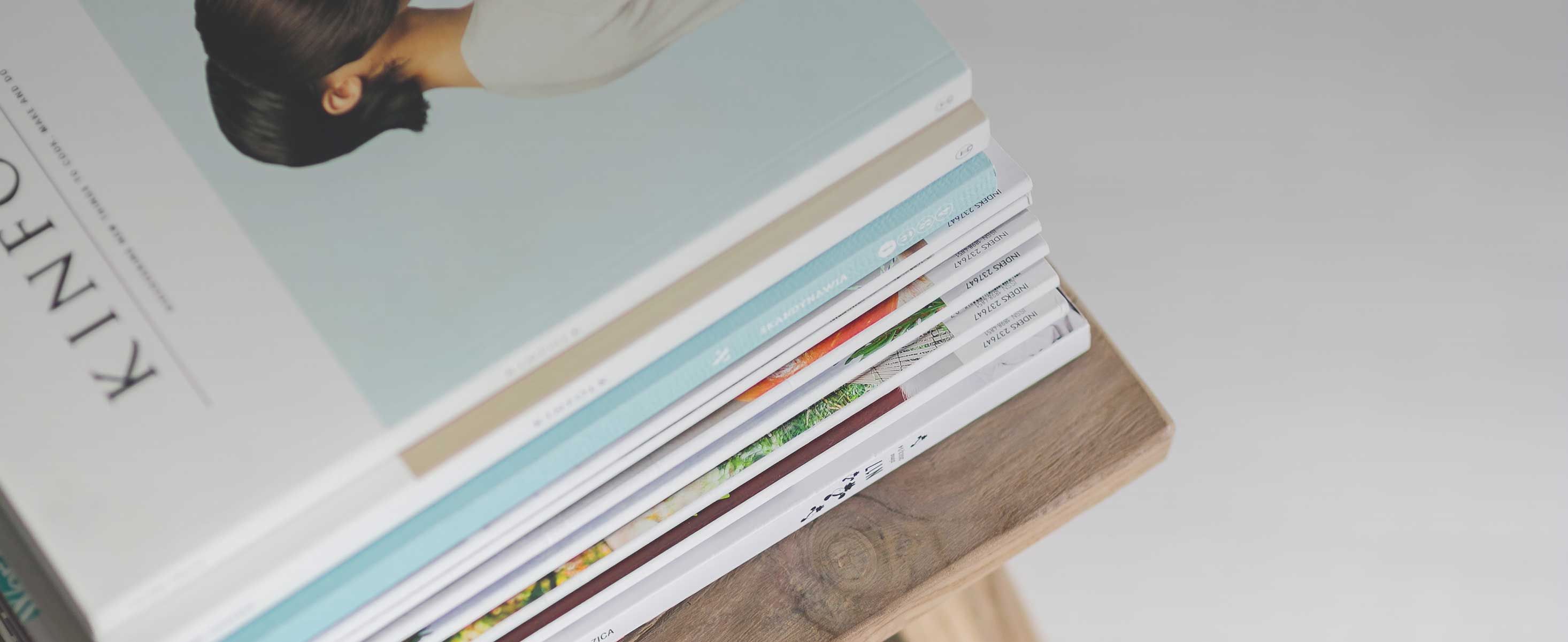
3 minute read
Speed of change
faults in the engine due to water intake or hydro-locking, water getting into mechanical gearing through vents and breathers, to more covert and longlasting issues such as wiring and connector sweating and corrosion. Water does not discriminate where and how it can enter a space. The distinction between fresh water and saltwater damage in flood-damaged vehicles is only in the time it takes to start damaging components. Hence, disputes about ‘only being freshwater damage’ do not hold much significance.
