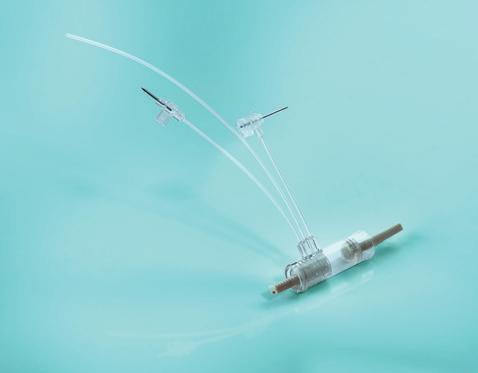
SMART COMBINATION OF PROCESSES AND TECHNOLOGIES
“The complex requirements of modern medical technology, in particular in drug delivery, call for intelligent process combinations,” Mielert says. “Longterm applications, safety and reliability for home-care use, miniaturization and greater user-friendliness all mean challenges in developing and manufacturing drug delivery systems. All the components have to dovetail reliably.” There is customized know-how in every phase of a development project along with the constant pursuit of the optimal complete system — from the fi rst sketch and initial 3D models for rapid prototyping all the way to fi nal specifi cations. “We observe the market and see the diffi culties that can arise when components come from diff erent suppliers and must be assembled into an overall system,” Mielert explains. Often, the components or materials are incompatible. The result can be additional corrections, a need for optimization or even costly design or concept changes. That costs time and money unnecessarily – a powerful argument given rising costs and deadline pressures in healthcare, especially in light of the acute energy debate. “We consider the whole system right from the start: We fi nd individual solutions for every requirement, no matter how complex,” Mielert says. This not only saves time and money, it minimizes risk: Individual components are developed, manufactured and validated by an experienced expert.
INDIVIDUALLY DESIGNED SOFT CANNULAS
Raumedic has demonstrated its expertise in combining technology and materials. This includes integrating soft cannulas into the fl uid outlet of patch pumps. The cannula replaces the classic steel injection cannula and remains inside the patient for the duration of the application, enhancing comfort and drug delivery. With an assembled solution, the highest quality standards for materials, geometry and dimensions can be realized in the extrusion process, off ering possibilities when post-processing extruded tubing to expand the assembly into customized soft cannulas. Alternatively, injection molding reduces the number of steps because both the cannula shaft and the housing are produced from a single mold.
ALEX KAKAD, GLOBAL PRODUCT MANAGER FOR TEKNIPLEX HEALTHCARE, HIGHLIGHTS THE WAYS TO AVOID COMMON PARATUBING ISSUES
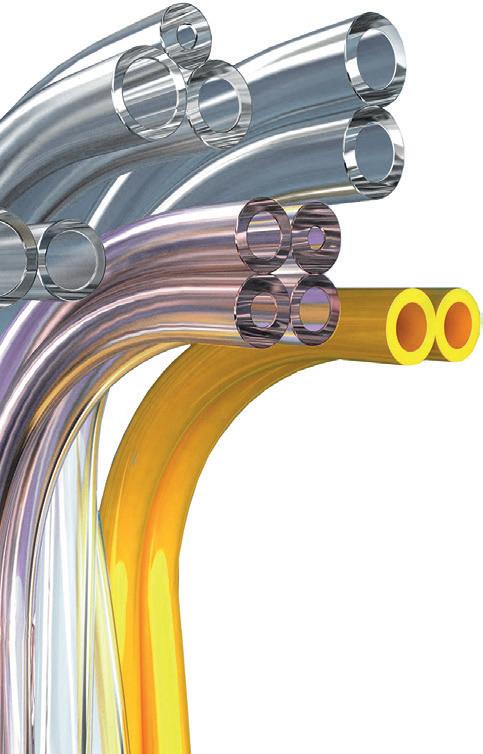
Also known as peel-apart tubing, paratubing entails a set of tubes bonded to remain bundled together until device assembly, patient care, or other pre-determined point of separation. For medical devices, among the more sensitive risks is loss of suction during a procedure. Proper and consistent vacuum levels for fl uid or mass removal are a critical factor in many application areas. The other application factor of high importance is adequate and constant anesthetic or medicinal delivery. Disruption of an anesthetic agent can be painful and even dangerous for a patient, while insuffi cient medicinal supply caused by a tubing line leak could render a procedure ineff ective or even harmful. Considering all this, it is paramount that a paratubing assembly-based solution have a validated, consistent manufacturing process behind a welldesigned and robust product solution.
