
5 minute read
Working together - How our future is growing
By Scott Morahan and Kate Grant
Growth in any business is necessary, whether it is planning to expand product lines, streamline efficiencies in workflow processes or advance communication systems to improve impact on productivity and therefore value to the customer.
Ball Australia targeted these areas with their move to Skye in 2017, with a purpose-built nursery and a site that allowed scope to maximise growth. Now five years on the company has settled well into the site at Skye and is realising the planning for further future growth an essential need. As Scott Morahan the Head of Production noted, ‘We had 40% extra growing capacity when we moved here, thinking it would give us some years to utilise that space, yet our growth has increased to 80% and we are ready for further expansion.’
The company was thrown a challenge in 2019 after a fire heavily affected part of their production area, and as Scott realised, ‘Even though the site was relatively new, it forced our hand and allowed us to re-assess and re-design how our production flow and layout could be more effective, resulting in better customer fulfilment’.
A number of areas were reviewed as part of the re-build and once the clean-up from the fire had been completed, the first key area to improve was the quarantine house. The opportunity to split the quarantine house into two smaller zones was essential, enabling the flow of product through the quarantine house to be more manageable, offering greater flexibility with what can be brought into the house and when.
Tissue culture volumes have increased significantly for the business over the past five years. The fire consumed the de-flasking tent and benches from this area leaving a significant gap in the production flow. De-flasking can be complicated and is potentially a high-risk operation if you do not have the right set-up. While the rebuild for this department was underway, the operation had to be relocated to the germination houses. This was good for the plants, but not for the process flow, KPI’s and more importantly the staff who had to work in such a humid environment month after month.

Aftermath from the fire - 2019
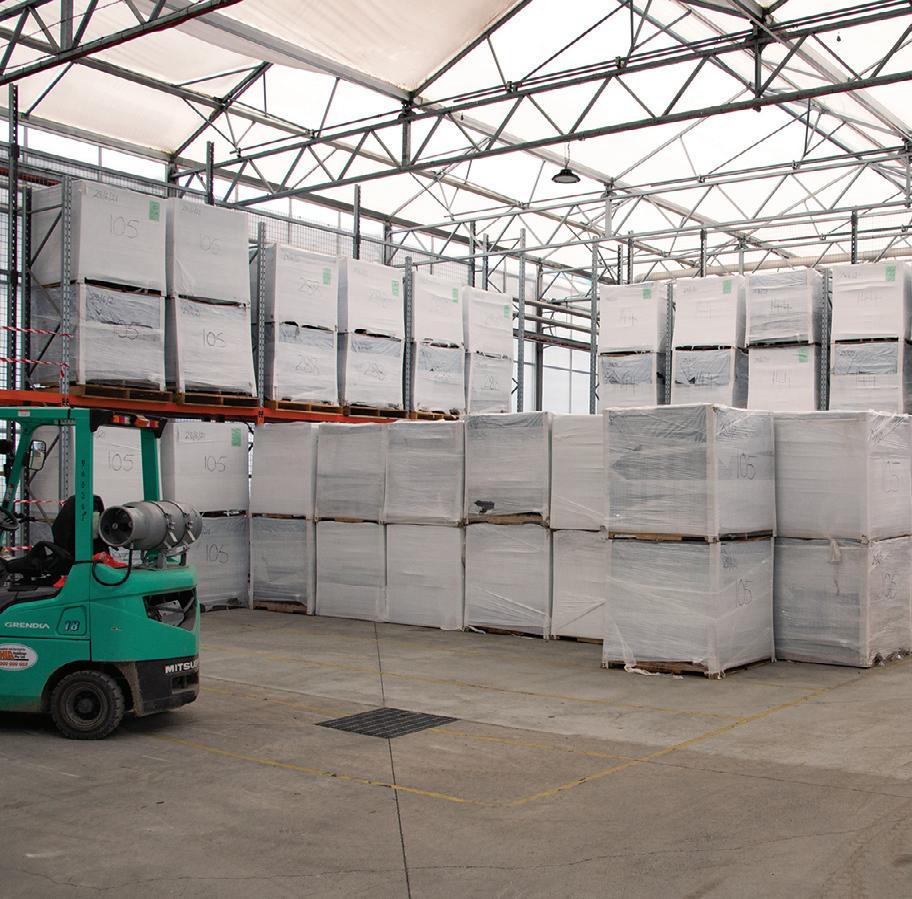
New storage racking
Ball Australia now has a fantastic new system that incorporates a temperature-controlled chamber for receival, unpacking, inspection and holding. Minimizing the stress on very small plants waiting to be transferred to plug trays. The new design incorporates two-way conveyors, individual workstations that maintain efficient production and good hygiene. Two misting tents have been installed to further reduce environmental stress on warm days so as to not impact the production flow of the sowing and vegetative lines as the benches make their way into the fog compartments.
