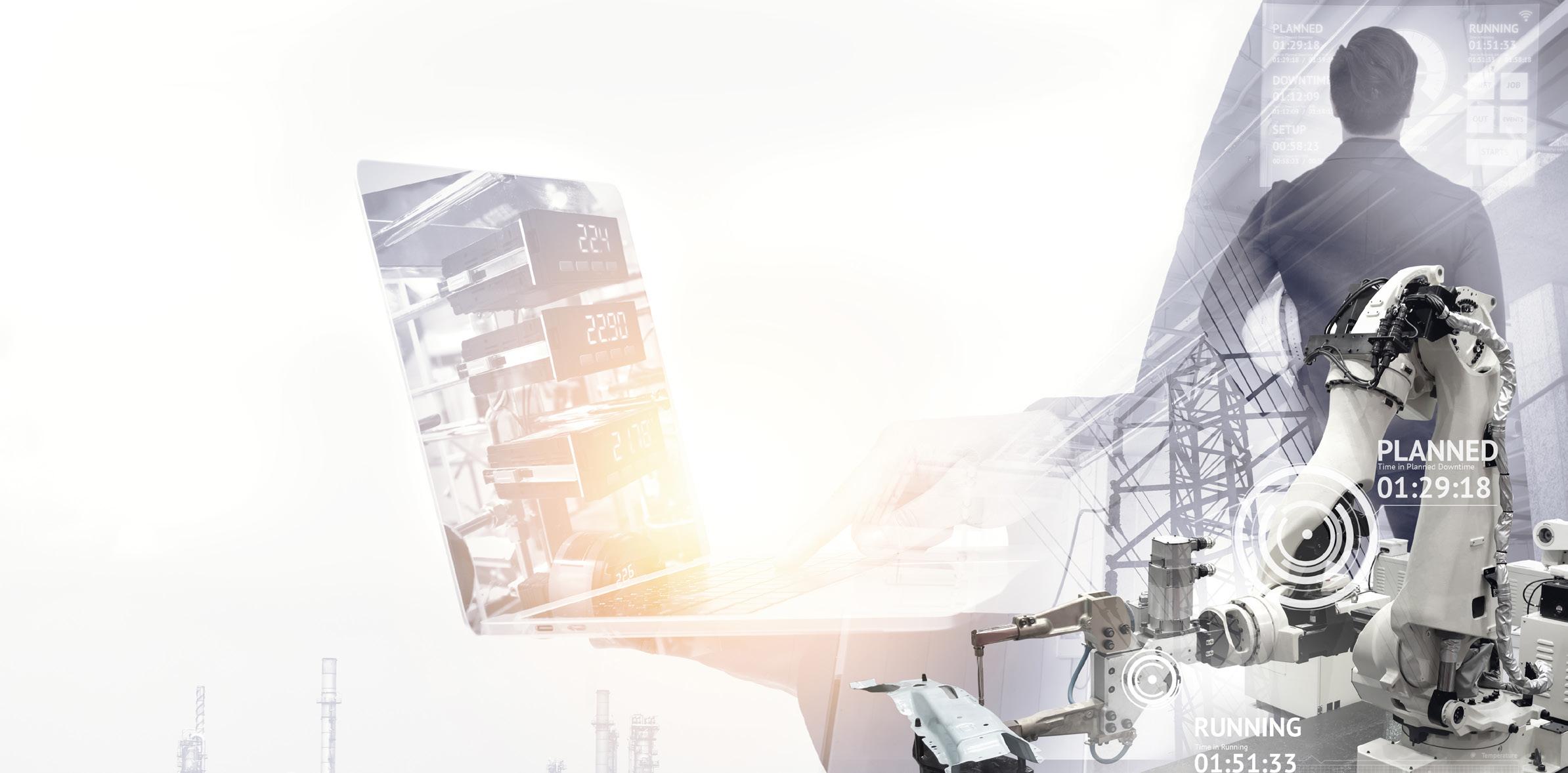
3 minute read
Evolving to meet the factory of the future
The Covid-19 pandemic has shaken the manufacturing industry profoundly. Amid the pandemic, the world could not afford for these industries to grind to a halt. From food to medical supplies, these were some of the sectors that remained at the heart of the economy and needed to operate at all costs. Although the global supply chain is usually a well-oiled machine, the unprecedented crisis forced organisations to not only rethink manufacturing and distribution, but to adapt operations to remain resilient for a postpandemic world.
IN ORDER TO understand the impact of the pandemic on manufacturers and distributors as well as emerging trends, Syspro conducted a survey in August 2020 that was completed by 144 industry professionals of different managerial levels within the United States, Canada, EMEA and APAC. The study - titled The inflection point for the factory of the future - focused on the rise of the remote workforce and the need for increased collaboration, the impact of supply chain disruptions and emerging trends that will shape the manufacturing and distribution sectors moving forward.
THE VIRTUAL SHIFT
Industries needed to change the way they operate and move into digital environments for the first time. The necessary pivot required extensive adjustment.
From the study, 37% of companies were unable to provide the remote work capabilities to employees that were needed. Organisations needed solutions that combine remote collaboration technologies, 73% of businesses stated they would need to invest in technology to facilitate remote working in the future.
SUPPLY CHAIN AGILITY
The pandemic tested the ingenuity, resilience and flexibility of supply chain leaders globally. The survey showed 60% of businesses were impacted by supply chain disruptions during the pandemic.
In response, 56% of businesses investigated dual sourcing and other initiatives to reduce supply-chain risk, and 37% were looking at planning tools that could actually incorporate visibility into the supply chain. For decades, supply chains have been heavily integrated and increasingly reliant on foreign raw material, in particular from Asia. Industries experienced increasing shortages of parts and started to find alternative supply sources and establish more resilient supply chains. In the study, 42% of businesses stated that they would transfer business operations that was moved overseas back to the country from which it was originally relocated. Organisations also started to explore industry-built technology solutions to deliver functionality to optimise, control and simplify operations.
THE FACTORY OF THE FUTURE
The study mainly revealed that business systems lacked the necessary accessibility, availability, insights and basic planning tools needed by the industry to react to the pandemic.
From the research, 37% of businesses agreed that their business systems lacked those basic planning tools that could adjust to day-to-day changes in the environment. In fact, 29% of businesses stated that their systems lacked in responsiveness during the pandemic and they would be pursuing cloud-based business systems to address immediate needs and accelerate digital transformation.
THINKING FORWARD WITH DIGITAL TRANSFORMATION
Digital adoption has taken a quantum leap in the manufacturing and distribution industry due to the pandemic.
The study revealed that manufacturers and distributors needed to increase agility in operations by continuing to invest in digital initiatives across their production process and supply networks. Benefits of transforming digitally have been farreaching. This includes the ability to innovate rapidly, the ability to offer a shorter time to market and a capability to prevent wastage by storing less inventory. Long-term results include more efficient supply chains and higher capital efficiency.
As these businesses attempt to stabilise, the challenge for many is understanding which technologies to adopt and how to pursue this transformation. •
Syspro - www.syspro.com