Let’s explore.
MIXING AND MATCHING Many medical devices must incorporate multiple single-use tube lines, each of which supplies or removes a diff erent fl uid or gas. In addition, some of these devices also require a separate power line to provide a light source. A paratube makes it possible to combine these tubes into a single structure that is signifi cantly easier for clinicians to manage. In this landscape, versioning is the surest path toward safety and success. To minimize risk during medical procedures requiring multiple lines to deliver fl uids, gases, suction and power to the same application space, a custom design may be recommended or even necessary to best ensure proper line connections. Tubes can be composed of diff ering compounds engineered to accommodate the fl uid, gas or suction it provides, and tube ends can be separated to ensure effi cient and secure bonding into connecting ports. Some advanced tubing manufacturers, such as TekniPlex Healthcare, can even produce confi gurations of up to eight tubes in eight distinct colors, bonded together in a single device solution. But of course, matching the right tubes to the right ports isn’t the only challenge associated with paratubes. Several other pitfalls may arise far upstream from patient care, in the production and inspection processes.
SEPARATION ANXIETY Paratube production is far from simple, presenting opportunities for several unacceptable issues to arise. For starters, there’s a “Peel strength Goldilocks Zone” – a sweet spot that must be maintained throughout the manufacturing process to best ensure paratubing effi cacy. On one end of the spectrum, to avoid premature separation it is crucial that tubes maintain a consistent bond, which typically requires a minimum 0.22 pounds of peel strength. On the other end, bond strength must not surpass 1.5 pounds of peel strength at any spot otherwise, mission-critical damage can occur to one or multiple tube lines. There are two distinct bonding methods – thermal and chemical – and various die confi gurations utilized to manufacture paratubes. All setups have their own subsets of challenges that often come to light only when the application moves to full-scale production – a result of inadequate steps toward ensuring product consistency at higher production line speeds. Fortunately, some of the resulting product problems are instantly obvious. Among the more catastrophic issues with paratubing design occurs when the bond strength between two tubes goes beyond 1.5 pounds of pull force. In this scenario, signifi cant portions of adjacent tube walls can stick to one another upon separation, causing improper mating connection. This insuffi cient fi tting attachment adds to the risk of a fl uid path leak or loss of suction in the application. Other issues associated with excessive bond strength are less noticeable but nonetheless vital. A more subtle failure can occur if non-uniform bonding between tubes leads to smaller markings (chatter marks) or void spaces on an individual tube. While large portions of a tube wall sticking are more recognizable and therefore likelier to be caught during inspection, smaller chatter marks are more diffi cult to identify but can lead to process leaks all the same. This outlines the importance of maintaining proper process controls and inline testing to ensure uniform, repeatable, and consistent peel strength, as well as inner and outer diameter tolerancing on individual tubing lines. Such rigorous process controls signifi cantly improve the likelihood that products received during design stages will be representative of those produced at high-speed, full-scale manufacturing.
A COHESIVE SOLUTION Solutions must maintain a consistent bond between 0.22 and 1.5 pounds of pull force – and be able to do so at high speeds. As with many medical device manufacturing scenarios, quality control becomes far more challenging as production scales up and speeds up. For that reason, it is absolutely necessary for paratubing manufacturers to impose a strict policy of full validation for both bond strength and inner and outer dimension (ID & OD) consistency.
avoid premature separation it is crucial that tubes maintain a consistent bond, which typically requires a minimum 0.22 pounds of peel strength. On the other end, bond strength must not surpass 1.5 pounds of peel strength at any spot otherwise, mission-critical damage can occur to one or multiple tube lines. manufacture paratubes. All setups have their own subsets of challenges that often come to light only when the application moves to full-scale production – a result of inadequate steps toward ensuring product consistency at higher
MEDICAL DEVICE COMPONENTS THAT INHIBIT BACTERIAL GROWTH
Vyon porous plastics from Porvair Sciences are the perfect material for fi ltration applications in the healthcare and medical device market.
