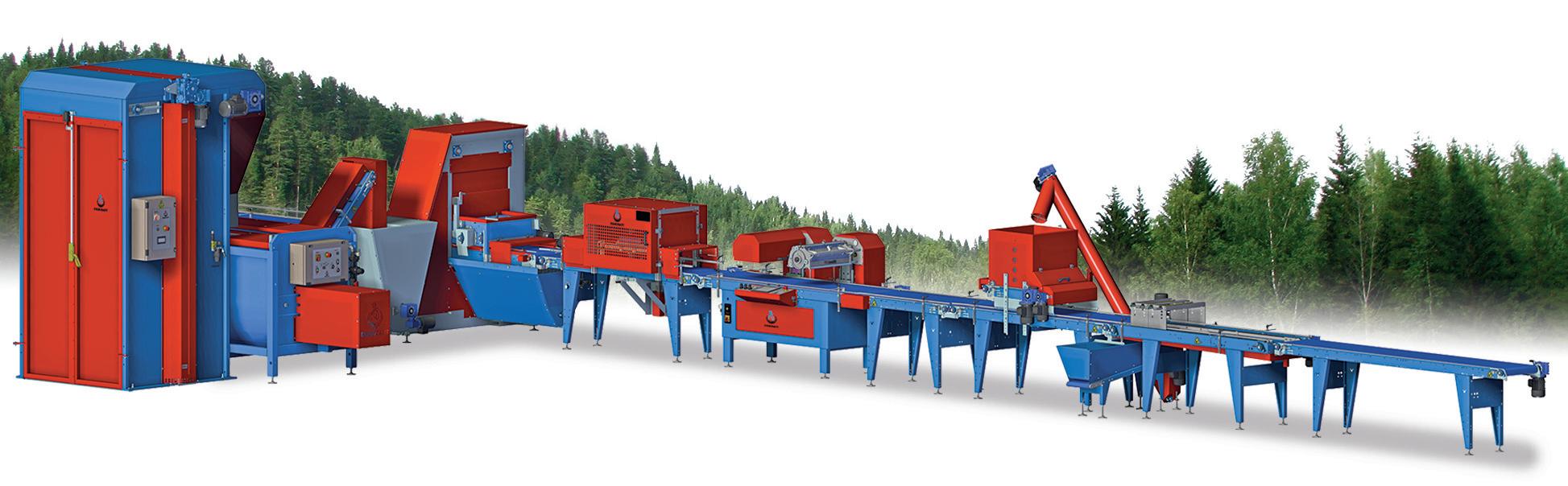
4 minute read
LOCAL AND GLOBAL APPETITE FOR AUTOMATION
By Malcolm Calder, Transplant Systems Pty Ltd
In recent years we have seen a steady upward trend within the production nursery world to explore tangible and workable ways for businesses to automate their growing processes. The two areas that are driving this are high cost of labour and the need for consistent finished product quality outcomes.
Nurseries and growers can engage automation at all levels of the production process. Return on Investment (ROI) becomes paramount when purchasing machinery and that means our role as suppliers becomes dependent on clear consultation and that is at the core of what we offer. It’s up to us to help identify a machine operation match to the outcomes needed in the nursery.
In this unprecedented time people are spending increased time in their homes and wanting to create a plant-based atmosphere. They want to grow it, admire it, eat it and enjoy the process. Everything from indoor plants and vegetable seedlings to potted fruit trees and ornamentals are in high demand.
In Australia and New Zealand this trend is creating a new level of production pressure on nurseries. This in turn has prompted an increased interest in automation and how that could work in a plant production environment. Is this behaviour being replicated globally?
Jack Ford, Sales Manager at Agrinomix in Oberlin, Ohio says, “What we have seen in the ‘woody’ side of our business is most projects revolve around material handling as most nursery operations struggle to find labourers that are willing to do that type of work. So, growers are looking for ways to do functions where there is no human touch or bringing the work up to waist level so that workers do not have to bend over” .
“While sales of potting machines have been steady, we see broader interests in conveyor systems, buffer tables, and fork systems. All items we struggled with selling in the past but an easy sale today.
On the more advanced side, we see nursery growers getting serious about using grading systems and transplanters to ensure consistent quality from starter plants to finished. Labour rates keep going up, and there are fewer and fewer labourers.”
Geert Maris, General Sales Manager at TTA BV in the Netherlands has a similar viewpoint, with growers struggling to find suitable labourers to keep up with the demand for plantlife, “What we are seeing is a trend towards data driven greenhouses for production of plants. This includes a scan management process that tracks plant movement and growth outcomes.
People have better control of their systems and it gives a new level of information that can be used to improve even more of the plant growing platform. This in turn saves a lot of labour cost. An example is a combination of sorting, grading and transplanting seedlings. The customers have the ability to do so much with the same machine now. The TTA Flexsorter provides the ability to transplant with vision selection, grading plants with multiple classifications, spacing and set them a bit wider apart and then packing into larger containers. Plants grow for example 50 per cent in the tray in the greenhouse then prior to despatch 50 per cent having been transplanted into a larger cell.”

