
Committed to setting standards for safety and excellence as one of the world’s leading ship classification organisations
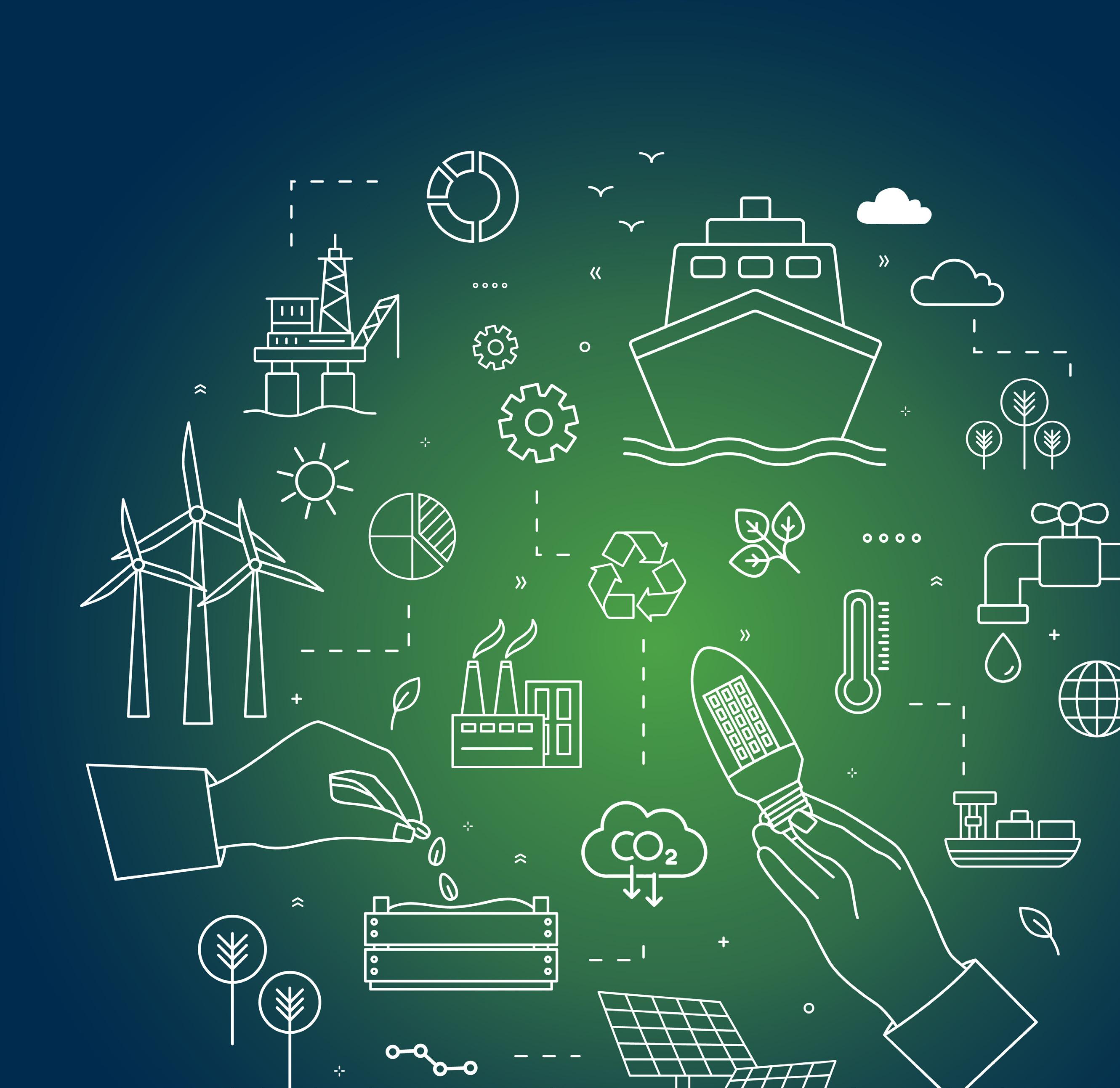

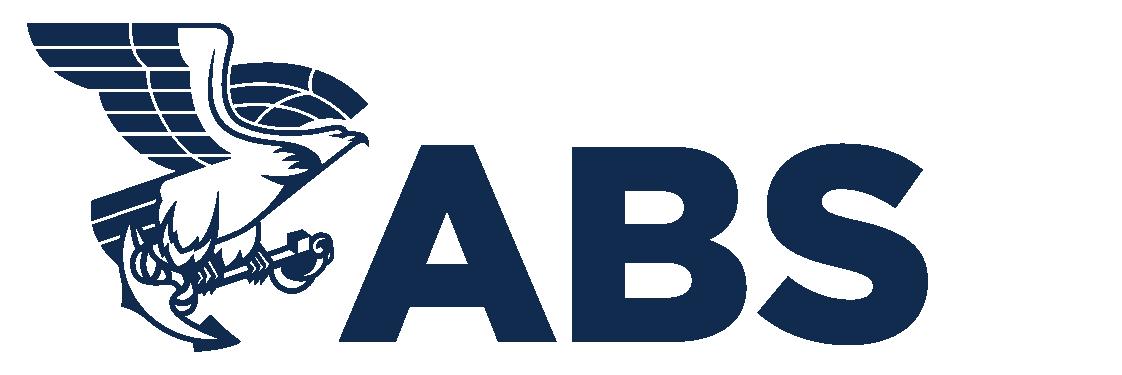
Committed to setting standards for safety and excellence as one of the world’s leading ship classification organisations
Technology is advancing more rapidly than any other time in maritime history, with digital technologies moving fastest of all.