The tortuous path of Vyon porous plastics make these materials particularly eff ective at bacterial fi ltration and preventing microbial ingress. Manufactured to a variety of pore sizes and thickness, Vyon porous plastic materials can also be used to fi lter out a wide variety of diff erent contaminating particles.
Employing a standard procedure, based upon ASTM F2101, Porvair Sciences can manufacture for OEM partners - Vyon porous plastic fi lters for incorporation into a medical device that off er greater than 99% Bacterial Filtration Effi ciency (BFE).
Porvair Sciences is a leading OEM supplier of pipette tip fi lters that are highly eff ective at inhibiting bacterial growth as well as being fully compliant with FDA, USP Class VI and European Pharmacopoeia statutory regulations. For further information please visit https:// www.vyonporousplastics.com/pipettetip-fi lters/ or see us at Compamed 2022 (Stand 8AF08).
To discuss development of a porous plastic component for your medical device that off ers high bacterial fi ltration effi ciency please contact Porvair Sciences Ltd on +44-1978-661144 or enquiries@ porvairsciences.com.
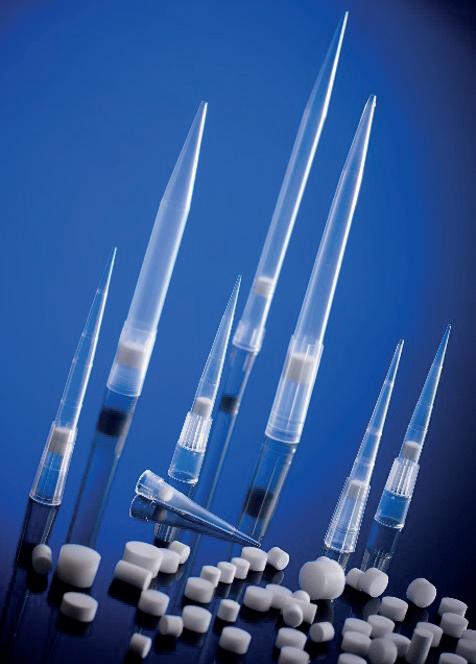
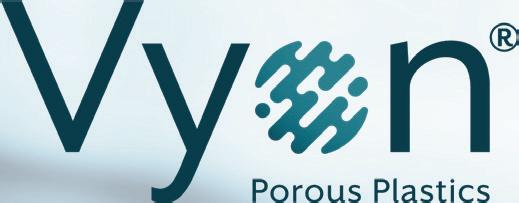
Your Source for Porous Plastics Solutions
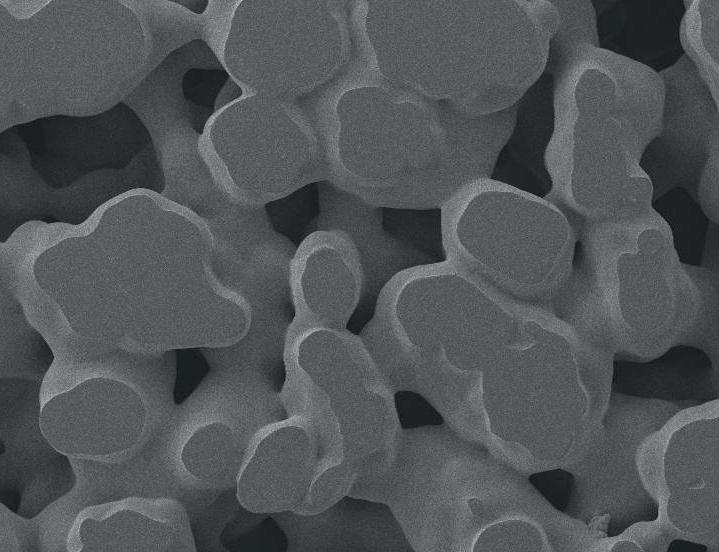
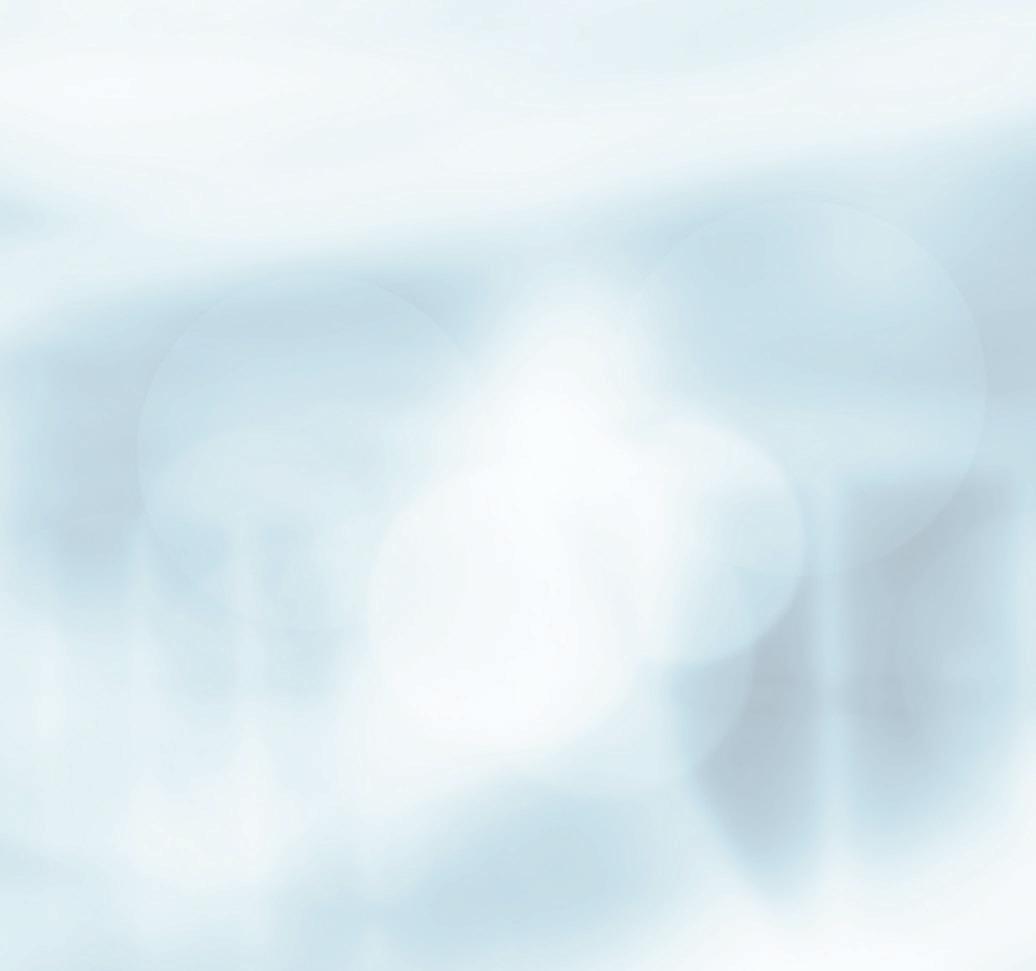
Whether you are looking for porous plastic materials with tight tolerances, a unique property or a complex shape, look no further than Vyon®. Choose Vyon® for precision-engineered, high-quality, versatile porous plastic components for life science and medical applications.
