
5 minute read
USNR and the Evolution of Sawmill Technology
Sawmills have existed since the medieval period, and they have come a long way since then. Sawmill machinery and technology have advanced over the years, most notably in the 19th century, when steam power was introduced, and again in the 20th century, when electricity became commonplace. Sawmills took another giant leap forward in the 1980s with the advent of artificial intelligence and machine learning.
One of the world’s premier technology and equipment manufacturers, UNSR, played a vital role in the evolution of sawmills. They started in the 1850s as an equipment supplier, bringing the talents of well-respected innovators together with design and technology. By the mid-1980s, USNR had begun to see the importance of supplying the machinery AND the optimization and controls that accompany it. Now, in the 21st century, USNR has hundreds of patents to its credit and continues to push the hardwood industry forward through invention and investment.
Scott Norton, a Vice President at USNR, was one of the early authors of hardwood edger optimization and has been with the company for 30 years. He says, “Our push into artificial intelligence (AI), vision tools, and deep learning is something from which all our customers can benefit. There is value in the technology that we have developed. It’s a paradigm shift in solution accuracy that achieves a new level of defect detection, making grading solutions more accurate and more profitable.”
Typically, when you think about a sawmill, you think about multiple machine centers that are like islands of automation. We are actively advancing those systems’ ability to work together by gathering information from each one and using it to improve productivity, reduce downtime, and identify potential maintenance issues before they become problems. USNR’s Self-Adjusting Machine (SAM) technology closes the loop between operators, optimizers, and control systems to adjust machines in real-time.
Relationships are one of the top values at USNR. Norton explains, “From the beginning, USNR has understood the importance of close customer relationships. We get to know our customers to understand their needs and requirements. We don’t just drop an optimization or scanning package and say, ‘Okay, here it is; you’re on your own.’ We take the time to help set it up and ensure their operation works.
USNR views its employees as one of the keys to its success, with Norton saying, “Our greatest strength is our employees, who are willing to learn, be creative, and consider new concepts and ideas. They listen to thoughts and frustrations from a broad range of people and identify the key concepts that USNR can provide our customers that will give them the most value. We’re a company with over 2,000 employees working on various products. The expertise and creativity they bring to the table make USNR a stronger company.”
The Covid-19 pandemic and the ensuing supply chain crisis were difficult for all businesses in the technology sector. USNR was not immune, with Norton crediting good relationships with their suppliers, who kept their shelves stocked for the company. The company was also able to navigate the situation thanks to the foresight of its leadership team. Norton continues, “We also purchased a lot of inventory in advance to deal with supply-chain problems. This allowed our customers to have access to parts they needed without having to shut down as they waited for a part. We have stayed ahead of the crisis thanks to our fantastic purchasing group and our management team, who recognized what was happening early on and knew it would be an issue, so they took quick action. There are still challenges with the supply chain today, but we deal with them as they come.”
USNR has been a member of NHLA for 49 years, and Norton says they wouldn’t have it any other way, revealing, “The most important thing about our membership with NHLA is the connections they give us. The networking opportunities that NHLA creates are a huge benefit for us. Going to the annual Convention is a great way for us to interact with customers and get to know what they need and how we can provide it.
We also appreciate that NHLA maintains the standard for grading hardwood lumber -- particularly from an optimization standpoint. The Rules and processes that form an industry-wide standard are beneficial because they help us understand how we need to design our systems to benefit our customers. For example, we have applied deep learning AI to hardwood sawmill edgers and trimmers and achieved a proven increase in finished grade accuracy, recovery, and total value.”
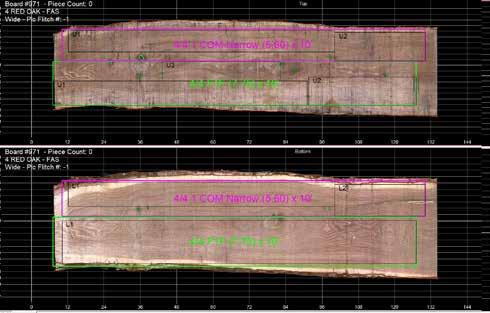
Mills have reported improved grading accuracy and an increase in higher-grade finished products. In the future, USNR expects to bring more integration and data collection in sawmills along with the expanded use of AI and machine learning. They cannot wait to discover what the next innovation will bring.