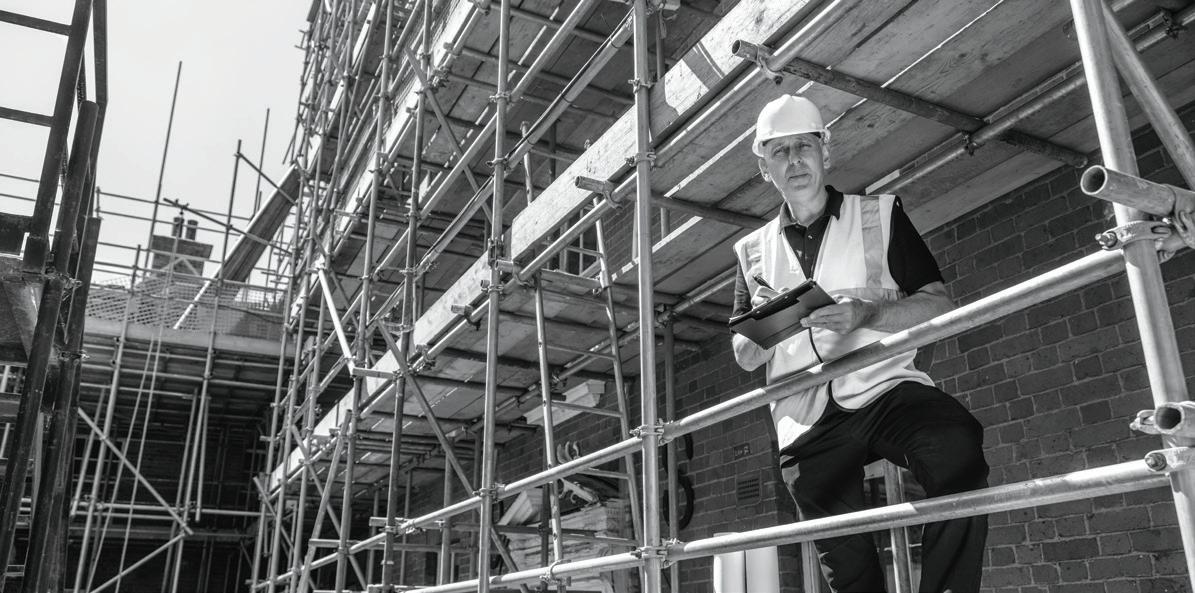
23 minute read
News from the Regions
PHIL HEFFERNAN, SCAFFOLD ERECTION SERVICES LTD
The ending of the latest lockdown on Monday 19 July, albeit with the welcome recognition that there will be long-term Coronavirus risks for some considerable time, should help see renewed and stronger growth in the second half of the year for our Midlands NASC membership.
Advertisement
Most construction sectors including our own with the help of NASC guidance, were able to adopt Covid mitigation during the lockdowns, helping sustain turnover and growth. Coupled with the re-opening of the wider services economy, a more sustainable but moderate growth trajectory could be achievable.
However, there are always hurdles to jump over and now we have interruptions to global supply chains, and all the UK membership are suffering from decreasing availability of materials and massive price increases. Steel tube, boards and fittings have escalated in cost dramatically. Immediately, current shortages are being exacerbated by reviving demand in the US and China as well as a shift in consumer patterns brought on by the global pandemic. For example, the increased demand has seriously disrupted the timber supply from Scandinavia with the obvious consequences we are now encountering.
Furthermore, as well as international freight costs multiplying, commodity prices are also on an upswing, and PPE and consumables are equally as hard to secure and suffering similar price hikes.
Whilst much of this surge can be attributed to the accelerated pace of global economic recovery, the change in demand patterns is also a factor that could affect our members’ ability to sustain turnover and growth.
I would very much hope to be writing a brighter outlook for the latter part of the year. Watch this space!