Another vital part of Ball Australia’s operation is the vegetative plug supply from home grown mother stock that is generated from elite imported material. Cuttings are taken from the mother stock production and are then stuck. Previously the design and process flow for this work section was fairly basic. So, in a similar manner to how the company improved it’s e-flasking operation, they replicated the same for this work area by Introducing another row of conveyors, workstations and timers.
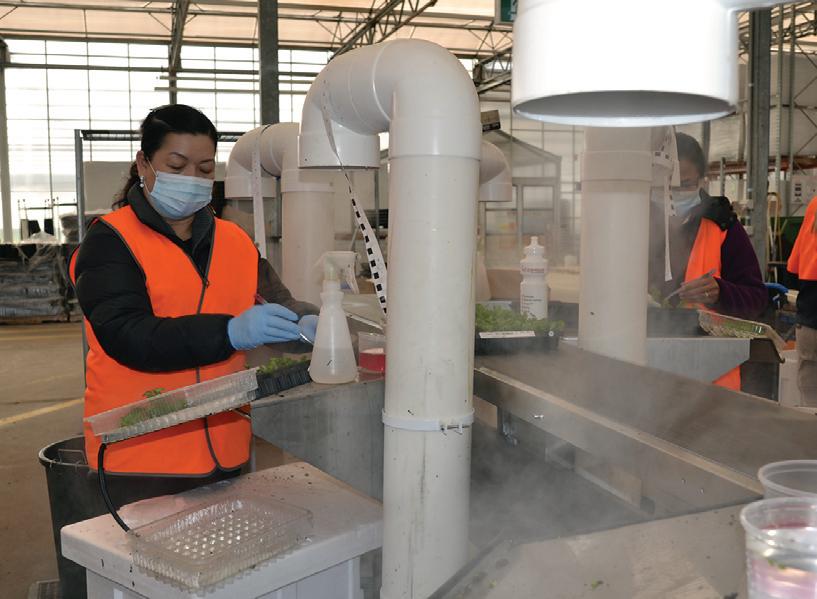
The new TC work stations
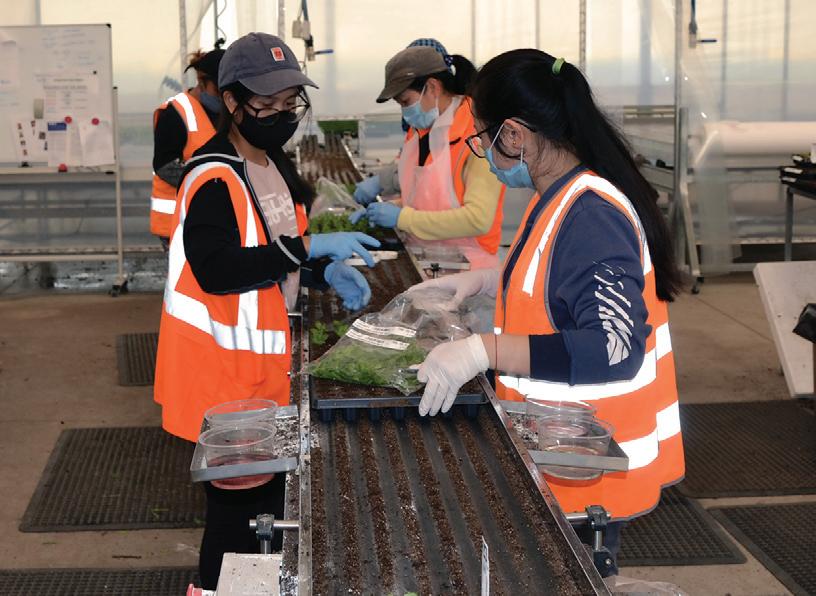
The new sticking line in action
Scott Morahan commented, ‘We have made a progressive sticking line that has significantly reduced the impact and down time created for this operation, by building a chamber for storing cuttings to manage the post-harvest stresses on leafy material. This has improved the speed and precision of the sticking lines, minimising environmental impacts that could spoil product quality.’
