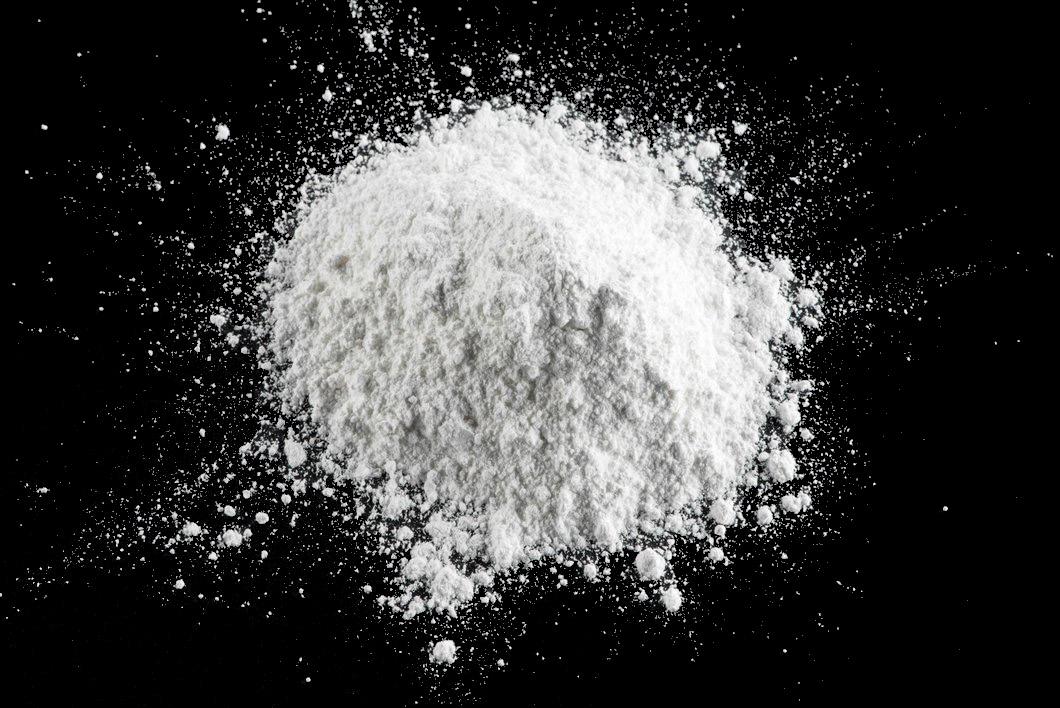
6 minute read
Understanding calcium carbonate and dolomite as extenders
Author: Harshil Kansara, technical director, Victoria International.
If the image of coating extenders were on par with the price to performance properties as well as durability – extender manufacturers and suppliers would be highly pleased. Unfortunately, this is not always the case. Some paint chemists have reservations on the selection of extenders for paints.
Extenders may vary in characteristics such as reactivity, sensitivity and solubility in water, as well as ph of their aqueous mediums. Reactivity may be due in part to origin and processing methods, but some is inherent in the particular extender itself an example, calcium carbonate is more readily affected by acidic conditions.
The reason may lie in the knowledge of their chemical and physical characteristics. Further extenders may be used in significantly high quantities in paints relative to pigment, binder and additive levels. Paint chemists must recognise the necessity of evaluating these extenders carefully or work closely with the manufacturers and suppliers in open and effective discussions.
In this article the authors examine the use of calcium carbonate vs dolomite in a typical universal matt acrylic paint and textured coating.
Three grades were evaluated: 5microns, 10microns and 45microns (textured). The main purpose is to highlight the individual physical and chemical characteristics of calcium carbonates and dolomite (naturally occurring grades), in terms of their mineralogy, crystal form, presence of impurities, and degree of refinement and processing, mainly for the paint chemist to make specific selections to achieve certain end results in their paints and coatings.
EXTENDERS
The range of naturally occurring white minerals and synthetic white inorganic pigments that are relatively colourless and transparent in organic binder films are referred to as extenders.
Extenders are paint additives that are insoluble in the binder and solvents of formula and have little or no opacity or colour effect on the film. They are added to modify the flow and mechanical properties of the paint as well as the permeability, gloss and levelling characteristics of the paint film.
Extenders are generally used in paints to give or enhance certain properties. They have extensive application, the major areas of use being as fillers and sanding aids in putties. It is used as filling compounds, primers and undercoats as a flatting agent to give inter-coat adhesion.
It has been used as viscosity modifier in matt and semi-gloss paint, as well as a surface modifier in texture paint. Higher micron size such as calcium carbonate 45 or dolomite 45 are used to give the texture effect.
There are several types of extenders available, main extenders used in the coatings industry for various properties are: calcium carbonates, dolomites, barytes, kaolin clay, talc, mica, silica, wollastonite (calcium metasilicate), perlite and vermiculite.