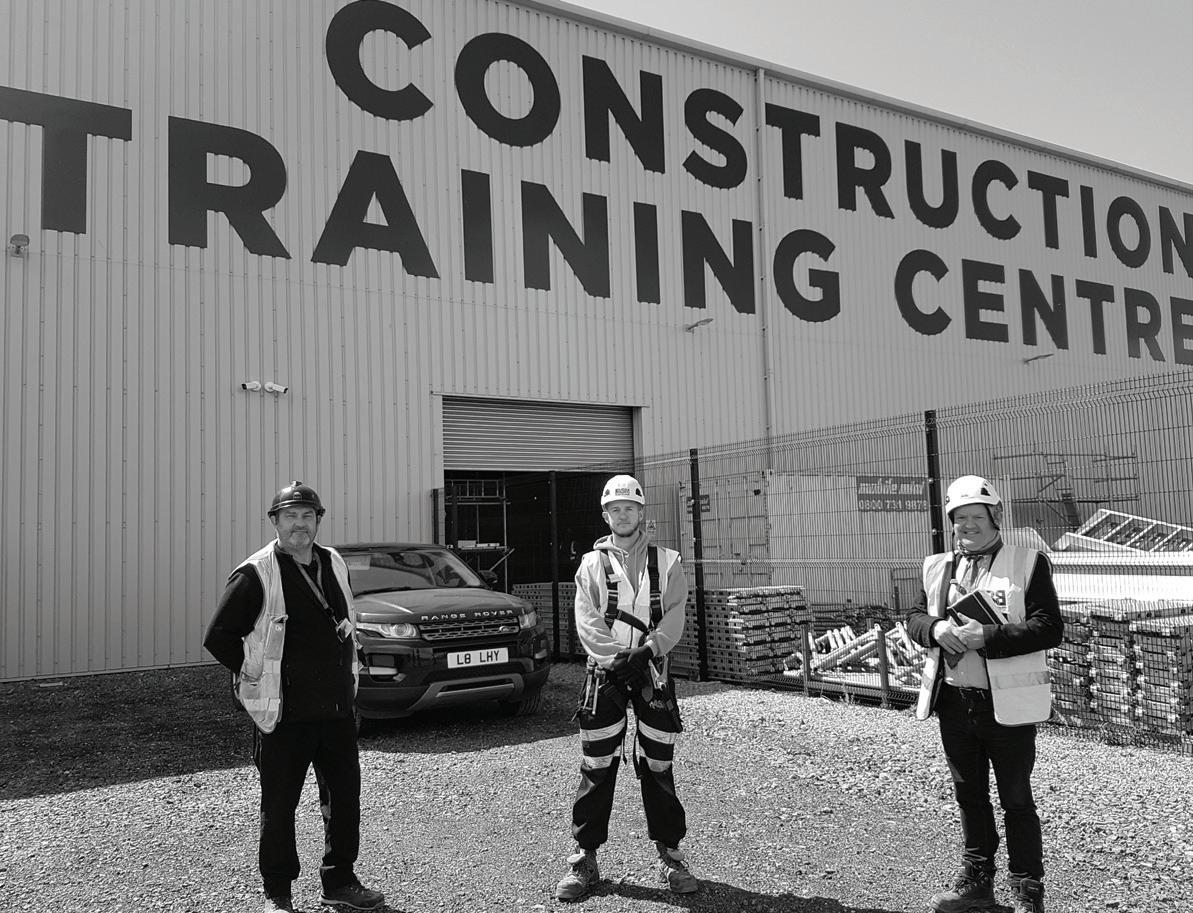
SCOTLAND AND NORTHERN IRELAND
KEVIN FITZPATRICK, BRAND ENERGY & INFRASTRUCTURE SERVICES UK LTD T/A LYNDON SGB
Further relaxation of the Covid restrictions has been great on the one hand as it’s allowed us all some more freedom and time to socialise with friends and family.
On the work front, we continue to go through a time no one has ever experienced before. With excellent guidance notes issued by the NASC on a regular basis we’ve been allowed to safely manage our people and operate on site, granted on a far smaller scale than we previously did.
The full construction sector needs to continue to be vigilant and follow the guidance to avoid disruption.
As we know, the construction industry continued to work through the pandemic which the scaffolding industry supports.
However, with the closing of training facilities during the pandemic and people deciding to change careers or new entrants to our industry declining, the scaffolding industry is now having issues with scaffolders, yard staff, drivers and staff having to isolate or leaving, making it difficult to maintain manning levels on sites. As a supplier, we need to work on ways to attract people to join our industry as there are many opportunities open to all and not just in scaffolding. This could be office work, surveying, engineering accountancy etc. The NASC is aware of this and has put numerous plans in place to promote the industry to jobseekers of all ages and backgrounds.
Another issue we face is the rising prices of both steel and timber with some products doubling in cost compared to this time last year with the supply chain even struggling to give delivery times due to shortages of raw materials.
Why is this happening? Brexit and the pandemic combined seems to be at the heart of it all.
Many people are now suggesting it is also a knock-on effect from the hold ups at the Suez Canal. In addition, people globally are still returning to manufacturing and non-essential domestic work, so it is a perfect storm.
DAVID ANDERSON , ALLEN & FOXWORTHY LTD
Recently I visited the Construction Training Centre, operated by Simian and Southwest Training Centre.
On arrival to site in Weston-super-Mare, I was greeted by Simian’s Rob Wolstanholme who immediately made me feel very welcome. I was due to visit when the centre opened, but due to Covid-19 a delayed visit was arranged.
My first impression from outside was wow! After a short tour of classrooms full of our region’s finest operatives working with their instructors to develop theory skills and knowledge.
It’s been a long time since I was in one of these centres and have to say I was very happy to see how spacious and organised the areas were. The areas allocated to different types of scaffolding operations full of trainees keen to get on with training.
The areas felt safe and zoned off between different structures. The training centre was spotless and very well organised.