Understanding what the impacts of digital technologies will be, what investments ought to be made, when and why, are the daily concerns of Patrick Ryan, Senior Vice President, Global Technology & Digital Products, and Chief Technology Officer, ABS.
A qualified Naval Architect, Patrick brings decades of experience in technology development within the shipbuilding industry to ABS with a mission to share that information with the shipping community.
He focusses on innovation surrounding digital engineering technologies – computer-aided engineering, computer-aided design and digital twin technology – and is the author of seven patents in the area of industrial augmented reality for ship construction.
With the recent release of the commercial product, the Apple Vision Pro in mind, we asked Patrick to address opportunities for visualisation technologies to impact shipping.
Visual technologies augmented reality and virtual reality - are reshaping the approach to operations, training, and maintenance… tell us about them, and what opportunities do they present
Augmented reality (AR) enhances real world environments, overlaying digital information such as schematics or navigational information onto physical objects. To achieve this, cameras, accelerometers, gyroscopes, and depth sensors continuously monitor the environment to answer questions like: Where am I? What is around me? And how far away is it?
The data collection and processing happen nearly simultaneously as a digital overlay is projected to the user. Augmented reality headsets are providing constant real time information to crewmembers freeing them from computer screens and mobile devices.
Virtual reality (VR), on the other hand, immerses users completely into a virtual world. Computer games in VR are common today. This is ideal to provide a scalable, low-cost solution simulating environments for training purposes. ABS calls these environments “Meta-Ships” and their ability to be reconfigured digitally make them great training tools.
Today, advances in spatial information capture with tools like 3D scanning or 360 cameras enhance the more traditional CAD or gaming object libraries to build even more realistic VR experiences. This allows for more realistic training scenarios than navigating 3D models, though perhaps with less ability to customise them.
VR and AR are well-developed technologies, though they have room to grow. They both can be used with wearables like head-mounted displays or standard hand-held devices like tablets, laptops, or smartphones.
AR, VR and mixed reality (MR) can enhance decision-making by allowing users to interact with and relate to an asset they are viewing. These technologies have the potential to help reduce cognitive load by providing users with visuals that support understanding and provide context. There are also great examples of using visualisation technologies being used both on and away from the asset or vessel in a collaborative fashion – giving operation teams an ability to communicate and collaborate in ways previously impossible.
How important is safety to the process of introducing new technologies like AR and VR and how is ABS working to mitigate risk?
As with introducing all new technology, safety needs to remain at the forefront to mitigate unintended risks. To this end, ABS is funding research at Texas A&M to better understand the safety implications of utilising wearable devices in a field environment. These features include analysing various AR hardware devices, fitness for purpose, UI design, hazard perception capabilities, and maintaining situational awareness.
In 2023, ABS joined Crowley’s new service network using augmented reality onboard their vessels. This joint mission enabled crew members to present technicians with real-time visuals. This collaboration will lead to quicker maintenance and upgrades. The focus of ABS is to explore what is possible for future survey operations as well as safety.
What is 3D model-based engineering, how does it fit within the evolution of digitalisation in the maritime industry, and what is its role relative to visualisation?
3D model-based systems engineering (MBSE) is an end-to-end 3D design process which applies 3D models instead of traditional 2D drawings to improve collaboration across the asset lifecycle, saving time and resources. 3D models provide an improved view of a design, helping to identify potential problems at an early stage. While this practice broadly benefits new designs, 3D models can also be developed to help with retrofitting new systems for older vessels.
Improved integration of 3D design tools like computer-aided design (CAD) and computer-aided engineering (CAE) tools will contribute to Model Based Systems Engineering and set-based design. They typically also allow engineers to bring richer design tools like modelling and simulation into the process. This synthesis design model can improve feedback cycles between design, engineering and construction teams.
