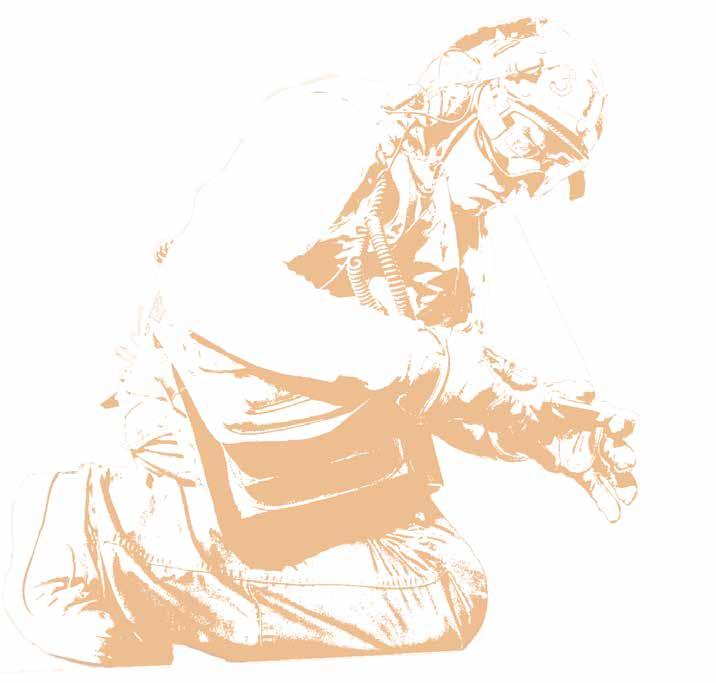
4 minute read
Trying Too Hard
By AT3 Dominic Ellingson
It was a humid night aboard USS John C. Stennis (CVN 74) and the flight schedule had just ended for the evening. My AT shop was tasked to repair four of our FA-18E aircraft by the following day, as we were entering our first day of combat flight operations during the 2011 deployment. Maintenance Control assigned my shop the maintenance priorities for night shift so the aircraft would be ready for the flight schedule the next day.
My shift supervisor gave me the pass down from maintenance of things that needed to be done for the night. I was tasked with fixing aircraft 200, which had multiple discrepancies, and was the number one priority aircraft for the shift. Given the task, I read over the list of discrepancies on aircraft 200’s workload report. My plan was to change out an antenna on the leading edge flap, plus op-check a few avionics systems on the aircraft. I also noted that we had special inspections that were coming due as well. A 336-day and 84-day were on the workload, but I failed to ask my supervisor if I could work on those specials. I took my notes and decided that if I had time after completing the major maintenance I would take care of the specials and reduce the work center’s workload.
Motivated for the shift, I checked out my tool box, ladder, and multi-meter, and donned my float coat and cranial. Doing everything correctly, I completed all pre-operational checks required for the gear, put my work orders in work, and had my supervisor check all of my tools, equipment, pre-ops, and sign all required blocks. I picked up the new antenna that needed to be installed and proceeded to the flight deck to start maintenance on the aircraft. As soon as I got to the aircraft, I set my tools down, completed a good ATAF and began removing the fasteners on the antenna. While I was removing fasteners, I found that one of the fasteners was stripped and I could not remove it by myself. I quickly went downstairs and called Airframes and informed them of the fastener. They asked me to write an assist MAF for the fastener before they would remove it, in case they needed to drill the fastener out. I cut the MAF and headed back to the flight deck to wait.
While I was waiting, I realized that it would take a while for Airframes to get to the flight deck to remove the stripped fastener, so I read over my notes

and saw that I could at least do a part of the 336-day, which was to read out the voltage on the acoustic beacon and copy its serial number and expiration date. It sounded like an easy job, so without thinking I grabbed my multi-meter and began removing panel 18 (turtle back) on top of the aircraft where the acoustic beacon was located.
Once I removed panel 18, I set it on top of the panel aft of it, thinking the panel was secured. I wrote down the serial number and the expiration date, and then pulled out my multi-meter to read the voltage. Unexpectedly, a gust of wind swept up, and I helplessly watched the panel sail through the air and crash on the deck below. I knew immediately that I had made a terrible mistake.
I climbed down the aircraft and grabbed the panel off the deck and began inspecting it for damage. I noticed that two corners had missing paint, composite damage, and seemed very brittle. I brought the panel to the other side of the aircraft and set it down, this time securing it so that it would not blow away again.
I stopped one of my flight deck coordinators and asked him to come over to see what I had done. I explained to him how the panel fell; he radioed Maintenance Control to inform them of what happened. He told me Airframes was on the way to inspect the panel and would verify the extent of the damage. After an Airframes CDI arrived, he inspected the panel and told me that it was damaged beyond our repair level and that it needed to be replaced.
Had I not taken it upon myself to do unneeded maintenance, this incident would have been avoided and I could have saved my squadron the trouble of downing an up aircraft during the first day of combat operations. It was supposed to be a good night. I should have communicated with my supervisor better, or asked my Maintenance Control if the 336-day needed to be completed, or if they were planning to send the aircraft to the hangar. Had I asked the question, I would have been told to hold off until a later date and this entire incident could have been avoided.
In my thirst to show initiative, I lost sight of the bigger picture. I now have a greater understanding why supervisors decide what maintenance I can do and what resources I need to complete the job. Our squadron currently has standing orders not to remove panels on the flight deck without personnel standing by to secure it. Unfortunately, this panel was not repairable onboard the aircraft carrier and requires Depot-level repair. Now, my squadron has a jet down in the hangar bay waiting for a $47,000.00 replacement panel and I have learned an invaluable lesson about executing bythe-book maintenance.
AT3 Dominic Ellingson is a mech with VFA-14