I met the centre manager, Adie Holmes, and felt his enthusiasm to produce properly trained scaffolders at different levels of their careers.
I was introduced to a young Part 1 operative called James Bourton who agreed to talk about his training and workplace experience. I was especially pleased to hear him being grateful to his employer for sending him to be trained properly and I also advised him to be loyal and productive to his employer.
With that a rewarding future in our industry will be achieved. James stated he was enjoying the experience and chance he had been given – learning new practical skills and theory of our specific trade that he hoped would lead him to a good career, with more responsibility/training and of course better wages!
Simian and Southwest Training Centre should be really proud of what has been achieved to date at The Construction Training Centre. Being able to deliver the range of courses that they do and deliver them across the South West Region and into South Wales, is a positive move.
Working with NASC and NASC members across the region is an area of importance to all members in the future, further developing these links and providing a service to newly accredited members, be it training, consultancy or apprenticeships, is something that Simian actively promotes.
WALES IN FOCUS
More Welsh firms have remained operational through the pandemic than elsewhere in Britain, meaning increased orders for scaffolding and more training and apprenticeships opportunities. Wales is thus well-placed to play a leading role in the UK’s post-Covid economic recovery.
The £1.5 million CWIC Scaffolding Academy, based in South Wales, is a fully accredited centre that has invested £150,000 to support the Welsh scaffolding industry with fully funded COTS, CPD and Part 1 courses.
Currently they deliver up to CISRS part 2 training, with CISRS advanced scaffolding accreditation due in November 2021.
INCREASING SCAFFOLDING SAFETY
THE NASC HAS PUBLISHED ITS MOST COMPREHENSIVE ANNUAL SAFETY REPORT
The 2021 Safety Report shows NASC Contractor members, employing more than 16,000 operatives collectively, reported just 81 incidents in 2020, the second lowest figure recorded. This means that 99.5% of NASC member-employed operatives went through the year accident and injury free. There were no operative fatalities, for the eighth consecutive year. For the latest report, the NASC collected more detailed accident information from its full Contractor members than ever before. This enabled the NASC to identify a number of trends, causes of accidents and injuries, and the operatives that are most susceptible to injury – by role, age and size of employer. These findings are summarised on the next page.
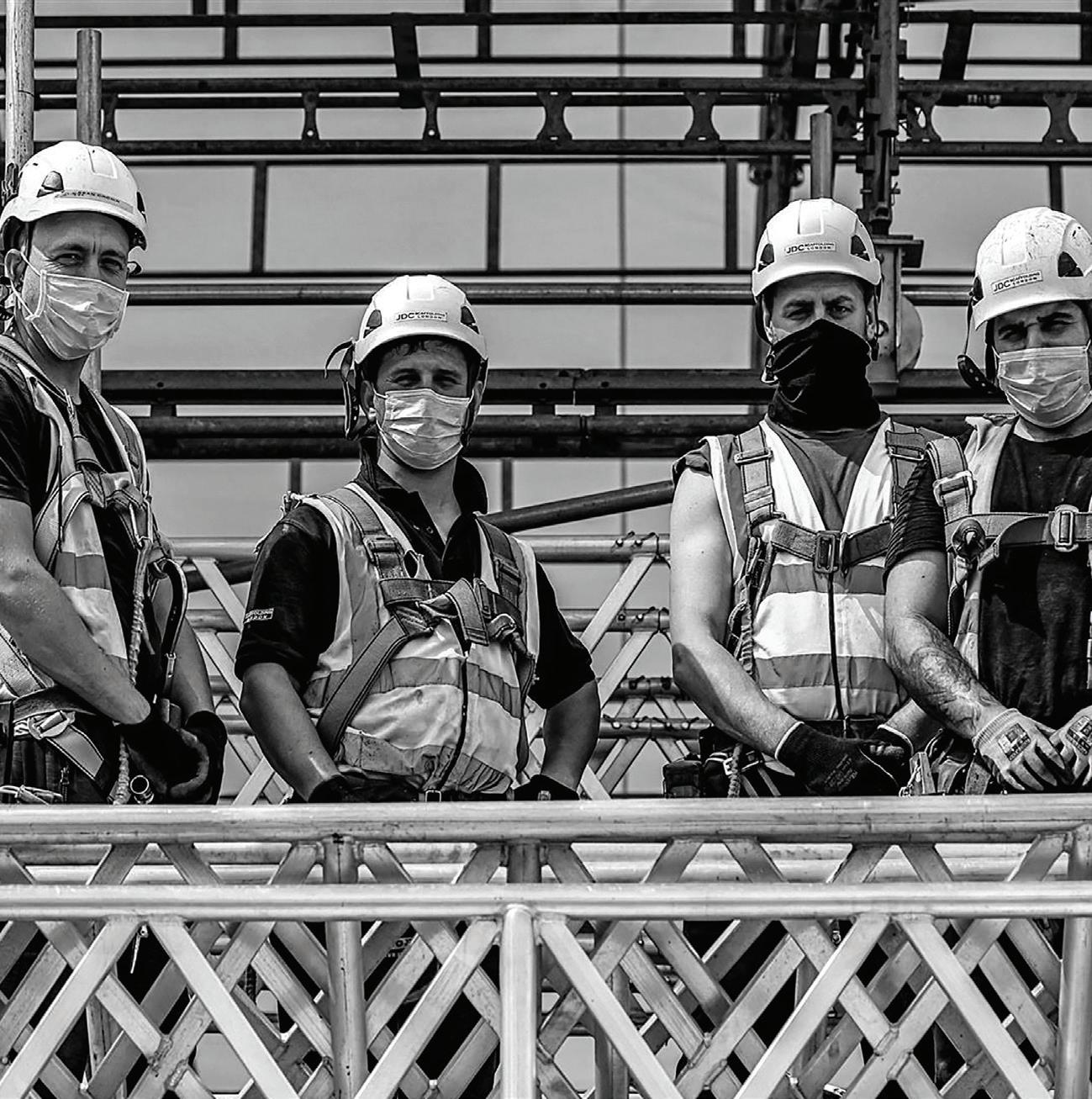
1: SLIPS AND TRIPS ON THE SAME LEVEL IS THE MOST COMMON CAUSE OF INJURY
31 of the 81 accidents reported were slips and trips on the same level.