Calcium carbonate

Dolomite
CALCIUM CARBONATES
Calcium carbonate is considered a high-volume usage extender in the industry. It has been the workhorse in the extender range.
It is the most widely used of the extender pigments and is employed as a bright, yet inexpensive extender for titanium dioxide to increase the bulk and lower the cost, as well as to control rheology and gloss levels. It is available in many grades varying in average particle size and particle size distribution.
Calcium carbonate is used throughout water and solvent based coatings for both interior and exterior applications. In exterior application calcite has good weatherability except in highly acidic atmospheres. Its hydrophilic nature accounts for easy dispersibility, especially in water-based systems. The low oil absorption of calcium carbonate is an advantage as it requires less vehicle to bind it and subsequently leaves more vehicle available to bind to the substrate.
Other than natural calcium carbonates it is also available in synthetic form, which is precipitated calcium carbonates and nano calcium carbonates, which are used in specific applications.
DOLOMITE
Dolomite is magnesium calcium carbonate, which is generally used in paint as a filler. Dolomite is a hard mineral, thus it imparts very good scrub resistance to the paint. It is a white extender, which does not interfere with paint colour and give opaqueness to paint film. It is easy to disperse due to its hydrophilic nature same as calcium carbonate.
PROPERTIES OF CALCIUM CARBONATES AND DOLOMITE
Calcium carbonate, the chemical formula of which CaCo3, and similarly dolomite with chemical formula CaCo3MgCo3, does not reflect the complexity of these natural minerals. In fact, each carbonate deposit has its own genesis and identity, having products with equivalent chemical compositions, but different end properties. Source, origin, temperature and pressure differences and quantities of the original chemical compounds are the root of the major differences in minerology, structure, whiteness, brightness and so forth.
TECHNICAL COMPARATIVE EVALUATION
To highlight the main advantages of using these two extenders interchangeably, a short evaluation on universal or general purpose super acrylic emulsion formula with pvc of 30-35% with carbonate loading of 16% or 200g/l. The typical 5-micron grades were used in this case. The results are coming out very similar in terms of washability, opacity, whiteness with slight change in formulation.
The 10 and 45 micron grades were compared in a typical coating formula with a pvc of 76% and 37% loading or 600g/l incorporation of combined 10 and 45. Where it is noted that dolomite with more hardness than calcium carbonate is giving slightly better hardness, which can be obtained by calcium carbonate also by some change in formulation.
Different kinds of calcium carbonate such as precipitated calcium carbonate and nano calcium carbonate makes it more advantageous than using dolomite due to special advantage of brightness and opacity with higher scrub resistance.
MARKET RESEARCH
The customer base to use extenders include paint, ink, rubber, ceramic, paper, construction and plastic industries. Market research is showing that there is potential of 60 000mt (metric tons) to 100 000mt (metric tons) of market available for carbonates in the South African coating industry per annum where the majority of companies are using calcium carbonates than dolomite due to large production capacity and imports of calcium carbonates against dolomite.
The work horse is calcium carbonate where dolomite is slowly gaining with better consistency and better quality with more equivalent grades to calcium carbonates. Chemists have a wide range of carbonates to choose from depending on cost factors and loading of carbonates and required properties.
Dolomite also has potential of larger volume over time providing a broader range of products competing with equivalent grades to calcium carbonates.
Local companies of dolomite is emerging with higher volume production and with increasing numbers of resourcing where it was a challenge in the past. Other challenges such electricity supply, the right equipment to produce the required micron size material which leads in broader choice of carbonates availability in market have also been overcome.
CONCLUSION
Considering the supply of the differing grades, consistency, quality and availability of the local and imported calcium carbonates and dolomites in South Africa, the three grades selected for these evaluations were most appropriate. In our test we found dolomite is harder and thus gives more hardness in texture coatings on coarser particles, and on the other side calcium carbonates are found to be more brighter depending on source of origin.
Calcium carbonates have an advantage in terms of its varieties available in the market over dolomite, which can be used for special applications.
These two products can be interchangeable in some formulations depending on what properties are more desirable for particular formulation.
Chemists can make decisions based on their extensive work in the lab and can interchange with some tweaks in formulation. Further and more extensive work needs to be done on their suitability in other coatings at varying pvc levels and varying loading levels.
In my personal experience I worked with dolomite 45 and dolomite 10 rather than calcium carbonate 45 and 10 and vice versa and both are interchangeable depending on pvc level and desirable properties.
This article is based on basic evaluation done with three different kinds of carbonates used in two universal formulations.
More detail evaluation of different grades of calcium carbonates and dolomites in different kind of formulation will follow in later stage and would be presented in a future article.c