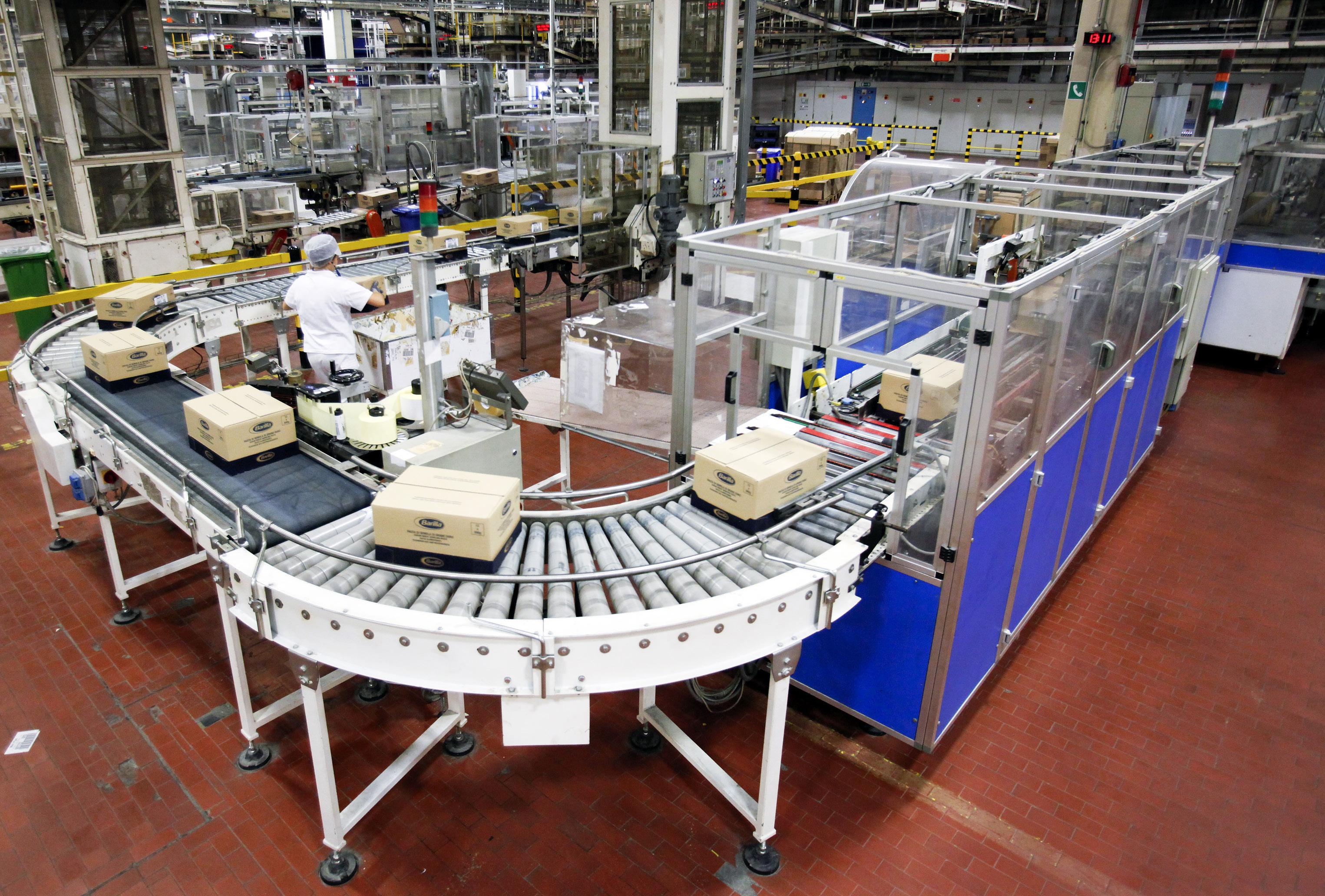
2 minute read
Tank-free hot melt technology in action
The InvisiPac Hot Melt System can improve end-of-line packaging productivity at any speed, within a compact footprint.
In the fast-paced world of manufacturing, downtime is not only an inconvenience, but also a costly setback that can have a significant impact on productivity, profitability and customer satisfaction. Each minute of halted production translates into lost revenue and wasted resources.
The InvisiPac Hot Melt System offers a revolutionary solution that goes beyond mere possibility and
A standout innovation with many benefits
• Created by leading experts, the Invisipac Hot Melt System offers many advantages: transforms downtime into a thing of the past. This cuttingedge adhesive application technology is designed to minimise interruptions and maximise uptime, enabling businesses to maintain seamless operations and gain a competitive edge.
• No Glue Build-Up: The Invisipac system ensures a consistent and controlled flow of adhesive, eliminating the common issue of glue build-up. This helps to avoid disruptions in production lines and maintain product quality.
• Reduced Risk of Burns: Traditional hot melt systems involve handling molten glue, which can pose a risk of burns to operators. In contrast, the Invisipac system minimizes this risk by keeping the adhesive in a solid state until it is precisely needed.
• Efficient and Precise: The on-demand melting feature allows for efficient adhesive application. The system only heats the necessary amount of adhesive, reducing energy consumption and minimising waste.
Enhanced safety and user-friendly benefits
Graco’s InvisiPac tank-free melt on demand technology boasts an industry-leading start-up time of merely 10 minutes, significantly reducing start-up energy consumption by 40%. Furthermore, InvisiPac achieves a minimum reduction of 30% to 50% in adhesive usage and effectively prevents unplanned downtime associated with charring, nozzle blockages and hose complications. Collectively, these advantages ensure substantial savings. The InvisiPac Hot Melt System maintains a uniform temperature and viscosity for adhesives. It functions based
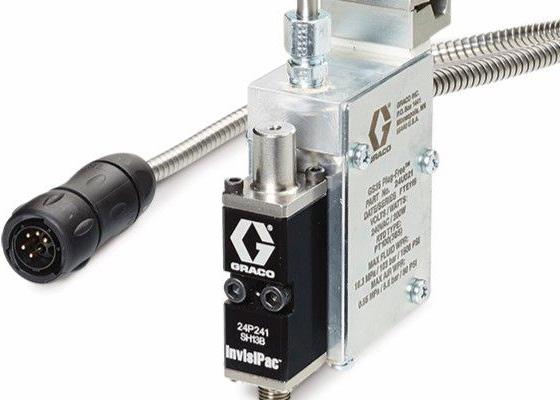
“The InvisiPac Hot Melt System epitomises reliability and efficiency within the manufacturing sector” on a first-in-first-out (FIFO) methodology, which prevents temperature variations and the development of char. Throughout production, material output remains stable, ensuring no downtime.

The integrated module filtering of the InvisiPac applicator prevents nozzle blockages and guarantees a consistent adhesive bead on each box. Additionally, it allows for the monitoring of adhesive consumption, system performance and line data from any location at any time, facilitating the achievement of Industry 4.0 objectives.
The InvisiPac system enhances safety by ensuring that operators do not come into direct contact with the hot molten adhesive, thereby mitigating risks associated with burns, toxic fumes and slippage. When the adhesive within the melter attains a predetermined level, an automatic signal is dispatched to the feeding system, prompting the adhesive to be drawn from the container directly into the melter, all without the need for operator involvement.
This compact device features a hot melt output of 11.3kg per hour, making it suitable for medium to high volume case and carton sealing applications. It is available with four to eight channels, and the melt-on-demand system seamlessly integrates into end-of-line packaging processes.
Efficiency in manufacturing
In the ongoing quest for operational excellence, reducing downtime stands as a paramount objective.