More than half of these incidents (17 or 55%) were due to human error with the operative not taking care of their working environment. Six (19%) of the incidents were due to poor site housekeeping (holes and obstructions such as waste materials).
A further six (19%) were due to poor ground conditions (uneven surfaces).
The operatives most prone to these injuries fall into age ranges of 21-30 (13 incidents, 42% of the total reported) and 41-50 (10, 32%). The majority of incidents were suffered by operatives working for Small companies (with between 21 and 50 operatives). The 29 incidents these companies recorded represent 35.8% of all incidents seen in 2020 despite the 3,104 operatives employed by these members only representing 19.3% of the total NASC member operative workforce.
Small Medium (51-100) company operatives suffered 23 injuries (just over a quarter of the total) despite their 2,669 operatives representing only 16.6% of the total workforce. Conversely, there were only six injuries reported by Large members (1,001+ operatives), whose 4,840 operatives make up 30.1% of the total number of NASC operatives.
Armed with these findings, the NASC’s Health & Safety Committee is developing a number of resources aimed at reducing incident figures.
This includes the production of two new A2 site posters; SG6 Manual Handling in Scaffolding Operations and SG31 Management of Slips and Trips.
The Committee is also updating the H&S Toolbox Talk Suite – available for free download via the Members’ Area of the NASC website – and updating guidance such as SG6 and SG20 Access and Egress from Scaffolds.
Plans are also being developed to engage with Small Contractor members to try to establish reasons why they may have accounted for a disproportionate percentage of the recorded incidents and what additional support measures could be created to lower this number.
On the Safety Report as a whole, Robin James, NASC Managing Director, said: “The 2021 Safety Report shows NASC Contractor members continue to work to the highest standards – with just 81 incidents reported. It should be remembered that during 2020 members were faced with challenging Covid-19 related working conditions, with operatives forced to significantly change the way they worked on site.
“Members rose to this challenge, not only continuing to operate wherever possible – in line with Government guidance – but also ensuring safety standards were not compromised.”
Lynn Way, NASC President, added: “Whilst we’re proud of the headlines figures contained within this year’s Safety Report, this publication is intended to be much more than just a line in the sand, an annual yardstick to measure general safety success against previous years.
“It is also a way in which we can learn why incidents occurred with a view to developing ways in which to reduce them – benefiting both
NASC members and the wider scaffolding and construction industries.
“To support this endeavour, this year we changed the way in which we gather accident information from NASC members. As a result, this year’s analysis is boosted by a more defined and detailed set of accident returns. This extra information has enabled us to delve much deeper into the 81 incidents reported, identifying potential causes and trends hidden beneath the figures and making recommendations that we hope will lead to safety improvements throughout the industry.”
2: NO DECREASE IN TOTAL FALLS FROM HEIGHT
There were 13 falls from height in 2020, up 1 from 2019. However, how this total was reached differed greatly from year to year. In 2020, there were five falls from 4m+ (up from 1 in 2019) and eight falls from under 4m (down from 11 in 2019).
These incidents caused operatives to be absent from work a total of 1,175 days. The falls from 4m+ related to operatives not working to SG4 Preventing Falls in Scaffolding Operations (2), a ladder (1), collapsed walkway gantry (1) and collapse of a car park floor (1).
The cause of the under 4m falls include operatives loading and unloading materials from vehicles and trailers, losing their balance while erecting and dismantling scaffolding and losing their footing on ladders.
3: THE 31-40 AGE BRACKET SUFFERED THE MOST FALLS
Nine of the 13 falls from height were suffered by operatives in the 31-40 age bracket, equating to 69% of all incidents. Three of these incidents occurred above 4m.