“Another trend is a machine that can actually mix different coloured plants into a single pot. So, as you can see there is becoming a lot more choice on using specific automation. The data generated by the machines can improve operational efficiencies.”
“During the COVID crisis a lot of growers are shocked because they cannot gain access to the labour needed in normal conditions. Being unable to calculate labour numbers has meant that we are seeing the best year in history at TTA for automation. Growers can accurately calculate growing cycles for small runs and large runs for herbs, forestry, bedding plants, potted colour and more.”
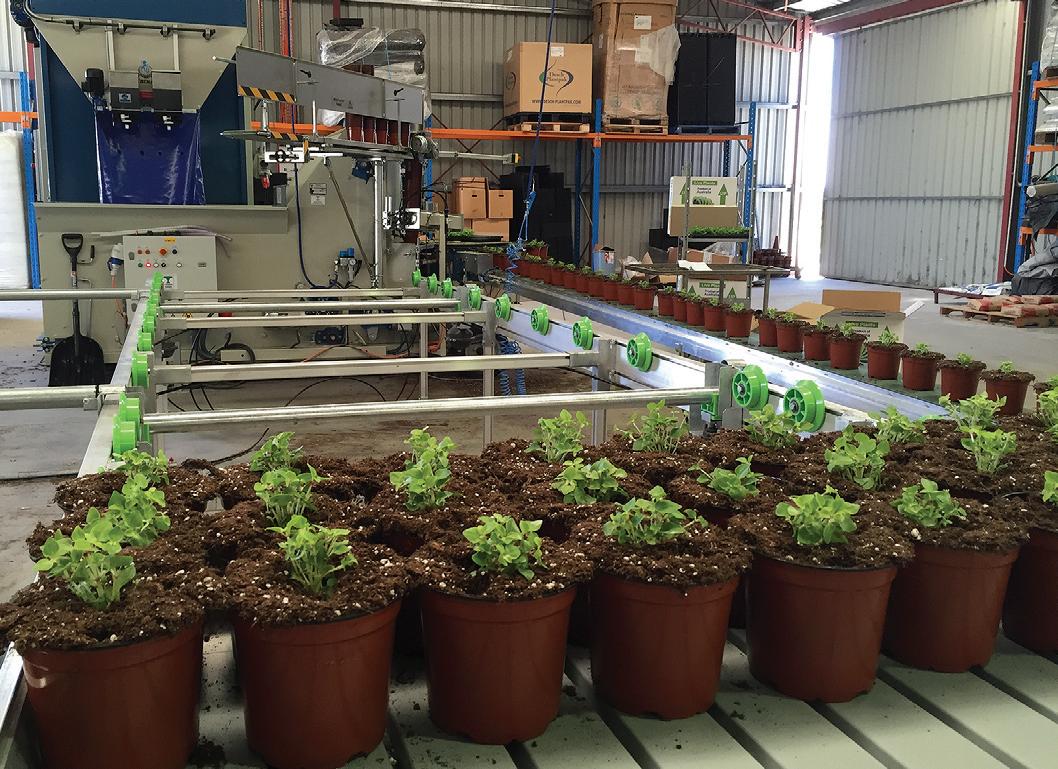
The continuing trend into containerised controlled growing has also seen consistently good results. In Australia and New Zealand, we have been privileged to be a contributor in injection moulded tray design, which is important for seeding line operation and bench space economics per plant mass in the nursery. The tray cell design is critical in the successful growing of a healthy plant with attention given to root development over a wide variety of species. A good example is in the forest sector where focus given during the early stages of growing determines the quality of the seedling being planted in the ground. Without a healthy root-system the tree will not perform, and this directly affects the profitability of the forest sector. When we look at a Transplant Systems TS45 cell tray most observers would not recognise the amount of careful time and effort put into the cell design to enable a specific, consistent seedling outcome. This is a major component in the automation process when growing from seed or cuttings.
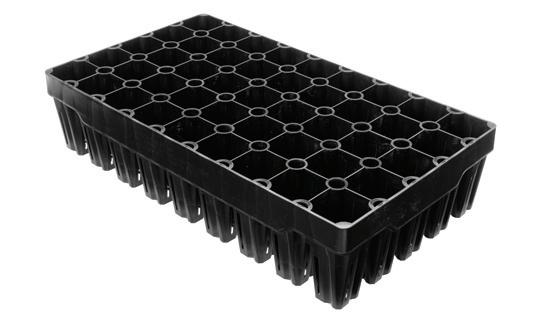

We believe automation will continue to play a key role in plant production throughout the world. As demand increases, so too does the need for efficiency in production. We look forward, along with a number of key companies here in Australia, to offering and supplying, our industry with operational solutions to help them grow.