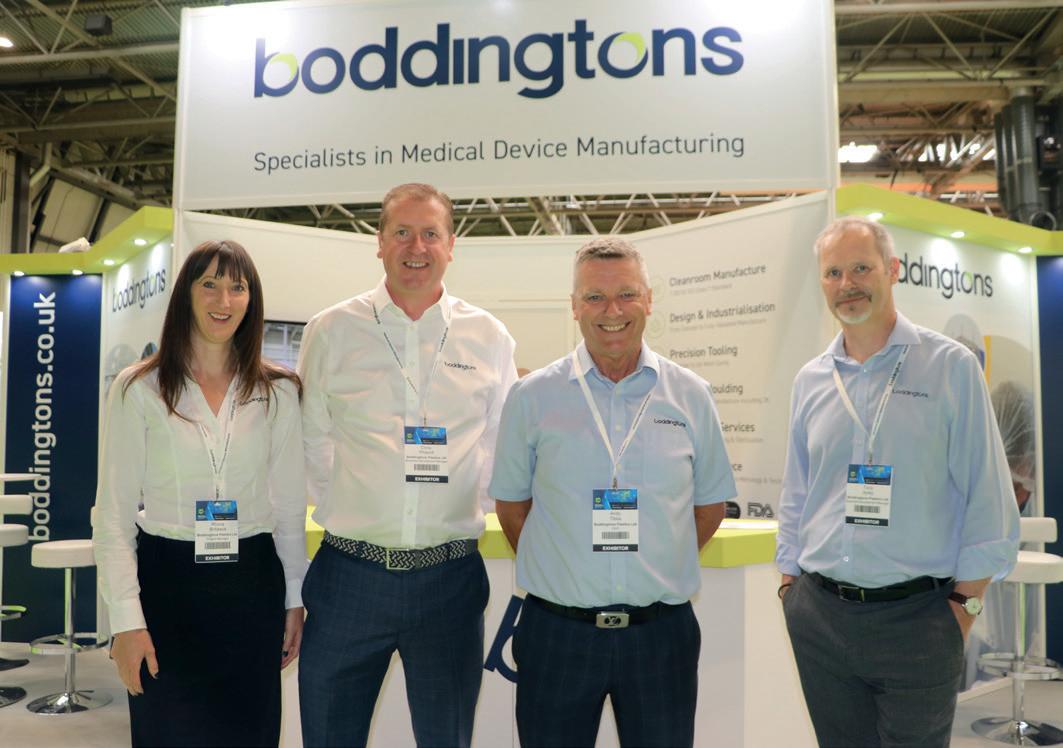
3 minute read
Boddingtons –A firm for all seasons
According to Boddingtons Plastics CEO Andy Tibbs, Med-Tech Innovation Expo 2022 was the company’s most successful exhibiting experience of the year. One year on we catch up with Boddingtons ahead of their return to the NEC.
Last year left Boddingtons with a considerable amount of follow through work to do. “Expo always delivers in terms of quality sales leads,” notes Chris Philpott, commercial and technical manager. “I am pleased to say that – one year on – many of these Expo contacts and enquiries are still bearing fruit. Our stand position at the show undoubtedly set down a marker to the industry - our biggest possible construction dominated the exhibition entrance. We’re going to repeat the formula this year; broadening our appeal to all comers and to customers old and new.”
2022 saw Boddingtons successfully shortlisted for several of the UK’s Plastics Industry Awards: “Our Class 7 cleanroom is the jewel in our crown at the Marden site,” says Philpott, “and we were delighted to have its achievements documented and acknowledged at the PIA awards.”
The successful production of Class I and Class II medical devices including assembly depends heavily on the skill sets of the Boddingtons workforce. The company’s Class 7 Cleanroom training programme was therefore also among the award finalists.
The full operation of Boddingtons’ Class 7 cleanroom means a failsafe and scrupulous approach to standards – an approach that has been developed from the first cleanroom construction which helped attract key business before and accelerated through COVID, is now crystalised and expressed in the pages of the operation and training manual at the company. Cleanroom access is only allowed with a minimum of two full days of training.
“We operate a high-value, controlled and sensitive manufacturing environment here,” notes Philpott, “one that can never be put at risk under any circumstance. Therefore, our operations and our training schemes are second to none.”
These high standards need to accommodate and prevail for all new Class 7 projects in all circumstances. For example, new tooling equipment for vacuum formed trays matched with an upgraded material required close communication, project management and support to allow for sterility testing developed from protocols between Boddingtons QA, operations and the customer’s engineering, QA and regulatory teams.
Another large cleanroom project also necessitated the purchase of seven additional injection moulding machines with a further three on order. This work also resulted in the expansion of the Motan central materials handling feed system at Boddingtons. A second materials direct link was created, ensuring a dedicated material feed line to this part of the cleanroom.
“Cleanroom training will always be constantly updated,” says Philpott. “Our new projects help drive the cutting edge of the Class 7 cleanroom, further modifying and improving the skills sets of our people.”
2022/23 also saw Boddingtons create a new and dedicated cell for a US OEM; one which needed small batch manufacturing at short notice over a spread of some 300 different tools.