Young operatives aged 16-20 accounted for two falls while the 21-30 and 41-50 groups suffered a single fall each.
4: AGE COULD BE A FACTOR IN CAUSES OF INJURIES
The highest number of injuries by age were suffered by operatives aged between 31 and 40 (25), closely followed by both the 21-30 and 41-50 brackets, both 21. The 31-40 group’s incidents were split fairly equally across falls, manual handling operations, work equipment and slips, trips and falls on the same level.
However, the accidents recorded by the 21-30 and 41-50 brackets were much more concentrated on slips and trips on the same level; accounting for 13 of the 21 (62%) injuries suffered by the 21- 30 group and 10 of the 21 (48%) injuries suffered by the 41-50 group.
TO READ A COPY OF THE NASC 2021 SAFETY REPORT VISIT THE NASC WEBSITE AND CLICK INFORMATION AND THEN SAFETY REPORTS. HARD COPIES ARE ALSO AVAILABLE UPON REQUEST. EMAIL NASC MARKETING MANAGER SIMON ROBINSON VIA SIMON.ROBINSON@NASC.ORG.UK
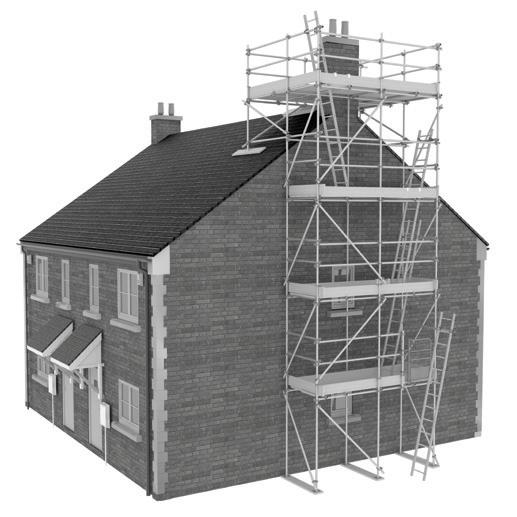

TG20 TAKE UP STRONG
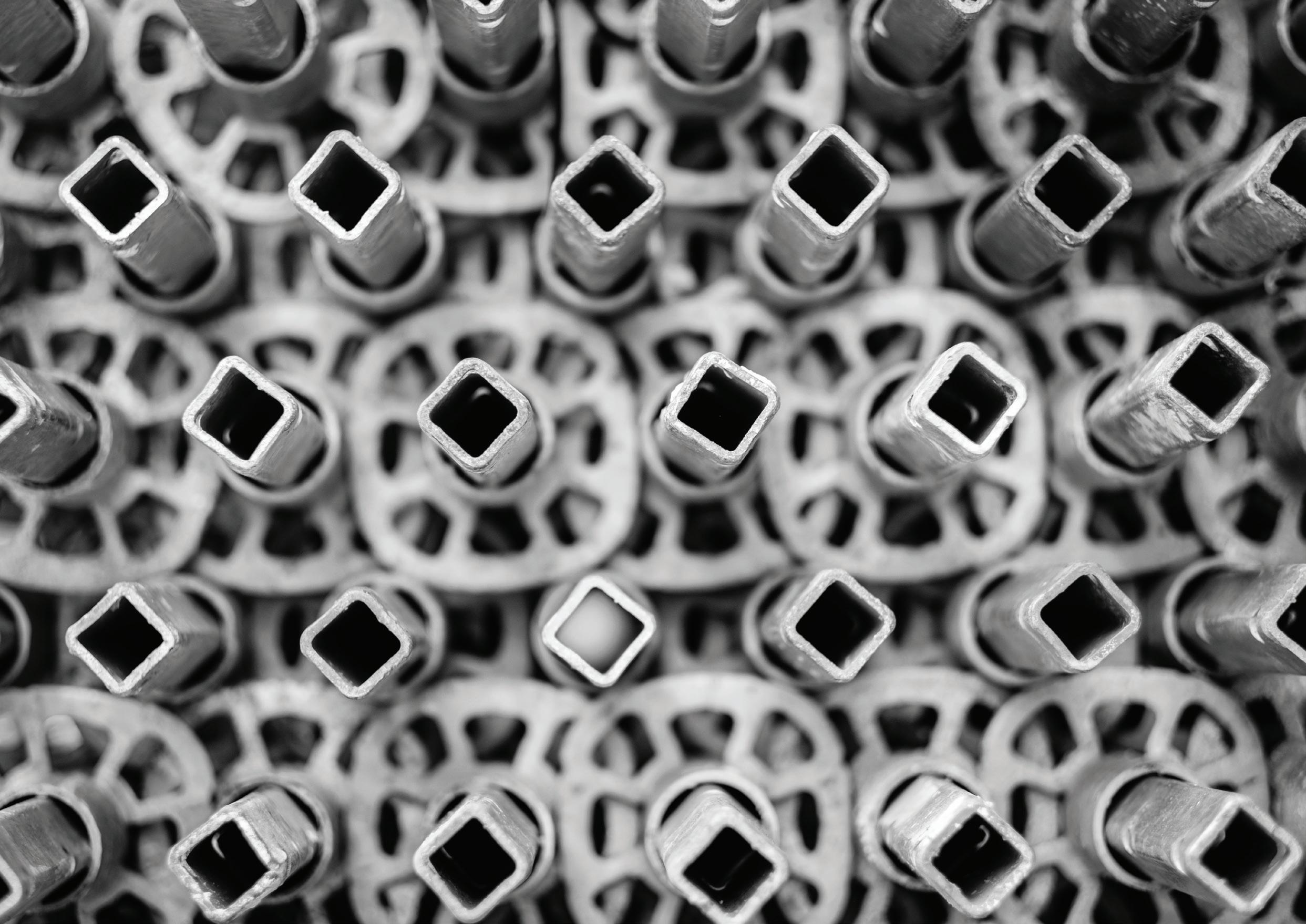
MORE THAN 1,300 USERS ACCESSED TG20:21 VIA THE NASC E-PORTAL IN ITS FIRST THREE MONTHS OF OPERATION, NEW DATA HAS REVEALED
Statistics provided by CADS, which developed and manages the updated and extended software on behalf of the NASC, shows 1,383 unique users registered for TG20:21 between April 12 and July 31.
Download data shows these licence holders generated 21,817 TG20:21 compliance sheets during this time – equating to nearly 200 per day.
Independent scaffolds were the most popular in this period, with 13,652 downloads (63% of the total), followed by free-standing tower scaffolds (1,587) and external birdcage scaffolds (1,573) – a new addition to TG20.
A full break down of downloads by type can be seen below.
SCAFFOLD TYPE COMPLIANCE SHEET DOWNLOADS
Chimney stack scaffold
External birdcage scaffold
Free-standing tower scaffold
Independent scaffold
Internal birdcage scaffold
Lift shaft tower scaffold 877
1,573
1,587
13,652
1,566
396
Mobile tower scaffold 376
GUIDES IN STOCK SOON
Hard copies of the TG20:21 Operational and Design Guides will be in stock shortly. A free copy of each will be sent to all Full members. The TG20:21 User Guide is also available to buy via the Guidance page on the NASC website.
Digital versions of both the Operational and Design Guides can be accessed via the NASC ePortal.
TG20:13 SUPPORT TO END
Technical support for TG20:13 will be withdrawn from Tuesday 12 October – six months after TG20:21 was launched.
From this day onwards it will no longer be possible to activate, move or reset a licence.
