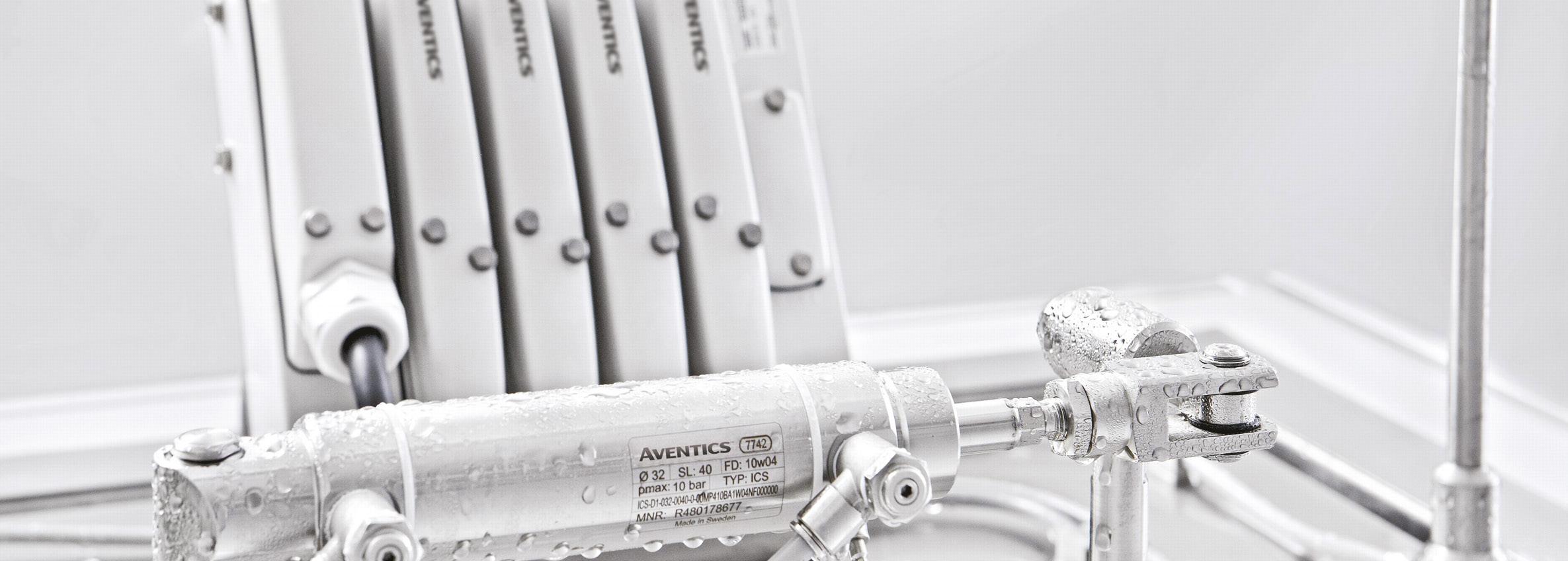
3 minute read
Simplify food & beverage
pneumatics selection with these 7 tips
Pneumatic component selection in the food and beverage industry requires special care and consideration. Strict quality and hygiene standards must be followed, and the environments in which equipment operates can vary widely, writes Giles Wilcox.
Machine designers are expected to commission pneumatic systems with excellent compressed air quality and hygienic designs quickly and efficiently. Here are seven tips that make pneumatic selection faster and easier.

1. Ensure pneumatic system efficiency
When precisely designed, pneumatic systems save a significant amount of energy. To properly size actuators, it’s important to consider the required force, pressure and mechanical limitations of an application. Find appropriate components in a few clicks and save engineering time by using online sizing software and cylinder configuration tools. When the appropriate pneumatic valve is fit near an actuator, it provides just the right flow requirements needed for the cylinder to move the load and can reduce cycle times by improving overall machine performance.
In addition, mechanical or electropneumatic pressure regulators ensure that processes only use the energy they need by giving users precise pressure control, and some even offer customised pressure control. Integrating vacuum sensors into machines with vacuum components can save energy, too, since sensors automatically switch pressure on and off when vacuum levels have been met.
2. Know the food zones
There are three zones typically recognised in the food and beverage industry, and each have their own regulations. Standards related to hygiene are strictest in the food zone where food product directly contacts machinery. In the splash zone, food product may come into contact with parts of equipment but is cleaned off and doesn’t move into the handling process. In the non-food zone, food product doesn’t touch machinery or components.
3. Understand hygienic requirements
According to regulations, food and beverage equipment must be designed and built to avoid any contamination risk. It’s also essential that it’s built to withstand the rigors of industry demands. To make them durable and easy to clean, pneumatic components must be made of corrosion-resistant, nontoxic, non-absorbent materials.
4. Consider compliance requirements
National and international regulations shape the way equipment used to produce food and beverage products is designed. These regulations vary from region to region, so it’s important to know which apply in your manufacturing location as well as where the machine will be used. Compliance has extra advantages too. It often extends equipment service life and reduces maintenance.
5. Recognise operational demands
From high-pressure cleaning to chemical agents, food and beverage washdown processes can be harsh. It’s important to know where components will be located and which processes, they’ll be subject to. Pneumatic components should be built to endure frequent cleaning, like Emerson’s Aventics Clean Line Air Valves Series CL03. With an ingress protection rating of 1P-69K, these valves are robust enough to not require a protective cabinet in washdown areas.
6. Incorporate smart pneumatics
The diagnostic and preventive maintenance data that smart pneumatic solutions provide can help anticipate wear and significantly, minimise machine downtime and wasted energy. From leak detection to pressure and consumption monitoring, smart pneumatics solutions can be seamlessly integrated into systems. Edge computing solution, like Emerson’s RXi2-LP Edge Computing Device, provides real-time operations control that delivers key insights into equipment and systems that help end users increase uptime and overall efficiency.
7. Talk to pneumatics experts
Working with a proven pneumatics supplier in the food and beverage industry makes the design process quicker and easier. An expert supplier will have a complete pneumatics portfolio, often with preassembled actuator control systems, freeing engineering resources and streamlining procurement. For instance, Emerson’s pneumatic specialists can provide resources for the design and implementation of pneumatic positioning systems that use IIoT and advanced feedback control, like the Aventics Series AES fieldbus module. These systems can be easily designed to monitor the correct position of a cylinder and load while transferring critical machine data to a PLC for analytics and predictive maintenance. •
About the author: Giles Wilcox is the subSahara African Manager, fluid control and pneumatics at Emerson