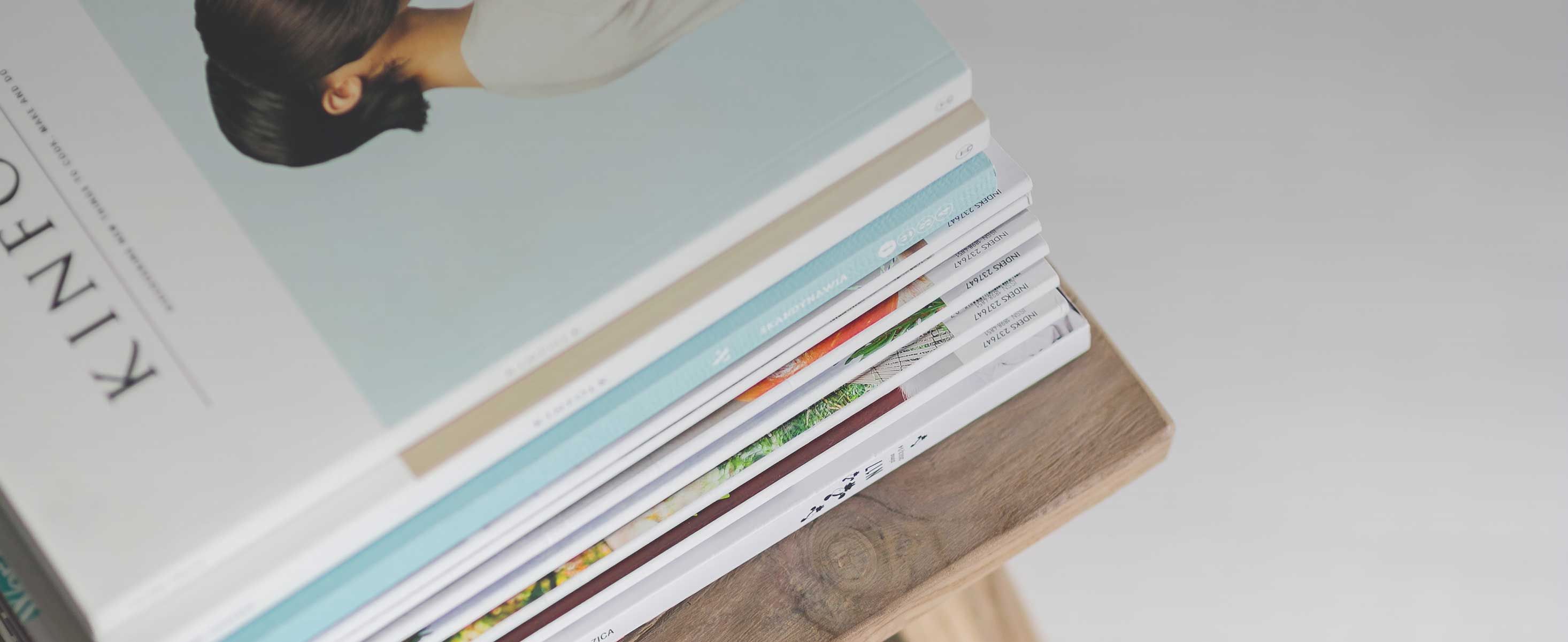
3 minute read
Electrical Connector Crimping Technology – The Right Lug, The Right Tool, The Right Connection
MANY PEOPLE IN THE ELECTRICAL INDUSTRY UNDERESTIMATE THE IMPORTANCE OF CRIMPING AND ITS IMPACT ON THEIR INSTALLATION’S PERFORMANCE. WE TAKE A LOOK AT HOW CRIMPING CAN HELP ENSURE THE RIGHT CONNECTION.
Crimping, also called swaging, is a method of cold forging an electrical conductor within the connector’s barrel. It involves compressing the connector and conductor material into a smaller cross-sectional area of the die resulting in a compression ratio, which is compared to successfully tested products.
Die shapes
In Australia and New Zealand, the hex die is the most common die shape used with compression connectors. Indent crimping is common in smaller sizes, especially hand crimping tools. Indent crimping is common with solid aluminium used with larger size conductors e.g., 240mm2 . Copper conductors require copper or reverse bi-metal lugs and aluminium conductors require aluminium or bi-metal lugs. The two metals compress differently and have different rates of thermal expansion, so connectors need to suit the metal type. Galvanic corrosion between copper and aluminium is also an additional restriction.
Dies for copper or aluminium are metalspecific and are not interchangeable. Copper dies have a narrower width than aluminium dies as copper is a harder metal. Check the dies against the recommended “across the flat” (AF) of the hex measurement to select the correct die.
Australia and New Zealand have crimp connectors with thicker walls than European DIN or USA style lugs and links. Australian dies are specifically designed for lugs and links used in Australia and do not work on European or USA connectors.
Checking the crimp is correct
A good method for checking the crimp is correct is to use a vernier caliper to measure the AF across the compaction. The die must close and this test will confirm the compaction. The measurement should be the same as the AF of the die ±0.2mm.
Good Crimp
Minimal to no air gaps with nicely formed sharp corners on the hex of the crimp.
Under Crimped
Many air gaps present with rounded corners on the hex of the crimp many may result in join failure.
Over Crimped
Minimal to no air gaps with winging obvious on two adjacent corners of the hex where the dies meet and may result in joint failure.
Preparation and installation
Proper cable and conductor preparation is essential. Always work as cleanly as possible, removing any dirt from the cable. Use appropriate stripping tools with
PPE such as cut level 5 gloves. Remove any insulation, water block or foreign material. Aluminium must be scratch-brushed to remove aluminium oxide, which has a high electrical resistance. Once the connection point has been prepared, the lug or link can be installed using the correct tooling. The right lug, the right tool for the right connection. Once the connector is installed, dress it with sand paper to remove any flashing or burrs, before installing any heat shrink or cold applied tubing.
Mike Matulewicz
Legend Cabac www.cabac.com.au
Testing
Underground lugs and links are tested according to AS/NZS 4325. Two tests are required for Class B – mechanical tension and an accelerated aging test by heat cycling. The heat cycle test is lengthy, subjecting the connectors to 1000 hot and cold cycles to test the viability of the cold forge. The standard has a Class A requirement, which includes short time current tests.
Overhead connectors in Australia are tested to AS 1154. Mechanical tension is mandatory, but heat cycling and short time current is optional. Cabac has a NATA accredited laboratory to test their connectors according to AS/NZS 4325. Cabac Lugs and links are manufactured to the relevant specifications.
View the full webinar
To find out more about crimping, visit: www.bit.ly/crimpneca