The online wind map functionality will also be removed from TG20:13. For now, users will still be able to produce compliance sheets for scaffolds that do not use the wind map and it will still be possible to use the simplified ‘offline’ wind map.
Those wishing to continue to produce TG20 compliance sheets with data drawn from the online wind map function will need to purchase a TG20:21 licence, available in one-, three- and five-year subscriptions.
The five-year subscription, which costs 20% less than buying a one-year subscription and renewing each year, is a limited-time offer so users are encouraged to buy now to receive this saving.
The TG20:13 eGuide software is being formally withdrawn as the software platform it was developed on, Adobe Air, is no longer supported or maintained by Adobe.
During the lifetime of TG20:13, it has been necessary to update the software when third party platforms that TG20:13 is reliant upon, such as Google Maps, were changed.
After Tuesday 12 October, no further updates to TG20:13 will be made.
CONSTRUCTION INDUSTRY CONSULTATION
NASC MEMBERSHIP CRITERIA WORKING GROUP ESTABLISHED TO REVIEW MEMBERSHIP REQUIREMENTS
To borrow a line from the Marketing Committee, the NASC “sets the standard for scaffolding in the UK”, going to great lengths since 1945 to lead our industry and promote best practice wherever possible.
We believe this has worked in regards to the industry standards we have championed, like CISRS, SG4 and TG20, which have been widely adopted across the industry.
Main contractors continue to prefer and specify NASC members to supply their scaffolding requirements, and it is generally accepted that NASC members provide a safe and competent scaffolding service.
Being part of the NASC, all full contracting members are empowered to share our commitment to safety and quality. But how does the NASC quantify and assess such values?
Currently we do that through assessing applicants – requiring them to meet predetermined minimum criteria as laid out in the membership application process, which has evolved over the decades through paper and physical audit.
However, could we do better? Have the current criteria drifted out of date? Are they fully aligned with the current direction of the construction industry?
I believe the NASC should speak for all of the scaffolding industry, from large multinationals to the small family operated firms, and to do that we have to be engaging with our industry and clients, and focused on the ever-changing times we are constantly facing.