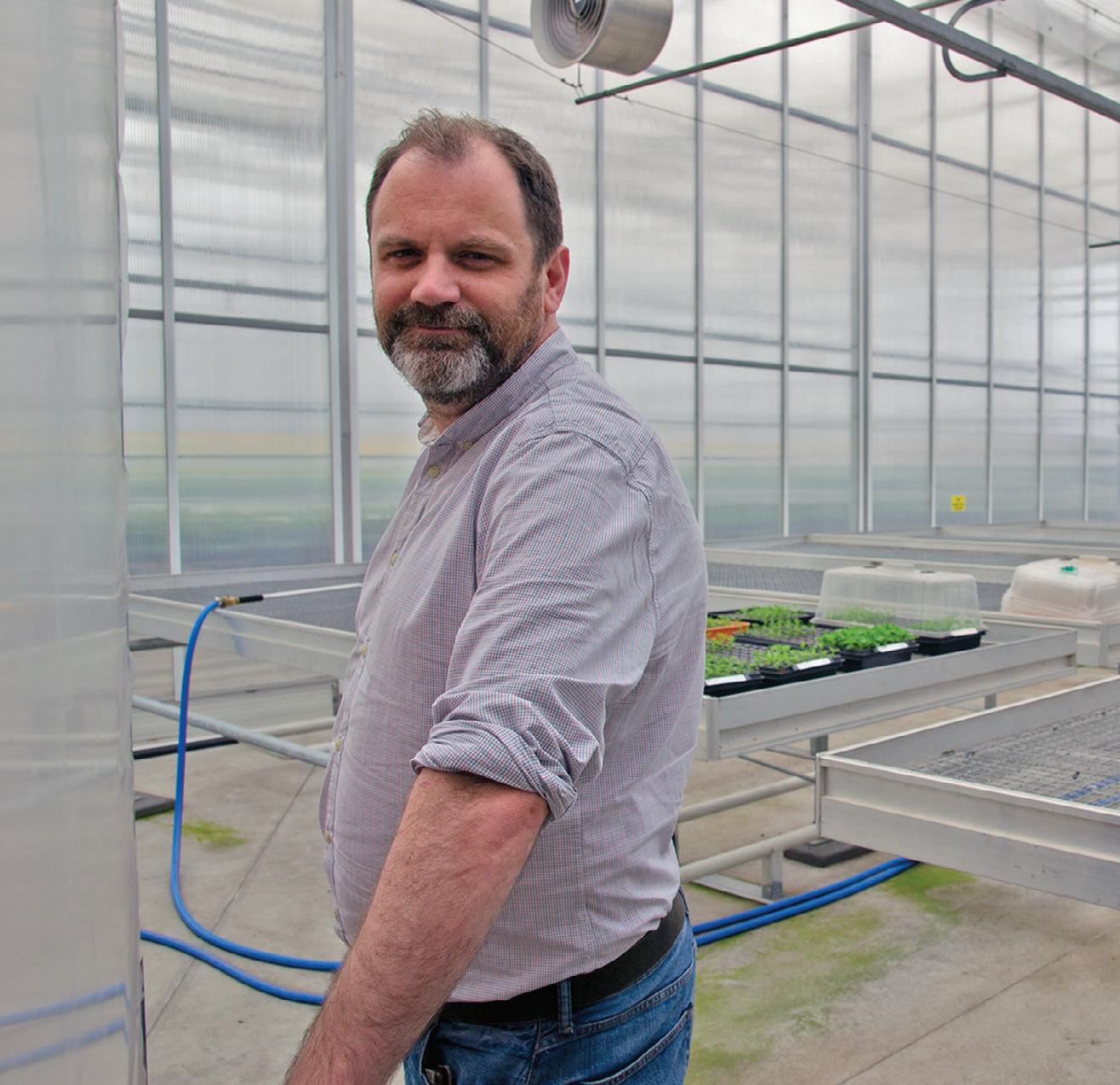
Scott Morahan entering the existing quarantine house
This proved to be an ergonomically savvy design plan for the business and improvements have seen a market rise in the KPI rates not only at the point of sticking but gapping and rework further down the production line.
Whilst not an obvious part of the company’s production flow, storage for bulk volumes of trays that come in were now able to be housed closer to the production area, placed onto a newly built racking system and housed internally.
The maintenance area and chemical storage departments had been situated within the greenhouse and had the greatest damage from the fire. Sean Warren the Facility & Infrastructure Manager with the company noted, ‘We needed a safer re-location for a purpose-built maintenance shed erected away from the main nursery so jobs involving welding, flames or fuel usage were not being performed within the plastic skin of the greenhouse. So to the storage of chemicals used for our feeding programs, need to be stored away from the greenhouse for health and safety improvements.’
The company has plans underway for the build of a chemical storage shed this year, that is to be located centrally to the main entry point of the greenhouse, ease of forklift access and bunded to contain spillages inside the shed so that nothing leaches back into the water system. A wash bay for staff will also be included, keeping the whole process of mixing and handling chemicals safer for the environment and staff.
