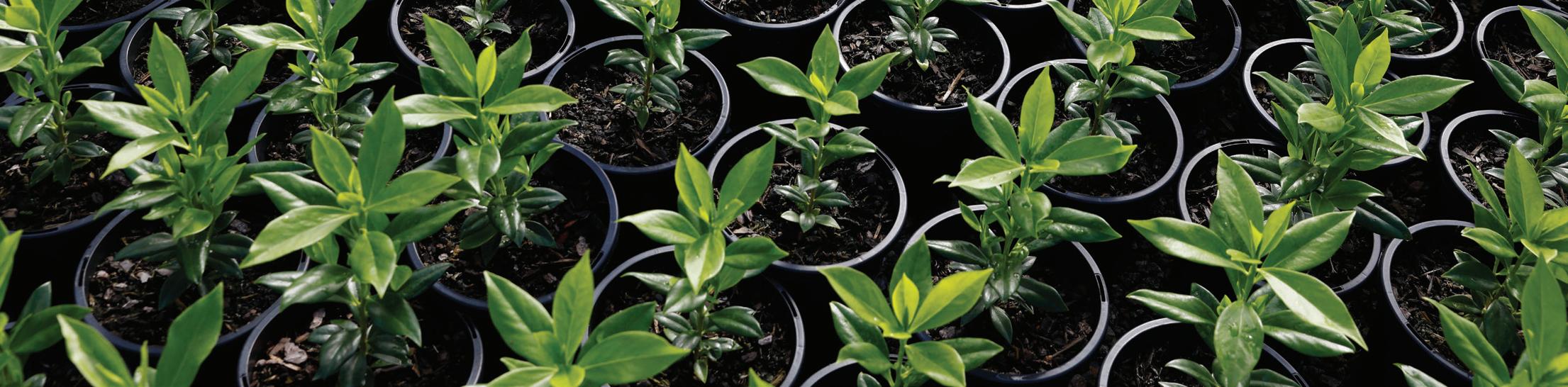
6 minute read
Improving safety across the nursery and garden industry
By Keith Govias, Risk Advisory, Gallagher
The nursery and garden industry plays a vital role in enhancing our surroundings, providing plants, trees and landscaping materials to create beautiful spaces and amenities across Australia. However, like all other industries, business operations carry inherent risks that must be addressed to ensure that the safety of workers, customers and the environment are maintained. Listed below are some key strategies from the Gallagher Workplace Risk team to improve safety across the nursery and garden industry.
1. Induction, training and competency
One of the fundamental ways to ensure safety in the nursery and garden industry, is through a comprehensive induction, training and competency assessment program for all workers. A best practice approach should include:
» Safe work procedures – Every worker should understand the hazards that are present in their job tasks and the nominated business controls or safe work process to complete the task; for example, using manual handling equipment, or how to safely decant and handle chemicals.
» Emergency response – Employers need to train workers in proper incident reporting and emergency response procedures. This includes how to react to incidents, fires, chemical spills and weather conditions. A well-trained worker can also respond better to customer incidents, potentially saving both the customer experience and in some cases reducing or eliminating the risk of public liability claims.
» Communicable illness – Workers should understand the risk from plant-borne diseases and pests, how to identify these and the appropriate measure to both prevent spread, but also prevent becoming ill through exposure.
2. Regular safety inspections and audits
Frequent workplace inspections and audits to confirm safe work procedures are being followed are essential to any good business to proactively identify and address potential workplace hazards. A robust inspection program should include:
» Machinery and equipment checks – Regularly inspect and maintain all machinery and equipment to ensure they are in a safe working condition. Where possible, keep a register that tracks the machinery or equipment, the recommended service schedule, who completed the work and when it is next due for servicing. Also consider using pre-start checks to engage workers to check machinery before use each day.
» Site safety – Conduct routine safety checks of the complete site, including walkways for egress and storage areas to identify and control any hazards such as uneven surfaces, slippery floors or inadequate lighting. Where possible try to have a schedule that allows for inspections prior to opening and again periodically during the day.