However, determining how best to deliver on this is a tricky proposition, and this is why we’ve created an NASC Membership Criteria Working Group, of which I am proud to be Chair.
Our working group has set out on a major research project, where we are engaging with the wider construction industry, consulting NASC members, non-members, and main contractors across the UK to gain a better understanding of what you and they think of the NASC, what works and doesn’t work for you and them, what we do right and just as importantly what we can do better.
I look forward to sharing this research with you in the near future, pinpointing areas we can focus on and delivering meaningful changes that further strengthens the standing of the NASC and its members in the UK construction industry.
By Wayne Connolly
NASC Audit Committee Chair

HIRE, SALES AND MANUFACTURING COMMITTEE UPDATE
PRODUCT PURCHASING GUIDELINES SUITE EXPANDED
Two new purchasing guidance notes have been added to the PG suite - PG8:21 Purchasing Guidelines on Ancillary Scaffolding Components and PG9:21 Purchasing Guidelines on Scaffold Ladders.
PG8:21 provides guidelines for those looking to source ancillary scaffolding components such as girder couplers, flange clamps and non-timber scaffold boards, while PG9:21 offers purchasing guidelines for scaffold ladders required to provide access and egress within scaffolds.
As ladders manufactured to BS EN 131-1:2015 + A1:2019 are generally unsuitable for use on scaffolding, PG9:21 provides the required specification for scaffold ladders.
PG publications 1-7 cover core scaffolding products, for which NASC Code of Practice (CoP) product audits exist. The committee is now looking at possible subjects for further guidelines.
PG8:21
Purchasing Guidelines for Ancillary Scaffolding Components
Updated August 2021
1. INTRODUCTION PG9:21
Purchasing Guidelines for Scaffold Ladders
Updated August 2021
This guide considers ancillary scaffolding components that are widely used in the UK but are not specifically covered by other NASC guidance.
Overview
It is recommended that all components used on scaffolds that could conceivably be expected to carry load are suitably tested and/or calculations carried out to ensure that they are suitable for their intended use. Although some scaffolding components are referred to as “non-load bearing” most, if not all, will be required to support some sort of load, even if this is predominantly wind load (e.g. board clamps or roofing couplers). This guide aims to provide advice to engineers, buyers and component manufacturers regarding the recommended safe working loads of components and testing requirements, where applicable. The specified data can then be used by scaffold design engineers and NASC contracting members to better ensure that all components incorporated in scaffolding structures are fit for purpose.
Materials
Where components are designed to connect to scaffold tubes, the tube should be TG20 compliant (i.e. BS 11391-1:1990, BS EN 39 Type 4 or BS EN 10210-1:2006) and where strength or stiffness is required, the components shall be made from materials specified in BS EN 12811-2:2004 or from steels with equivalent mechanical and chemical properties.
INTRODUCTION
BS EN 131 is now the single British and European product standard covering most types of portable ladders and steps, for use throughout the UK. This replaces BS 2037, BS 1129 and previous versions of EN131. The new standard incorporates two classes of ladder, ‘Professional’ and ‘Non-Professional’ of which only ‘Professional’ class should be used in the workplace. The new standard provides ladders with more strength and durability than previous specifications (see below) but requires that all ‘leaning ladders’ longer than 3.0m, must also be wider at their base to provide more stability when in use. Unfortunately, this feature makes them totally unsuitable for use on most types of scaffolding, as the increased base dimension will generally require wider access holes through working platforms, thus increasing the risk of falls and when used within the relative confines of a scaffold platform, provides potential and unacceptable trip hazards at the ladder base.
Where castings are used, they shall conform to BS EN 12811-2:2004 section 5. Elements of parts manufactured from ferrous metals shall be protected against corrosion as a minimum by application of zinc coating C2 or C3 according to BS EN 12811-2:2004 section 8.1. All other materials should be selected to suit their intended use and where appropriate, in accordance with applicable British and European Standards. This standard does not therefore cater for ladders required to provide access and egress within scaffolds, which by their design and instructions are intended for and limited to ‘specific professional use’ only. This document therefore aims to provide guidance for buyers, hire and sale specialists and ladder manufacturers regarding the essential requirements for scaffold ladders.
Components STATUTORY REQUIREMENTS
1. Girder Coupler (Flange Clamp)
NASC
1 of 4
2. Shear Plate The Work at Height Regulations 2005 requires that: • Work equipment is appropriate to the nature of work to be performed and the foreseeable loadings. (Regulation 7). • A ladder shall be so positioned as to ensure its stability during use (Schedule 6). • A portable ladder shall be prevented from slipping during use by (a) securing the stiles at or near their upper or lower ends; (b) an effective anti-slip or other effective stability device; or (c) any other arrangement of equivalent effectiveness (Schedule 6).
The Provision and Use of Work Equipment Regulations 1998 (Regulation 4) requires that: • Work equipment is so constructed or adapted as to be suitable for the purpose for which it is used or provided.