Visualisation in the design process helps mitigate the risk of late-stage changes. Such changes can have escalating costs in time and resources the longer they go unnoticed. Of course, these same models can be used later in the lifecycle of the vessel for training, operations, and other opportunities after the design work is complete.
With so much data to manage, how can a design office or shipyard keep control of a project?
Bringing all data of an asset into the 3D workspace can help mitigate data fragmentation and issues with information retrieval. While the key benefits of 3D models are rooted in the design and build stages, such models and CAE simulation capabilities can later support operational digital twins.
Thus, a technology to manage this lifecycle data emerged in the late 1990’s called Product Lifecycle Management (PLM). PLM technology is only more recently entering into the shipping industry since the design cycles had been traditionally slower than automotive for example –early industry adopters of PLM. The green energy transition is driving faster design cycles in shipping, which is making PLM more important.
3D models and advanced CAE software, modelling and simulation, and ultimately streaming data all merged together within PLM will deeply impact stakeholders in the design and build stages, and beyond.
How is ABS working with the industry to help develop best practices and standardisation of the application of modelling and simulation to tackle technology challenges?
Modelling and simulation involve creating and using a mathematical representation of a system to analyse its behaviour under different conditions. The mathematical models are created with multiple physical and software attributes, which allows users to quickly evaluate different solutions and determine their performance, identify software vulnerability, and cost-effectiveness.
Model development depends on the complexity of the system, the data available - and its accuracy - and the intended use case. Physics-based models characterise a real-world system’s behaviour using physics or first principles. These models are consistent and not limited to the range of data
What are the different simulation techniques that can be applied and what do they deliver to users?
It enables users to shift their focus and dive deeper into the understanding of inputs and objectives in addition to being a valuable design tool. Different simulation techniques can be applied based on the objectives. For example, a continuous simulation provides insights into variables such as temperature, power, or fluid flow, which change continuously over time. A discrete-event simulation can be used to model processes that change at discrete points in time.
Both techniques give the user a bird’s eye view, identifying bottlenecks that build up over time. An agent-based simulation can help predict outcomes by predicting the interaction of two entities and revealing patterns and insights in complex systems to users.
In this role, ABS has supported studies using simulation tools to optimise various areas of maritime operations. In one study, ABS used advanced modelling and simulation technologies to develop emergency response methods to assist ports and crew in responding to ammonia leaks or spills, taking the first step towards a comprehensive and fast ammonia release response system.
ABS has also launched a pioneering Green Shipping Corridors Simulation service to support international design and development of clean energy initiatives. The service offers a simulation of the complex network of stakeholders involved in corridor development.
How do you see the connection between simulation and visualisation technologies helping shipping?
Physics based multi-physics models certainly need a variety of visualisation solutions for the engineer to really understand the behaviour of the design or operation. The model and simulation technology are really about the mathematics and understanding of the constraints of the design or situation.
Communicating this design intent, whether a product design like a ship or a process design like emergency response, needs great visualisation technology to be effective. So now we are getting beyond static images from CAD or laser scans, and understanding dynamic situations with high degrees of complexity. VR is very well suited to help human understanding of all that math.
As systems become increasingly complex and software driven, how does ABS ensure more robust virtual testing is delivered to ensure the safety of new systems?
Virtual testing is the practice of using simulations to verify and validate the performance and functionality of a system. This practice can speed up development and implementation time by reducing the need for physical testing. Physical testing of unproven systems can be an impractical and slow process, consuming finite resources. Virtual testing, alternatively, allows a wide range of testing options that can be performed simultaneously without impacting real-world assets or prototypes.
Thousands of specific requirements in new software are not practical to perform manual testing. Ensuring software is tested in different conditions, scenarios and parameters reduces risk and cost in the hardware testing phases. The development of highly detailed and accurate virtual models of complex maritime systems is key to technology’s journey. Access to more high-quality data will help inform more accurate models. This data will come from the growing number of sensors on board modern and future assets.
How is better modelling the key to more reliable, safer systems?
Better models can support more reliable simulations, both improving output and driving broader adoption. The models can live with a vessel throughout its life cycle, supporting future testing and other applications, such as digital twins. In this way virtual testing can save time and resources for all stages of the industry. Virtual testing and commissioning can impact all stakeholders in a vessel’s life cycle. A model-based systems engineering (MBSE) approach enables engineers to explore many arrangements at an early stage. Validating designs and configurations before the asset is built can help save time in the shipyard and beyond. Issues such as interoperability can be fixed long before they become a problem, as the systems can be tested virtually for new or retrofit systems.
Established in 1862, the American Bureau of Shipping (ABS) is a premier global maritime classification society, devoted to the security of life, property, and the environment, setting marine and offshore standards.
Patrick Ryan Sr. Vice President and Chief Technology Officer