In today’s high-tech vehicle landscape, cars are essentially computers on wheels, filled with advanced technology and controllers to monitor and operate them. While most exterior controllers in engine bays (such as ECUs and ABS) are waterresistant to some extent, they are not waterproof. Interior controllers (BCMs, SRS modules etc) vary in construction, with some being exposed to the exterior and others being sealed. Although sealed interior modules are designed to withstand dust and debris, they are not meant to be submerged in water for any length of time, and the chances that water has entered them if submerged is high.
Even if modules and controllers look dry, the likelihood of them having water inside them is high. The pressure from being submerged in a flood can force water through dust seals, but the water cannot escape once the floodwater has dissipated. This, combined with a few hot, dry days, can lead to internal sweating and condensation,
Glen.mcgarry@mta.org.nz
causing internal components, connectors, and circuit boards to fail rapidly, sometimes within days, not years. Additionally, it is important to consider the presence of pyrotechnic charges mounted low in some vehicles, such as in seatbelts.
Given the potential risks and complications associated with working on flood-damaged vehicles, MTA strongly advises against repairing them. Doing so could put you, the repairer, in a vulnerable position if the vehicle continues to experience faults, which is a likely scenario.
The speed with which we see change and disruption in the collision and refinish space has increased dramatically, as has the technology within our modern motor vehicle.
Technology that was pioneered in exclusive or premiumbranded vehicles would slowly trickle down over years to mainstream motor vehicles.
Take the driver’s-side airbag they were first patented in the early 1950s and introduced in the 1970s as an optional extra. It wasn’t until the early 90s that they became a standard feature in everyday vehicles. AntiLock Braking Systems (ABS) followed a similar 40-year introduction pathway.
The rate that technology is becoming available in every day cars is staggering, it seems like just yesterday that airbags, ABS including traction control were the big improvements. Now Advanced Driver Assist Systems (ADAS), multiple airbags (6-10+), 3600 cameras are all becoming the norm from most manufacturers across their premium, mid and entry-level vehicles.
Multiple Steel Use And The Weight Savings
Larry.fallowfield@mta.org.nz
The 360O camera, first showcased by Nissan in 2007, is available less than 15 years later and is currently in vehicles that sell for under $30,000 in New Zealand. In addition to the technology advancements all original motor manufacturers (OEMs) continue to look at ways of sacrificing weight for improved economy (fuel or battery) and strength, we are now seeing multiple steel and composites making up a vehicle. In the drive to reduce weight, we are seeing third-generation ultra-highstrength steel (3GenUHSS), being used in key structural areas that have a 10-20 percent weight saving. The strength, especially in 3GenUHSS will continue to make the repair process more technical, resulting in an increase of bonding and riveting as a means of returning the vehicle back to pre-accident condition.
If
you undertake work on a flood-damaged vehicle
If faced with the situation where a customer insists on repairing their uninsured, flood-damaged vehicle, MTA strongly advises proceeding with caution and exercising extreme care during any repairs.
It is recommended to present a notice and or a disclaimer for the customer to sign, acknowledging the flood damage and the exclusion of normal warranty claims and future MTA warranty coverage due to water damage and ingress. A notice/disclaimer like this may not offer complete protection but offers a mechanism for the customer to acknowledge that they are aware of the potential risks and limitations associated with repairing a flood-damaged vehicle.
If you have any further questions around the possible implications of working on a flood-damaged vehicle, we recommend you seek your own independent legal advice.
Multiple Steel Use And The Varying Strength
• Steel parts are colour-coded based on their tensile strength in megapascals (MPa).
• High-strength steel (HSS) is defined as any steel with a tensile strength of 340 MPa or higher.
• Ultra-high-strength steel (UHSS) is defined as any steel with a tensile strength of 980 MPa or higher.
• Steel repair and welding procedures vary depending on the tensile strength of the parts involved.
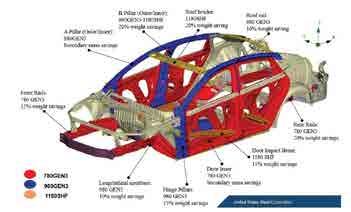