» Chemical storage – All chemicals must comply with the Globally Harmonised System (GHS) of chemical labelling and storage. Ensure that labels are clear, permanently fixed and have sufficient hazard information about the product and how to respond in an emergency. Also ensure that chemicals are appropriately stored in Dangerous or Flammable Goods cupboards where required or with the use of drip trays or bunding to protect against spills and corrosion. Also periodically check containers for leaks or damage.
3. Personal Protective Equipment (PPE)
Where required, ensure that workers are aware of mandatory personal protective equipment (PPE) requirements through training and signage in the workplace adjacent to the task or work area where PPE is required to be worn. Provide PPE for workers including:
» Gloves – to protect worker’s hands from plant thorns or branches, chemicals and sharp or rough objects
» Eye protection – Safety goggles or glasses can guard against flying debris, dust, chemicals and UV radiation
» Footwear – Sturdy, closed toed shoes with good traction should be a basic requirement. Consider steel capped footwear if in same work area as mobile plant (i.e. forklifts) or the potential for heavy items to fall on feet exits.
4. Hazard communication and signage
Clear communication of nursery and garden hazards is crucial to protect both workers and customers:
» Signage – Use clear and standardised signage to warn of potential danger. Examples could be the use of warning signage such as: “SLIPPERY WHEN WET” or prohibition signage such as “NO UNAUTHORISED PERSONS BEYOND THIS POINT”. Safety signage is coded to help provide consistent messages.
> Prohibition signs tell people what they cannot do. This is a sign with a red circle and diagonal line through it.
> A Mandatory sign alerts workers to an instruction that must be followed and is usually used for PPE. This is a white symbol in a blue circle.
> Danger signs warn people about a potentially lifethreatening hazard. This is a red oval inside a black rectangle with the word DANGER in bold.
> A warning sign identifies a hazard or condition that is not life-threatening but could still hurt. These signs are marked by a yellow background and black triangle.
» Safety Data Sheets (SDS) – Ensure that all workers have access to and understand SDS for chemicals used in the workplace.
5. Preventing manual handling risk
Promote good ergonomic and manual handling practices to prevent musculoskeletal injuries and strains/sprains:
» Proper lifting technique – Train workers in how to lift and carry heavy objects to safely prevent back injuries. Keeping your nose over your toes when moving (avoiding twisting) and keeping loads close to your stomach are two techniques to minimise risk of injury.
» Workstation ergonomics – Ensure that workstations with computers are correctly set up with adequate space for keyboard, mouse and any paper-based information. Ensure that adjustable task chairs and monitor raisers are used to help workers adjust workstations to suit their height and needs.
6. Hazard and incident reporting:
Encourage workers, contractors and customers to report safety concerns, near misses or incidents:
» Reporting process – Ensure that the process to report and record hazards and incidents is simple and accessible for workers and provide opportunities for anonymous reporting if this will encourage more reports
» Incident investigations – Always conduct and document thorough investigations for all safety incidents to identify root causes and prevent recurrence. Remember these can be legal documents to help with Worker Compensation or Public Liability claims, so try to be factual and only put down on paper what you would be happy to read aloud in court. Also ensure that no matter the outcome, you close out the investigation by notifying the person that reported the issue of your controls.
Improving safety in the workplace and building a safe culture is like growing a plant.
You have to be present, constantly feeding the culture with active leadership and conversations on safety. Additionally, you have to react when you notice that things are quite right, to prevent damage or harm.
Implementing these strategies can assist in providing a safe workplace for your workers to flourish and an environment where your customers and contractors feel comfortable to enter.

The Gallagher Workplace Risk Team are available to support questions or queries that you may have on how else to keep your workplace safe. We have a team of over 30 risk advisory, injury management and worker compensation professionals across the country to help you.
Feel free to visit our website to contact us or find out more about the services we offer: https://www.ajg.com/au/ consulting/workplace-risk/