“Ultimately, we and our OEM customer wished to drive efficiency of production and flexibility on volume with every moulding produced with us. We recognised that this cell would be different in kind to our volume injection moulding machine business – equipped as it is with a Universal die set enhancing quick change tooling.”
The benefits have been considerable with more material purchased –allowing batch production of several parts using the same materials and colours for as long as required, while also supporting quick tool changeovers.
In January 2023 Andy Tibbs, CEO, said: “We have used the post-pandemic period to grow and consolidate our investments, technical capabilities and services; both for Class 7 cleanroom and non-cleanroom production. In summary, we believe we’re in great shape for whatever 2023 might throw at us.”
In February, a new marketing initiative saw Boddingtons exhibiting at Pharmapack, Paris.
Philpott added: “We are always looking to spin-off new sectors from our core competences in medical and cleanroom-based production. Pharmapack was one of those and it did very well for us –winning us a brand-new order now in production.”
Throughout 2022 and 2023 Boddingtons pursued a sustainable manufacturing agenda as several multidisciplinary teams focused on issues to simplify procedures, raise efficiency, and reduce costs. This resulted in winning the environmental standard 14001.
Philpott commented: “Even in our highly proscribed and process validated medical manufacturing world, it does no harm at all to add in and demonstrate our environmental know-how. More and more of our medical and technical clients are asking for this expertise and we are very happy to supply and support the drive for a sustainable future.”
Boddingtons will exhibit at Med-Tech Innovation Expo on Stand E11.
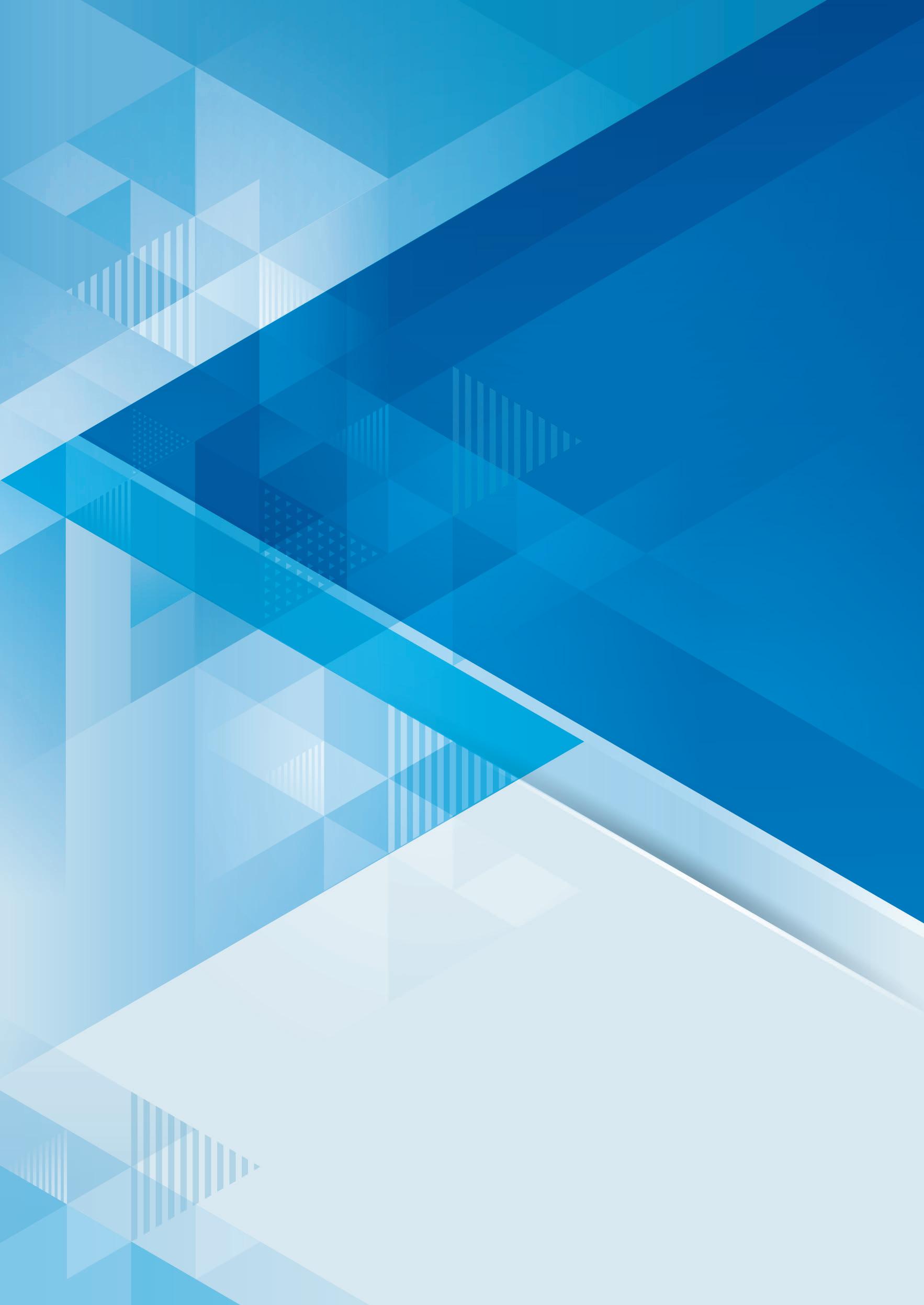