The HSE published ACOP and Guidance document, L22, ‘Safe Use of Work Equipment’, also requires that equipment must be suitable by design, construction or adaptation for the actual work it is provided to do. This means that if work equipment is adapted, it must still be suitable for its intended purpose.
June 2021
NASC
1 of 4 June 2021
AUDITS DUE TO RESUME
During the pandemic, opportunities to carry out overseas manufacturing site audits in connection with the NASC CoP product audit have been seriously compromised, but it is envisaged that these audits will resume in 2022.
NASC full Supplier members are required to submit product for audit, where an NASC Code of Practice audit exists for that product. The Confederation regularly updates listings of compliant products on its website. The next update will be to October 1 2021.
TIMBER AND STEEL SHORTAGES
Materials shortages are currently a major problem for the UK construction sector, and scaffolding is no exception. Sean Pike, NASC Hire, Sales, and Manufacturing Committee Chair, sits on the Construction Leadership Council (CLC) working group which deals with materials issues. He has reported that steel and timber are both in short supply, and that this is having significant repercussions for the industry.
This situation has been compounded further by logistical issues affecting the UK road transport industry, and the international shipping container sector. These issues are unlikely to be resolved before the middle of 2022.
THE COMMITTEE IS PLEASED TO WELCOME IDEAS AND SUGGESTIONS FOR NEW AND INNOVATIVE PRODUCTS FROM THE CONTRACTING MEMBERSHIP. PLEASE DO NOT HESITATE TO GET IN TOUCH, WE LOOK FORWARD TO HEARING FROM YOU.
FUNDING UPDATE
NASC members are reminded that funding is still available to offset the cost of a variety of training courses.
Members can claim for employees that complete the CISRS Operative Training Scheme (COTS), Continuing Professional Development (CPD) and mental health first aid courses.
They can also gain financial support for training ex-Armed Forces personnel. This funding stream has recently been expanded to cover the entire cost of taking a new recruit through scaffolder training – from COTS up to and including their Part 2 qualification. More details below.
In total, £280,000 is available to members through these funds.
FUNDING CLAIMED
More than 280 funding claims have been processed by the NASC in 2021. These include more than 200 applications for CPD funding, 65 for COTS funding and more than a dozen for mental health first aid funding.
These claims total more than £30,000.
SERVICES TO SCAFFOLDERS
The NASC’s latest funding pot has been set up to encourage more current and ex-Forces personnel to retrain as scaffolders.
Under this fund, NASC members can receive the full cost of taking an ex-Forces starter through the core CISRS Scaffolder training scheme – COTS, Part1, Part2, VQ2 and Skills tests.
Lynn Way, NASC President, said: “Through this additional Armed Forces fund, we have significantly strengthened our careers proposition to Armed Forces personnel. All ex-Forces individuals that enter the scaffolding industry through an NASC member will be eligible to receive up to £1,000 in training as before.
“Those wishing to become a scaffolder will now receive their full training – from COTS course up to and including their Part 2 qualification – for free.”
The Armed Forces fund provides members with up to £1,000 towards non-operative training for ex-Forces employees. This can cover the cost or partial cost of one course or several shorter duration courses and can be used in full on one individual or smaller payments on several individuals.
Eligible courses include IOSH, NEBOSH, first aid, SSSTS/SMSTS, estimating, design and HGV driving. Other courses will also be considered for funding.

CONNECTING WITH THE FORCES
The NASC has recently taken steps to actively promote the Armed Forces Training Fund directly to ex-Forces personnel.
The NASC exhibited at a British Forces Resettlement Services careers event in Nuneaton and remains in regular correspondence with both the Career Transition Partnership (CTP) and RFEA, the Forces employment charity.
NASC Training Officer Henry Annafi said: “I’m passionate about raising awareness of the opportunities in the scaffolding industry to jobseekers of all backgrounds, none more so than current Forces personnel and veterans.
“Our offer is now clearer and stronger than ever. Backed by the
Scaffolding Careers website, and the many live vacancies on offer on it, we’re able to showcase the many careers open to ex-
Service personnel, the access to free training via NASC member employers and a host of current jobs.
“While the NASC is happy to serve as middleman between Forces personnel and NASC members, we’re also encouraging members to play a direct role in bringing more Service personnel into their employment. There are a variety of careers events – both in the real world and online – taking place throughout the year attended by current Service personnel and recent Service leavers looking to start a new career.
“We’ll be sharing these with members through the NASC Bulletins.”

FOR MORE ON THE NASC’S TRAINING FUNDS AND TO SUBMIT A CLAIM, VISIT THE MEMBERS’ AREA OF THE NASC WEBSITE. PLEASE NOTE, WE ASK MEMBERS TO WAIT UNTIL OPERATIVE CARDS HAVE BEEN ENDORSED WITH COTS AND CPD TRAINING ACCREDITATIONS BEFORE THEY SUBMIT REQUESTS FOR FUNDING.