While the re-assessment and work flow improvements have been taking shape since 2019, Ball Australia is excited by the opportunities that it has ahead for itself and is embarking in investing in a new glasshouse for further future growth with a one hectare, high health mother stock facility.
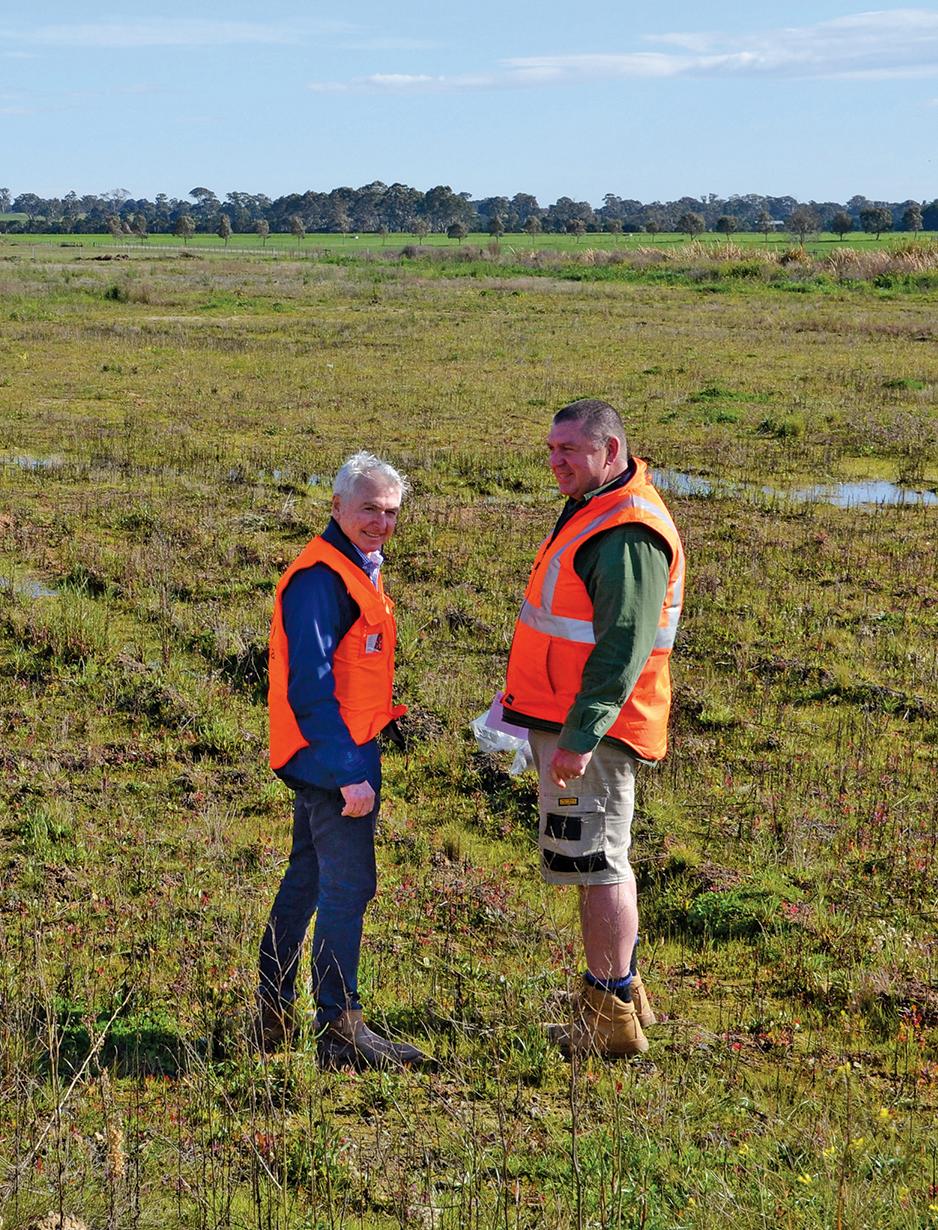
Paul Boland and Sean Warren on the site of what will be the new mother stock facility
The current mother stock house, which was always a temporary situation, will now be integrated into the new build and the space it took up will now be used for better flow and volumes of tray production.
Paul Boland, Ball Australia’s Managing Director, has been heartened by the staff and their efforts to continue to position the business as a state of the art operation. ‘Our goal at Ball Australia is to work towards having the best facility with the best people using the best practices to produce the best product ultimately satisfying our customers needs. We are confident that the steps we have taken in recent years and our plans for the future align with this goal and will ensure that we are able to continuously improve.’
About the authors
Scott Morahan, Head of Production
Kate Grant, Marketing Manager
www.ball australia.com.au