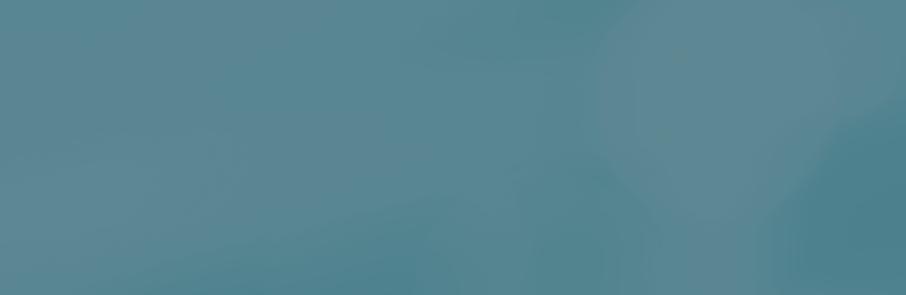

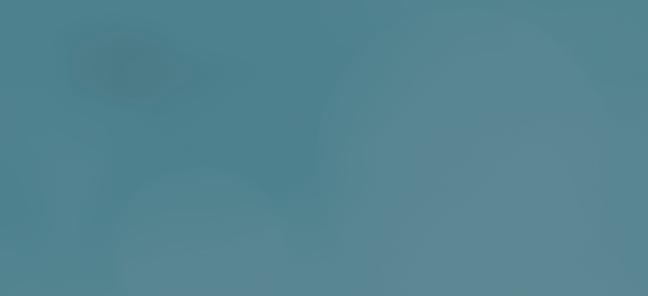
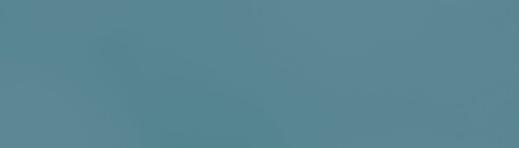
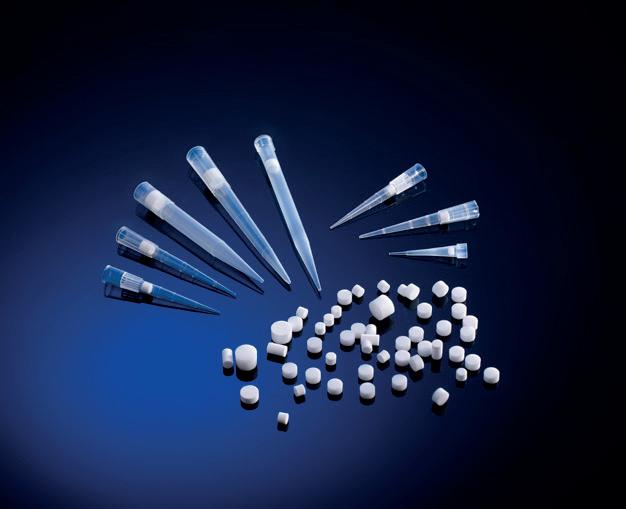
• Excellent edge finish • Cut-to-fit precision • Wide range of shapes & sizes • Available in PP, PE & PTFE Get in touch to discover your Vyon® porous plastic solution. Contact: enquiries@porvairsciences.com Website: www.vyonporousplastics.com
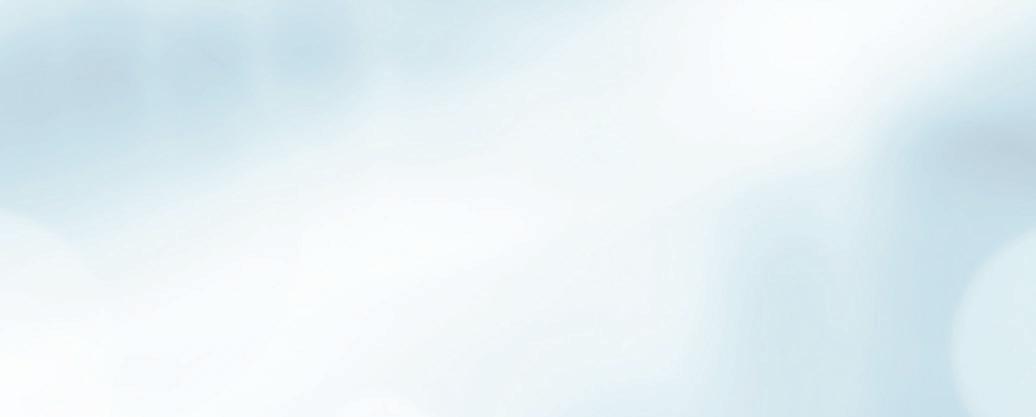